- TOP
- Tetsu-to-Hagané
- Vol. 75 (1989), No. 9
Tetsu-to-Hagané Vol. 75 (1989), No. 9
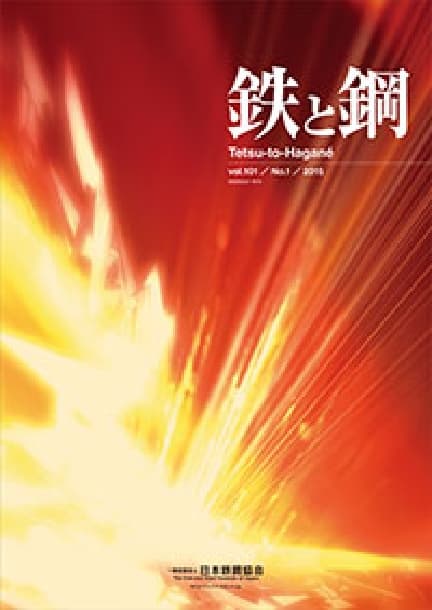
Grid List Abstracts
ONLINE ISSN: | 1883-2954 |
PRINT ISSN: | 0021-1575 |
Publisher: | The Iron and Steel Institute of Japan |
Backnumber
-
Vol. 111 (2025)
-
Vol. 110 (2024)
-
Vol. 109 (2023)
-
Vol. 108 (2022)
-
Vol. 107 (2021)
-
Vol. 106 (2020)
-
Vol. 105 (2019)
-
Vol. 104 (2018)
-
Vol. 103 (2017)
-
Vol. 102 (2016)
-
Vol. 101 (2015)
-
Vol. 100 (2014)
-
Vol. 99 (2013)
-
Vol. 98 (2012)
-
Vol. 97 (2011)
-
Vol. 96 (2010)
-
Vol. 95 (2009)
-
Vol. 94 (2008)
-
Vol. 93 (2007)
-
Vol. 92 (2006)
-
Vol. 91 (2005)
-
Vol. 90 (2004)
-
Vol. 89 (2003)
-
Vol. 88 (2002)
-
Vol. 87 (2001)
-
Vol. 86 (2000)
-
Vol. 85 (1999)
-
Vol. 84 (1998)
-
Vol. 83 (1997)
-
Vol. 82 (1996)
-
Vol. 81 (1995)
-
Vol. 80 (1994)
-
Vol. 79 (1993)
-
Vol. 78 (1992)
-
Vol. 77 (1991)
-
Vol. 76 (1990)
-
Vol. 75 (1989)
-
Vol. 74 (1988)
-
Vol. 73 (1987)
-
Vol. 72 (1986)
-
Vol. 71 (1985)
-
Vol. 70 (1984)
-
Vol. 69 (1983)
-
Vol. 68 (1982)
-
Vol. 67 (1981)
-
Vol. 66 (1980)
-
Vol. 65 (1979)
-
Vol. 64 (1978)
-
Vol. 63 (1977)
-
Vol. 62 (1976)
-
Vol. 61 (1975)
-
Vol. 60 (1974)
-
Vol. 59 (1973)
-
Vol. 58 (1972)
-
Vol. 57 (1971)
-
Vol. 56 (1970)
-
Vol. 55 (1969)
-
Vol. 54 (1968)
-
Vol. 53 (1967)
-
Vol. 52 (1966)
-
Vol. 51 (1965)
-
Vol. 50 (1964)
-
Vol. 49 (1963)
-
Vol. 48 (1962)
-
Vol. 47 (1961)
-
Vol. 46 (1960)
-
Vol. 45 (1959)
-
Vol. 44 (1958)
-
Vol. 43 (1957)
-
Vol. 42 (1956)
-
Vol. 41 (1955)
Keyword Ranking
07 Sep. (Last 30 Days)
Tetsu-to-Hagané Vol. 75 (1989), No. 9
Carbon Fiber Reinforced Carbon Composite Produced with Pitch Binder
Kiyoshi SUDANI, Yukihiro SUGIMOTO, Yoshihiko SUNAMI
pp. 1426-1433
Abstract
The condition to produce carbon fiber reinforced carbon composite (C/C composite) of high performance by hot-pressing has been investigated. Cutted carbon fiber clothes were dipped into the paste consisting of 30-40wt% binder pitch, 60-70wt% coke powder and 160wt% ethyl alcohol, so that the content of carbon fiber in the resulting C/C composite might be maintained at a constant value of about 60wt%. These caron fiber clothes were stacked in a mold and hot-pressed at the pressure of 8MPa in the temperature range from 390°C to 520°C. The hot-pressed product was carbonized at 1 000°C under nitrogen atmosphere, followed by the graphitization up to 2 500°C in argon. The resulting C/C composite has high flexural strength of 200MPa after a pitch impregnation treatment. It has been also confirmed that adequate temperature difference between upper and lower dies can effectively suppress the crack formation in the production of large size C/C composite by hot-pressing, probably due to the easiness of degasing.
Design Problem for Metal Matrix Composites
Mikio MORITA
pp. 1434-1439
Readers Who Read This Article Also Read
Tetsu-to-Hagané Vol.73(1987), No.2
Tetsu-to-Hagané Vol.76(1990), No.7
Tetsu-to-Hagané Vol.76(1990), No.5
Design Method of Composite Laminates with a Controlled Coefficient of Thermal Expansion
Takashi ISHIKAWA, Hisao FUKUNAGA, Koh-ichi ONO
pp. 1440-1447
Abstract
A lamination tailoring technique is proposed in order to control a coefficient of thermal expansion (CTE) of carbon/epoxy composites in a principal direction. This technique consists of two concepts of the thermoelastic invariants and the lamination parameters. The expansion free condition yields to a parabola in the feasible region of the lamination parameters. The calculated curves for a wide range of temperature intersect almost at a point. A laminate with the construction corresponding to this point exhibits a null CTE in one direction in that temperature range. Some experimental results indicate that the present procedure is possible and promising. Controlling to a small negative CTE to cancel an extension of metal part is also feasible.
Wettability and Interfacila Phenomena in Metal Matrix Composites
Ichiro SHIOTA
pp. 1448-1454
Interfacial Reaction of C/Al Composite and Influence of Reaction Product on Its Tensile Strength
Hyung-Suk YOON, Akimitsu OKURA, Hideki ICHINOSE
pp. 1455-1462
Abstract
Interfacial reaction between PAN (Polyachrilonitrile) based and Pitch based carbon fibers and pure aluminium was investigated. The C/Al composite was prepared by depositing aluminium on the surface of carbon fiber in vacuum. The degradation in the tensile strength of C/Al composites was associated with interfacial reaction product, which is aluminium carbide (Al4C3). Al4C3 was observed by transmission electron microscope (TEM) after heat treatment of C/Al composites.
