- TOP
- Tetsu-to-Hagané
- Vol. 69 (1983), No. 8
Tetsu-to-Hagané Vol. 69 (1983), No. 8
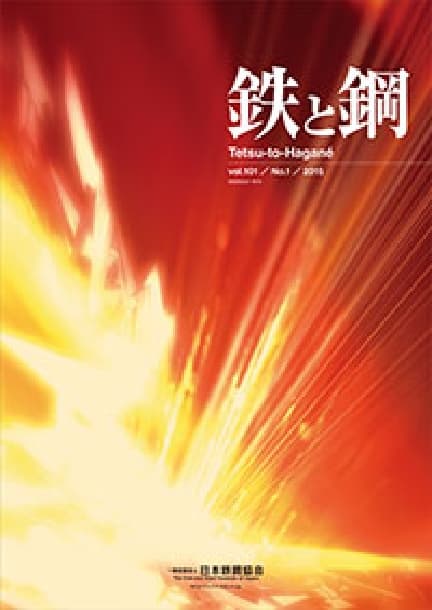
Grid List Abstracts
ONLINE ISSN: | 1883-2954 |
PRINT ISSN: | 0021-1575 |
Publisher: | The Iron and Steel Institute of Japan |
Backnumber
-
Vol. 111 (2025)
-
Vol. 110 (2024)
-
Vol. 109 (2023)
-
Vol. 108 (2022)
-
Vol. 107 (2021)
-
Vol. 106 (2020)
-
Vol. 105 (2019)
-
Vol. 104 (2018)
-
Vol. 103 (2017)
-
Vol. 102 (2016)
-
Vol. 101 (2015)
-
Vol. 100 (2014)
-
Vol. 99 (2013)
-
Vol. 98 (2012)
-
Vol. 97 (2011)
-
Vol. 96 (2010)
-
Vol. 95 (2009)
-
Vol. 94 (2008)
-
Vol. 93 (2007)
-
Vol. 92 (2006)
-
Vol. 91 (2005)
-
Vol. 90 (2004)
-
Vol. 89 (2003)
-
Vol. 88 (2002)
-
Vol. 87 (2001)
-
Vol. 86 (2000)
-
Vol. 85 (1999)
-
Vol. 84 (1998)
-
Vol. 83 (1997)
-
Vol. 82 (1996)
-
Vol. 81 (1995)
-
Vol. 80 (1994)
-
Vol. 79 (1993)
-
Vol. 78 (1992)
-
Vol. 77 (1991)
-
Vol. 76 (1990)
-
Vol. 75 (1989)
-
Vol. 74 (1988)
-
Vol. 73 (1987)
-
Vol. 72 (1986)
-
Vol. 71 (1985)
-
Vol. 70 (1984)
-
Vol. 69 (1983)
-
Vol. 68 (1982)
-
Vol. 67 (1981)
-
Vol. 66 (1980)
-
Vol. 65 (1979)
-
Vol. 64 (1978)
-
Vol. 63 (1977)
-
Vol. 62 (1976)
-
Vol. 61 (1975)
-
Vol. 60 (1974)
-
Vol. 59 (1973)
-
Vol. 58 (1972)
-
Vol. 57 (1971)
-
Vol. 56 (1970)
-
Vol. 55 (1969)
-
Vol. 54 (1968)
-
Vol. 53 (1967)
-
Vol. 52 (1966)
-
Vol. 51 (1965)
-
Vol. 50 (1964)
-
Vol. 49 (1963)
-
Vol. 48 (1962)
-
Vol. 47 (1961)
-
Vol. 46 (1960)
-
Vol. 45 (1959)
-
Vol. 44 (1958)
-
Vol. 43 (1957)
-
Vol. 42 (1956)
-
Vol. 41 (1955)
Keyword Ranking
30 Aug. (Last 30 Days)
Tetsu-to-Hagané Vol. 69 (1983), No. 8
Structure and Control of Magnetic Domain in Grain-oriented Silicon Steel
Tadashi ICHIYAMA
pp. 895-902
Readers Who Read This Article Also Read
Tetsu-to-Hagané Vol.71(1985), No.4
鉄鋼技術を支える論文と講演発表件数の推移/1982年の内外鉄鋼業/技術開発の駆動力/発明は天才のひらめきである/溶質原子の大きさはどうして測る?/学術用語の乱れ
稲葉 晋一, 佐々木 稔, 木原 諄二, 森田 善一郎
pp. 902-902,912
Readers Who Read This Article Also Read
Tetsu-to-Hagané Vol.69(1983), No.8
Delayed Fracture of High Strength Bolts Used for Bridges
Shinsaku MATSUYAMA
pp. 903-912
Abstract
[in Japanese]
Solubility of Nitrogen in Liquid Chromium and Chromium-Iron Alloys
Fujio ISHII, Yasutaka IGUCHI, Shiro BAN-YA
pp. 913-920
Abstract
The solubility of nitrogen in liquid chromium and chromium-iron alloys has been studied by a sampling method at the temperatures of 1550°1780°C and under 0.041.0 atm of nitrogen.
