- TOP
- Tetsu-to-Hagané
- Vol. 76 (1990), No. 2
Tetsu-to-Hagané Vol. 76 (1990), No. 2
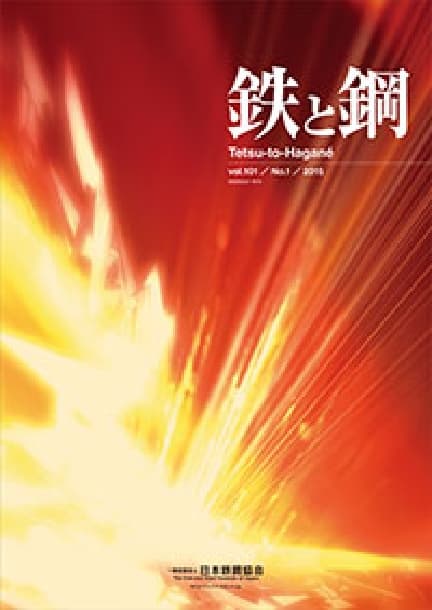
Grid List Abstracts
ONLINE ISSN: | 1883-2954 |
PRINT ISSN: | 0021-1575 |
Publisher: | The Iron and Steel Institute of Japan |
Backnumber
-
Vol. 111 (2025)
-
Vol. 110 (2024)
-
Vol. 109 (2023)
-
Vol. 108 (2022)
-
Vol. 107 (2021)
-
Vol. 106 (2020)
-
Vol. 105 (2019)
-
Vol. 104 (2018)
-
Vol. 103 (2017)
-
Vol. 102 (2016)
-
Vol. 101 (2015)
-
Vol. 100 (2014)
-
Vol. 99 (2013)
-
Vol. 98 (2012)
-
Vol. 97 (2011)
-
Vol. 96 (2010)
-
Vol. 95 (2009)
-
Vol. 94 (2008)
-
Vol. 93 (2007)
-
Vol. 92 (2006)
-
Vol. 91 (2005)
-
Vol. 90 (2004)
-
Vol. 89 (2003)
-
Vol. 88 (2002)
-
Vol. 87 (2001)
-
Vol. 86 (2000)
-
Vol. 85 (1999)
-
Vol. 84 (1998)
-
Vol. 83 (1997)
-
Vol. 82 (1996)
-
Vol. 81 (1995)
-
Vol. 80 (1994)
-
Vol. 79 (1993)
-
Vol. 78 (1992)
-
Vol. 77 (1991)
-
Vol. 76 (1990)
-
Vol. 75 (1989)
-
Vol. 74 (1988)
-
Vol. 73 (1987)
-
Vol. 72 (1986)
-
Vol. 71 (1985)
-
Vol. 70 (1984)
-
Vol. 69 (1983)
-
Vol. 68 (1982)
-
Vol. 67 (1981)
-
Vol. 66 (1980)
-
Vol. 65 (1979)
-
Vol. 64 (1978)
-
Vol. 63 (1977)
-
Vol. 62 (1976)
-
Vol. 61 (1975)
-
Vol. 60 (1974)
-
Vol. 59 (1973)
-
Vol. 58 (1972)
-
Vol. 57 (1971)
-
Vol. 56 (1970)
-
Vol. 55 (1969)
-
Vol. 54 (1968)
-
Vol. 53 (1967)
-
Vol. 52 (1966)
-
Vol. 51 (1965)
-
Vol. 50 (1964)
-
Vol. 49 (1963)
-
Vol. 48 (1962)
-
Vol. 47 (1961)
-
Vol. 46 (1960)
-
Vol. 45 (1959)
-
Vol. 44 (1958)
-
Vol. 43 (1957)
-
Vol. 42 (1956)
-
Vol. 41 (1955)
Keyword Ranking
07 Sep. (Last 30 Days)
Tetsu-to-Hagané Vol. 76 (1990), No. 2
Strength and Toughness of Ceramics
Toshiro KOBAYASHI
pp. 149-157
Readers Who Read This Article Also Read
Tetsu-to-Hagané Vol.86(2000), No.1
Tetsu-to-Hagané Vol.76(1990), No.1
Tetsu-to-Hagané Vol.66(1980), No.1
Lattice Structures and Mechanical Properties of Intermetallic Compounds Containing Titanium
Ei-ichi FURUBAYASHI
pp. 158-171
Determination of Total Iron Content and XRF Analysis of Iron Ores
Takashi OHTSUBO
pp. 172-182
Readers Who Read This Article Also Read
Tetsu-to-Hagané Vol.76(1990), No.6
Tetsu-to-Hagané Vol.76(1990), No.2
Tetsu-to-Hagané Vol.75(1989), No.3
Distribution of Sulphur between Liquid Iron and FetO-(CaO+MgO)-(SiO2+P2O5) Phosphate Slags
Retsu NAGABAYASHI, Mitsutaka HINO, Shiro BAN-YA
pp. 183-190
Abstract
