- TOP
- Tetsu-to-Hagané
- Vol. 61 (1975), No. 1
Tetsu-to-Hagané Vol. 61 (1975), No. 1
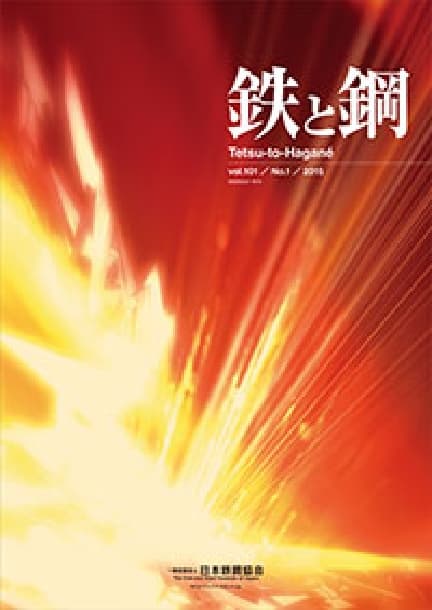
Grid List Abstracts
ONLINE ISSN: | 1883-2954 |
PRINT ISSN: | 0021-1575 |
Publisher: | The Iron and Steel Institute of Japan |
Backnumber
-
Vol. 111 (2025)
-
Vol. 110 (2024)
-
Vol. 109 (2023)
-
Vol. 108 (2022)
-
Vol. 107 (2021)
-
Vol. 106 (2020)
-
Vol. 105 (2019)
-
Vol. 104 (2018)
-
Vol. 103 (2017)
-
Vol. 102 (2016)
-
Vol. 101 (2015)
-
Vol. 100 (2014)
-
Vol. 99 (2013)
-
Vol. 98 (2012)
-
Vol. 97 (2011)
-
Vol. 96 (2010)
-
Vol. 95 (2009)
-
Vol. 94 (2008)
-
Vol. 93 (2007)
-
Vol. 92 (2006)
-
Vol. 91 (2005)
-
Vol. 90 (2004)
-
Vol. 89 (2003)
-
Vol. 88 (2002)
-
Vol. 87 (2001)
-
Vol. 86 (2000)
-
Vol. 85 (1999)
-
Vol. 84 (1998)
-
Vol. 83 (1997)
-
Vol. 82 (1996)
-
Vol. 81 (1995)
-
Vol. 80 (1994)
-
Vol. 79 (1993)
-
Vol. 78 (1992)
-
Vol. 77 (1991)
-
Vol. 76 (1990)
-
Vol. 75 (1989)
-
Vol. 74 (1988)
-
Vol. 73 (1987)
-
Vol. 72 (1986)
-
Vol. 71 (1985)
-
Vol. 70 (1984)
-
Vol. 69 (1983)
-
Vol. 68 (1982)
-
Vol. 67 (1981)
-
Vol. 66 (1980)
-
Vol. 65 (1979)
-
Vol. 64 (1978)
-
Vol. 63 (1977)
-
Vol. 62 (1976)
-
Vol. 61 (1975)
-
Vol. 60 (1974)
-
Vol. 59 (1973)
-
Vol. 58 (1972)
-
Vol. 57 (1971)
-
Vol. 56 (1970)
-
Vol. 55 (1969)
-
Vol. 54 (1968)
-
Vol. 53 (1967)
-
Vol. 52 (1966)
-
Vol. 51 (1965)
-
Vol. 50 (1964)
-
Vol. 49 (1963)
-
Vol. 48 (1962)
-
Vol. 47 (1961)
-
Vol. 46 (1960)
-
Vol. 45 (1959)
-
Vol. 44 (1958)
-
Vol. 43 (1957)
-
Vol. 42 (1956)
-
Vol. 41 (1955)
Keyword Ranking
30 Aug. (Last 30 Days)
Tetsu-to-Hagané Vol. 61 (1975), No. 1
Reduction of Sintered Ore by CO Gas in Fixed Bed with Radial Distribution of Particle Sizes
Masayoshi AMATATSU, Tanekazu SOMA
pp. 22-28
Abstract
The characteristics of the reduction process of sintered ore in a fixed bed with the radial distribution of particle sizes were studied. The reduction rate of sintered ore by CO gas was measured continuously by a weighing method in the range of reducing gas flow rate from 12g·6 to 50.4 NI/min at 900°C.
