- TOP
- Tetsu-to-Hagané
- Vol. 65 (1979), No. 14
Tetsu-to-Hagané Vol. 65 (1979), No. 14
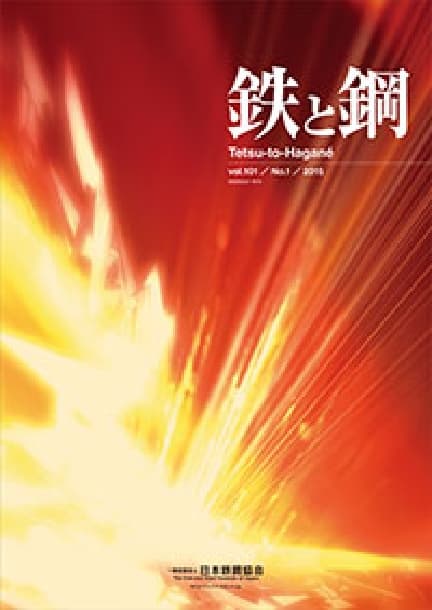
Grid List Abstracts
ONLINE ISSN: | 1883-2954 |
PRINT ISSN: | 0021-1575 |
Publisher: | The Iron and Steel Institute of Japan |
Backnumber
-
Vol. 111 (2025)
-
Vol. 110 (2024)
-
Vol. 109 (2023)
-
Vol. 108 (2022)
-
Vol. 107 (2021)
-
Vol. 106 (2020)
-
Vol. 105 (2019)
-
Vol. 104 (2018)
-
Vol. 103 (2017)
-
Vol. 102 (2016)
-
Vol. 101 (2015)
-
Vol. 100 (2014)
-
Vol. 99 (2013)
-
Vol. 98 (2012)
-
Vol. 97 (2011)
-
Vol. 96 (2010)
-
Vol. 95 (2009)
-
Vol. 94 (2008)
-
Vol. 93 (2007)
-
Vol. 92 (2006)
-
Vol. 91 (2005)
-
Vol. 90 (2004)
-
Vol. 89 (2003)
-
Vol. 88 (2002)
-
Vol. 87 (2001)
-
Vol. 86 (2000)
-
Vol. 85 (1999)
-
Vol. 84 (1998)
-
Vol. 83 (1997)
-
Vol. 82 (1996)
-
Vol. 81 (1995)
-
Vol. 80 (1994)
-
Vol. 79 (1993)
-
Vol. 78 (1992)
-
Vol. 77 (1991)
-
Vol. 76 (1990)
-
Vol. 75 (1989)
-
Vol. 74 (1988)
-
Vol. 73 (1987)
-
Vol. 72 (1986)
-
Vol. 71 (1985)
-
Vol. 70 (1984)
-
Vol. 69 (1983)
-
Vol. 68 (1982)
-
Vol. 67 (1981)
-
Vol. 66 (1980)
-
Vol. 65 (1979)
-
Vol. 64 (1978)
-
Vol. 63 (1977)
-
Vol. 62 (1976)
-
Vol. 61 (1975)
-
Vol. 60 (1974)
-
Vol. 59 (1973)
-
Vol. 58 (1972)
-
Vol. 57 (1971)
-
Vol. 56 (1970)
-
Vol. 55 (1969)
-
Vol. 54 (1968)
-
Vol. 53 (1967)
-
Vol. 52 (1966)
-
Vol. 51 (1965)
-
Vol. 50 (1964)
-
Vol. 49 (1963)
-
Vol. 48 (1962)
-
Vol. 47 (1961)
-
Vol. 46 (1960)
-
Vol. 45 (1959)
-
Vol. 44 (1958)
-
Vol. 43 (1957)
-
Vol. 42 (1956)
-
Vol. 41 (1955)
Keyword Ranking
06 Sep. (Last 30 Days)
Tetsu-to-Hagané Vol. 65 (1979), No. 14
Visualization of CO Bubbles Evolution Accompanying the Silica Reduction Reaction by X-ray Fluoroscopy
Kazumi OGINO, Atsushi NISHIWAKI
pp. 1985-1994
Abstract
The X-ray fluoroscopy technique has been successfully applied in studying the CO bubble evolution accompanied with the reduction of silica in blast furnace type slag by carbon-saturated iron in graphite crucible. Visual images have been obtained of the residence and behaviour of the bubbles at slag/metal and slag/graphite interface.