Equilibrium sulphur distribution between slag and liquid iron has been studied at the temperature range from 1 573 to 1 953 K. The slag systems studied were of FetO-P2O5-MxOy (MxOy=CaO, MgO, SiO2) ternary and of FetO-P2O5-CaO-MxOy (MxOy= MgO, SiO2) quaternary. The data were obtained in our previous works concerning the effect of additives on the phosphorus equilibrium and the approximate validity of the regular solution model for the phosphate slag.
The distibution ratios, (% S)/aS, and the sulphide capacities, CS, of those slags were determined as the function of the slag composition. The results obtained were summarized as follows:
log CS = -4.210 + 3.645 (BI)
(BI) = NCaO + NFeO + 0.5NMgO - 0.5NP2O5
log{(% S)/ aS} = log CS - log aFetO + 5 685/ T - 1.430
It was confirmed that these equations were applicable to all the experimental results, not only on the phosphate slags, which was obtained in the present work and were reported by the others, but also on the silicate slags by the other investigators.
Transport Phenomenon of Oxygen through Molten CaO-SiO2 System Containing Zinc and Nickel Oxides
Minoru SASABE, Shin-ichi KITAMURA
pp. 191-198
Abstract
Oxygen transfer rates, P, through molten NiO-CaO-SiO2, ZnO-CaO-SiO2 and NiO-ZnO-CaO-SiO2 systems were measured by using a molten thin film penetration method developed by the author. Temperatures of the measurement were about 1 450, 1 500 and 1 550°C.
The transfer rates were 1 to 5 time 10-8 mol·O2·cm-1·s-1. They were the same order of the magnitude as that in the case of iron oxide-CaO-SiO2 system measured previously. In the case of system containing NiO, the more NiO contents the higher oxygen transfer rate. On the other hand, in the case of system containing ZnO, the higher ZnO contents the higher oxygen transfer rate in the case of less than 20mol%ZnO and the higher ZnO contents the lower oxygen transfer rate in the case of more than 20%ZnO.
Effects of constituent on oxygen transfer rate, P, with the unit of mol O2·cm-1·s-1 are empirically expressed as follows:
System less than 12.5 mol% NiO : P = 3.15×10-9 (mol%NiO)
System less than 35mol% ZnO : P = -8.5×10-11 (mol%ZnO-22)2+4.2×10-8
Temperature dependencies of the oxygen transfer rates are as follows:
7.5 mol%NiO-46.3 mol%CaO-46.3 mol%SiO2 : P = 3.51×10-2 exp (-25.3×103 / T)
10 mol%ZnO-45 mol%CaO-45 mol%SiO2 : P = 3.24×10-2 exp (-25.3×103 / T)
20 mol%ZnO-40 mol%CaO-40 mol%SiO2 : P = 6.39×10-2 exp (-25.3×103/ T)
30 mol%ZnO-35 mol%CaO-35 mol%SiO2 : P = 4.96×10-2 exp (-25.3×103 / T)
It was estimated that NiO and ZnO acted as p- and n-type semiconductors, respectively, on the basis of the discussion on the dependency of the transfer rate on oxygen partial pressure at the surface of the molten oxide.