The following results were obtained.
(1) At a constant ratio of the bed weight to gas flow rate (M/V), 25g·min/Nl the effect of gas film resistance in the range of reducing gas flow rate from 12g·6 to 50g·4NI/min on the reduction process was to be disregarded.
(2) The gas utilization coefficient obtained in the fixed bed with a mixed charge of different sizes of sintered ore was observed to be greater than that obtained with a radially distributed charge of the same sintered ore. The calculated results using the rate constants for the reduction process for the uniform size in a bed were in a good agreement with the data obtained in the fixed bed with a mixed charge and a distributed charge of different sizes of sintered ore, respectively.
(3) In a fixed bed with a radially distributed charge of different sizes of sintered ore, the effect of gas flow rate in the range from 12g·6 to 24g·4 NI/min on the reduction process was small.
Fundamental Study on the Rate of Desulphurization of Pig Iron by Solid Lime
Yasuji KAWAI, Katsumi MORI, Yoshifumi SAN-NOMIYA
pp. 29-35
Abstract
The rate of desulphurization of pig iron by solid lime was measured by the chemical analysis of sulphur content of metal samples taken from a liquid Fe-C-S alloy in a lime crucible under CO gas atmosphere.
The experimental result was interpreted by a rate equation derived from the reaction model that the reaction proceeds with the growth of a reaction product layer and the rate-determining step is the transport of sulphur through this layer.
The effect of temperature on the rate was small, the apparent activation energy of the reaction being about 14 kcal/mole.
An addition of silicon to the alloy, contrary to the results of previous investigators, was harmful for desulphurization and this was ascribed to the formation of calcium silicate on the surface of lime.
Kinetics of Manganese Oxide Reduction from Molten Slag by Carbon Saturated Iron
Masahiro ASHIZUKA, Atushi MORIBE, Kiyoshi SAWAMURA
pp. 36-45
Abstract
The rates of MnO reduction from slag by carbon saturated iron and Cu-Si alloy have been measured in the temperature range from 1500°C to 1600°C and the rate controlling steps have been determined by an electrochemical consideration.
The results obtained are as follows:
1. Apparent activation energies of MnO reduction by carbon saturated iron are about 120, 80 and and 73kcal/mol for 40CaO50SiO210Al2O3+4.O3Mn0 (slag A), 50CaO40SiO210Al2O3+3.9Mn0 (Slag B), and 50CaO50Al2O3+2.3Mn0 (wt%)(slag C), respectively.
2. The rate of MnO reduction is promoted by the addition of Si to carbon saturated iron or Cu but is not increased by the addition of Si beyond 5wt%, and its rate coefficient is Km=180×10-5 (g/cm2-min) for a slag B at 1510 deg;C.
3. The rate controlling step of MnO reduction by carbon saturated iron containing small amounts of Si is an anodic reaction of CO evolution and that by carbon saturated iron or Cu-Si alloy containing Si above 5 wt% is Mn diffusion in slag.
Readers Who Read This Article Also Read
Tetsu-to-Hagané Vol.68(1982), No.1
Tetsu-to-Hagané Vol.74(1988), No.1
Tetsu-to-Hagané Vol.85(1999), No.9
The Estimation of Viscosity Coefficient, Self-diffusion Coefficient, and Surface Tension of Molten Metals by the Principle of Corresponding States
Yoshio WASEDA, Masayasu OHTANI
pp. 46-53
Abstract
The principle of corresponding states has been applied to the measurements of viscosity and selfdiffusion of molten metals using the reducing form suggested by Helfand and Rice. In the present work, the parameters were determined by means of the pair potentials directly derived from the experimental structural data. Viscosity coefficient (η) and self-diffusion coefficient (D) data for several molten metals whose melting points are low were examined and the temperature dependence for molten metals are ex-expressed by the following equations.