Experimental results is as follows;
(1) The reactivity at the interface between carbon fiber and aluminium differed with the surface structure change, . which ascribes to the internal structure of fiber.
(2) The intrinsic crack length (C0) in C/Al composites can be calculated from the relation between the thickness of reaction product and the tensile strength. These values were 0.036 μm and 0.049 μm of PAN based and Pitch based C/Al composites respectively. The relation between the tensile strength (σ) of composite and the thickness of reaction product (X) can also be expressed as follows, σ= K/(X)1/2, where K is proportional constant. KPAN = 66.4 × 103 [ kg· m-3/2] K/Pitch = 70.8 × 103 [kg· m-3/2]
(3) The activation energy for the formation of Al4C3 at the interface was 63 kcal/mol for PAN based carbon fiber and 82 kcal/mol for Pitch based carbon fiber. These results suggest that the reactivity of PAN based carbon fiber is high in comparison with that of Pitch based carbon fiber at the interface. The high reactivity must be due to the amount of edge carbon atoms on the fiber surface.
Fracture Strength of PCS- SiC Fibers Extracted from Metal Matrix Composite : Effects of Surface Defects and a New Evalution Method
Masayuki KONDO, Yoshikazu IMAI, Hideshi TEZUKA, Akira KOHYAMA
pp. 1463-1469
Abstract
The objectives of this study are to provide an evaluation model of fracture strength for reinforcing fibers and to apply this model to PCS-SiC fiber reinforced composite wires with variations of aluminum alloys as matrices. In the case of high strength composite materials, surface flaws or defects of fibers dominate fracture strength of reinforcing fibers and hence composites. A new model, where fracture strength is evaluated through surface defect density, is proposed as a method of statistical analysis. Mechanical property changes of PCS-SiC fibers during fabrication of Al, Al-Ni and Al-Si matrix composite wires are analyzed by this model. As the first part, fracture toughness of PCS-SiC fibers is derived using the size of "mirror" on fracture surfaces and the obtained value of 1.0 MPam1/2 is applied to the evaluation model. In SiC/Al, the density of surface defects with the sizes from 90 nm to 130 nm increases. The effect of Ni addition to Al is found to suppress the increment of the surface defect density in the same range, whereas Si addition rather degrades the property comparing with the pure Al matrix. These results are consistent to the results of composite wires and prove the applicability of this model to these prroblems.
Development of Advanced SiC/Al Composite Materials Through Microstructural Evaluation and Design
Hideshi TEZUKA, Yoshikazu IMAI, Masayuki KONDO, Akira KOHYAMA
pp. 1470-1477
Abstract
Research and development of advanced high performance SiC/Al-alloy composite materials was performed with the emphasis on correlations between microstructures and mechanical properties. Microstructural investigation was mainly carried out by means of electron microscopy (SEM, TEM, STEM-EDX). Mechanical property was evaluated by tensile test at room temperature and 723 K.
As the scoping study, SiC reinforced composite plates with varieties of alloys were investigated. Mainly from the stand point of interfacial reaction A1050 was selected as matrix material for the next step.
SiC/A1050 preform wires were produced by liquid metal infiltration method. At the first stage, formation of shrinkage cavities and thermal degradation of fiber strength were the dominant issues. Minimizing these issues by process controlling with the help of new ceramic nozzle for drawing and purification of matrix Al, the tensile strength of preform wire has reached to the value of simple rule of mixture.
Al-Ni alloys were selected to improve high temperature strength of the composites. The Microstructural design concept of this system is to utilize matrix strengthening by in-situ composite and to improve interfacial microstructures. TEM inspections of the composites proved the realization of this concept. As the results, the tensile strength of SiC/A1-5.2% Ni preform wires successfully reached to 1.7 GPa at R. T. and 1.5 GPa at 723 K.
Effect of α-AlB12 Phase at Interface on Tensile Strength of Mono-filament B/Al Composite
Yoshikazu SHINOHARA, Koichi HONDA, Akimitsu OKURA
pp. 1478-1485
Abstract
Laminated B/Al films and mono-filament B/Al composites were prepared by ion plating aluminium onto boron films and boron fibers respectively. The formation of the α-AlB12 phase at the boron-aluminium interface and its influence on the tensile strength of the mono-filament B/Al composite were investigated quantitatively. It was found that the α-AlB12 phases were formed continuously on the boron films and the boron fibers and also partially in aluminium matrice in the determining process of boron-diffusion rate into α-AlB12. The activation energy of the formation of the α-AlB12 phase was 130 kJ/mol. Thermal exposure decreased the tensile strength of the mono-filament B/Al composites due to the formation of the α-AlB12 phases at the interface. Relation between the tensile strength of the mono -filament B/Al composite and the thicknness of the α-AlB12phase was represented by a Griffith's equation.
The α-AlB12 phase is brittle and fractures under small strains, forming notches. The formed notch hastens fracture of the boron fiber, resulting in loss of the tensile strength of the mono-filament B/Al composite. The dependence of the tensile strength of the mono-filament B/Al composite on heat treatment conditions can be expressed by the following equation.
σc= 8.3 × 107{exp(-16000/ T )× t } -1/4 (Pa)
where σc is the tensile strength of the mono-filament B/Al composite and T and t are heat treatment temperature and time respectively.
Nickel Induced Recrystallization of Doped Tungsten Wire and Diffusion of Nickel to It
Takehiko ITAGAKI, Takashi KIMURA, Toshiharu KOBAYASHI, Takashi ARM
pp. 1486-1492
Abstract
Nickel-induced recrystallization of tungsten wire was investigated using a lamp-grade tungsten wire of 1mm diameter having a 40 μm thick layer of nickel formed by electrolytic plating. The wire was exposed to hot argon environments of 1 200 to 1 300°C and the resulting microstructural changes were examined in correlation with the distribution of nickel atoms detected by electron probe microanalysis (EPMA).