The free energy of solution and the activity of nitrogen in liquid chromium and chromium-iron alloys were determined by applying the interstitial model for the experimental results.
The results obtained are summerized as follows:
(1) Nitrogen dissolved in liquid chromium and chromium-iron alloys upto 50% Fe does not obey Henry's law, and solubility of nitrogen in liquid chromium is given by the following equation.
log K(Z)=5515/T-3.193, K(Z)=aN/√PN2=ψNZN/√PN2
(2) Activity coefficients of nitrogen based on pure liquid chromium are expressed as follows :
log ψNN(cr)=(4235/T-1.513)·YN YN<0.21
log ψFeN(cr)=1.80·YFe YFe<0.7
(3) Activity coefficients of nitrogen in iron-chromium alloys based on pure liquid iron are shown by the following equations :
log γcrN(Fe)=(-13765/T+3.10)·XCr Xcr<0.16
log fcrN(Fe)=(-148/T+0.033)·[%Cr] [%Cr]<15
Where YN and ZN are the mole ratio and the lattice ratio of nitrogen in liquid metal respectively.
Readers Who Read This Article Also Read
Tetsu-to-Hagané Vol.69(1983), No.8
The Effects of C, Si, Al, and B on the Activity of Phosphorus in Liquid Iron
Shiro BAN-YA, Nobutoshi MARUYAMA, Shinji FUJINO
pp. 921-928
Abstract
The vapor pressure of P on liquid Fe-P-j (j= C, Si, Al, or B) alloys has been measured by the transportation method at 1673 K.
The results obtained were treated by the model of interstitial solution proposed by J. CHIPMAN, and the effect of alloying elements on the activity coefficient of P in liquid iron was determined by assuming C and B as interstitial elements and Si and Al as substitutional ones respectively.
The interaction parameters are summarized as follows:
εCP=(∂1nγP/∂Xc)XFe→1=5.43±0.67
εSlP=(∂1nγP/∂Xsi)XFe→1=7.68±0.44
εAlP=(∂1nγP/∂XAl)XFe→1=3.57±0.33
εBP=(∂1nγP/∂XB)XFe→1=1.49±0.16
Fundamental Studies on Recovery of Na2CO3 from the Sodium Containing Slag
Teruo MATSUO, Teruo YOKOOJI, Makoto YOSHIDA, Satomi YAMAMOTO, Kazuo KAWAMURA
pp. 929-936
Abstract
Chemical reactions for the recovery of Na2CO3 from the slag obtained in the refining of hot metal with Na2CO3 were studied. The process for the Na2CO3 recovery consisted of three main unit operations.
1) Dissolving of the slag in the circulating aqueous solution.
2) Removal of residue and impurities (Si, P) from the solution.
3) Recovery of Na2CO3 from the solution.
More than 90% of Na, P, V and 40 to 50% of S, Si contained in the slag dissolved in the solution and main ion species in the solution were proved as Na+, V5+, OH-, CO2-3, SiO2-3, PO3-4, S2-, S2O2-3and SO2-4. With the addition of CO2, OH-/CO2-3 ratio in the solution turned to nil and Si concentration in the solution reduced to 2g/l because of hydrolysis of SiO2-3 ion. Addition of Ca(OH)2 in the solution caused reduction of P concentration to less than 3g/l, due to the formation of Ca3(PO4)2·Removal of V and S ion were also studied. From these experiments, a process-flow for the Na2CO3 recovery from the slag was proposed.