Behavior of Sprash Formation by Top Blown Oxygen Gas under Hot Metal Decarburization
Shin-ya KITAMURA, Kazuo OKOHIRA
pp. 199-206
Abstract
To clarify the sprash formation behavior by top blown oxygen gas under hot metal decarburization, the experiments by small scale induction furnace and water model were carried out and the following points were found.
1) Between sprash height and cavity depth, when the oxygen gas was blown to hot metal, clear relationship was not found but when the Ar gas was blown to hot metal or the oxygen gas was blown to low carbon content molten steel, good relation was found.
2) When Ar gas was blown to hot metal, carbon content of the sprash particles were simillar to that of hot metal bath and the size were large. On the contrary, when oxygen gas was blown to hot metal, very low carbon containning, small size sprash particles were collected.
3) For oxygen gas blowing condition, good relationship was found between sprash height and waste gas flow rate calculated by the degree of decarburization.
According to the above mentioned results and energy balance calculation, it can be considered that the energy generated by gas formation when decarburization reaction took place was the primary affecting factor for sprash formation rather than the kinetic energy of the top blown gas.
Oxidation Behavior of Al, Si and Mn during Oxygen Top Blowing for Rising of Steel Temperature in Ladle
Yoshihiko HIGUCHI, Yoshiyasu SHIROTA, Nobuhiro KUROKAWA, Yasuyuki TOZAKI, Kiyoto FUJIWARA
pp. 207-213
Abstract
Studies were carried out on the oxygen gas blowing process of molten steel in an argon gas stirring ladle. It was aimed to increase the bath temperature rapidly and to improve the steel cleanliness by minimizing oxidation losses of silicon and manganese.
A mathematical model, describing oxidation behaviors of [Al], [Si] and [Mn], was developed by considering reaction and mixing zones, and was compared with the measurement.
Results obtained were as follows:
(1) The model can reasonablly explain the heating speed and oxidation behavior of solute elements in molten steel. All parameters used in the model can be determined from operating conditions.
(2) In order to minimize oxidation of [Si] and [Mn] and to promote oxidation of [Al], it is necessary to increase circulation rate of molten steel and velocity of oxygen gas blown to molten steel, and to shorten the distance between top blowing lance and surface of molten steel.
Readers Who Read This Article Also Read
Tetsu-to-Hagané Vol.75(1989), No.8
Tetsu-to-Hagané Vol.75(1989), No.2
Tetsu-to-Hagané Vol.77(1991), No.9
Estimation of Critical Strain for Internal Crack Formation in Continuously Cast Slabs
Shuji NAGATA, Tooru MATSUMIYA, Kosaku OZAWA, Tetsuro OHASHI
pp. 214-221
Abstract
In order to estimate the exact condition of the internal crack formation in continuously cast slabs, a new evaluating equation for this critical strain has been introduced based on many factors such as steel grades, strain rate, solidified shell thickness, and surface temperature of the slabs.
The characteristic of this equation is to determine the hot ductility, especially ZDT at the neighbourhood of solid-liquid interface, which has not been investigated quantitatively, and to make clear the relation between the critical strain for internal crack and the width of poor ductility range calculated from shell thickness, surface temperature, and ZDT.
The cracking condition in cast slabs could be explained well, using this calculated critical strain based on these factors.
Characteristics of Tin Flash-coated Chromium Plated Steel Sheet
Nobuyoshi SHIMIZU, Fumio KUNISHIGE, Terunori FUJIMOTO, Tsuneo INUI
pp. 222-229
Abstract
Tin flash-coated chromium plated steel sheet for a welded can has been developed using a low concentrated stannous sulfate solution. The performance of this sheet was discussed from the point of the coating weight and structure.
