- TOP
- Tetsu-to-Hagané
- Vol. 71 (1985), No. 1
Tetsu-to-Hagané Vol. 71 (1985), No. 1
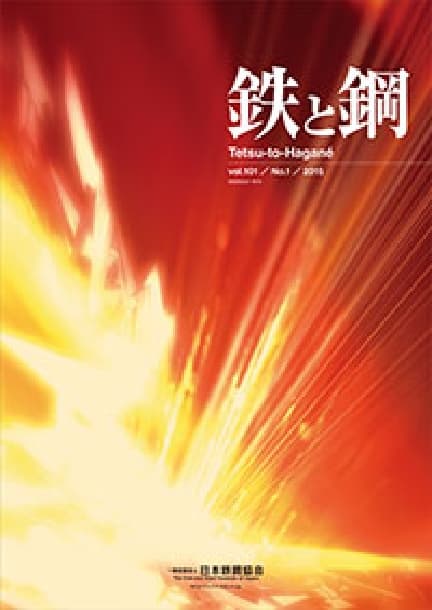
Grid List Abstracts
ONLINE ISSN: | 1883-2954 |
PRINT ISSN: | 0021-1575 |
Publisher: | The Iron and Steel Institute of Japan |
Backnumber
-
Vol. 111 (2025)
-
Vol. 110 (2024)
-
Vol. 109 (2023)
-
Vol. 108 (2022)
-
Vol. 107 (2021)
-
Vol. 106 (2020)
-
Vol. 105 (2019)
-
Vol. 104 (2018)
-
Vol. 103 (2017)
-
Vol. 102 (2016)
-
Vol. 101 (2015)
-
Vol. 100 (2014)
-
Vol. 99 (2013)
-
Vol. 98 (2012)
-
Vol. 97 (2011)
-
Vol. 96 (2010)
-
Vol. 95 (2009)
-
Vol. 94 (2008)
-
Vol. 93 (2007)
-
Vol. 92 (2006)
-
Vol. 91 (2005)
-
Vol. 90 (2004)
-
Vol. 89 (2003)
-
Vol. 88 (2002)
-
Vol. 87 (2001)
-
Vol. 86 (2000)
-
Vol. 85 (1999)
-
Vol. 84 (1998)
-
Vol. 83 (1997)
-
Vol. 82 (1996)
-
Vol. 81 (1995)
-
Vol. 80 (1994)
-
Vol. 79 (1993)
-
Vol. 78 (1992)
-
Vol. 77 (1991)
-
Vol. 76 (1990)
-
Vol. 75 (1989)
-
Vol. 74 (1988)
-
Vol. 73 (1987)
-
Vol. 72 (1986)
-
Vol. 71 (1985)
-
Vol. 70 (1984)
-
Vol. 69 (1983)
-
Vol. 68 (1982)
-
Vol. 67 (1981)
-
Vol. 66 (1980)
-
Vol. 65 (1979)
-
Vol. 64 (1978)
-
Vol. 63 (1977)
-
Vol. 62 (1976)
-
Vol. 61 (1975)
-
Vol. 60 (1974)
-
Vol. 59 (1973)
-
Vol. 58 (1972)
-
Vol. 57 (1971)
-
Vol. 56 (1970)
-
Vol. 55 (1969)
-
Vol. 54 (1968)
-
Vol. 53 (1967)
-
Vol. 52 (1966)
-
Vol. 51 (1965)
-
Vol. 50 (1964)
-
Vol. 49 (1963)
-
Vol. 48 (1962)
-
Vol. 47 (1961)
-
Vol. 46 (1960)
-
Vol. 45 (1959)
-
Vol. 44 (1958)
-
Vol. 43 (1957)
-
Vol. 42 (1956)
-
Vol. 41 (1955)
Keyword Ranking
04 Sep. (Last 30 Days)
Tetsu-to-Hagané Vol. 71 (1985), No. 1
Influence of Hot Metal Flow on the Heat Transfer in a Blast Furnace Hearth
Jiro OHNO, Masaharu TACHIMORI, Masakazu NAKAMURA, Yukiaki HARA
pp. 34-40
Abstract
The influence of hot metal flow on the heat transfer in a blast furnace hearth was studied by the flow calculation, the water model experiment and the investigation of wear profiles of dissected hearth.