Pilot Plant Test on Recovery of Na2CO3 from the Sodium Containing Slag
Teruo MATSUO, Teruo YOKOOJI, Makoto YOSHIDA, Seiji YAMAMOTO, Satomi YAMAMOTO, Shoichi FUKUDA
pp. 937-943
Abstract
Recovery of Na2CO3 from the sodium containing slag was studied. The experimental plant process consisted of several unit operations, such as dissolving of the slag in the aqueous solution, removal of Si and P from the solution, separation of the precipitate and the residue from the solution, crystallizing of Na2CO3 hydrate from the solution and drying the Na2CO3 hydrate. The plant could process the slag and produce Na2CO3 at the rate of 120 kg/h and80 kg/h, respectively. The slag obtained in the continuous refining of hot metal with Na2CO3 was used as the raw material. By examining for more than ten days, the following results were obtained. 1) Small particles (1.3mm dia.) of Na2CO3were obtained and the yield was 82.5%. The contents of impurites (P, Si, and S) in the recovered Na2CO3 were lower than the ranges which were unfavarable for the refining of hot metal. 2) The plant was operated without difficulties and treatment of the byproducts such as insoluble material and precipitate of dephosphorization presented no problem.
Deoxidation Characteristics and Morphology of Deoxidation Products in Molten Iron with Ti and Ti-Si, Ti-Mn, and Ti-Si-Mn Complex Deoxidizers
Takehiro DAN, Koki GUNJI
pp. 944-950
Abstract
The purpose of this investigation is to study the variation of total oxygen content in molten iron deoxidized by Ti, and Ti-Si, Ti-Mn and Ti-Si-Mn alloys as well as to observe the morphology of the deoxidation products.
The results obtained are summarized as follows:
(1) Titanium deoxidation: With less than 0.12% Ti addition, molten FeO-TiO2 binary droplets were formed. With more than 0.15% Ti, titanium oxide with high melting point precipitated as deoxidation product. In the latter case the deoxidation rate and limit were satisfactory.
(2) Ti-Si deoxidation: The products have the similar morphology to that in the case (1) but their sizes were considerably larger. The very low Si content in the products was found. The deoxidation rate and limit were slightly worse than those in the titanium deoxidation.
(3) Ti-Mn deoxidation: The products seemed to be liquid complex oxides containing Ti and Mn. They were very large and perfectly spherical. The deoxidation rate and limit were deteriorated.
(4) Ti-Si-Mn deoxidation: The products consisted of titanium, manganese and silicon oxides. Their Si contents were as low as that in the Ti-Si deoxidation. The deoxidation rate and limit were superior to those in the case (3) and inferior to those in the case (2).
Oxidation Behavior of Silicon, Phosphorus and Vanadium in Carbon-saturated Iron Melt by Sodium Carbonate
Ryo INOUE, Hideaki SUITO
pp. 951-958
Abstract
From an experiment that Na2CO3 reacted with solid Fe-54% V alloy at 1100°C, the following equation was derived for the reaction of vanadium oxidation by soda ash.
Na2CO3+ 4/5V= Na2O+ 2/5V2O5+ C
Vanadium valencies in the soda flux (Na2CO3, Na2CO3-FeO) reacting with carbon-saturated iron melt have been examined as a function of time. The V2O5 produced by the above equation was found to gradually reduced by carbon and/or silicon, changing to the valency V5+→V4+→V3+. The reduction rate of vanadium oxide was reduced by the addition of iron oxide.
The oxidation behavior of phosphorus, vanadium, and silicon in carbon-saturated iron melt has been studied by use of soda flux (Na2CO3, Na2CO3-Fe2O3) at 1300°C. The oxidation of phosphorus and vanadium were initially retarded if a small amount of flux was added by installments and after the end of flux addition the reversion of phosphorus and vanadium occurred. In comparison with the results obtained in the addition of soda flux by a lump, the retardation of initial oxidation was explained by the fact that the reversion rate of phosphorus and vanadium was considerably fast. The effect of Fe2O3 addition to the flux was found to be significant in both experiments using a lump and installment additions. The extensive removal of vanadium was observed in the addition of Fe2O3 by installments, while neither dephosphorization reaction nor the vanadium reversion took place. The same oxidation behavior found in the Na2CO3-Fe2O3 flux was obtained in an experiment using the CaO-CaF2-Fe2O3 flux.
