- TOP
- Tetsu-to-Hagané
- Vol. 61 (1975), No. 6
Tetsu-to-Hagané Vol. 61 (1975), No. 6
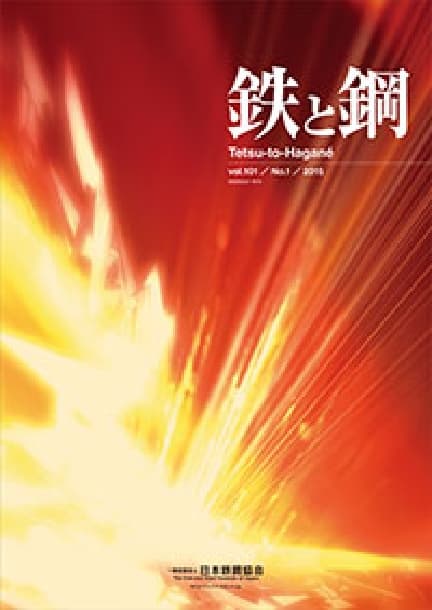
Grid List Abstracts
ONLINE ISSN: | 1883-2954 |
PRINT ISSN: | 0021-1575 |
Publisher: | The Iron and Steel Institute of Japan |
Backnumber
-
Vol. 111 (2025)
-
Vol. 110 (2024)
-
Vol. 109 (2023)
-
Vol. 108 (2022)
-
Vol. 107 (2021)
-
Vol. 106 (2020)
-
Vol. 105 (2019)
-
Vol. 104 (2018)
-
Vol. 103 (2017)
-
Vol. 102 (2016)
-
Vol. 101 (2015)
-
Vol. 100 (2014)
-
Vol. 99 (2013)
-
Vol. 98 (2012)
-
Vol. 97 (2011)
-
Vol. 96 (2010)
-
Vol. 95 (2009)
-
Vol. 94 (2008)
-
Vol. 93 (2007)
-
Vol. 92 (2006)
-
Vol. 91 (2005)
-
Vol. 90 (2004)
-
Vol. 89 (2003)
-
Vol. 88 (2002)
-
Vol. 87 (2001)
-
Vol. 86 (2000)
-
Vol. 85 (1999)
-
Vol. 84 (1998)
-
Vol. 83 (1997)
-
Vol. 82 (1996)
-
Vol. 81 (1995)
-
Vol. 80 (1994)
-
Vol. 79 (1993)
-
Vol. 78 (1992)
-
Vol. 77 (1991)
-
Vol. 76 (1990)
-
Vol. 75 (1989)
-
Vol. 74 (1988)
-
Vol. 73 (1987)
-
Vol. 72 (1986)
-
Vol. 71 (1985)
-
Vol. 70 (1984)
-
Vol. 69 (1983)
-
Vol. 68 (1982)
-
Vol. 67 (1981)
-
Vol. 66 (1980)
-
Vol. 65 (1979)
-
Vol. 64 (1978)
-
Vol. 63 (1977)
-
Vol. 62 (1976)
-
Vol. 61 (1975)
-
Vol. 60 (1974)
-
Vol. 59 (1973)
-
Vol. 58 (1972)
-
Vol. 57 (1971)
-
Vol. 56 (1970)
-
Vol. 55 (1969)
-
Vol. 54 (1968)
-
Vol. 53 (1967)
-
Vol. 52 (1966)
-
Vol. 51 (1965)
-
Vol. 50 (1964)
-
Vol. 49 (1963)
-
Vol. 48 (1962)
-
Vol. 47 (1961)
-
Vol. 46 (1960)
-
Vol. 45 (1959)
-
Vol. 44 (1958)
-
Vol. 43 (1957)
-
Vol. 42 (1956)
-
Vol. 41 (1955)
Keyword Ranking
06 Sep. (Last 30 Days)
Tetsu-to-Hagané Vol. 61 (1975), No. 6
The Shrinkage of Burden Materials and Pressure Drop of Gas in Softening and Fusing Zones of Blast Furnace
Katsuya ONO, Yukihiro HIDA, Akitoshi SHIGEMI, Koretake KODAMA
pp. 777-786
Abstract
The behavior of burden materials in the softening and fusing zones in the blast furnace was investigated using sinters and pellets under the condition simulating the blast furnace.
Materials with higher basisity showed less degrees of shrinkage at the same elevated temperature and begin to melt and drop at higher temperatures than materials with low basisity, because the materials with higher basisity have higher melting points. The degree of shrinkage of the materials studied was 70-90%, when they began to melt down.