The main results obtained are as follows:
(1) The rate of bubble evolution at each interface varies with temperature and slag composition.
(2) The bubble evolution at slag/graphite interface proceeds more slowly than that at slag/metal interface and is accelerated when slag wets the interface. The shapes of detaching bubbles from the interface are spherical and their diameters are not more than 3 mm.
(3) The aspect of bubble evolution at slag/metal interface differs greatly with a period of the reaction. In the initial stage, numerous small bubbles evolve vigorously all over the interface, while in the later stage, large bubbles of dome shape are formed periodically at certain sites of the interface.
(4) The volume of detaching bubble from the interface in stationary state is nearly equal to that calculated from the balance between buoyancy and interfacial tension force.
On the Rate of CO Evolution with the Silica Reduction Reaction
Kazumi OGINO, Atsushi NISHIWAKI, Takahisa SUZUKI, Susumi IKUSHIMA
pp. 1995-2004
Abstract
The evolution rate of CO gas produced by the reduction of silica in CaO-SiO2-Al2O3 slag by molten carbon-saturated iron in graphite crucible has been measured in the temperature range between 1 510°C and 1 620°C, and the effects of tempenature, slag composition, silicon content of iron and ratio of interface area of slag/metal and slag/graphite on the rate have been examined.
The rate of CO evolution is proportional to activity of silica in slag and increases with an increase of the interface area. Apparent activation energies of the rate are 87 kcal/mol for acid slag and 62 kcal/mol for basic slag.
On the basis of the changes of over-all reaction rate with the ratio of the interface areas, the CO evolution rates of unit interface area are evaluated. The proportion of contribution of the reaction at each interface to over-all evolution rate is varied with temperature and slag composition. The rates of silica reduction estimated by present results are in good agreement with that already reported by many investigators.
The results obtained in this work show a good correspondence to the results of our previous study in which CO bubbles formation were observed by X-ray fluoroscopy method.
It is suggested that in this experimental condition, the reaction is controlled by chemical reaction step.
Readers Who Read This Article Also Read
Tetsu-to-Hagané Vol.64(1978), No.1
Tetsu-to-Hagané Vol.65(1979), No.7
Tetsu-to-Hagané Vol.64(1978), No.11
Equations for Determining the Optimum Number of Tuyeres of Blast Furnace
Takatsu SUGISAKI, Susumu OHTA, Takeshi KITAGAWA, Shunsaku SHIMADA
pp. 2005-2011
Abstract
On the consideration about the optimum number of tuyeres of blast furnace, the race way depth in comparison with the hearth diameter is noted.
As the measure of active race way depth in general, “the active race way dimension rate” (η) is adapted to the analysis of relations between practical data.
In the cases of good operation results of blast furnaces, the values are in the range from 0.45 to 0.50. Therefore, the equations for determining the optimum number of tuyeres are derived by taking η=0.47.
By taking the generalized combined blast condition into consideration, the constant term in LEONIDOV'S formula is analyzed to get a more optimum answer. Also, the validity of this equation is proved by the data from the blast furnace in operation.
The Effect of Oxygen Content in Molten Steel on the Interfacial Tension between Molten Steel and Slag
Kazumi OGINO, Shigeta HARA, Takashi MIWA, Shinji KIMOTO
pp. 2012-2021
Abstract
The interfacial tension between molten steel and slag was measured by the sessile drop method with transmission X-ray technique. The results were summarised as follows;
(1) The increase of oxygen content in steel caused the remarkable decrease of the surface tension of steel and the interfacial tension at steel-slag boundary. The fact shows that the oxygen dissolved in steel acts as the surface-active reagent at metal-slag boundary as well as at metal-gas interface.