The examination revealed two different microstructural states corresponding to the primary and the secondary recrystallization. In the primary-recrystallized region extending inwards from the wire periphery, the presence of nickel atoms was detected by EPMA. Individual grains therein were hardly visible with standard technique of optical metallography but clearly observed on a room-temperature fractograph of the wire. These grains had the < 110 > preffered orientation. The secondary recrystallization, on the other hand, was characterized by a coarse grain structure. By applying an immage processing tech nique to one of the EPMA results, it was demonstrated that nickel atoms were enriched in and around the grain boundaries. Although the high temperature strength of the wire was little affected by the recrystal lizations, the ductile brittle transition temperature (DBTT) considerably increased. While DBTT was as low as 200°C for the nickel-free wire even after heat treatment at 1 300°C for 100 h, it was around 400°C and 900°C for the nickel-coated wire after the primary and the secondary recrystallization, respectively.
Readers Who Read This Article Also Read
Tetsu-to-Hagané Vol.73(1987), No.2
Tetsu-to-Hagané Vol.76(1990), No.7
Tetsu-to-Hagané Vol.76(1990), No.5
Multi-layer Coatings for Preventing Diffusion of Nickel into Tungsten Fiber
Takashi ARAI, Toshiharu KOBAYASHI, Takehiko ITAGAKI, Sokichi TAKATSU, Kunio SHIBUKI, Tetsuharu TSUKAMOTO
pp. 1493-1500
Abstract
Attempts have been made to develop multi-layer ceramic barrier coatings over the reinforcing wire in tungsten wire reinforced nickel-base superalloys suitable for their fabrication by a casting technique. Using the processing of chemical vapor deposition, the wire was first coated with a 1 μm thick layer of TiN, then with a 5 μm thick layer of TiC or TiN or Al2O3, and finally with a 1 μm thick layer of Al2O3. It was found that none of these multi-layer coatings was damaged during the composite fabrication by casting.
The most favorable in terms of the barrier effect was the Al2O3-based coating (TiN-Al2O3/Al2O3), which completely inhibitted the nickel-induced recrystallization of tungsten wire even after 1 000 h exposure at 1 200°C. The TiC-based coating (TiN/TiC/Al2O3) was unfavorable because complicated chemical interactions occured especially between TiC and TiN. While the TiN-based coating (TiN/TiN/Al2O3) was structurally similar to the Al2O3-based coating, results were somewhat different since the constituent layers, TiN and Al2O3, had different thickness. The superiority of the Al2O3-based coating was also confirmed by the composite creep-rupture testing.
Readers Who Read This Article Also Read
Tetsu-to-Hagané Vol.73(1987), No.2
Tetsu-to-Hagané Vol.76(1990), No.7
Tetsu-to-Hagané Vol.76(1990), No.5
Carbon Distribution Near Interface between Base and Cladding Steels in Austenite Stainless Clad Steel Sheet
Masayoshi SUEHIRO, Yoshio HASHIMOTO
pp. 1501-1507
Abstract
The distribution of carbon in austenite stainless clad steel sheets which consist of austenite stainless steel (SUS304L) as a cladding steel and 0.01%C steel as a base steel was investigated by means of a computer aided electron probe micro analysis, chemical analysis and emission spectrophotometry. A peak of carbon content near the interface between base steel and cladding steel was observed after hot-rolling and after annealing subsequent to hot-and cold-rolling. A coarse grain region was observed in base steel near the interface. These results were compared to the results calculated by diffusion equations where the carbon diffusion through the interface was considered by a chemical potential gradient of carbon. The calculated results showed the existence of the carbon peak in cladding steel near the interface and a carbon decrease in base steel near the interface, and agreed with results observed. By the comparison between results calculated and observed, the calculation method was confirmed to be applicable to predicting carbon distribution in an austenite stainless clad steel sheet.
Hydrogen Disbonding of Stainless Clad Steels by Cathodic Current
Takahiro KUSHIDA, Takeo KUDO
pp. 1508-1515
Abstract
Hydrogen disbonding of stainless clad steels was examined by "in-situ detection method", which is composed of ultrasonic wave inspection and cathodic hydrogen charging.
Disbonding cracks occurred in the hard martensitic layers in the interface region between high alloy and carbon steel.
Ni and Cr in the high alloy diffuse into the carbon steel, and C in the carbon steel migrates into the intermediate phase to cause the martensitic transformation.
The susceptibility to hydrogen disbonding is affected by the hardness of this layer.
The hardness of the martensitic layer is increased with increasing the carbon content in the carbon steel, which leads to the raised susceptibility to the hydrogen disbonding.
The concentration of hydrogen in the carbon steel under cathodic protection was measured by electrochemical hydrogen permeation method.
The concentration of hydrogen is less than 0.01 mass-ppm under usual cathodic protecting condition.
On the other hand, the threshold concentration of the hydrogen disbonding is more than 0.1 mass-ppm.
So it is thought that there is no possibility of the hydrogen disbonding under the cathodic protection.
Fabrication and Characteristics of Ceramic Whisker and Short Fiber Reinforced Aluminum Alloys
Yoneaki FUJITA
pp. 1516-1525
Readers Who Read This Article Also Read
Tetsu-to-Hagané Vol.73(1987), No.2
Tetsu-to-Hagané Vol.76(1990), No.7
Tetsu-to-Hagané Vol.76(1990), No.5
Fabrication of Potassium Titanate Whisker Reinforced Aluminum Alloy (AC4C) Composite and Their Some Properties
Isao TSUCHITORI, Akira NITTA, Nobuhiko HARA, Hidefumi HARADA
pp. 1526-1533
Abstract
The modified potassium titanate whisker being stabler at higher temperature was developed recently. This whisker was only composed of K2O· 6TiO2 which free from other chemical constitutions and, was used to make the preform with addition of small amount of inorganic binder. This preform was infiltrated aluminum alloy(AC4C) by squeeze casting, and the dimentional change of the composite was very small. Therefore, the K2O· 6TiO2 whisker reinforced aluminum alloy composite with lower volume fraction of the whisker could be fabricated without large deformation and distortion. Some properties of the composites were investigated. Tensile and hardness tests, measurment of elastic modulus, damping capacity, thermal expansion and thermal analysis were carried out. In particular, it was found that this whisker began to react with aluminum over about 1 123 K.
Reinforcement of 6061 Alloy with Potassium Titanate Whisker
Katsuaki SUGANUMA, Teruaki FUJITA, Koichi NIIHARA, Nobuyuki SUZUKI
pp. 1534-1540
Abstract
Feasibility of potassium titanate whisker as the reinforcement of 6061 aluminum alloy was examined. The volume fraction of whisker was 20% and the squeeze casting method was adopted. Tensile test, measurements of Young's modulus and thermal expansion coefficient were performed. Reaction at the whisker/matrix interface was observed by analytical and high resolution transmission electron microscopy.
