- TOP
- Tetsu-to-Hagané
- Vol. 62 (1976), No. 1
Tetsu-to-Hagané Vol. 62 (1976), No. 1
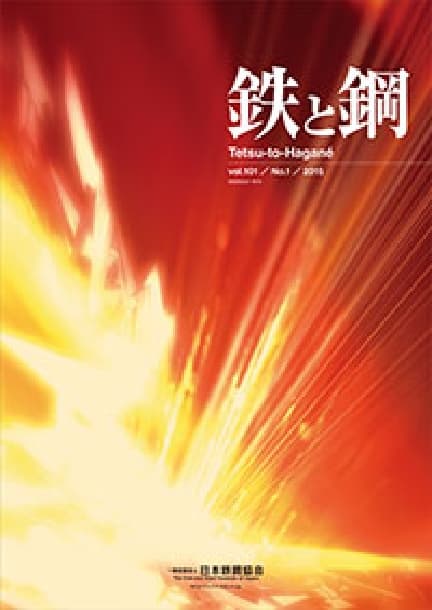
Grid List Abstracts
ONLINE ISSN: | 1883-2954 |
PRINT ISSN: | 0021-1575 |
Publisher: | The Iron and Steel Institute of Japan |
Backnumber
-
Vol. 111 (2025)
-
Vol. 110 (2024)
-
Vol. 109 (2023)
-
Vol. 108 (2022)
-
Vol. 107 (2021)
-
Vol. 106 (2020)
-
Vol. 105 (2019)
-
Vol. 104 (2018)
-
Vol. 103 (2017)
-
Vol. 102 (2016)
-
Vol. 101 (2015)
-
Vol. 100 (2014)
-
Vol. 99 (2013)
-
Vol. 98 (2012)
-
Vol. 97 (2011)
-
Vol. 96 (2010)
-
Vol. 95 (2009)
-
Vol. 94 (2008)
-
Vol. 93 (2007)
-
Vol. 92 (2006)
-
Vol. 91 (2005)
-
Vol. 90 (2004)
-
Vol. 89 (2003)
-
Vol. 88 (2002)
-
Vol. 87 (2001)
-
Vol. 86 (2000)
-
Vol. 85 (1999)
-
Vol. 84 (1998)
-
Vol. 83 (1997)
-
Vol. 82 (1996)
-
Vol. 81 (1995)
-
Vol. 80 (1994)
-
Vol. 79 (1993)
-
Vol. 78 (1992)
-
Vol. 77 (1991)
-
Vol. 76 (1990)
-
Vol. 75 (1989)
-
Vol. 74 (1988)
-
Vol. 73 (1987)
-
Vol. 72 (1986)
-
Vol. 71 (1985)
-
Vol. 70 (1984)
-
Vol. 69 (1983)
-
Vol. 68 (1982)
-
Vol. 67 (1981)
-
Vol. 66 (1980)
-
Vol. 65 (1979)
-
Vol. 64 (1978)
-
Vol. 63 (1977)
-
Vol. 62 (1976)
-
Vol. 61 (1975)
-
Vol. 60 (1974)
-
Vol. 59 (1973)
-
Vol. 58 (1972)
-
Vol. 57 (1971)
-
Vol. 56 (1970)
-
Vol. 55 (1969)
-
Vol. 54 (1968)
-
Vol. 53 (1967)
-
Vol. 52 (1966)
-
Vol. 51 (1965)
-
Vol. 50 (1964)
-
Vol. 49 (1963)
-
Vol. 48 (1962)
-
Vol. 47 (1961)
-
Vol. 46 (1960)
-
Vol. 45 (1959)
-
Vol. 44 (1958)
-
Vol. 43 (1957)
-
Vol. 42 (1956)
-
Vol. 41 (1955)
Keyword Ranking
06 Sep. (Last 30 Days)
Tetsu-to-Hagané Vol. 62 (1976), No. 1
Production and Technology of Iron and Steel
Tsuneyo IKI
pp. 3-24
Readers Who Read This Article Also Read
Tetsu-to-Hagané Vol.60(1974), No.14
Tetsu-to-Hagané Vol.61(1975), No.3
Tetsu-to-Hagané Vol.62(1976), No.1
An Experimental Study of the Formation of Raceway Using a Cold Model
Michiharu HATANO, Mitsuichiro FUKUDA, Masayuki TAKEUCHI
pp. 25-32
Abstract
The raceway formed in front of a tuyere is one of decisive factors to operate a blast furnace stably and efficiently, because the gas distributions from the raceway and the descent of the burden are greatly affected by the characteristics of the raceway.