(2) Consequently, the interfacial tension depended in most part on the oxygen content in steel and the effect of slag composition on the interfacial tension was not so much.
(3) In order to clear the effect of slag composition on the interfacial tension, the experimental results were discussed by the values of Δσ (=σm-σms) which indicated the differences between the surface tension and the interfacial tension at constant of oxygen content in metal. The values of Δσ dereased with increase of silica content in a slag.
(4) The work of adhesion between molten steel and slag Wad (=σm+σs-σms) was dependent sufficiently on the slag composition. The work of adhesion for a fluoride slag-steel system was smaller than that for an oxide slag-steel system, while the work of adhesion for oxide slag-metal system decreased with increasing of silica content in a slag.
Readers Who Read This Article Also Read
Tetsu-to-Hagané Vol.66(1980), No.10
Tetsu-to-Hagané Vol.67(1981), No.9
Tetsu-to-Hagané Vol.66(1980), No.2
Thermal Elasto-plastic Stress Analysis of Solidifying Shell in Continuous Casting Mold
Katsuo KINOSHITA, Toshihiko EMI, Manabu KASAI
pp. 2022-2031
Abstract
Temperature- and Stress-field in solidifying shell, and air gap formation in continuous casting mold have been numerically investigated by using a mathematical model to find conditions for strand-casting defect-free slabs. The model is based on a two dimensional non-steady state heat transfer analysis connected with a two dimensional thermal elasto-plastic stress analysis, and is capable of including the interaction between the temperature- and the stress-field. The model also involves operating variables, such as slab size, withdrawal rate, casting temperature, rate of water cooling in mold, mold taper, and, in particular, characteristics of mold flux.
Calculated variation of heat flux along the mold height agrees well with experimental one. Also, calculated shell profile, which exhibits retarded solidification owing to the formation of air gap near the corner of the shell, closely resembles experimental one.
The model developed in the present work has enabled us to get comprehensive information on the mode of solidification in continuous casting mold under varying casting conditions without making elaborating experiments. The model has been utilized as a potential simulator to determine optimum casting conditions for strand casting a variety of steels at high withdrawal rate.
Separate Recovery of Iron and Phosphorus from BOF Slags by Using Tin
Sumio SHIOMI, Masafumi MAEDA, Nobuo SANO, Yukio MATSUSHITA
pp. 2032-2037
Abstract
The present study was carried out to search for the possibility of the separate recovery of iron and phosphorus as gas from BOF slag by using graphite crucible or graphite powder with the presence of tin bath, which is considered to enhance the activity of phosphorus in iron reduced from slag or not to absorb the phosphorus vapor readily.
When the slag was reduced by graphite crucible, being in contact wtih tin bath, the phosphorus reduced from slag was carried away by CO explosively generated on the reduction of iron oxide. When graphite powder was used as reductant instead, 78% of phosphorus was removed from slag, only 3% of which was absorbed into the tin bath and the rest left the system as gas. The extent of gaseous dephosphorization was observed to depend on the mode of contact between slag and reductant as well as the amount of the latter.
Characteristics of Embrittlement in Steels above 600°C
Hirowo G. SUZUKI, Satoshi NISHIMURA, Shigehiro YAMAGUCHI
pp. 2038-2046
Abstract
Hot ductility in steels was studied. Special emphases were placed on the effects of thermal history, strain rate and fracture mode in order to clarify the sensitivity of surface cracking during both continuous casting operation and direct hot rolling.