The strength of the extruded composite reached 410 MPa, which is quite good. TEM obsevation revealed that no severe reaction occurred between the whisker and the matrix though magunesium segregated at the interface. Thus, the potassium titanate whisker is very much stable in the 6061 matrix and it has a good potential as the reinforcement of aliminum alloys because of its low cost.
Readers Who Read This Article Also Read
Tetsu-to-Hagané Vol.73(1987), No.2
Tetsu-to-Hagané Vol.76(1990), No.7
Tetsu-to-Hagané Vol.76(1990), No.5
Effects of HIP Consolidating Temperature on the Mechanical Properties of SiC Whisker Reinforced Aluminum Alloy Composites
Hiroyuki MORIMOTO, Ken-ichiro OHUCHI
pp. 1541-1548
Abstract
The effects of consolidating temperature on the strength, impact value, microstructure and fractograph of SiC whisker reinforced 6061 (1%Mg) and 5056 (5%Mg) composites were studied. The composites were fabricated with a powder metallurgical method using HIP. The optimum consolidating temperature was 625°C (semi-liquid region) for the 6061 composite and 500°C (solid region) for the 5056 composite. The quantitative analysis of Al4C3 using gas chromatography showed that the extent of the reaction between SiC whisker and Al was accelerated by the increase of Mg in the Al alloy. An examination of X-ray diffraction, SEM and EPMA revealed that in addition to Al4C3, the reaction produced Si in the 6061 composite and Mg2Si in the 5056 composite. The degradation of strength and impact value at a higher consolidating temperature was considered to be due to the presence of such coarse reaction products as Mg2Si and Si, coarse Al-Fe (Cr, Mn)-Si precipitates and the decrease of the Mg solution content in the Al rather than because of the decrease of interfacial bonding strength and the damage of SiC whiskers.
Mechanical Properties of SiC Particle Reinforced Aluminum Alloy Composite
Susumu USHIGOME, Kungi YAMAMOTO, Tomomi SOEDA
pp. 1549-1554
Abstract
Some mechanical properties of SiC particle reinforced 6061 aluminum matrix composites were investigated. The composites were fabricated by a powder metallurgical method. Cold pressed green bodies of uniformly mixed powder were consolidated by hot extrusion into 15 mmφ× 1 m bars.
Mechanical properties depend on SiC particle size and content.
In the case of average SiC particle diameter of 7.2 μm, the ultimate tensile strength (σB) of 45 kgf/mm2 was obtained at Vf= 20%, and Young's modulus (E) reached 13 000 kgf/mm2 at Vf= 30%. High temperature tensile strength of composites (Vf= 20%) is more than 30% higher than that of conventional 6061 Al alloy over the testing temperature range.
Development of advanced SiC/Al Composite Materials Manufacturing of Preform Wires by Liquid Metal Infiltration
Yoshikazu IMAI, Yoshikazu TANAKA, Hiroshi ICHIKAWA, Toshikatsu ISHIKAWA
pp. 1555-1562
Abstract
The continuous SiC fiber produced from polycarbosilane, an organosilicone compound, possesses outstanding characteristics and is expected to be an excellent reinforcement for MMC. This study concerned the research and development of the manufacturing process of "preform wires" which are composites with an aluminum matrix and are also semi-finished materials used for the fabrication of SiC/Al.
SiC/Al (A1050) preform wires were produced continuously by the liquid metal infiltration method. The process basically consisted of desizing, dipping for spreading and infiltrating, passing through a nozzle hole and taking up for winding. Each processing condition was tested and improved on.
As an improved condition, after SiC fiber yarn was heated at 1 373K for desizing, it was dipped into a molten aluminum bath at 953K for infiltration and then passed through a ceramic nozzle hole (diameter 0.25 mm). As the results, preform wire with a tensile strength of 1 560 MPa at fiber volume fraction 0.53 was obtained. This strength was about 95 % of rule of mixture, and it is considered that the fiber strength was highly utilized. Consequently, we consider that preform wires may become promising materials for the fabrication of MMC.
Mechanical Properties of Si-Ti-C-O Fiber Reinforced Aluminium Composite
Yoshiharu WAKU, Tadashi YAMAMOTO, Michiyuki SUZUKI, Narihito NAKAGAWA, Tadashi NISHI
pp. 1563-1570
Abstract
In order to clarify the possibility of application of recently developed Si-Ti-C-O fiber to metal matrix composite, the compatibility of Si-Ti-C-O fiber with aluminium alloys and the mechanical properties of Si-Ti-C-O fiber/SiC powder hybrid fiber reinforced aluminium composite fabricated by using a squeeze casting method were investigated.
The main results obtained were summarized as follows.
(1) The drop in tensile strength of Si-Ti-C-O fiber immersed in molten pure aluminium and 6061 aluminium alloy is significantly smaller than that found with SiC(pc) fiber. From this fact, it is found that Si-Ti-C-O fiber has excellent compatibility with aluminium alloys.
(2) For the hybrid fiber reinforced aluminium composite, excellent mechanical properties of high flexural strength of 1.4 GPa in the longitudinal direction and particular high strength of 0.3 GPa in the transverse direction were attained because Si-Ti-C-O fiber uniformly dispersed and did not contact each other.
(3) No fiber surface is exposed in the transverse fracture surface and the dimple pattern showing ductile fracture behaviours is observed. This phenomenon shows that the Si-Ti-C-O fiber and matrix are tightly bonded
(4) Aluminium composite reinforced with the hybrid fiber maintains its flexural strength of 1.13 GPa in the longitudinal direction until approximately 573 K. The flexural strength in the longitudinal direction is not affected by the heat treatment time and has almost constant value during heat treatment at 623 K.
Y2O3 Dispersion Strengthened Ni Base Superalloys
Takashi DAIKOKU, Ikuo OKADA
pp. 1571-1579
Microstructural Control and High Temperature Strength of Oxide Dispersion Strengthened Superalloys
Kazuaki MIND
pp. 1580-1587
Effects of the Amount of γ' Phase on the Creep Strength of the Dispersion Strengthened Ni-base Superalloys
Katsuyuki KUSUNOKI, Yozo KAWASAKI, Shizuo NAKAZAWA, Michio YAMAZAKI
pp. 1588-1595
Abstract
Effect of the amount of γ' phase was studied on the creep strength of an oxide dispersion strengthened nickel-base superalloy TMO-2, and its related alloys in which the γ' content was varied from 35 to 75 %. At middle or low temperature (1 075 to 1 223 K), both the creep resistance and the rupture life increased with increasing the amount of the γ', phase. This is due to the fact that the creep deformation in this temperature range is accompanied by the shear of the γ' particles precipitated in the γ' phase. At high temperature (1 323 K), neither the creep resistance nor the rupture life depended on the amount of the γ' phase. The creep deformation at this temperature is related to the growth of voids or cracks generated at around needle-like carbides precipitated upon creep testing. Creep rupture elongations were very small (14%) in all test condions, and independent of the amount of the γ' phase. At temperatures below 1 233K, DOBES-MILICKA's relation holds among the rupture elongations, rupture lives and the steady state creep rates.