The hearth flow can be classified into the one in a uniformly packed hearth of coke with good permeability and the one in a hearth having a coke free space at the bottom part of it. The result of water model experiment shows that the heat transfer of the former is similar to that of the cyrindrical packed bed, and that of the latter the laminar flow within parallel plates.
By virtue of these similarities, the heat conductance of a packed hearth can be expressed as the function of the dimension of hearth, the flow rate as well as the thermal properties of fluid. The heat conductance of real furnaces can be shown as
h=(14.2/d)+(6.3/D+1.7/d2)(Q/D),
where h is the heat conductance (kcal/m2 h°C), d is the depth of iron pool (m), D is the diameter of hearth (m) and Q is the tapping rate (t/h).
The wear level at the bottom part of carbon hearth can be calculated from h thus obtained. Good agreement has been confirmed between the calculated wear level and the observed ones at dissected hearths.
Readers Who Read This Article Also Read
Tetsu-to-Hagané Vol.62(1976), No.14
Tetsu-to-Hagané Vol.73(1987), No.15
Tetsu-to-Hagané Vol.78(1992), No.7
Burden Distribution in Shaft Furnace for Direct Reduction of Iron Ores
Shoichi KUME, Kunio HACHISUKA, Takashi SUGIYAMA, Toru WAKABAYASHI, Rikuo KAHARU, Yoshisato SUGA
pp. 41-46
Abstract
Experiment was conducted with a 45°segment full-scale model to investigate the burden distribution in direct reduction shaft furnaces equipped with the charging pipe. The findings are as follows :
1) The charged material moves from the charging pipe first in a pushing flow like a landslide and then in a rolling flow toward the wall.
2) Size segregation occurs in the rolling flow through a percolation process, while less segregation in the pushing flow.
3) The size distribution can be expressed as relative distance of charged material movement irrespective of throat diameter.
4) High content of fine particle in lump ore layer remarkably increases the gas permeability resistance around the charging pipe.
Readers Who Read This Article Also Read
Tetsu-to-Hagané Vol.61(1975), No.7
ISIJ International Vol.41(2001), No.Suppl
Tetsu-to-Hagané Vol.72(1986), No.7
A Simulation Model for Gas Flow in Direct Reduction Furnace for Iron Ores
Shoichi KUME, Takashi SUGIYAMA, Yasuto SHIMOMURA, Yoshisato SUGA, Kunio HACHISUKA, Tooru WAKABAYASHI
pp. 47-54
Abstract
Based on the previous research on the blast furnace simulation, a gas flow simulation model for direct reduction shaft furnaces which are free of a coke layer and operated by a fixed charging cylinder system was developed. In order to derive the calculation formula, experiments were conducted using a burden distribution model for the fixed charging cylinder system mentioned above to analyze the characteristic features of the furnace. Radial distributions of particle diameter and void fraction were considered for the estimation of gas velocity distribution in this model. The results obtained by this simulation system agreed well with those acquired in actual operation of a 500 t/d furnace.
Solubility and Dissolution Rate of Water Vapor in Liquid CaO-SiO2-Al2O3 Slags
Shiro BAN-YA, Yasutaka IGUCHI, Shunsuke NAGATA
pp. 55-62
Abstract
The solubility of water vapor and the rate of water vapor dissolution in liquid CaO-SiO2-Al2O3 slags have been measured at 1 400°C by a sampling method.
From the results obtained, solubilities of water in slags were shown with water-vapor capacity, defined by K' =(%H2O)s/√PH2O.