The results are as follows:
1) An uniform and well-adhered tin layer can be deposited on the chromium layer by a low concentrated stannous sulfate solution.
2) The chromium layer inhibits the iron-tin alloy reaction during the lacquer curing and leaves much tin unalloyed. The residual metallic tin coating above 0.1 g/m2 in weight can considerably reduce the electric contact resistance.
3) This steel sheet shows good weldability, high corrosion resistance, good lacquer adhesion and high abrasion resistance due to the combination of metallic tin layer with a chromium plated steel sheet.
Effect of Chemical Composition and Manufacturing Condition on Overheating in Steel for Low Pressure Turbine Rotor
Masaaki KATSUMATA, Isamu TAKAGI, Haruo KAJI
pp. 230-237
Abstract
For low sulphur steels recently used for a low pressure turbine rotor in order to improve mechanical properties, it became to a problem for an onset temperature of overheating to shift low temperature with decrease in sulphur content. Effects of chemical composition and manufacturing conditions on overheating were investigated in 2.83.5Ni-1.7Cr-0.4Mo-0.1V steels. The lowest onset temperature of overheating was obtained in a steel with about 0.005% S. The susceptibility to overheating increased with decreasing the Mn content, but overheating was not observed at heating temperature of 1 350°C by decreasing the sulphur content to less than 0.001% even in a low Mn (0.02%) steel. Cerium addition of 0.024% (Ce/S=4) prevented overheating. Lowering the heating temperatures and/or the finishing deformation temperatures reduced overheating. Overheating was observed at cooling rate widely ranging from 0.5 to 300°C/min, especially remarkable overheating occured at cooling rate of 2 to 170°C/min. It appears that overheating relates to the increase in the volume fraction of MnS precipitated on unite area of intergranular facet (Vs) and that decreases in sulphur and/or Mn contents and rises in heating temperature and/or deformation temperature resulted in coarsening austenite grain and consequently increasing Vs.
Relationship between Ductile Intergranular Fracture and MnS in Overheated Ni-Cr-Mo-V Steel
Masaaki KATSUMATA, Isamu TAKAGI, Haruo KAJI
pp. 238-245
Abstract
Fracture appearance in an overheated Ni-Cr-Mo-V steel for low pressure turbine rotor was characterized as the occurence of intergranular fracture in ductile fracture range. The facet size of intergranular fracture surface corresponded to the austenite grain size of the steel heated at high temperature during heating before forging. The facet size was not changed by re-austenitizing treatment such as normalizing and quenching whose temperature was relatively low. The intergranular facet consisted of small equiaxed dimples and MnS particles located at the bottom of dimples. The number of MnS particles was approximately 50% of the number of dimples. Voids formed at interfaces between MnS particles and matrix, grew and coalesced, and consequently ductile intergranular fracture occured. The decreases in upper shelf energy and reduction of area by overheating were explained by the low strain requisite for void formation at the interface of MnS particle. Coarsening of MnS particles with slow cooling resulted in recovering toughness and ductility due to increasing the strain for void formation. Since most austenite grain boundaries before re-austenitizing were eliminated by re-austenitizing, most ductile cracks propagated in grain interior. Voids nucleated at MnS particles on prior austenite grain boundaries before re-austenitizing, grew and coalesced. Thus, facetted fracture surface was formed similar to ductile intergranular fracture surface. The susceptibility to temper embrittlement was not affected by overheating.
Effect of Solute Elements on Dislocation Substructures Developed during High Temperature Creep in High Chromium High Nickel Steel
Yoshihiro KONDO, Tohru INAZUMI, Masao TAKEYAMA, Takashi MATSUO, Ryohei TANAKA
pp. 246-253
Abstract
The effect of nine solute elements on the dislocation substructures developed during high temperature creep in a 25Cr-35Ni austenitic steel was investigated by TEM at steady state stage at 900 and 1000°C, and was discussed in terms of the frictional stress obtained in the previous works.