An experiment for pressure drop of gas through the shrinkaged material was carried out and the following equation was presented;
K=K010α0 where. K: index of permeability resistance of softened material K0: index of permeability resistance before shrinkage
σ: degree of shrinkage
α: constant determined by the brand and size of the material
Using this equation, some consideration was tried for the pressuse drop of gas in the softening and fusing zones in the actual blast furnac.
Readers Who Read This Article Also Read
Tetsu-to-Hagané Vol.54(1968), No.3
Tetsu-to-Hagané Vol.57(1971), No.4
Tetsu-to-Hagané Vol.57(1971), No.11
A Mathematical Model for Blast Furnace Operation with Inclined Layers of Burdens
Mamoru KUWABARA, Iwao MUCHI
pp. 787-796
Abstract
A mathematical model of the blast furnace with the layered coke and are burdens in which the thickness of each layer varies in the radial direction has been developed over the region from the toplevel to the melting zone of the furnace.
On the basis of this model, the longitudinal and radial distributions of the process variables, such as temperature, gas composition, gas velocity, and fractional reduction of ironre, in an existing blast furnace in Japan, B. F.(D II), have been analized with the aid of a digital compute.
It is found from the calculated results that the radial distributions of the process variables mentioned above and the melting level are remarkably uneven in B. F.(D II), and are similar to the results observed by the other investigators.
The Influence of Kind of Deoxidizer on Rimming Action
Kazuo OKOHIRA, Minoru IWAMOTO, Hisashi MORI
pp. 797-807
Abstract
The influence of various deoxidizers on the rimming action was studied by making 330 kg ingots.
Each deoxidizer was used only during the teeming of an ingot, without the addition of deoxidizers during tapping.
The state of rimming action, the quantity of foam in the soldifying liquid steel, the structure of the ingot, the degree of the negative segregation of carbon in the rim zone, and the characters of deoxidation-products were observed.
It was found that the deoxidizers were classified into the two groups, rimming-promoting deoxidizers and rising-promoting ones, from the different influence on the rimming action.
We presumed that this difference was caused by the different influence of these deoxidation-products on the life of the foam in the liquid steel, which came from the difference of the melting point of each deoxidation-product.
Readers Who Read This Article Also Read
Tetsu-to-Hagané Vol.60(1974), No.11
Tetsu-to-Hagané Vol.60(1974), No.13
Tetsu-to-Hagané Vol.61(1975), No.4
The Effect of Degree of Spheroidization on the Cold Forgeability of Steel
Tsuyoshi INOUE, Yoshitaka OCHIDA, Shushi KINOSHITA
pp. 808-816
Abstract
The cold forgeability has been studied using a medium carbon steel, (0.48%C), spheroidizeannealed to give a wide variation of degree of spheroidization.
The degree of spheroidization varies with the temperatures and insufficient degrees are brought about with both higher and lower temperatures than the optimum. A spheroidization treatment with lower temperatures gives the structure containing the unresolved pearlite, whereas the treatment with higher temperatures reforms well-defined pearlite.
The degree of spheroidization has a minor effect on the deformation resistance (strength), it, however, has a pronounced effect on the formability (ductility). Although the unresolved pearlite deteriolates the ductility to a less extent, the reformed pearlite impairs it noticeably.
The microscopic observation has been carried out by means of scanning electron microscopy on the ductile fracture process to interpret the results mentioned above. The observation substantiates that voids associated with fully or partially spheroidized carbides tend to grow separately along the tensile axis and to consume a considerable amount of the strain to fracture after void initiation. On the other hand, voids with reformed pearlite are ready to grow to the size as large as pearlite nodules and to propagate in the transverse direction.
The difference in ductile fracture behavior is expected to account for the effect of degree of spheroidization on ductility.
Readers Who Read This Article Also Read
Tetsu-to-Hagané Vol.84(1998), No.10
The Production of Cold Rolled Steel Sheet of Extra Deep Drawing Quality by Continuous Annealing Process
Nobuo FUKUDA, Mineo SHIMIZU
pp. 817-827
Abstract
The Ti-stabilized steel has a uniform distribution of very fine precipitates (TiC) already in the hot rolled state. These prior precipitates are effective in developing a strong {111} recrystallization texture on annealing after cold rolling, and the slow heating up to annealing temperature such as undertaken for Al-killed steel to get effective precipitates or pre-precipitation clusters is not necessary forTi stabilized steel. Lowering carbon content of the steel to less than 0.01% results in great increases of the grain size and γ value in a very short time with the raising annealing temperature. The Tistabilized very low carbon steel (e. g., 0.005%C-0.1%Ti) therefore can get a very high γ value of above 2.0 even by applying a rapid annealing cycle with heating rates of 104 to 105°C/sec and with soaking times within a few minutes.
