- TOP
- Tetsu-to-Hagané
- Vol. 57 (1971), No. 14
Tetsu-to-Hagané Vol. 57 (1971), No. 14
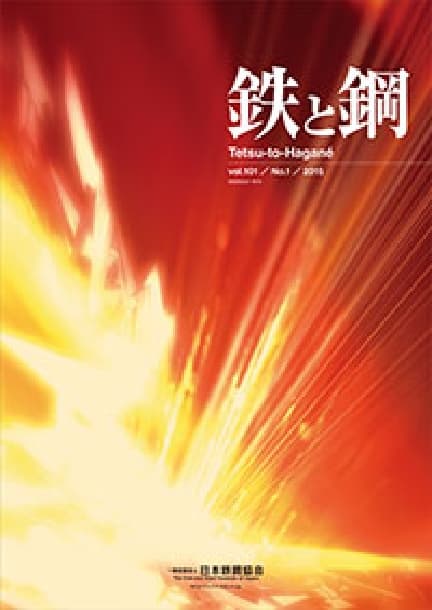
Grid List Abstracts
ONLINE ISSN: | 1883-2954 |
PRINT ISSN: | 0021-1575 |
Publisher: | The Iron and Steel Institute of Japan |
Backnumber
-
Vol. 111 (2025)
-
Vol. 110 (2024)
-
Vol. 109 (2023)
-
Vol. 108 (2022)
-
Vol. 107 (2021)
-
Vol. 106 (2020)
-
Vol. 105 (2019)
-
Vol. 104 (2018)
-
Vol. 103 (2017)
-
Vol. 102 (2016)
-
Vol. 101 (2015)
-
Vol. 100 (2014)
-
Vol. 99 (2013)
-
Vol. 98 (2012)
-
Vol. 97 (2011)
-
Vol. 96 (2010)
-
Vol. 95 (2009)
-
Vol. 94 (2008)
-
Vol. 93 (2007)
-
Vol. 92 (2006)
-
Vol. 91 (2005)
-
Vol. 90 (2004)
-
Vol. 89 (2003)
-
Vol. 88 (2002)
-
Vol. 87 (2001)
-
Vol. 86 (2000)
-
Vol. 85 (1999)
-
Vol. 84 (1998)
-
Vol. 83 (1997)
-
Vol. 82 (1996)
-
Vol. 81 (1995)
-
Vol. 80 (1994)
-
Vol. 79 (1993)
-
Vol. 78 (1992)
-
Vol. 77 (1991)
-
Vol. 76 (1990)
-
Vol. 75 (1989)
-
Vol. 74 (1988)
-
Vol. 73 (1987)
-
Vol. 72 (1986)
-
Vol. 71 (1985)
-
Vol. 70 (1984)
-
Vol. 69 (1983)
-
Vol. 68 (1982)
-
Vol. 67 (1981)
-
Vol. 66 (1980)
-
Vol. 65 (1979)
-
Vol. 64 (1978)
-
Vol. 63 (1977)
-
Vol. 62 (1976)
-
Vol. 61 (1975)
-
Vol. 60 (1974)
-
Vol. 59 (1973)
-
Vol. 58 (1972)
-
Vol. 57 (1971)
-
Vol. 56 (1970)
-
Vol. 55 (1969)
-
Vol. 54 (1968)
-
Vol. 53 (1967)
-
Vol. 52 (1966)
-
Vol. 51 (1965)
-
Vol. 50 (1964)
-
Vol. 49 (1963)
-
Vol. 48 (1962)
-
Vol. 47 (1961)
-
Vol. 46 (1960)
-
Vol. 45 (1959)
-
Vol. 44 (1958)
-
Vol. 43 (1957)
-
Vol. 42 (1956)
-
Vol. 41 (1955)
Keyword Ranking
06 Sep. (Last 30 Days)
Tetsu-to-Hagané Vol. 57 (1971), No. 14
Study on the Source of Oxide Inclusions Originated from Casting-Pit Refractories by Zircon Tracer
Hiroshi NAGAYAMA
pp. 2171-2183
Abstract
In order to investigate the source of oxide inclusions orignated from refractories of casting-pit in top-teeming ingots, Al2O3-SiO2 refractory zircon (Containing 10% and 40% as ZrO5) were used as the bottom lining of trough and ladle, trough nozzle, and the lining of mould top.
The behaviors of oxide inclusions originated from refractories of casting-pit were studied by determining ZrO2 content in oxide inclusions extracted from steel specimens.
The following results are obtained.
(1) The entrapped quantity of the trough bottom brick into oxide inclusions was about 10% and the entrapped quantity into oxide inclusions was in the order of; trough bottom brick>ladle bottom brick trough mortar>trough nozzle brick>trough ramming materials>castable refractories for mould top.