High Temperature Material Properties of Ceramic Particle Composite
Yoshiyasu MORITA, Kazuo OKAMURA, Hisakazu KAWASHIMA, Manabu SEGUCHI
pp. 1596-1603
Abstract
The composite materials consisting of alumina ceramic particles and heat-resistant alloys were manufactured, and both the heat conductivity and compressive creep of composites in the high temperature range were investigated for the purpose of developing a new type of heat resistant material. The compsites containing alumina ceramic particles of 2 or 3 mm diameter in about 50 percent volume fraction were produced by lost wax process. It was made clear that the heat conductivity of the composite was decreased to a half of that of matrix metal in the temperature above 600 K, and the creep strain of the composite at 1 523 K could be decreased to a tens of that of matrix. It was also discussed about the effect of the purity of alumina particles and the component system of matrix metal on the creep strain of the composite.
Effect of Addition of Mo2CoB2, TiH2 and TiC0.7 N0.3 on Mechanical Properties of TiB2 Based Ceramics
Tadashi TAKAHASHI, Makoto MURAI, Yoshikazu KONDO
pp. 1604-1611
Abstract
The addition of Mo2CoB2 and TiH2to the TiB2 improved the density, the bending strength and other properties. Especially, the additions of 15wt %Mo2CoB2 and 2wt %TiH2 brought the highest bending strength as 149 kgf/mm2 and high hardness as HV2 800. Sliding wear test against mild steel showed that TiB2-TiH2-Mo2CoB2 ceramics have relatively little specific wear rates compared with SiC, Si3N4, ZrO2 but have large specific, wear rates compared with Al2O3 and cemented carbides (D10). Specific wear rates of TiB2 based ceramics could be decreased less than Al2O3 and cemented carbides (D10) by the addition of TiC0.7N0.3 without lowering the bending strength. Furthermore this ceramics have good abrasive wear resistance.
Microstructures and Mechanical Properties of Si3N4-BN Composite Ceramics Produced by Slipcasting Method
Keiichiro ISOMURA, Toshiaki FUKUDA, Kazuki OGASAHARA, Toshihiko FUNAHASHI, Ryoji UCHIMURA
pp. 1612-1619
Abstract
A new type of Si3N4-BN composite ceramics (SNB ceramics) has been developed using an unique slipcasting method which utilizes homogeous mixing of ultra-fine constituent ceramics powders (Si3N4, BN), and gas pressure sintering. An important feature of the SNB ceramics in the present work is that their mechanical properties can be tailored by changing BN/Si3N4 ratio over a wide range. The SNB ceramics have excellent thermal shock resistance, and machinability while retaining relatively high strength. In this paper, microstructures and various mechanical properties of the SNB ceramics are described.
Sliding Wear Characteristics of Iron Containing Multiple Boride Base Cermet
Tadao WATANABE, Tsuneyuki IDE, Ken-ichi TAKAGI, Yoshikazu KONDO
pp. 1620-1627
Abstract
An advanced iron containing multiple boride base cermet has been developed. This new type of cermet consists of a Mo2FeB2 type complex boride as a hard phase and a ferrous binder phase has excellent wear and corrosion resistance. The dry adhesive wear properties of the cermet against mild steel and alloy steels were studied by Ogoshi wear tester (a ring-on-block type) at sliding velocities of 0.1 m/s to 4.39 m/s. The wear characteristics were compared with that of high speed steel and cemented carbide. From the experiments, results were summarized as follows ;
(1) The sliding wear characteristics of the boride cermet against mild steel at low sliding velocity are very similar to that of steels due to the ferrous binder phase, however, quite different from that at middle and high sliding velocity range presumably due to its hard phase.
(2) The wear characteristics of the boride cermet and cemented carbide against hard steels (SKH3, SUJ2, SKD11 and SUS440C ) significantly depend on the counter materials. The specific wear rate ( Ws) of the boride cermet against SKH3 and SUJ2 is nearly the same as cemented carbide, and the Ws of this cermet against SKD11 and SUS440C is less than that of cemented carbide.
Readers Who Read This Article Also Read
Tetsu-to-Hagané Vol.73(1987), No.2
Tetsu-to-Hagané Vol.76(1990), No.7
Tetsu-to-Hagané Vol.76(1990), No.5
Production and Properties of Carbide Dispersion-strengthened Coppers by Compocasting
Kiyoshi ICHIKAWA, Masakazu ACHIKITA
pp. 1628-1635
Abstract
An investigation was made for the electrical and mechanical properties of dispersion-strengthened (DS) coppers compocast at 25 rev/s and with the addition of fine carbide particles in the range of 0.5 to 30 mass% WC, TaC, VC, TiC, NbC, ZrC, Mo2C, Cr3C2 and Al4C3. Homogeneous distribution of carbides was observed in the microstructures of the compocast DS coppers except with the addition of Mo2C, Cr3C2 or Al4C3. The measured values of electrical conductivity of the DS coppers were 77.9 %IACS at 20 mass%WC, 73.4 %IACS at 20 mass%TaC, 72.0 %IACS at 10 mass%NbC, 85.2 %IACS at 5 mass%TiC and 68.9%IACS at 5 mass%VC. The values of Vickers hardness were 197 at 30 mass%WC, 155 at 30 mass%NbC, 110 at 30 mass%TaC, 158 at 20 mass%VC and 121 at 20 mass%TiC. The values of ultimate tensile strength were 402 MPa at 30 mass%NbC, 357 MPa at 20 mass%TiC, 330 MPa at 20 mass%WC, 269 MPa at 20 mass%TaC and 323 MPa at 10 mass%VC. The values of elongation were 12.9 % at 20 mass%TaC, 10.9 % at 20 mass%WC, 25.2 % at 10 mass%NbC, 21.8 % at 10 mass%VC and 17.5% at 5 mass%TiC.