η=η(V*)2/3×(1.28×10-4)×(TmM)1/2/(Mρ)2/3 (Poise)
log η*(V*)2/3=(-0.11±0.08)+(0.55±0.09) (1/T*)
D=D*/(V*)1/3×(1.28×10-4)×(Tm/M)1/2(M/ρ)1/3 (cm2/sec)
log D*/(V*)1/3=(-0.28±0.03)-(0.91±0.05) (1/T*)
T*=T×(0.71/Tm)
where Tmis the melting point in K M is atomic weight, ρ is density (g/cm3) and T is the absolute temperature. The simple form of surface tension (γ) was also derived from the relationship between viscosity coefficient and surface tension as follows;
γ=η*(V*)2/3×(T·Tm)1/2/(M/ρ)2/3 (dyne/cm)
Using these equations and density data, it is possible to estimate the values of viscosity coefficient, self-diffusion coefficient, and surface tension for any molten metals at any temperatures. The usefulness of these eqations was demonstrated on the molten metals which have high melting points.
The Structure of Molten Fe and Fe-C Alloys by X-ray Diffraction
Yoshio WASEDA, Masanori TOKUDA, Masayasu OHTANI
pp. 54-70
Abstract
X-ray diffraction patterns were obtained for molten Fe, Co, and Ni and molten, Fe-C, Ni-C, and Fe-Si alloys at temperatures between melting point and 1650deg;C. After calculating the structure factor (Fourieranalysis) the atomic radial distribution function was evaluated from which nearest neighbour distancer1 and coordination number n1, were obtained. Comparing the results with those previously observedby other investigators, a reasonable agreement was found.
The dependence of the structure of molten Fe-C alloys on carbon concentration was found as follows;the nearest neighbour distance r1 and coordination number n1 become larger with an increase in carbonconcentration up to 2·1wt% C. Between 2·1wt% and 3·0wt% C, r1 and n1 remain constant. Above 3·0wt% C, r1 and n1 slightly decrease. On the other hand, r1 and n1, are almost constant in molten Ni-C alloysup to 2·0wt% C. In molten Fe-Si alloys, r1 and n;1 become smaller with an increase in silicon concentrationup to 10·0wt% Si. The structural behavior of molten alloys was discussed with reference to theircrystal structures in the solid state.
Effect of Tube Size and Heat Treatment on Formability of Steel Tube for Automobile
Soichi IZUMI, Kuniyoshi KAITA, Hidetoshi TAKEDA, Kyoichiro NISAWA
pp. 71-79
Abstract
Effects of the tube size (t/D) and heat treatment on formability of steel tubes for automobiles were studied by using steel tubes of the size 45∅×5.0mm and 75∅×1.6mm (the tensile strength range from 30 to 60Kg/mm2).
The main results obtained are as follows.
(1) Expanding and 90°C flattening formabilities are decreased by the increment of tube size (t/D). In the flare forming of materials having tensile strengths above 50kg/mm2, singular behavior is recognized, in comparision with the other forming processes, in that an increase of t/D gives a superior formability.
(2) In flare forming, the circumference of a tube is not deformed into a uniform shape but the “earing” is remarkably increased in tensile strength materials. On the other hand, in expand forming, as the circumference of a tube is deformed into a uniform shape and the ratio of strain of a welded part to that in the circumference of a tube increases; this is considered to be a very severe forming method.
(3) The effect of heat treatments of formability of steel tubes becomes larger by increasing the tensile strength on S content. The effect of heat treatments is also varied by the method of forming. These changes of formability result from the variation of the microstructure, metal flow, and hardness at welded parts affected by the heat treatment.
Effects of Cooling Rates after Hot Rolling on the Planar Anisotropy of Extremely Low Carbon Niobium Cold Rolled Steel Sheets
Taisuke AKAMATSU, Tetsu SAKAMOTO, Mikio TAUMI, Kunio WATANABE
pp. 80-95
Abstract
The effects of the cooling rates after hot rolling on the planar anisotropy of cold-rolled Nb steel sheets with extremely low C (C-0.004%, Nb-0.12%) were examined. The specimens were hot-rolled to 3.2mm and cooled with various cooling rates; quenching in water, rapid cooling with water spray, air cooling and furnace cooling.