There exist three temperature regions where typical embrittlement is noticed, i. e, Tm-1200 (I), 1 200-900 (II), and-700°C (III). The cause of embrittlement in the region I is the existence of residual liquid film along the dendritic interfaces. The ductility was found to be indepent of the strain rate. In the region II, the precipitation of finely distributed oxy-sulfides at the austenite grain boundary weakens the boundary strength, and thus overaging treatment such as slow cooling, holding for certain time, or slow rate of straining result in good ductility. On the other hand, the embrittlement in the III region is manifested by the slower strain rate of test. Controlling factors of this embrittlement are precipitation of oxides, sulfides and nitrides, precipitation of proeutectoid ferrite film along austenite grain boundary as well as grain boundary sliding. Detailed mechanism was discussed.
Metallurgical Changes due to Welding Conditions and a Long Term Heat-treatment in Austenitic Stainless Steel Weld Metals
Michio INAGAKI, Takayoshi KASUGAI, Kazuo EI, Tomokazu GODAI, Osamu TANAKA
pp. 2047-2056
Abstract
Effect of welding conditions and a long term heat-treatment at 650°C on metallurgical changes in austenitic stainless steels (SUS 304 and SUS 316) weld metals have been investigated. Results were as follows; 1) The solidifying structure at center parts of weld metals tend to grow parallel to the direction of plate thickness of the 1 pass 1 layer welded joint. 2) δ-ferrite forms in the order to the solidifying directions. 3) δ-ferrite changes those morphologies from granular and rod-like shape to net-like shape with increase of the amount of δ-ferrite. In the case of large amount δ-ferrite, this net-like δ-ferrite takes the form into densely three-dimentional network in the inner part of each pass. 4) There is no δ-ferrite network in the boundary zone between pass and the following pass, because δ-ferrite in these boundary zone are mixed granular and rod-like shape. 5) Networks of δ-ferrite in high heat input weld metals are larger than that in low heat input weld metals. 6) Carbides and δ phase precipitate in δ-ferrite subjected to heating for a long term at 650°C. 7) Carbides and δ phase take the form of network with a long term heating at 650°C in the weld metal containing a large volume of δ-ferrite.
From above results and the correlated research results of creep test and notch toughness of austenitic stainless steel weld metals subjected to a long term heat-treatment, it is considered that the following processes are advisable for the prevention measure of material worse at high temperature; 1) Selecting of the weld metals in which have the amount of δ-ferrite under about 5%, for the reason of dispertion of δ-ferrite and for destruction of δ-ferrite networks. 2) Making use of 2 pass 1 layer welding sequence to disperse the solidifying direction and applying the low heat input welding process to destroy δ-ferrite networks.
On the Sliding Wear Characteristics of Borided Steel Surface
Yoshio SHIBUYA, Yoshiaki IMAZAWA, Kazutoshi KUWANA
pp. 2057-2066
Abstract
A study has been made of the sliding wear characteristics of boride layer formed on S45C steel by boriding. As compared with the unborided S45C steel, the wear resistance of boride layer was very large in sliding velocity region between 0.1 and 4.5 m/s. It was on a level with the wear resistance of SKS3 in sliding velocity region between 0.1 and 1.0 m/s, and it was larger than that of SKS3 in sliding velocity region between 2.0 and 4.5 m/s. In the wear characteristics of boride layer, the oxidative wear was preferentially observed in sliding velocity region between 0.1 and 1.0 m/s. The maximum wear rate was observed 1.4 or 2.0 m/s in sliding velocity and in this region the mechanical wear was observed. It was considered that the melting wear was caused in sliding velocity above 3.0 m/s. The metallic debris caused by sliding wear with borided steel-low carbon steel was produced even in the slow sliding velocity of 0.1 m/s, and it increased with the increase of sliding velocity. It was considered that the wear loss of boride layer was largely influenced by the metallic debris contents produced with sliding wear of borided steel-low carbon steel. The oxide that were produced in the oxidative wear region restrained the adhesion between frictional surfaces. It was confirmed by the X-ray diffraction that the oxide consisted mainly of Fe3O4 and α-Fe2O3.