The apparent rate of water vapor dissolution was independent of the flow rate of Ar-H2O gas mixture over the range of 200910 ml/min. The dissolved water content was a linear function of the square root of time during the initial period of dissolution with a slope proportional to the square root of PH2O in the gas.
Consequently, the reaction would be controlled by the non-steady-state diffusion of H2O in the bulk slag. The obtained apparent diffusion coefficient of water vapor, DH2O, in 44 mol% CaO-44 mol%SiO2-12 mol%Al2O3 slag at 1 400°C was 1.9×10-5 cm2/s. The effects of slag composition, such as alumina content or basicity and temperature on DH2O were discussed.
Rate of Dephosphorization of Liquid Iron by the Flux of Na2O-SiO2 System
Kyoji KUNISADA, Hikoya IWAI
pp. 63-69
Abstract
The experiments of the dephosphorization of liquid iron by Na2O-SiO2 flux containing Fe2O3 were carried out at temperatures of 1 550, 1 600 and 1 650°C, and kinetics of the reaction was studied.
The distribution ratio of phosphorus obtained from the experiments was expressed as follow :
log LP=log (%P)/[%P]=0.092(%Na2O)+2.5 log(%FetO)-3.79 (1 600°C)
The rate of dephosphorization was analysed on the assumption that the reaction was first order, and the reaction rate constant obtained was 0.12-2.40 ×10-2 cm/s. The apparent activation energy of the reaction obtained was 13-34 kcal/mol. The reaction rate constant showed a strong correlation with the distribution ratio of phosphorus obtained from the experiment.
The diffusion of phosphorus from slag-liquid iron interface to slag phase was considered as the ratedetermining step in the dephosphorization reaction.
Readers Who Read This Article Also Read
Tetsu-to-Hagané Vol.71(1985), No.6
Rate of Absorption of Injected Nitrogen in Molten Iron
Korehito KADOGUCHI, Masamichi SANO, Kazumi MORI
pp. 70-77
Abstract
A study was made on the rate of absorption of injected nitrogen in molten iron. Nitrogen was injected into the melt through an immersed alumina nozzle of 0.1 cm in I. D. and 0.3 cm in O. D. The immersion depth of the nozzle was 3.34.7 cm. The gas flow rate was 1.121.67 Ncm3/s. The oxygen and sulfur concentrations in the melt were varied widely. During the nitrogen absorption experiment, the bubble formation time was measured by using a pressure pulse technique.
The measured rate data are compared with calculations from a mixed control model of liquid-phase mass transfer and chemical reaction at the bubble-metal interface. Nitrogen absorption during bubble formation is taken into account in the model. From the comparison between calculation and experiment, the chemical reaction rate constant is obtained. It is shown that the chemical reaction rate constant decreases with increasing [%O]+[%S]/2. The rate constant for the bubble interface roughly agrees with that for the free surface of melt.
Prediction of the Formation Region of Eutectic NbC in a Large 12Cr-Mo-V-Nb Steel Ingot
Kimihiko AKAHORI, Shigeo MAENO, Hideyo KODAMA, Norio MORISADA, Toshihiko OSHIMA
pp. 78-84
Abstract
The purpose of this study is to predict the formation region of eutectic NbC in large ingots and to eliminate its detrimental effects. The correlation between the formation region of eutectic NbC and the ratio of the height H to the diameter D (H/D) was investigated experimentally using ingots of 2 t and 10 t and the temperature gradient at the end of solidification in these ingots was calculated by a finite difference method.
The plots of the logarithm of the critical temperature gradient for the formation of eutectic NbC which was obtained experimentally against the logarithm of the calculated average cooling rate during solidification yielded a straight line. It was predicted from this result that when casting a 100 t ingot eutectic NbC would not be formed if the value of H/D is less than 0.6 and magnetic particle test indication would not be detected if the value of H/D is less than 1.0. A 100 t ingot having ratio H/D of 0.96 was made and a turbine rotor shaft was produced from this ingot. The center core portion of the rotor shaft had satisfactory mechanical properties and no indication of defects was detected by magnetic particle testing.