(2) Some comparisons were made between zircon tracer method and R.I. method in the investigation of the formation of oxide inclusions originated from refractories of casting-pit.
Readers Who Read This Article Also Read
Tetsu-to-Hagané Vol.57(1971), No.1
Tetsu-to-Hagané Vol.57(1971), No.12
Tetsu-to-Hagané Vol.58(1972), No.1
Phenomena of Oxygen Enrichment in a Blast Furnace Process and its Limit
Tsuneo MIYASHITA, Mitsuru OHTSUKI
pp. 2184-2196
Abstract
An investigation was made on the oxygen enrichment to blowing gas up to 40% by using an experimental blast furnace.The oxygen ratio in this experiment was increased under the condition of constant bosh gas volume per unit time.Coke rate was slightly decreased with inc: easing the oxygen content up to 25%. In further increase of oxygen content beyond 25%, the coke rate was increased to about 2.5kg/t HNI for each 1% of oxygen enrichment, but increase of prcductivity of iron of 5% was obtained.
Gas temperature distribution was measured to make clear the heat exchange phenomena between gases and solids, and the temperature of solids was estimated by simulation calculation. From this result, it was deduced that the oxygen enrichment blowing operation was limited due to the shortening of the length of thermal reserve zone with increase of oxygen enrichment.
The main reason for the increase of the coke rate could be explained by calculated results of decreasing indirect reduction rate of ores which was influenced by the above temperature distribution change.
This became another commercial limit of oxygen enrichment blowing.
Kinetic Study on the Dissolution Reaction of SiO2 into Liquid Iron
Rokuro SAKAGAMI, Takashi SASAI
pp. 2197-2206
Abstract
The kinetics of dissolution of SiO2 into liquid iron has been investigated by a method of rapid rise of the temperature of the melt in silica crucible from 1550° to 1600°, or 1635°.
The oxygen increase of liquid iron is rate-controlled solely by interfacial reaction, until the equilibrium at these temperatures is reached.The following reaction in which the oxygen adsorbed at the crucible-melt interface takes part as a reactant explained well the experimental results.
SiO2+O(ads)=Si+2O+O(ads)
It is impossible to discuss the phenomena of the Si-deoxidation under the assumption that the local equilibrium is kept at the interface where the reaction proceeds.
The oxygen adsorption isotherm for the interface is-estimated.
A Study on the Nitrogen Desorption Reaction of Liquid Iron and Steel
Kiichi NARITA, Shinji KOYAMA, Takehisa MAKINO, Masayoshi OKAMURA
pp. 2207-2218
Abstract
Kinetics of nitrogen desorption reaction of liquid iron and steel has been investigated by means of blowing various gas on the surface of the melt.
The nitrogen desorption reaction of liquid iron is of second order, and the reaction rate is remarkably affected by oxygen content in liquid iron.The rate constant decreases in inverse proportion to the second power of oxygen content above 0.03%, increases gradually below this value of oxygen content and tends to approach a constant value below 0.01% of oxygen.
From the standpoint of chemisorption of nitrogen atoms on the surface of liquid iron, these results lead to the conclusion that the rate-controlling step is the reaction between these atoms, which is disturbed by adsorbed oxygen atoms.
The activation energy of nitrogen desorption reaction is 39 kcal/mole in liquid iron containing oxygen less than 001%.
When the decarburization and the nitrogen desorption reactions proceed simultaneously by blowing argon and oxygen mixed gas to liquid steel, the latter reaction is deviated from the second order, and its rate becomes considerably slow in comparison with that of liquid iron by blowing only argon. These facts are considered to be caused by the disturbance of the reaction of nitrogen atoms by the oxygen atoms adsorbed on the surface of liquid steel.
Diffusion of Oxygen in Molten Iron
Kanae SUZUKI, Kazumi MORI
pp. 2219-2229
Abstract
The interdiffusivity of oxygen in molten iron was measured by the capillary method over the temperature range from 1560 to 1660°. The sample melt in a magnesia crucible reacted with Ar-H2OH2gas.
When the initial oxygen content was below about 002%, the oxygen concentration in the lower part of the melt was increased abnormally during the process of diffusion. On the other hand, when the initial oxygen content was higher than about 002%, the abnormal behavior of oxygen was not observed.The abnormal phenomenon may be ascribed to surface diffusion of oxygen along the cruciblemelt interface. The diffusivity of oxygen which was obtained from the normal concentration profile agreed with that calculated from the total amount of oxygen diffused into the melt.
The result is expressed by the following Arrhenius-type equation.
D=(5.59±0.80)×10-3 exp(-19500/±750/RT) (cm2/sec)
The present result is in good agreement with that obtained by MCCARRON and BELTON.