Evaluation of the Fatigue Damage of Rolls for Strip Mills below the Surface by X-ray Diffraction Method
Hiroshi TAKECHI, Kazuo NAMBA, Koichi KAWASAKI, Keizo FUJIWARA
pp. 2067-2075
Abstract
Technique of the X-ray diffraction line profile analysis has been applied to the study of fatigue damage below the surface of the work and the backup rolls of cold strip mill and the backup rolls of hot strip mill. Half value breadth has been taken as a measure of fatiguing.
Fatigued zone below the surface of rolls is well correlated with the half contact length of roll, L; 0.03 L in the work roll of cold strip mill and 0.1 L in the other rolls. Changes in the half value breadth with increase in cycles of roll contact differ in accordance with the surface hardness of the rolls: continued cycling results in decrease of the half value breadth at surface in hard rolls (Hs≥60) and increase in soft rolls (Hs≤50). The technique of X-ray study of fatigue can be extended to prediction and prevention of accidental failure of rolls due to fatigue fracture such as spalling. Furthermore the amount of surface dressing at regular maintenance of rolls can be saved significantly on the basis of accurate evaluation of the depth of fatigue damaged zone.
Current Status of NRIM Creep Data Sheet Project
Shin YOKOI, Sadao IKEDA, Hiroshi ITO, Eiji BABA
pp. 2076-2087
An Appraisal of Wire Rod and Bar Technology Developments and the Future
Kokichi TAKAHASHI
pp. 2088-2096
Readers Who Read This Article Also Read
Tetsu-to-Hagané Vol.62(1976), No.13
Tetsu-to-Hagané Vol.86(2000), No.7
Development of Mass Production Process for High Purity Ferritic Stainless Steel
Shoji IWAOKA, Nobuo OHASHI
pp. 2097-2103
Readers Who Read This Article Also Read
Tetsu-to-Hagané Vol.84(1998), No.11
ISIJ International Vol.52(2012), No.7
MATERIALS TRANSACTIONS Vol.60(2019), No.9
Sixth International Vacuum Metallurgy Conference San Diego, California, April 23-27, 1979
Micho INOUYE
pp. 2106-2107
抄録
月橋 文孝, 小林 一彦, 雀部 実, 斎藤 健志, 拝田 治, 古君 修, 三宅 英徳, 長井 寿, 村上 雅人, 柴田 浩司, 岡部 功, 別所 永康
pp. 2108-2112
Article Access Ranking
06 Sep. (Last 30 Days)
-
Perspectives on the Promising Pathways to Zero Carbon Emissions in the Steel Industry toward 2050
ISIJ International Vol.65(2025), No.2
-
Growth, Removal, and Agglomeration of Various Type of Oxide Inclusions in Molten Steel
Tetsu-to-Hagané Vol.111(2025), No.11
-
Finite Element Analysis of Bubble Growth and Particle Swelling during Coal Pyrolysis
ISIJ International Vol.65(2025), No.9
-
Interface behavior leading to Al/Cu dissimilar metal bonding formation with high-speed eutectic reaction induced by applying current
QUARTERLY JOURNAL OF THE JAPAN WELDING SOCIETY Vol.43(2025), No.2
-
Corrosion Behavior of Carbon Steel under Soil Drying Conditions
ISIJ International Advance Publication
-
Cold Spot Joining of 980 MPa-class Ultra-high Strength Steel
Tetsu-to-Hagané Advance Publication
-
Combination Effect of Premixing Conditions and Iron Ore Size Distribution in Sintered Ore Granulation Process with Intensive Mixer
ISIJ International Advance Publication
-
A preliminary study on reduction degradation of iron ore sinter using sinter analogue and X-ray micro-computed tomography (MCT)
ISIJ International Advance Publication
-
Copper removal of liquid steel containing 0.25 % carbon using Fe2O3-CaCl2-SiO2 flux
ISIJ International Advance Publication
-
Evaluation of Feature Selection Methods for Oxygen Supply Prediction in BOF Steelmaking
ISIJ International Advance Publication
You can use this feature after you logged into the site.
Please click the button below.