Effect of Intermediate Layer on Weldabilities in Steel-plastic-steel Laminates
Masatoshi SHINOZAKI, Yoshihiro MATSUMOTO, Kohki SATOH, Yasunobu UCHIDA, Noboru NAKANO
pp. 1636-1643
Abstract
Effect of intermediate layer on weldabilities has been studied in steel-plastic-steel laminates. Acceptable welds can be obtained, when the electric resistance at the first cycle of spot welding is less than 0.6 mΩ. To obtain the suitable resistance, the control of thickness of the intermediate layer, diameter of electric-conductive particles, ratio of the thickness and diameter, and content of the particles are important. The intermediate resin layer is harmful of arc welding and laser welding ; thinner layer is preferable.
Spot Weldability of the Vibration Damping Steel Sheet
Yoshiki TANAKA, Motoo SATO, Yoshiyuki YUTORI, Kazuhiko KOORIDA
pp. 1644-1650
Abstract
The improvement in spot weldability of a vibration damping steel sheet has been studied by mixing iron particles in the no-conductive resin film sandwiched by steel sheets. The influences of the particle size and the volume fraction has been investigated in relation to the occurrence of pinholes and micro-sparks. These defects are eliminated by using mixture of 3 volume percent particles where the particle diameter is 1.5 times the film thickness. The vibration damping steel sheet produced under these conditions shows good spot weldability without any bypass circuits, as well as high damping property.
Development of Conductible Vibration Damping Steel Sheet
Mizuo EJIMA, Hiroshi ENDO, Taizo NAKAMURA, Jun-ichi MORITA, Shigeru HORISAWA
pp. 1651-1658
Abstract
To get rid of defects of ordinary vibration damping steel sheets, studies were caned out to improve weldability and thermo-endurance in the baking temperature of cosmetic coatings. It has been shown that weldability can be obtained by adding to the resin layer conductive metal particles by 5 to 40 wt % to the resin layer. The diameter (δ) of Metal particle must satisfy the following equation, with regard to the thickness of the resin layer (T) : T/δ= 1.0 1.2 In addition, new thermosetting resins with both good vibration capability and good thermo-endurance have been developed by using the bridging reaction of curring agents between moleculas of the thermoplastic polyester resin. Based on these new findings, a new manufacturing process of coiled products of conductible vibration damping steel sheets has been established.
Readers Who Read This Article Also Read
Tetsu-to-Hagané Vol.73(1987), No.2
Tetsu-to-Hagané Vol.76(1990), No.7
Tetsu-to-Hagané Vol.76(1990), No.5
Effect of Hardening Agent Content on Durability of Composite Damping Steel Sheets Used Thermosetting Type Resin
Yoshihiro MATSUMOTO, Fuminori MUKAIHARA, Yasunobu UCHIDA, Tadahiro WAKUI
pp. 1659-1665
Abstract
The composite damping steel sheets were made using thermosetting resin composed of saturated polyester and isocianate type hardening agents as polymer. They had high damping properties at room temperature. The effects of crosslinking system on chemical and thermal durability were studied. In chemical resistance, adhesive strength and damping properties did not change after soaking in hydrocarbons or alcholic solvents. However, for MEK or aceton, the adhesive strength was slightly decreased, suggesting gradual dissolution of the polymer in such polar solvents. In thermal resistance, the adhesive strength sligthly increased and the damping capability with increasing temperature up to 200°C also slightly changed. It may be due to futher reaction of the polyester with unreacted isocianates at an elevated temperature. An increase of crosslinking density may increase the adhesive strength and decrease the damping capbility at low temperature range. It is concluded that a proper selection of saturated polyester and hardening agents provide the possibility of production of the composite damping steel sheets having high damping properties at room temperature and high chemical and thermal durability.
Improvement of Damping Capacity and Adhesion of Vibration-damping Steel Sheets by Polymer Alloy Technique
Yukichi WATANABE, Yasushi FUJII, Akihiko NISHIMOTO
pp. 1666-1672
Abstract
The relationship between damping capacity of vibration-damping steel sheets (VDS) and viscoelasticity, measured by dynamic test, of damping resins as been investigated by using polymer and polymer alloy.
Damping capacity has a tendency to be proportionally increased not only to tanδ ( mechanical loss tangent), as predicted by the formula proposed by CREME et al, but also dynamic modulus of damping resins. Damping capacity caluculated by KERWIN'S formula is in good agreement with observed value on high frequency range.
The relationship between tensile shear strength of VDS and dynamic modulus of damping resins has been also investigated. Tensile shear strength is increased by using damping resins of high dynamic modulus.
Polymer is difficult to achieve high tanδ and high dynamic modulus. On the other hand, polymer alloy which is mixture of a high tanδresin and a resin of high dynamic modulus possesses these two properties, and VDS used this polymer alloy as damping resin can be achieved high damping capacity and high tensile shear strength.
Application of Finite Element Simulation to Material Design of Steelplastic Laminated Sheets
Koji HASHIMOTO, Mizuo EJIMA, Michio TAKITA, Akitake MAKINOUCHI
pp. 1673-1679
Abstract
Elastic-plastic finite element method has been applied to the bending process of steel-plastic laminated sheets. It is confirmed that the forming defects such as deformed geometries, which are often found in bending process of steel-plastic laminated sheets, can be simulated, for different kinds of core resins and different thickness compositions of skin sheets, exactly by using this simulation method.
Computational results show some important aspects of material design, by which deformed geometries of steel-plastic laminated sheets are expected to be eliminated. The findings obtained here are as follows;
(1) Deformed geometries of bending process can be eliminated by raising the yield strength or plasticity coefficient of resin. However, this may be accompanied by the thickness reduction of outer skin sheets, resulting in a fracture.
(2) Deformed geometries can be decreased by increasing the thickness ratio of inner and outer steel sheets. This method is more effective when thinner skin steel sheet is used for outer side.
(3) The effect of using steel sheets with different yield strength for inner and outer sheets is smaller than those of using wide die opening and using skin sheets of different thickness for inner and outer sheets.
Manufacturing Techique for Stainless Steel Clad Plates by Enshrouding Casting and Rolling Process
Hidenari KITAOKA, Ikuo YARITA, Akira KAWAHARADA, Tetsuya Fuii, Taketo OKUMURA, Shouichi SENGAN
pp. 1680-1687
Abstract
Coating conditions of organic polymers on the cladding metal surface are found to form a film of suitable thickness; thus, reoxidation of the cladding metal surface and scum entrainment can be completely prevented, resulting in satisfactory bonding at the interface between cladding metal and base metal.; An effect of hot top on a remelting behaviour of the cladding metal has been investigated. The plate with low clad ratio is realized by applying the proper hot top condition. In order to achieve uniform distribution of clad ratio and flatness in the product, new rolling and levelling methods have been developped by investigating deformation behaviour during the slab and plate rollings and levelling processes of the two-layer stainless-carbon steel clad plate.