Unlike usual understanding, subgrain size does not seem to be an important substructural parameter which determines the creep resistance. The increase in dislocation density with increasing in solute content was correlated well with the increase in the frictional stress, irrespectively of the kinds of solute elements. The temperature dependence of the dislocation density became larger with the addition of solute elements, and the temperature and stress dependences of the dislocation density were the same as the temperature and stress dependences of the frictional stress. The relationship between the logarithm of dislocation density and that of normalized frictional stress can be represented by a single straight line, irrespectively of temperatures and the kinds and amounts of solute elements.
The results conclusively demonstrate that the increase in the frictional stress yielding the increase in creep resistance due to the addition of solute elements corresponds directly to the increase in the dislocation densities.
Characteristics of Bonding Interface and Strength of Hot Rolled Stainless Clad Steel
Takashi FUKUDA
pp. 254-261
Abstract
The composite steel of SUS316L and SM50B made by diffusion and hot roll bonding processes were subjected to the investigations of nature of bonding interface and bonding strengths. The test results obtained are summarized as follows ;
(1) Bonding strength of clad steel increases with increase of bonding temperature and deformation ratio, and reaches the tensile strength of mother steel, when the temperature is over 900°C. And also the bonding strength increases with increase of bonding ratio of the interface. The dependence of bonding ratio becomes larger for KC value, compared with shear or ram tensile strengths.
(2) The bonding strength of clad steel changes, when the clad steel is hold at high temperature. This is caused by the both effects of increased strength of martensite structure and decreased strength of decarbonized layer at bonding zone.
(3) The stable cracks initiate at the defects on bonding interface, propagate accompanied with linkage of each defect and finally lead to debonding of clad steel with small fracture ductility. The behavior of crack initiation is affected by bonding ratio of interface, difference in measuring method of bonding strength and strength of each material composing clad steel.
Fretting Fatigue Strength Analysis of Ti-6Al-4V in Air
Norio MARUYAMA, Masae SUMITA, Kozo NAKAZAWA
pp. 262-269
Abstract
The influence of fretting damage on fatigue strength has been investigated using Ti-6Al-4V alloy. Axial fatigue loading was applied at frequencies of 20 Hz and 0.5 Hz in a laboratory environment with the fretting applied to the specimen central section through a fretting pad made of the same material as the fatigue specimen.
The reduction in fatigue strength due to the fretting damage depended on the contact pressure, p. When the value of p is about 20 MPa, the fatigue life exhibited a minimum. The fretting fatigue crack initiated at the center of the fretted surface. Many micro cracks existed prior to main crack initiation. However, when the value of p is more than 30 MPa, the fretting fatigue crack initiated at the edge of the fretted surface. Few micro cracks existed prior to main crack initiation.
Fretting fatigue cycles more than 90 % of the total life in the interrupted fretting fatigue test are required in order to continue crack propagation after the removal of the fretting pad, although the crack already initiated at cycles less than 50 %.
Stress Corrosion Crack Growth Bihavior of Austenitic Stainless Steel Composite Material in 35% MgCl2 Solution
Hideo NUMADA, Isao TOMIZUKA, Michio YAMAZAKI, Akihiko HOSHINO
pp. 270-277
Abstract
Stress Corrosion Cracking(SCC)in 35%MgCl2 aqueous solution was investigated at 363K for a sheathcore type composite material comprising two types of stainless steel :SUS316L in the core and SUS304 in the sheath. Followings are main points of the obtained information.
a)The value of the KISCC for the composite was lower than those of the component steels.
b)The rate of the crack propagation, which was initially identical with that of SUS304, suddenly decreased at the SUS304/316L interface to a value which was lower than that of either component.
c)After the crack arrived at the SUS304/316L interface, it propagated through SUS304 as Well as through SUS316L, although the rate of propagation was much slower in the latter.
d)The slow rate of propagation in SUS316L in the composite was explained from Evans diagram taking account of a shift of the potential by applied stress.