The Effect of Tensile Strength and Ductility on High Temperature Low Cycle Fatigue of Cast Ni-base Superalloys
Hidehiro ONODERA, Yoshihito RO, Toshihiro YAMAGATA, Michio YAMAZAKI
pp. 85-91
Abstract
The effect of tensile strength and ductility on high temperature low cycle fatigue of cast Ni-base superalloys was studied. The main results obtained are as follows :
(1) At total strain ranges above 0.01, where plastic fatigue was dominant, fatigue lives of high ductility alloys (MM247 as cast and HT, IN738LC as cast, TM-321 HT, HT standing for heat-treated) were longer than those of low ductility alloys (TM-185 as cast, TM-49 as cast). At total strain ranges below 0.005, where elastic fatigue was dominant, fatigue lives of high strength alloys (TM-185 as cast, TM-321 as cast and HT, MM247 as cast and HT) were longer than those of low strength alloy (IN738LC as cast).
(2) High temperature low cycle fatigue lives of cast Ni-base superalloys could be roughly estimated by the Universal Slope method combined with 10% rule.
(3) Fatigue crack was considered to initiate at the surface-connected grain boundary, and crack propagation was mixture of intergranular and transgranular types.
(4) In the long life range, preferential oxidation of surface-connected grain boundaries was considered to reduce fatigue life.
The Role of Simulated HTGR Helium on the Low Cycle Fatigue Behavior of Ni-Cr-W Alloys
Kazuo FURUYA, Kouichi SATO, Toshio KAINUMA, Heitarou YOSHIDA
pp. 92-99
Abstract
Low cycle fatigue behavior of two Ni-Cr-W alloys (Ni-15Cr-25W (KSN) and Ni-23Cr-18W (113MA)) was investigated at 1 273 K in the simulated High Temperature Gas-cooled Reactor (HTGR) helium, He-2. Both alloys showed little cyclic hardening in fatigue tests and failed in a completely intergranular manner. Although the fatigue life (Nf) of 113MA was a little longer than that of KSN, observed intergranular fractures indicated that the fatigue properties of both alloys were severely influenced by impurities in He-2.
As well as in He-2, fatigue tests of KSN and 113MA were carried out in pure He, air and vacuum. The results clearly showed that, regardless of the concentration of reactive gases, both alloys failed intergranularly with short Nfs in gaseous environments, as compared with the transgranular fracture with long Nf in vacuum. A minor effect of impurity contents was shown as an increase in Nf with substituting the environment from air then He-2 to pure He. It is considered from these behaviors that the fatigue fractures were affected by residual oxygen gas in the environments penetrating into specimens along the grain boundaries.
Properties of Induction Heat-treated High Strength Spring Wire
Kazuhiro KAWASAKI, Yoshiki SETO, Takao YAMAZAKI
pp. 100-106
Abstract
Induction heat-treatment technique has been applied to develop a new high strength Si-Cr steel (SAE 9254) spring wire. The features of this technique are : (1) uniform heating (by rapid heating and holding) and (2) short heating time.
The induction-heating, quenched and tempered wires (ITW) with diameter of 12 mm show fine micro structure, fine austenite grains and less decarburization. The ITW have very high tensile strength from 1 770 to 2 060 MPa, and also show high ductility and toughness. These properties are attributed to their fine microstructure and non-equilibrium tempering effect with short induction heating time for tempering, and provide excellent cold formability.
Coil springs cold-coiled from the ITW possess sufficient sag resistance and fatigue life. As no decrease in fatigue life is observed even at such high strengths, advantage can be taken of the fact that sag resistance rises with the increase in tensile strength. Since maximum stress of coil spring can be raised by using the ITW, considerable weight saving becomes possible.