There are, however, many unknown facts about the formation of the raceway and incidental phenomena. This study has been carried out for the purpose of solving some of them using a cold model and an experimental blast furnace.
In this paper, some results obtained through cold model experiments are presented.
The summary of the results is as follows:
1) Particles in the raceway rotate around at high speed, colliding with rotating particles or the raceway wall and some of them are reduced in size.
2) A lot of fine particles formed in the raceway accumulates on the surface of the raceway in front of the tuyere.
3) Under a condition of reduced particle size in front of tuyere, the raceway is enlarged, especially upwards along the furnace wall.
4) The depth of the raceway can be expressed by the relationship between the raceway factor (P·V2·ρgo/g·ds·ρs·S2) and the penetration factor (DR/DT).
Readers Who Read This Article Also Read
Tetsu-to-Hagané Vol.78(1992), No.1
Tetsu-to-Hagané Vol.62(1976), No.5
Rate of Desulphurization from Liquid Iron and Iron Alloys with Hydrogen
Mitsutaka HINO, Shiro BAN-YA, Tasuku FUWA
pp. 33-42
Abstract
A study has been made of the rate of sulphur removal from liquid iron and iron alloys, containing carbon, silicon, phosphorus, vanadium, and oxygen respectively, by hydrogen as a reaction gas at 1600°C. The results obtained are as follows:
1. The effects of alloying elements on the rate of desulphurization depend on the effect of the activity of sulphur in the liquid iron.
2. The reaction of sulphur removal is of the second-order, and it is considered that the chemical reaction on the surface of liquid iron is the rate-determining step. The rate of the reaction, H2 (gas) +S (in liquid iron) =H2S (gas), is expressed by the following equation:
-d [%S] /dt=A/VK2'PH2aS
where, A and V are the surface area and the volume of liquid iron.
3. The apparent activation energy of the sulphur removal is 11.0Kcal/mol.
4. The surface active element decreases the rate of desulphurization markedly. A mechanism of sulphur removal from liquid iron is proposed to describe the rate of reaction quantitatively, taking into consideration of the effect of the adsorption of the surface active element.
Decarburization and Denitrogenization of Iron and Iron-Chromium Alloys by Plasma Jet of Hydrogen-Argon Gas Mixture
Kyojiro KANEKO, Nobuo SANO, Yukio MATSUSHITA
pp. 43-52
Abstract
Trials to enhance the decarburization and the denitrogenization of molten Fe-Cr alloys were made by blowing plasma jet of argon-hydrogen gas mixture on to the surface of molten metals. The weight of melts was 1 to 3kg, the gas blowing rate 8 t/min and the electric power consumption 15 to 30kVA. The final concentrations of carbon and nitrogen obtained are as follows: C<0.002% for Fe, 18-8 stainless steel, 60% Cr-Fe alloy and Cr, N=0.0015% for Fe and N=0.0065% for 25% Cr-Fe alloy. This satisfies the conditions of intergranular corrosion resistance and ductility, C+N<100-130ppm, for ferritic stainless steel. By estimating the dissociation constant of H2 in plasma jet at the metal surface, it is indicated that hydrogen atoms in the plasma which are not thermally recombined to molecules react with carbon and nitrogen in molten metals. The mechanisms of decarburization and denitrogenization were also discussed.
Surface Tension and Density of FeO-CaO-SiO2 Melts
Yasuji KAWAI, Katsumi MORI, Hiroaki SHIRAISHI, Noboru YAMADA
pp. 53-61
Abstract
The surface tension and density of FeO-CaO, FeO-SiO2, and FeO-CaO-SiO2 melts, CaO content up to 40 mol% and SiO2 up to 50 mol%, in contact with solid iron, have been measured at temperatures from melting points to 1430°C by the maximum bubble pressure method.
Surface tension values of these melts are in the range from 350 to 530 dyn/cm.