The sheets were cold-rolled to 0.8mm and annealed at 780°C for 5 hr. The direction of earing at conical cup test varied from diagonal to rolling-transverse according to the decrease of cooling rate after hot-rolling.
To clarify this phenomenon, specimens were exposed in air for several kinds of interval after hot-rolling and quenched in water.
Specimens quenched from γ state showed the earing of diogonal direction and those quenched from a state showed the earing of rolling-transverse direction.
At conical cup test after cold-rolling and annealing, the textures of the sheets of diagonal earing were (554)[225] and those of rolling-transverse directional earing were (111)[110] and (111)[112].
The difference of earing direction can be attributed to the difference of texture formation which is affected by the particle size of precipitated Nb carbonitride in hot-rolled sheets.
On the Formation of Austenite Grains from Prior Martensitic Structure
Seiichi WATANABE, Tatsuro KINITAKE
pp. 96-106
Abstract
Electron microscopic studies have been made of austenite partially transformed from prior martensitic structure in the temperature range between Ac1and Ac3.
It has been found that each acicular austenite grain which has been formed from ferrite laths with same orientation has same crystallographic orientation and the austenite has the KURDJUMOV-SACHS orientation relationship with the ferrite. The both lath boundary and cementite play an important role in the formation of acicular austenite grains, with same orientation. When austenite is formed adjacent to precipitated cementite on the boundary, the austenite must have PITSCH orientation relationship with cementite and the KURDJUMOV-SACHS orientation relationship with ferrite. Consequently, the variant of formation of austenite is limited to only one, so that acicular austenite grains are identically oriented with each other. When the specimen is heated over Ac3after acicular austenite structure has sufficiently been developed, coarse austenite grain structure is formed from the prior coarse γ grain structure. It is observed that a coarse austenite grain does not consist of a single crystal grain but consists of several divided regions, each of which is corresponding to recovered ferrite regions which have been formed by the recovery of lath martensite during heating.
On the Tensile Deformation Behaviour of Two-Phase Iron Alloys
YO TOMOTA, Koshiro KUROKI, Imao TAMURA
pp. 107-118
Abstract
Tensile deformation behaviour of two-phase iron alloys with ductile second phase is studied and tried to be understood by the difference in strain between the harder phase and the softer phase. The alloys used are classified into the three groups; Fe-Cr-Ni alloys, Fe-Ni-C alloys and Fe-Calloys composed of austenite and ferrite, austenite and martensite, and ferrite and Tensile deformation behaviour of two-phase iron alloys with ductile second phase is studied and tried to be understood by the difference in strain between the harder phase and the softer phase. The alloys used are classified into the three groups; Fe-Cr-Ni alloys, Fe-Ni-C alloys and Fe-Calloys composed of austenite and ferrite, austenite and martensite, and ferrite and martensite respectively with various volume fractions. The mean effective grain size of each alloy is adjusted to be nearly same by heat treatment.
The main results obtained are as follows:
(1) The tensile deformation behaviour of a two-phase alloy is dependent on theC-value (=0.2% proof stress of the harder phase/0.2% proof stress of the softer phase), volume fraction and shape of the harder phase. This is because the degree of strain-inequalitym(m=e2/e1:e1 is the mean strain of the softer phase and e2 is that of the harder phase) is affected by these factors.
(2) The flow stress of a two-phase alloy with small C-value (smaller than about 3) is estimated by the strain-equal model (m=1).
(3) The m-value of a two-phase alloy with nearly spherical second phase decreases with an increase in C-value and its tensile deformation behaviour approaches to the stress-equal model (m=0). In this case, the m-value is decreased with decreasing the volume fraction of the harder phase. When the volume fraction of the harder phase becomes close to unity, the deformation of the softer phase is strongly restricted by the around harder phase, so that the tensile deformation behaviour of a two-phase alloy approaches to the strain-equal model, independent onC-value.
(4) The m-value is slightly affected by the overall strain of a two-phase alloy. It is small at small strain and increases with an increase in strain.