Readers Who Read This Article Also Read
Tetsu-to-Hagané Vol.67(1981), No.1
Tetsu-to-Hagané Vol.71(1985), No.2
Tetsu-to-Hagané Vol.70(1984), No.7
Surface Appearance of Electrodeposited Zn-Fe Alloys
Takeshi ADANIYA, Tomihiro HARA, Hisaaki FUKUSHIMA, Kei HIGASHI
pp. 959-966
Abstract
Zn-Fe alloys were electrodeposited on a rotating sylindrical copper electrode from the sulfate bath, and the surface appearance of the alloys were observed. The alloys electrodeposited under certain plating conditions demonstrated a characteristic striated patterns which followed the direction of flow of the solutions. The reason of appearance of this striation was considered on the basis of the anomalous electrodeposition mechanism of Zn-Fe alloys proposed so far by the authors. In addition, several attempts were made in order to diminish the striated pattern.
Readers Who Read This Article Also Read
ISIJ International Vol.33(1993), No.9
Tetsu-to-Hagané Vol.74(1988), No.1
Effects of Silicon and Manganese Addition on the Morphology of Sulfides in the As-cast State and Their Deformation Behavior in Low Carbon Aluminum-killed Steels
Ichiro TSUKATANI, Masatoshi SUDO, Hisashi TAKADA
pp. 967-974
Abstract
The morphology and distribution of sulfides in steel ingots having different silicon contents from 0 to 2.0% at 0.3 to 1.5% manganese contents were investigated with a directional-solidification technique. The steels had carbon content of 0.05%, sulfur content of 0.05% and low oxygen content and they were solidified at cooling rate of 5°C/min. The deformation behavior of their sulfides during hot-rolling after heating at 800°1200°C was also investigated.
In the specimen containing 0% Si and 0.3% Mn, the manganese sulfides in the as-cast state were globular in shape and contained about 40% FeS (GlObular sulfide is called type It.). Silicon addition above 1.1% changed the morphology of sulfides from type It to type III according to Sims' classification and decreased the FeS content of manganese sulfide. Type II sulfide was observed in the specimens containing manganese in the range of 0.61.5% at 0% Si.
The relative plasticity of sulfides increased as the heating (_??_ rolling) temperature decreased from 1200°C. While with type II in 1.0% Mn steels the trend continued to 800°C, with type It and III in 0.3% Mn steels maximum plasticity was encountered at 1000°C. The decrease in relative plasticity had a close relationship with the increase in the FeS content of manganese sulfides and the decrease in manganese sulfide size. The difference in plasticity between type It and III MnS and type II MnS was thought to be due to presence of FeS.
Readers Who Read This Article Also Read
Tetsu-to-Hagané Vol.49(1963), No.14
Tetsu-to-Hagané Vol.69(1983), No.6
Tetsu-to-Hagané Vol.68(1982), No.1
Improvement of the Strength and Toughness of Steel Plates by Direct-quenching and Tempering
Nozomi KOMATSUBARA, Seiichi WATANABE, Hiroo OHTANI
pp. 975-982
Abstract
Direct-quenching after hot rolling above recrystallization temperature in austenite was investigated in low carbon and low alloy high tensile strength steels. Effects of cooling rates during direct-quenching on the microstructures, strength, and toughness were investigated, comparison being made with reheat-quenching.
It was clarified that the strength and toughness were remarkably improved by direct-quenching in a certain range of cooling rates, in which the microstructure of direct-quenching showed up as a mixture of martensite and fine bainite, while that of reheat-quenching was coarse bainitic. These results showed that the improvements of the strength and toughness were due to the enhancement of hardenability by direct-quenching.
By calculating ideal critical diameters from tensile strengths of as-quenched steel plates, it became clear that the increase in hardenability by diect-quenching was about by 40%. It was too large to ascribe the increase of hardenability only to the difference of austenite grain sizes in direct-quenching and reheat-quenching.
Some possible mechanisms for these interesting phenomena were discussed.