Readers Who Read This Article Also Read
Tetsu-to-Hagané Vol.74(1988), No.2
ISIJ International Vol.53(2013), No.4
ISIJ International Vol.54(2014), No.7
Effects of Alloying Elements on Embrittlement of 15Cr-26Ni-1.25Mo Type Precipitation Hardening Alloy
Katsumi IIJIMA, Norio YAMADA, Seishin KIRIHARA
pp. 107-113
Abstract
The object of this study is to characterize the effect of alloying elements on the toughness of 15Cr-26Ni-1.25Mo type alloy steels (A286) aged at 650°C.
The results obtained are summerized as follows.
(1) The Charpy absorbed energy of 15Cr-26Ni-1.25Mo type alloy steels aged at 650°C was decreased with increasing C content. This fact suggestes that aging embrittlement closely depended on C content.
(2) Precipitates were found on the grain-boundaries of the alloys aged at 650°C for 1 500h. Microscopic examination indicated that these precipitates grew as aging time increased. Auger electron spectroscopy showed that titanium carbides were included in the precipitates.
(3) Decreases of C to 0.03wt% and Ti to 1.65wt% were beneficial in keeping good Charpy absorbed energy the value of 35 to 55 N-m in the specimens aged for 6 000h at 650°C, without reduction of creep rupture strength at 650°C.
Readers Who Read This Article Also Read
Tetsu-to-Hagané Vol.67(1981), No.1
Tetsu-to-Hagané Vol.71(1985), No.2
Tetsu-to-Hagané Vol.70(1984), No.5
Creep Fracture Mechanism Maps Based on Creep Rupture Tests up to about 100 000 h for Type 316 Stainless Steel
Norio SHINYA, Hideo TANAKA, Masaharu MURATA, Masatsugu KAISE, Shin YOKOI
pp. 114-120
Abstract
Specimens of Type 316 stainless steel with rupture periods up to about 100 000h have been examined. metallographically in order to clarify creep fracture mechanisms and effects of microstructure on the mechanisms.
Main results obtained are as follows.
(1) Creep fracture mechanism maps constructed experimentally show the fields of dominance of each fracture mechanism : transgranular creep fracture, wedge-type cracking at triple point, intergranular cavitation, and cracking at interface between intermetallic phases and austenite matrix. The maps also indicate that this steel in power plants is used within the field of the cracking due to the intermetallic phases of sigma and chi.
(2) The creep fracture mechanisms are subject to the influence of precipitation behavior at grain boundary: grain boundary M23C6 promotes the transition from the wedge-type cracking to the intergranular cavitation, and grain boundary sigma or chi phases lead to the grain boundary cracking.
(3) Higher aluminum content than about 0.03% leads to the precipitation of AlN associated with the grain boundary sigma or chi phases, and this AlN is thought to cause early formation of the grain boundary cracks, resulting in the marked reductions in rupture strength and ductility at longer time.
Readers Who Read This Article Also Read
ISIJ International Vol.45(2005), No.2
Tetsu-to-Hagané Vol.71(1985), No.2
Tetsu-to-Hagané Vol.70(1984), No.7
Service Life Prediction of Industrial Pipe-line
Kazuo YAMAMOTO, Shigeru MIZOGUTI, Shinichiro NAGANO, Kunimasa YOSHIMITU, Etsuo NOMURA
pp. 121-126
Abstract
To perform the water-leak protection and effective renewal of industrial pipe line, the life-time prediction has been discussed on the basis of the measurements of the wall thickness of pipes in service. The followings are concluded : (1) the life time of a pipe line in inside corrosion can be predicted from the maximum pitting depth estimated by the extreme value statistical analysis of the data obtained from the relation between corrosion pit depth and rust-lump height. (2) the grooving depth of ERW pipes can be measured by the ultrasonic angle beam testing method quantitatively. If the supply water is drained, the estimation of the grooving depth is qualitatively made by means of the X-ray transmission method.