Surface tension and density of liquid iron oxides show an abnormal behavior, that is, a positive dependence on temperature. The addition of CaO or SiO2 to iron oxide lead to monotonous decreases of surface tension and density of melts, but the maximum of surface tension is observed in the iso-thermal curve of surface tension of FeO-CaO-SiO2 ternary melts of constant CaO content at 1400°C.
It is found that surface tension values of melts calculated from the equation containing terms of surface tension coefficients and the effect of ferric oxide agree well with the experimental results in the composition range of this experiment.
Molar volumes of FeO-CaO and FeO-30CaO-Si02 melts show negative deviations from ideal mixture of components.
Readers Who Read This Article Also Read
Tetsu-to-Hagané Vol.47(1961), No.14
Tetsu-to-Hagané Vol.48(1962), No.1
Tetsu-to-Hagané Vol.58(1972), No.10
Effect of Hydrogen on Blowhole Formation in Pure Iron during Solidification
Masahiro UDA, Takehiro DAN, Satoru OHNO
pp. 62-71
Abstract
The blowhole formation of the Fe-H system during solidification was investigated.
Pure iron was melted in various hydrogen partial pressures and temperatures by means of the levitation method, and cast into a water-cooled copper mold after equilibrated with the atmosphere. The blowholes in specimens were detected by means of specific gravity, radiograph and cross section methods.
The results were as follows:
The blowhole formation was influenced remarkably by hydrogen partial pressure and melt temperature. The results can be reduced to the simple relation between hydrogen concentration and blowhole formation in specimens. That is, the critical hydrogen concentration for the blowhole formation in specimens was found to be about 13cc/100gFe.
In order that a bubble is present stably in molten iron, the hydrogen concentration in molten iron must be at least 25.2cc/100gFe which is the equilibrium value at PH2=1atm. The above critical hydrogen concentration is lower than this value 25.2 cc/100gFe.
When the increase of hydrogen concentration in front of a solidification interface is considered, the maximum hydrogen concentration can exceed the value 25.2cc/100gFe. The effective distribution coefficient under these experimental conditions was estimated to be higher than the equilibrium one.
Effects of Free-Cutting Additives, Heat-Treated Structures and Cold Working on the Machinability of Low Chromium Case Hardening Steel Based on the Chip-Breaking Characteristics
Toshiro YAMAMOTO, Ken-ichi KUMAGAYI
pp. 72-81
Abstract
Effects of free-cutting additives, heat-treated structures, and cold working on the machinability of low chromium case-hardening steels based on the chip-breaking characteristics have been investigated.
The order of free-cutting additives in decreasing contribution to a favourable broken chip were Bi>Pb>S>Se and Te at the same amount of addition in weight per cent. The effects of P and N on the contribution to a broken chip were comparatively small.
The machinability of case-hardening steels based on the chip-breaking characteristics was the best for spheroidized structure and decreased in the order of annealed structure to normalized structure. Cold working was detrimental to the machinability of spheroidized structure in terms of the chip-breaking characteristics.
The effects of heat-treated structures and cold working on the machinability based on the chip-breaking characteristics is mainly explained by the ratio of the chip thickness to the diameter of a helical chip, i. e., a high ratio provides a favourable broken chip.
Application of the Threshold Stress Intensity Factor KISCC to the Evaluation of the Susceptibility to Delayed Fracture of High Strength Bolts
Fukukazu NAKASATO, Tetsu OHNO
pp. 82-89
Abstract
The fracture mechanics approach was used to analyze the delayed fracture behavior of heat-treated SAE1527 steel with tensile strength of 156kg/mm2. The threshold stress intensity factor KISCC was determined using wedge-loaded DCB specimens in various test environments on the basis of a 5000 hr exposure criterion. Although the incubation time τ1 varied considerably by changes of the test environment, KISCC was found to be virtually independent of the test environment, ranging from 65 to 85kg/mm3/2.