Strengthening of 350kgf/mm2 Grade Maraging Steel through Special Thermomechanical Treatment
Seiichi MUNEKI, Yoshikuni KAWABE, Junji TAKAHASHI
pp. 983-989
Abstract
When the conventional thermomechanical treatment (TMT) was applied to the 10Ni-18Co-14Mo maraging steel, the austenite grain was refined to below l0μ but the precipitation in austenite could not be suppressed, thus resulting in the rather lower strength. This study has been conducted to achieve the nominal 350kgf/mm2 tensile strength by optimizing the thermomechanical processing variables and by modifying the chemical composition of the steel. In order to obtain the microstructure with fine grain and no coarse precipitates formed in austenite, the special thermomechanical treatment (STMT) has been developed. STMT consisted of multipass rolling from the solution treatment temperature to 1000°C, interrupting the rolling and air cooling to the temperature which is below the nose temperature of precipitation start curve and just above the recrystallization temperature, re-rolling quickly by sufficient amount of reduction, and quenching below room temperature. This interrupted rolling is essential to suppress the strain-induced precipitation. When STMT was applied to two steels, the nominal microstructure was not obtained for the 10Ni-18Co-14Mo steel but was successfully obtained for the 10Ni-18Co-12Mo-1Ti steel. It is, however, essential to choice the correct re-rolling temperature and to employ the adequate amount of reduction, and by optimizing these rolling conditions, the tensile strength of 363kgf/mm2 was achieved in the 10Ni-18Co-12Mo-1Ti maraging steel.
Strength of Electron Beam Welded Joint in 250kgf/mm2 Grade Maraging Steel
Mitsutane FUJITA, Yoshikuni KAWABE, Hirosada IRIE, Susumu TSUKAMOTO
pp. 990-997
Abstract
The influence of the electron beam welding condition on the strength of welded joint in maraging steel sheets having strength level of 250kgf/mm2 has been studied. The influence has been discussed on the basis of the variation of the welding heat input and the width of weld metal under various welding conditions.
The strength of heat affected zone is equal to that of the base metal.The strength of weld metal is lower than that of the base metal and is not affected by the welding heat input. Therefore, the joint is such that the weld metal of lower strength is inserted between the base metal having higher strength.
The strength of the welded joint decreases gradually with the increase in the welding heat input. The plastic deformation of the weldment concentrates in the weld metal and in tensile test specimens fail there. On the other hand, the width of weld metal becomes wider with the increase in the welding heat input. Thus, the dependence of the strength of the welded joint on heat input can be explained by the fact that the plastic constraint of the base metal for the weld metal decreases with the increase in the width of the weld metal.
Readers Who Read This Article Also Read
Tetsu-to-Hagané Vol.67(1981), No.1
Tetsu-to-Hagané Vol.71(1985), No.2
Tetsu-to-Hagané Vol.70(1984), No.7
The Flow Stress of Unstable Austenitic Stainless Steel Accompanied by Deformation-induced Martensite
Kazuo HOSHINO
pp. 998-1005
Abstract
The flow stress (σ) of unstable austenitic stainless steels is studied by comparing stable austenitic and martensitic stainless steels.
(1) The root of dislocation density (√ρ) obtained by X-ray analysis in stable γ-phase increases with strain (ε) and the expression of ε as a function of √ρ is parabolic.√ρ of γ phase mixed with deformation-induced martensite (α') increases with the root of α'phase volume fraction (Vα'1/2) in addition to the above relation.
(2) σ of unstable steels is intermediate of the values caluculated by "equal stress model" and"equal strain model" and it becomes to take the values estimated by equal strain model with increase of α'-phase.In this case, the higher the strength of α' phase is and the larger the volume of α' phase is, the higher is the ununiformity of strain between γ and γ' phase. In the case that the strength of α' phase is almost the same, the smaller the volume of γ' phase is, the smaller is the ununiformity of strain between γ and α' phase.
(3) σ is affected not only by the volume but also by the strength of α' phase and inversely plastic flow depresses α'-transformation to inhibit the enhancement of higher σ values due to high strength of α'-phase.