Computation of Internal Stress for Steel Bar during and after Quenching
Yasutsugu TOSHIOKA, Munemitsu FUKAGAWA, Yoshinori SAIGA
pp. 2230-2242
Abstract
To draw benefits from fast quenching to strengthen and toughen as well as to increase the fatigue strength by taking advantage of residual stress, the stresses given rise to in steels during and after quenching were computed.
The quenching stress, which is due to thermal strain and transformation strain, was presented as a function of changes of temperature distribution, while the method of quenching and the sizes of steel articles were conceived as the factors that determined the temperature distribution.For the steel articles state during quenching, elastic parts and plastic parts were discriminated on the basis of the maximum shear stress theory, and the transient stress distributions were obtained by integrating the stress from the quenching temperature down to an instantanius temperature.
The computations revealed:
1) The superficial tensile stress becomes maximum during quenching just before the transformation at the center is completed, whereas, in cases of imperfect quench, the central tensile stress becomes maximum when the steel as a whole is cooled to the room temperature.
2) For the case of perfect quench, the superficial tensile stress is the greater the severer the quenching, though it decreases beyond a certain limit of quenching speed even becoming comperession.
3) For imperfect quench, the stress distribution, though much depends on the quenched structure and the severity of quenching, is generally such that the superficial stress is compressive and often a sharp peak of tensile stress exists at just below the surface.
A few practical applications have been presented and discussed.
Effects of Aluminum and Nitrogen Contents on Recrystallization in Fe-Al-N Alloys
Tadashi ICHIYAMA, Ikushi YOSHIDA, Mizuo EJIMA, Osamu MATSUMURA
pp. 2243-2252
Abstract
The effects of aluminum and nitrogen contents on recovery, recrystallization and texture-development in Fe-Al-N alloys were investigated.The specimens could be classified into two types according to their annealing behaviors.Alloys which contained less than 0.02% aluminum belonged to type I, and those which contained more than 0.060% aluminum or both aluminum (0.06%) and nitrogen were classified as type II.
During annealing, type I alloys recovered to a greater extent than type II in which recovery was inhibited.
In type I alloys, the recrystallization proceeded gradually after it had started.At 720°C, these alloys gave the {544}‹225›oriented recrystallization texture. This orientation became prominent as aluminum content was increased.
On the other hand, in type II alloys, the recrystallization proceeded rapidly once it had started because of their larger driving force for grain boundary migration.At 720°C, some specimens which contained 0.06% aluminum and less than 0.005% nitrogen yielded the {111}‹110›+ {554}‹225›oriented recrystallization texture, but the others, which contained excess amount of aluminum or nitrogen, showed a wider scatter from these orientations.
Discussions were made concerning the processes of texture development in Fe-Al-N alloys.
Thermodynamic and Kinetic Aspects of Vacuum Refining of Liquid Steel
Kiichi NARITA
pp. 2253-2272
Atomic Absorption Spectrochemical Analysis for Iron and Steel
Yoshihide ENDO, Yuki NAKAHARA
pp. 2285-2299
Article Access Ranking
06 Sep. (Last 30 Days)
-
Perspectives on the Promising Pathways to Zero Carbon Emissions in the Steel Industry toward 2050
ISIJ International Vol.65(2025), No.2
-
Growth, Removal, and Agglomeration of Various Type of Oxide Inclusions in Molten Steel
Tetsu-to-Hagané Vol.111(2025), No.11
-
Finite Element Analysis of Bubble Growth and Particle Swelling during Coal Pyrolysis
ISIJ International Vol.65(2025), No.9
-
Interface behavior leading to Al/Cu dissimilar metal bonding formation with high-speed eutectic reaction induced by applying current
QUARTERLY JOURNAL OF THE JAPAN WELDING SOCIETY Vol.43(2025), No.2
-
Corrosion Behavior of Carbon Steel under Soil Drying Conditions
ISIJ International Advance Publication
-
Cold Spot Joining of 980 MPa-class Ultra-high Strength Steel
Tetsu-to-Hagané Advance Publication
-
Combination Effect of Premixing Conditions and Iron Ore Size Distribution in Sintered Ore Granulation Process with Intensive Mixer
ISIJ International Advance Publication
-
A preliminary study on reduction degradation of iron ore sinter using sinter analogue and X-ray micro-computed tomography (MCT)
ISIJ International Advance Publication
-
Copper removal of liquid steel containing 0.25 % carbon using Fe2O3-CaCl2-SiO2 flux
ISIJ International Advance Publication
-
Evaluation of Feature Selection Methods for Oxygen Supply Prediction in BOF Steelmaking
ISIJ International Advance Publication
You can use this feature after you logged into the site.
Please click the button below.