Increase of the Ratio of Fatigue Limit to Tensile Strength after Tensile Prestrain in the Surface Layer Strengthened Hot Rolled Steel Sheet
Yoshio HASHIMOTO, Masaya MIZUI, Tomoo SEKINE, Shinichi NISHIDA
pp. 1688-1694
Abstract
A study has been made of the plane bending fatigue strength of the surface layer strengthened hot rolled steel sheets produced by austenite range rolling of cast composite ingot which in the surface layers, about 0.1%C-0.5 %Mn are added on the 0.08 %C-0.8%Mn base composition and also of the stainless clad hot rolled steel sheets. Following results are obtained.
(1) The ratio of fatigue limit to tensile strength (RFT) in the 8 % tensile prestrained surface layer strengthened hot rolled steel sheet is about 0.65 at 10 % surface fraction. In this case, dislocation hardening due to high work hardening properties in the surface and inner layers, and compression residual stress in the inner layer have increased fatigue limit of composite steel sheet.
(2) Fatigue crack initiates from inner layer in the stainless clad hot rolled steel sheets. The calculated RFT of inner layer becomes about 0.62. This value is higher than that of inner layer only, namely 0.44.
(3) It is thought that in the surface layer strengthened hot rolled steel sheet, the surface fraction at which RFT is highest becomes smaller by the tensile prestrain.
Microstructure of Reaction Phases and Interfacial Strength in Diffusion Bonding of Pure Ti to Pure Fe
Shigeharu HINOTANI
pp. 1695-1702
Abstract
The microstructure and the interfacial strength have been studied for the diffusion bonding pairs between a commercially pure Ti and Fe-0.003 wt%C or Fe-0.015 wt%C.
The transformation of α-Ti into β-phase and the formation of intermetallic compounds (TiFe and TiFe2) were induced by the interdiffusion in Ti/Fe-0.003 wt%C bonding pairs. During the cooling to room temperature, β-phase layer with higher Fe content retained in /β-phase, whereas β-phase layer with lower Fe content transformed into α'-Ti martensite. The specific crystallographic orientation relationship ; (0001)TiFe2//(101)α-Fe [1120]TiFeTiFe2//[111]α -Fe (Burger's relationship) was obtained between TiFe2 and α-Fe.The result indicates that TiFe2 was formed in α-Fe by the diffusion of Ti-atoms.
In Ti/Fe-0.015 wt%C bonding pairs, /β-transformed layer and intermetallic compound layer were not observed at the bonding temperatures below 1 073 K. In this case, TiC precipitates formed along the interface and they hindered the interdiffusion of Ti- and Fe-atoms. However β-transformed layer and intermetallic compound layer formed at the bonding temperature above 1 123 K.
The interfacial strength of Ti/Fe-0.003 wt%C bonding pairs depended on the width of intermetallic compound layer ( WIM). At the initial stage of bonding the strength was very low due to the inadequate diffusion, but it increased to the level of 300 MN m-2 in the WIM range between 0.4 and 1.2 μm. The strength decreased rapidly again after the growth of intermetallic compound layer thicker than 1.2 μm.
Deformation Behavior in Compression in an FCC/BCC Laminated Fe-Cr-Ni Alloy
Yo TOMOTA, Takashi KURODA
pp. 1703-1710
Abstract
The FCC and BCC Fe-Cr-Ni alloys sheets were laminated alternatively, then heated up to 1 273 K and bonded under the applied stress of 28 MPa. The thickness of each layer was approximately 600 μm. The cubic compression test specimens were cut from the laminated composite material, where three directions, i.e., the compression axis of 0°, 45° and 90° against the normal direction of each component layer were adopted(hereafter they are called 0°, 45° or 90° specimen). Some specimens were aged at 753 K for 360 ks to enlarge the strength of high Cr BCC layers. The bonded interface seemed to be so strong that no decohesion was observed by the compression test down to the strain of 30%.
The 90° specimen has shown the largest flow stress and the 0° one slightly smaller. The 45° specimen deforms in a distinguished anisotropic manner and has shown the lowest flow stress. This trend is emphasized when the strength of the BCC layer is enlarged. These results are discussed from the standing points of inhomogeneous deformation, the thickness of the layer, and the size of test specimen.
Erosion of Ceramic Particle Composite Products for Pipe Transportation
Yoshiyasu MORITA, Hisakazu KAWASHIMA, Manabu SEGUCHI
pp. 1711-1718
Abstract
The erosion of the metal-ceramic particles dispersion composite materials was experimented for the purpose of improving the erosion resistance of the elbow for the transportation line of solid particles. The composite flat plates were made by casting method adding the alumina particles of 3 mm diameter into each matrix. The effects of the impingement particle and the impingement angle on the erosion of the composite were investigated. It was made clear that the erosion ratio of the composite was decreased to a half of the average value of the matrix only. Then, the improvement of the erosion resistance of the trial composite elbow was confirmed.
Readers Who Read This Article Also Read
Tetsu-to-Hagané Vol.73(1987), No.2
Tetsu-to-Hagané Vol.76(1990), No.7
Tetsu-to-Hagané Vol.76(1990), No.5
Strength and Failure Process of Continuous Fiber-reinforced Metals
Yutaka KAGAWA, Akimitsu OKURA
pp. 1719-1729
A Computer Simulation Experiment on Influences of Yield Stress and Ductility of Matrix on Tensile Strength of Continuous Fiber-reinforced Metal Matrix Composites
Shojiro OCHIAI, Kozo OSAMURA
pp. 1730-1737
Abstract
Influences of yield stress and ductility of matrix on tensile strength of unidirectional continuous fiber-reinforced metal matrix composites with high interfacial bonding strength were studied by means of a Monte-Carlo computer simulation method. In the case where the ductility of matrix was high, the strength of composites increased with increasing yield stress of matrix but the efficiency of reinforcement became low at high yield stress. In this case, the strength decreased monotonically with increasing scatter of strength of fiber when the yield stress was low, while it decreased, reaching minimum, and then increased when the yield stress was high. In the case where the ductility of matrix was low, the strength was low especially when the volume fraction of fiber was high and scatter of strength of fiber was large. Depending on the values of yield stress and ductility of matrix, following cases were found; the case where the strength increased linearly with inctreasing volume fraction of fiber and it was approximately described by the rule of mixtures, the case where the strength was approximately described by the rule of mixtures when volume fraction of fiber was low but it became lower than the same rule when the volume fraction was high, and the case where the strength increased linearly with increasing volume fraction of fiber but it was much lower than the rule of mixtures.