Corrosion Behaviour of Inconel 617 in a Simulated HTGR Helium
Yoshikazu SAKAI, Tatsuhiko TANABE, Tadashi SUZUKI, Heitaro YOSHIDA
pp. 1006-1013
Abstract
Corrosion tests of Inconel 617 were carried out in a temperature range from 900°C to 1040°C in helium environment with small amounts of impurity gases, which was the simulated primary coolant of High Temperature Gas cooled Reactor (HTGR), and the carburization, decarburization, and oxidation were investigated in terms of temperature.
(1) The alloy was carburized in the temperature range from 900°C to 970°C, but was decarburized above 990°C. The transition temperature from carburization to decarburization was estimated to be 975°C. In the temperature range, where carburization occurred, the largest carbon pickup was observed at 940°C, however, in the temperature range of decarburization, the degree of decarburization increased with the increase of temperature.
(2) In the temperature range of carburization, the carburized layer was observed at near-surface region, and Cr-Mo carbides precipitated along the grain boundaries and twin boundaries. In the temperature range of decarburization, the carbides along the grain boundaries disappeared, and this led to the formation of altered layer, the depth of the layer reaching to about 2000μ after 500h corrosion at 1040°C.
(3) In contrast to the results that the oxide films formed at high temperature in air were dense and protective, the films formed in the helium environment were very porous and less protective. Further, the chromium content in the oxide films along the grain boundaries beneath the surface decreased with the increase of test temperature. This could lead to make the films much less protective.
Hot Corrosion Resistance of Aluminide and Platinum-Aluminide Coatings of a Ni-base Superalloy IN-738LC in Combustion Gas Atmosphere
Mitsuo CHIGASAKI, Ko SOENO, Yutaka FUKUI, Kiyoshi OTAKA
pp. 1014-1021
Abstract
Pack cementation process has been applied for aluminide and platinum-aluminide coating on a nickel-base superalloy IN-738LC. Burner rig test using light oil containing 0.33%S was carried out for the evaluation of hot corrosion resistance.
Aluminide coatings have two coating layers. The outer layer is high-Al NiAl and the inner layer consists mainly of low-Al NiAl. Hot corrosion resistance of the aluminide coatings can be improved by increasing the thickness of the outer layer.
In the burner rig tests at 850°C or below, the aluminide coatings whose outer layer thicknesses are about 80μ are more hot corrosion resistant than the platinum-aluminide coatings made by electroplating of platinum of 7μ thickness and aluminizing at 1120°C. This difference is attributed to the preferential attack of the PtAl2 dispersed in the outer layer of the platinum-aluminide coatings.
In the burner rig test at about 1000°C, the platinum-aluminide coatings are more hot corrosion resistant than the aluminide coatings, because of dissolution of the undesirable PtAl2 particles into the matrix and the increased Pt concentration in the coating layer, both due to the rapid diffusion of atoms at the high temperature.
Article Access Ranking
30 Aug. (Last 30 Days)
-
Perspectives on the Promising Pathways to Zero Carbon Emissions in the Steel Industry toward 2050
ISIJ International Vol.65(2025), No.2
-
Growth, Removal, and Agglomeration of Various Type of Oxide Inclusions in Molten Steel
Tetsu-to-Hagané Vol.111(2025), No.11
-
Copper removal of liquid steel containing 0.25 % carbon using Fe2O3-CaCl2-SiO2 flux
ISIJ International Advance Publication
-
Finite Element Analysis of Bubble Growth and Particle Swelling during Coal Pyrolysis
ISIJ International Vol.65(2025), No.9
-
Corrosion Behavior of Carbon Steel under Soil Drying Conditions
ISIJ International Advance Publication
-
Cold Spot Joining of 980 MPa-class Ultra-high Strength Steel
Tetsu-to-Hagané Advance Publication
-
Factors Affecting Generation of Iron Fines in Cold Sheet Rolling of Steel
ISIJ International Vol.65(2025), No.9
-
Experimental Study on Heat Transfer Characteristics of a Moving Single-Nozzle Jet Impingement
ISIJ International Vol.65(2025), No.9
-
Combination Effect of Premixing Conditions and Iron Ore Size Distribution in Sintered Ore Granulation Process with Intensive Mixer
ISIJ International Advance Publication
-
Evaluation of Feature Selection Methods for Oxygen Supply Prediction in BOF Steelmaking
ISIJ International Advance Publication
You can use this feature after you logged into the site.
Please click the button below.