Quench-aging does not occur at all in Ti-stabilized steel rapidly cooled from annealing temperature, as the carbon (and nitrogen) in the steel is stabilized with titanium. Then continuous-annealed Tistabilized steel is non-aging and very soft without over-aging treatment.
The Ti-stabilized very low carbon steels is the most suitable to get a non-aging steel sheet having an extra deep drawing quality by the continuous annealing process
Readers Who Read This Article Also Read
ISIJ International Vol.57(2017), No.7
The Influence of Reduction-Ratio in the Hot-Rolling on the Strength and Toughness of Quenched and Tempered Steel
Seiichi WATANABE, Tatsuro KUNITAKE
pp. 828-840
Abstract
The influence of reduction-ratio in the hot-rolling on the microstructure and mechanical properties of quenched and tempered low C, 3.5%Ni steel was investigated and the following conclusions were obtained;
The average γ grain size became finer with increasing reduction-ratio but, the grains were more elongated in their shape in the rolling-direction. With increasing reduction-ratio, the unit crack path (U. C. P.) observed in the fractured surface of longitudinal Charpy V-notch specimen became finer, while U. C. P. in the transverse specimen changed less evidently. The fracture appearance transition temperature in the longitudinal specimen behaved similarly to that of U.C.P. with increasing reductionratio.
The difference in the unit crack path and shape of non-metallic inclusions between longitudinal and transverse direction brought about the directional difference in Charpy transition temperature.
The upper and lower yield point in the stress-strain curve separated more appreciably with increasing reduction-ratio from 1 to 8. This is due to the fact that the inhomogeneity in the cast structure such as micro-segregation was leveled out and consequently the difference of tensile strength at various locations disappeared.
Both columnar and equiaxed zones in the cast structure responded similarly to the reduction-ratio, but the quantity of non-metallic inclusion was larger in equiaxed zone with the consequence of some what inferior ductility in the latter. The orientation of reduction with respect to the columnar axis in the cast structure had no appreciable influence on the various properties.
Delayed Failure Characteristics of Ultra High Strength Steels
Fukukazu NAKASATO, Fukunaga TERASAKI
pp. 841-855
Abstract
The effects of heat treatment on the characteristics of delayed failure crack propagation were investigated in 0.02N-HCI aqueous solution at room temperature using centre-notched specimens of SCM3 and 18Ni-maraging steels. Crack growth rate was directly measured by optical observation and was interpreted in terms of crack tip stress intensity factor KI.
When tempered at 300 and 400°C, SCM3 showed marked increase in crack growth rate in addition to the deterioration in Charpy impact toughness, although tensile strengthdecreased gradually with increasing tempering temperature. Transmission electron microscopy and fractography by SEM suggested that this increase of susceptibility to delayed failure is due to theprecipitation of film-like carbide along prior-austenite grain boundaries at above-mentioned tempering temperatures, which resulted in the formation of typical intergranular fracture surface at intermediate KI value in contrast with the duplex intergranular-transgranular fracture surface observed in the specimen tempered at other temperatures.
In the case of 18Ni-maraging steel, aging at temperatures above 500°C gave the best combination of strength and resistance to delayed failure and crack initiation was suppressed when aged at 600°C. But as the aging temperature decreased below 450°C, crack growth rate became comparable with that of SCM3 with identical tensile strength.
Thus, crack growth rate of delayed failure is not necessarily related to the tensile strength, toughness or ductility of steel, but can be affected by the variation of microstructures depending on the condition of heat treatment.
Delayed Fracture Characteristics of Tempered Bainitic (BIII-type) and Tempered Martensitic Steels
Fukukazu NAKASATO, Fukunaga TERASAKI
pp. 856-868
Abstract
The influence of cementite morphology on the delayed fracture characteristics of medium-carbon low-alloy high strength steels was investigated in 0.1N-HCl aqueous solution at room temperature.
Three different types of test were made depending on the characteristic values of delayed fracture in question. The variation of carbide morphology was attained by two kinds of heat treatment. One is isothermal transformation followed by tempering and the other quench-tempering which formed tempered bainite (BIII-type) and tempered martensite with same tensile strength respectively.
There was no remarkable difference in threshold stress intensity factor KISCC and the ratio of incubation time τi to total time to fracture tF between the two structures. In regard to crack propagation rate dC/dt, however, tempered bainite (BIII-type) showed much smaller value than tempered martensite, which resulted in longer time to fracture in tempered bainite.