The KISCC values obtained in the present investigation were applied to the design of tightening high strength bolts as an example of structural components subjected to the similar environments. For high strength bolts 22mm in diameter under standard tightening condition, the crack tip stress intensity factor KI for a crack initiating from a thread root was calculated based on a few assumptions. A critical crack length IC which can cause onset of delayed fracture crack propagation at KISCC was about 15 μ which is the same order of length as a prior-austenite grain size of conventionally heat-reated low-lloy steels. Thus it is confirmed that highly stressed and threaded fasteners of low-lloy steels with tensile strength. around 150kg/mm2 and higher are remarkably sensitive to delayed fracture even in an outdoor environment. These results bring about an understanding of in-service failures of high strength fasteners and arise an increasing demand for a strict inspection practice for them.
Readers Who Read This Article Also Read
Tetsu-to-Hagané Vol.77(1991), No.8
ISIJ International Vol.54(2014), No.10
Tetsu-to-Hagané Vol.79(1993), No.7
Strain Partitioning and Void Formation in Ferrite-Pearlite Steels Deformed in Tension
Tsuyoshi INOUE, Shushi KINOSHITA
pp. 90-99
Abstract
A study has been made of the deformation behavior of pearlite nodule and void formation process in the course of tensile deformation of ferrite-pearlite steels containing 0.05 to 0.91 wt%C.
Since pearlite nodule deforms to less extent than matrix, strain partitioning occurs between pearlite nodule and matrix ferrite. The degree of partitioning increases as pearlite volume fraction decreases, which means that the strain of pearlite nodule differs with the volume fraction of pearlite at a given strain of the specimen.
As the deformation of specimen proceeds, void formation occurs at pearlite nodule and the strain at void formation increases with decreasing volume fraction of pearlite. The strain of pearlite nodule at this point, however, is approximately equal (εp=0.3) regardless of the volume fraction of pearlite. Furthermore, the estimated stress to pearlite nodule at void formation is about 110-120kg/mm2 in each steel and this stress corresponds the fracture stress of pearlite nodule.
The results reveal that void formation in ferrite-earlite steel occurs when the strain and/or stress of pearlite nodule reaches to the critical levels relating to the fracture of pearlite nodule per se.
Readers Who Read This Article Also Read
Tetsu-to-Hagané Vol.96(2010), No.6
ISIJ International Vol.41(2001), No.7
Tetsu-to-Hagané Vol.68(1982), No.9
Effect of Cr, Mo and V on Spheroidization of Carbides in 0.8%C Steel
Taira NAKANO, Hiroshi KAWATANI, Shushi KINOSHITA
pp. 100-107
Abstract
Effect of Cr, Mo or V on spheroidization of carbides in 0.8%C steel by slow cooling annealing has been investigated.
An addition of Cr remarkably accelerates spheroidization of carbides, while additions of Mo and V do a little. X-ray and analysis of carbides has indicated that M3C and M7C3 are only carbides observed throughout the annealing process in 2% and 5%Cr steels, respectively. In Mo and V steels, however, carbides formed by eutectoid reaction proved to differ from those surviving in austenite on annealing, that is M23C6 and M3C are eutectoid carbides in Mo and V steels respectively, while Mo2C and VC survive in austenite in Mo and V steels respectively. Although the addition of any of these elements results in increasing amounts of undissolved carbides in austenite, the fact that Cr has a marked effect on spheroidization of carbides strongly suggests that an undissolved particle of carbides in austenite in Cr steels should act as a center for the precipitation of eutectoid carbides since undissolved carbides are identical with eutectoid carbides. Thus it is concluded that identity of carbide precipitating during eutectoid reaction with that surviving in austenite will be of a primary importance in spheroidization of eutectoid carbides by slow cooling annealing.
Effect of Carbon and Titanium Contents on the Oxidation Resistance of Fe-Cr-Al Alloys at High Temperatures
Yuji SHOJI, Shun-ichiro AKIYAMA, Masaru KISAICHI, Kyosuke NAGATOSHI, Hironobu HOSHI
pp. 108-125
Abstract
The oxidation behavior of Fe-18Cr-3Al alloys containing 0.015-0.12% carbon and 0-1.0% titanium has been investigated in air at 1000°C and 1200°C.
At 1200°C carbon and titanium contents have remarkable effects on the oxidation resistance of Fe-Cr-Al alloys, but little effect at 1000°C. Weight gain increases and the formation of unusual oxide scales is accelerated, with increasing carbon content. Though it increases weight gain, the addition of titanium has a tendancy to prevent exfoliation of scales by formation of titanium oxide in scales, and consequently suppresses unusual oxidation.