Effect of Fabricating Conditions on Tensile Strength of B/Al Composite
Yoshikazu SHINOHARA, Koichi HONDA, Akimitsu OKURA
pp. 278-285
Abstract
The effect of hot-pressing conditions such as temperature, time and pressure on the tensile strength of B/Al (1100) composite was investigated quantitatively. The B/Al (1100) composites were prepared invacuum by hot-pressing the sandwiches composed alternately of boron fibers and the thin plates of aluminium. The reaction products at the interface of B/Al were identified by X-ray diffraction and transmission electron microscopy (XRD and TEM). This indicates that the (100) plane of α-AlB12 crystal formed with the interfacial reaction reaction orients in parallel with the aluminium plane at the interface of B/Al. Increasing press temperature, time and pressure led to the degradation of the tensile strength of the B/Al (1100) composite due to the growth of the α-AlB12 phases.
The rule of mixtures was successfully applied to the tensile strength of the B/Al(1100) composite, on the assumption that the notches which were formed by fracture of the α-AlB12 phases caused loss of the tensile strength of boron fibers. The dependence of the tensile strength (σc) of the B/Al (1100) composite on press temperature (T) and time (t) can be expressed by the following equations :
σc=(2Eγs/πX)1/2 Vf + σm( 1-Vf ) (Pa)
X={2 × 10-8 × exp (-16 000/ T) ×t}1/2 (m)
where E is the Young's modulus, γs the surface energy of boron fiber, Vf fiber volume fraction, σm the tensile strength of aluminium and X the thickness of the α-AlB12 phase.
鉄鋼技術とセラミックス技術
岡部 侠児
pp. 286-287
Readers Who Read This Article Also Read
Tetsu-to-Hagané Vol.76(1990), No.1
Tetsu-to-Hagané Vol.76(1990), No.4
Tetsu-to-Hagané Vol.76(1990), No.5
ダンテ(1265~1321)の天国と親鸞(1173~1262)の極楽浄土が示唆する研究施設と生産現場との人材構成の違い
佐野 幸吉
pp. 306-306
Readers Who Read This Article Also Read
Tetsu-to-Hagané Vol.73(1987), No.5
Tetsu-to-Hagané Vol.73(1987), No.5
Tetsu-to-Hagané Vol.73(1987), No.5
Article Access Ranking
07 Sep. (Last 30 Days)
-
Perspectives on the Promising Pathways to Zero Carbon Emissions in the Steel Industry toward 2050
ISIJ International Vol.65(2025), No.2
-
Growth, Removal, and Agglomeration of Various Type of Oxide Inclusions in Molten Steel
Tetsu-to-Hagané Vol.111(2025), No.11
-
Finite Element Analysis of Bubble Growth and Particle Swelling during Coal Pyrolysis
ISIJ International Vol.65(2025), No.9
-
Interface behavior leading to Al/Cu dissimilar metal bonding formation with high-speed eutectic reaction induced by applying current
QUARTERLY JOURNAL OF THE JAPAN WELDING SOCIETY Vol.43(2025), No.2
-
Copper removal of liquid steel containing 0.25 % carbon using Fe2O3-CaCl2-SiO2 flux
ISIJ International Advance Publication
-
Corrosion Behavior of Carbon Steel under Soil Drying Conditions
ISIJ International Advance Publication
-
Cold Spot Joining of 980 MPa-class Ultra-high Strength Steel
Tetsu-to-Hagané Advance Publication
-
Combination Effect of Premixing Conditions and Iron Ore Size Distribution in Sintered Ore Granulation Process with Intensive Mixer
ISIJ International Advance Publication
-
A preliminary study on reduction degradation of iron ore sinter using sinter analogue and X-ray micro-computed tomography (MCT)
ISIJ International Advance Publication
-
Viscosity Measurement of Foam with High Gas Volume Fraction Using Sphere Pull-up and Dam-break Experiments
ISIJ International Advance Publication
You can use this feature after you logged into the site.
Please click the button below.