With KI around KISCC typical prior-austenite grain boundary fracture was found in both structures but with increased KI, the fraction of quasi-cleavage fracture surface increased in tempered bainite (BIII-type), while in tempered martensite the intergranular fracture still remained dominant with increasing KI. Reduced susceptibility to intergranular cracking with intermediate KI value in tempered bainite (BIII-type) is likely to be due to the suppression of cementite precipitation along prior-austenite grain boundaries as shown by transmission electron microscopy, resulting in the reduced crack propagation rate.
Readers Who Read This Article Also Read
Tetsu-to-Hagané Vol.82(1996), No.11
Study on the Formation of Scale Layer on Work Rolls in Hot Rolling
Yasuhiro SEKIMOTO, Morimichi TANAKA, Tadayoshi YOSHIMURA
pp. 869-874
Abstract
In hot strip mill, the surface of steel based Adamite work rolls are covered with black scale layer, which is considered to be mainly Fe3O4. It has been reported that the scale layer was transfered from rolled stock or was the oxide of roll material. To study the formation mechanism of scale layerappearing on work rolls, experiments have been done using a model four-high rolling mill with scale breaker, and the results has been discussed. Main experimental results are as follows:
1) In the case of rolling without descaling or taking long time after descaling, work rolls were not covered with black scale layer without regard to water cooling on work rolls.
2) In the case of rolling with descaling rolled stock and water cooling on work rolls, steel based adamite and stainless steel work rolls were covered with black scale layer.
Prior mechanism does not explain the results of experiment. Then, the following mechanism can be proposed. The scale layer on work rolls is formed by corrosion reaction between water and rolled stock of metallic state in roll gap; the scale layer is composed of the most part of magnetite produced by the following reaction; Fe+2H2O→Fe (OH) 2+H2 and 3Fe (OH) 2→Fe3O4+2H2O+H2, that is 3Fe+4H2O, Fe3O4+4H2
Study on the Brittle Fracture Propagation-arrest Characteristics of Low C-Ni Steel Plates by Tapered Double Cantilever Beam Test
Shigeo HASEBE, Yoshiaki KAWAGUCHI
pp. 875-883
Abstract
Brittle fracture propagation-arrest characteristics of low C-Mn steel plates containing 0-5%Ni have been investigated by newly developed Tapered Double Cantilever Beam Test, which is a small size test having good correlation to large size Double Tension Test. The results obtained are as follows:
1) Brittle fracture propagation-arrest characteristics are linearly improved with the increase of Ni content, whichever in normalized or quenched and tempered steel plates. Bainitic structure which gives deleterious effect on Charpy impact characteristics do not affect brittle fracture propagation-arrest characteristics.
2) Refinement of microstructure by heat treatment improves greatly Charpy impact characteristics, but very slightly brittle fracture propagation-arrest characteristics.
3) As a whole, brittle fracture propagation-arrest characteristics shows the behavior different from Charpy impact characteristics. The former is sensitive to the change of chemical compositions (Ni content) and insensitive to the change of microstructures (bainitic or refined structures).
Identification of Solidification Structure of Steel Ingots
Koki GUNJI, Taira OKAMOTO
pp. 884-898
Article Access Ranking
06 Sep. (Last 30 Days)
-
Perspectives on the Promising Pathways to Zero Carbon Emissions in the Steel Industry toward 2050
ISIJ International Vol.65(2025), No.2
-
Growth, Removal, and Agglomeration of Various Type of Oxide Inclusions in Molten Steel
Tetsu-to-Hagané Vol.111(2025), No.11
-
Finite Element Analysis of Bubble Growth and Particle Swelling during Coal Pyrolysis
ISIJ International Vol.65(2025), No.9
-
Interface behavior leading to Al/Cu dissimilar metal bonding formation with high-speed eutectic reaction induced by applying current
QUARTERLY JOURNAL OF THE JAPAN WELDING SOCIETY Vol.43(2025), No.2
-
Corrosion Behavior of Carbon Steel under Soil Drying Conditions
ISIJ International Advance Publication
-
Cold Spot Joining of 980 MPa-class Ultra-high Strength Steel
Tetsu-to-Hagané Advance Publication
-
Combination Effect of Premixing Conditions and Iron Ore Size Distribution in Sintered Ore Granulation Process with Intensive Mixer
ISIJ International Advance Publication
-
A preliminary study on reduction degradation of iron ore sinter using sinter analogue and X-ray micro-computed tomography (MCT)
ISIJ International Advance Publication
-
Copper removal of liquid steel containing 0.25 % carbon using Fe2O3-CaCl2-SiO2 flux
ISIJ International Advance Publication
-
Evaluation of Feature Selection Methods for Oxygen Supply Prediction in BOF Steelmaking
ISIJ International Advance Publication
You can use this feature after you logged into the site.
Please click the button below.