Stable oxidation is achieved by continuous formation of α-Al2O3, a small amount of TiO2, and Al-Ti oxide. An appearance of iron oxides causes unusual oxidation. The excellent oxidation resistance of Fe-18Cr-3Al alloy is obtained with a carbon content less than 0.03% and titanium content of 0.2 to 0.4%.
Readers Who Read This Article Also Read
Tetsu-to-Hagané Vol.60(1974), No.14
Tetsu-to-Hagané Vol.61(1975), No.3
Tetsu-to-Hagané Vol.62(1976), No.1
Unitized Annealing Department System
Toshio MATSUNAGA, Hiroshi HIRANO, Masuhiro SATO, Ichiro KOKUBO, Kyoichi KATAI, Kazuhiko KOURITA
pp. 126-132
Abstract
In the annealing process of cold rolled strip, the batch annealing has been a prevailing method.
Although several improvements have been made in this field for these twenty years, some difficulties in saving personnel, labour environment, and productivity still remain.
UAD (Unitized Annealing Department) system. was developed to solve these problems in 1966.
The newest system was adopted at Kakogawa Works, Kobe Steel, Ltd. and has been successfully in production.
UAD system consists of loose coiling unit, “VERTOHORT” tight coiling unit, box shaped furnaces, and automated transfer cars, and it can handle the maximum charge weight of 100 t for open coil and 200 t for tight coil annealing.
The advantages of UAD are as follows.
1. Lower capital investment.
2. Lower processing cost.
3. Excellent productivity.
4. Clean strip surface.
5. Uniform quality along the full strip length.
6. Easy adoption of full automatic operation.
Heat Resisting Alloys for Gas Turbines
Yoshinori SAIGA, Akira OHTOMO
pp. 133-146
Readers Who Read This Article Also Read
Tetsu-to-Hagané Vol.62(1976), No.4
Tetsu-to-Hagané Vol.65(1979), No.11
Tetsu-to-Hagané Vol.65(1979), No.4
抄録
伏見 直哉, 雀部 実, 川上 正雄, 一場 俊幸, 郡司 好喜, 福島 克治, 川上 正博, 江見 俊彦, 村上 勝彦, 内堀 勝之, 土山 友博, 鈴木 正, 武田 修一, 菊池 実, 浜上 和久, 山崎 道夫, 長井 寿, 柴田 浩司, 渡辺 敏, 宮地 博文, 吉原 一紘, 桝井 明
pp. 147-155
Article Access Ranking
06 Sep. (Last 30 Days)
-
Perspectives on the Promising Pathways to Zero Carbon Emissions in the Steel Industry toward 2050
ISIJ International Vol.65(2025), No.2
-
Growth, Removal, and Agglomeration of Various Type of Oxide Inclusions in Molten Steel
Tetsu-to-Hagané Vol.111(2025), No.11
-
Finite Element Analysis of Bubble Growth and Particle Swelling during Coal Pyrolysis
ISIJ International Vol.65(2025), No.9
-
Interface behavior leading to Al/Cu dissimilar metal bonding formation with high-speed eutectic reaction induced by applying current
QUARTERLY JOURNAL OF THE JAPAN WELDING SOCIETY Vol.43(2025), No.2
-
Corrosion Behavior of Carbon Steel under Soil Drying Conditions
ISIJ International Advance Publication
-
Cold Spot Joining of 980 MPa-class Ultra-high Strength Steel
Tetsu-to-Hagané Advance Publication
-
Combination Effect of Premixing Conditions and Iron Ore Size Distribution in Sintered Ore Granulation Process with Intensive Mixer
ISIJ International Advance Publication
-
A preliminary study on reduction degradation of iron ore sinter using sinter analogue and X-ray micro-computed tomography (MCT)
ISIJ International Advance Publication
-
Copper removal of liquid steel containing 0.25 % carbon using Fe2O3-CaCl2-SiO2 flux
ISIJ International Advance Publication
-
Evaluation of Feature Selection Methods for Oxygen Supply Prediction in BOF Steelmaking
ISIJ International Advance Publication
You can use this feature after you logged into the site.
Please click the button below.