(5) The tensile deformation behaviour of a two-phase alloy with long fiberous or disc second phase whose largest axis is parallel to the tensile direction is nearly shown by the strain-equal model even if Cvalue is large.
Effect of Pre-Aging Treatment on the Strain Aging Characteristics of Hard Drawn Eutectoid Carbon Steel Wire
Yoshiro YAMADA
pp. 119-129
Abstract
The effect of quench aging and intermediate strain aging on the aging characteristics of cold worked eutectoid carbon steels containing different quantities of free nitrogen has been examined by means of torsional pendulum damping, electrical resistivity, and room temperature tensile test.
It is found that the strength increase by aging in the temperature range from room temperature to about 150deg;C (1st stage aging) is enhanced by the introduction of an intermediate strain aging at 220deg;C or 350deg;C put in between two sets of wire drawing practices. During strain aging at 220deg;C or 350deg;C, locking or pinning of dislocations by carbon supplied from lamellar cementite is brought about. The following cold drawing unlocks the dislocations and results in the dissolution of the carbon atoms in normal lattice sites. These carbon atoms in solution lock dislocations again during 1st stage aging.
By cold drawing after strain aging, nitrogen atoms also can enter in normal lattice sites as a result of dislocation depinning. During the following aging at 1st stage, nitrogen atoms relock dislocations and age strengthening occurs.,
Quench aging at 100°C can, however, diminish much of the redissolution of nitrogen by cold work on Fe-0.8% C-0.01%N specimen. This may suggest thatthe iron nitride formed during quench aging is more stable to cold work than Cottrell atmosphere.
Some Properties of Sintered and Hot-Forged High Speed Steels
Hisashi ANDO, Akira OKAYAMA, KO SOENO
pp. 130-138
Abstract
Particle size distributions, microstructures and residual gas contents of high speed steel powders, ato-mized by spraying water or argon gas have been investigated. The particle size distributions and the micro-structures of the water-atomized powders are finer than those of the argon-atomized powders. Oxygen contents of the water-atomized powders are higher, but can be easily reduced by sintering in a vacuum furnace. In the argon-atomized powders, argon included in the powders are observed.
Sintered and hot-forged high speed steels of low oxygen contents have high transverse rupture strength and notch-toughness, because of their uniformly fine microstructures. Retained austenite is decreased and grinding is also relatively easy in the sintered and hot-forged high speed steels of fine microstructures.
Physico-Chemical Considerations on the Electroslag Remelting Process
Michio INOUYE, Yasushi KOJIMA, Makoto KATO
pp. 139-156
Article Access Ranking
30 Aug. (Last 30 Days)
-
Perspectives on the Promising Pathways to Zero Carbon Emissions in the Steel Industry toward 2050
ISIJ International Vol.65(2025), No.2
-
Growth, Removal, and Agglomeration of Various Type of Oxide Inclusions in Molten Steel
Tetsu-to-Hagané Vol.111(2025), No.11
-
Copper removal of liquid steel containing 0.25 % carbon using Fe2O3-CaCl2-SiO2 flux
ISIJ International Advance Publication
-
Finite Element Analysis of Bubble Growth and Particle Swelling during Coal Pyrolysis
ISIJ International Vol.65(2025), No.9
-
Corrosion Behavior of Carbon Steel under Soil Drying Conditions
ISIJ International Advance Publication
-
Cold Spot Joining of 980 MPa-class Ultra-high Strength Steel
Tetsu-to-Hagané Advance Publication
-
Factors Affecting Generation of Iron Fines in Cold Sheet Rolling of Steel
ISIJ International Vol.65(2025), No.9
-
Experimental Study on Heat Transfer Characteristics of a Moving Single-Nozzle Jet Impingement
ISIJ International Vol.65(2025), No.9
-
Combination Effect of Premixing Conditions and Iron Ore Size Distribution in Sintered Ore Granulation Process with Intensive Mixer
ISIJ International Advance Publication
-
Evaluation of Feature Selection Methods for Oxygen Supply Prediction in BOF Steelmaking
ISIJ International Advance Publication
You can use this feature after you logged into the site.
Please click the button below.