Readers Who Read This Article Also Read
Tetsu-to-Hagané Vol.77(1991), No.1
ISIJ International Vol.44(2004), No.2
Tetsu-to-Hagané Vol.67(1981), No.9
Solidification Behavior of a Nickel-base Superalloy, IN-100
Yoshinori MURATA, Natsuo YUKAWA, Toshiharu NODA, Takashi MITANI
pp. 127-134
Abstract
Solidification behavior of IN-100 and effect of alloying elements on it were investigated by means of differential thermal analysis (DTA), microstructural observation, X-ray diffraction, and EPMA analysis.
In alloy IN-100, it was revealed that six phase reactions took place successively during cooling from melt. These reactions and the onset temperatures were as follows, 1) L→γ(1 329°C), 2) L→γ+MC(D) (1319°C), 3) L→γ+MC(ID) (1 310°C), 4) L→γ+γ' (1 259°C), 5)γγ'→(1 210°C), and 6) L→γ+M3B2 (1 200°C), where L is melt, γ is fcc phase. MC(D) and MC(ID) denote MC carbides formed among dendrite arms and interdendritic regions, respectively. γ' is Ll2 type ordered phase and M3B2 denotes boride phase.
The occurrence of two kinds of carbide reactions ((2) and (3)) and M3B2 eutectic reaction ((6)) was identified for the first time in this study. SEM observation on the carbides, which were embossed on the γ matrix by an electrolytic etching, showed that the carbides had three types of morphology. These were blocky, lattice-like and flaky in shape. It was found that the blocky carbides were contained in MC(D), while the lattice-like and flaky carbides were frequently found in MC(ID). The influence of C, Al, Ti, and B on the above phase reactions and solidified structure was also clarified.
抄録
中島 一磨, 小林 睦弘, 磯部 浩一, 渡辺 健彦, 矢萩 正人, 宮地 博文, 望月 俊男, 長谷川 晃
pp. 139-141
Readers Who Read This Article Also Read
Tetsu-to-Hagané Vol.47(1961), No.10
Tetsu-to-Hagané Vol.51(1965), No.10
Tetsu-to-Hagané Vol.62(1976), No.1
Article Access Ranking
04 Sep. (Last 30 Days)
-
Perspectives on the Promising Pathways to Zero Carbon Emissions in the Steel Industry toward 2050
ISIJ International Vol.65(2025), No.2
-
Growth, Removal, and Agglomeration of Various Type of Oxide Inclusions in Molten Steel
Tetsu-to-Hagané Vol.111(2025), No.11
-
Finite Element Analysis of Bubble Growth and Particle Swelling during Coal Pyrolysis
ISIJ International Vol.65(2025), No.9
-
Interface behavior leading to Al/Cu dissimilar metal bonding formation with high-speed eutectic reaction induced by applying current
QUARTERLY JOURNAL OF THE JAPAN WELDING SOCIETY Vol.43(2025), No.2
-
Corrosion Behavior of Carbon Steel under Soil Drying Conditions
ISIJ International Advance Publication
-
Cold Spot Joining of 980 MPa-class Ultra-high Strength Steel
Tetsu-to-Hagané Advance Publication
-
Combination Effect of Premixing Conditions and Iron Ore Size Distribution in Sintered Ore Granulation Process with Intensive Mixer
ISIJ International Advance Publication
-
A preliminary study on reduction degradation of iron ore sinter using sinter analogue and X-ray micro-computed tomography (MCT)
ISIJ International Advance Publication
-
Copper removal of liquid steel containing 0.25 % carbon using Fe2O3-CaCl2-SiO2 flux
ISIJ International Advance Publication
-
Evaluation of Feature Selection Methods for Oxygen Supply Prediction in BOF Steelmaking
ISIJ International Advance Publication
You can use this feature after you logged into the site.
Please click the button below.