Readers Who Read This Article Also Read
Tetsu-to-Hagané Vol.73(1987), No.2
Tetsu-to-Hagané Vol.76(1990), No.7
Tetsu-to-Hagané Vol.76(1990), No.5
Strength of B/Al Estimated by Computer Simulation Based on Shear-lag Theory
Hideharu FUKUNAGA, Yoshihiro TAKAHASHI
pp. 1738-1744
Abstract
The computer simulation method based on the shear-lag theory was proposed to predict the tensile strength of the unidirectional ceramic fiber reinforced metal composites, in which the elastic-linear hardening behavior of matrix was taken into consideration. The boron fiber reinforced aluminum composites were prepared by hot-pressing technique, and tested to check the tensile strength. The average strength of the composites (Vf = 11%) showed the good agreement between the predicted value and the experimental value. By using the simulation method, the size effect of the fiber reinforced metal was predicted. There was very small effect of inter-fiber spacing on the average tensile strength, but the average strength of composites decreased slightly with increase in number or reinforced fibers.
Transverse Fracture Behavior of Unidirectionally-reinforced Carbon Fiber Aluminum Composite under Mixed Mode Condition
Yutaka KAGAWA, Teruo KISHI
pp. 1745-1752
Abstract
Transverse failure behaviors of unidirectionally-reinforced continuous carbon fiber (M40) reinforced aluminum (A1100) matrix composite under crack opening (mode I ), forward shearing (mode II), and their combined mode have been investigated. A modified form of ARCAN'S fixture was used to obtain mixed mode fracture behavior and fracture toughness. Transverse teusile elastic modulus and strength of the composite were also obtained.
Results showed that the elastic modulus of the composites was 23.5 GPa and was smaller than that of the matrix. The transverse tensile strength was 18 MPa and was approximately 1/10 of longitudinal one. It was found that the values of KIc was larger than KIIc. The fracture behavior of the composite varied with the ratio of applied mode I and mode II component. The KI - KII relation did not obey theoretically-obtained quadratic relation. This behavior was explained by crack shielding mechanism due to crack bridging by thin composite wire. The efficacy of crack shielding varied with the-ratio of applied mode I and mode II component.
Fatigue Fracture Mechanisms for SiC Whiskers and SiC Particulates Reinforced Aluminum Composites
Chitoshi MASUDA, Yoshihisa TANAKA
pp. 1753-1760
Abstract
Fatigue property was examined for three commercially fabricated aluminum matrix composites containing SiC whiskers and particles under rotating bending in laboratory air. Fatigue strength at 107 was about 67% higher for composite than that for matrix alloy, while for SiCp/A356 and SiCp/A357 composites the fatigue strengths of those composites were also higher than that for matrix alloy. Fractography revealed that mode II crack propagated through the whisker/matrix or particle/matrix interface for SiCw/A2024 and SiCp/A357 composite materials. On the other hand, for SiCp/A356 composite material crack initiated at some small voids situated beneath the surface of the specimens. In the region of fatigue crack propagation the crack arrested to the whiskers or particles for small crack length (or lower stress level), while for longer crack length (or higher stress level) voids or sub crack around the whiskers or particles situated ahead of the main crack. Mode I and Mode II fatigue crack propagation models was proposed and those models could discuss the increase of fatigue strength of composite materials in comparison to matrix materials.
Evaluation of Strength Distribution in Boron Fiber Reinforced Aluminum Matrix Composites by Recursion Analysis Technique
Koichi GODA, Hideharu FUKUNAGA
pp. 1761-1768
Abstract
The present work tries to apply the recursion analysis technique to boron fiber reinforced aluminum matrix composites. Several sizes of comopsites ( Vf : 0.10 0.15) prepared by hot-press were used as the test materials. The tensile strengths of filament and composite specimen were measured several times. On the other hand, Weibull parameters of the strength of fibers were estimated from the measured data, from which recursive distribution curves were predicted. The results showed that the strength of composites gradually decreased with increasing the size of composites. The recursive curves indicated appropriately such a tendency, i.e. agreed well with the Weibull plots of experimental data. This means the recursion analysis technique can be applied to the evaluation of strength distribution of boron fiber reinforced aluminum matrix composites in a laboratory scale. In addition, the effect of 2-parameter and bi-modal Weibull distribution on the recursive solusion was discussed.
Fracture Behavior and Scatter of Strength in SiC Whisker Reinforced Glass Composite
Yasuo KOGO, Yutaka KAGAWA
pp. 1769-1776
Abstract
Fracture behavior of SiC whisker-reinforced borosilicate glass composites was investigated and the relation between the failure process and scattering of strength is discussed. Both un-notched and notched specimens were used for the fracture test. Acoustic emission signals were also monitored to clarify the failure process.
The strength and fracture toughness of the composite were larger than that of monolithic borosilicate glass. Fracture of the composite initiated at an early stage of loading. Results of Acoustic Emission revealed that the microscopic scale failure occured cumulatively during the stable failure process and this behavior was completely different from that of the glass matrix.
The scatter of strength in the composite was smaller than that of the monolithic glass matrix. This difference seemed not only to be dependent on size variation of largest defect in the composites but also on difference in the failure process.
Development of Alumina-fiber/Aluminum Composite Impeller
Akiyoshi MIZIJTA, Toshinori NAKAMURA, Kuniyasu SAKAI
pp. 1783-1789
Abstract
Recently, fiber-reinforced metal (FRM) has called much attention in various fields of industry where high strength-to-weight ratios are requied, such as jet-engine parts and structure members of aircraft. In order to fabricate alumina-fiber/aluminum composite, we tried to develop a method to incorporate molten aluminum alloy into reinforcing fibers by pressurized casting method. This method was applied to investment moulds for precision castings, and consequently complex and large composite products, such as impellers, were produced more easily than conventional method.
In this paper we investigated desired properties of alumina-fiber/aluminum a composite impeller for gas turbine engines and manufacturing method. Prototype impeller had good composite structure and improved tensile strength. But the results were not satisfactory enough.
Application of Metal Matrix Composites to Diesel Engine Pistons
Tetsuya SUGANUMA, Atsuo TANAKA
pp. 1790-1797
Abstract
Aluminum based FRMs : Fiber Reinforced Metals (MMCs : Metal Matrix Composites) have been in use for the top ring groove of Toyota's diesel engine pistons since 1982.
At first, "KAOWOOL® " (alumina-silica short fiber) FRM as a standard grade and "SAFFIL®" (alumina short fiber) FRM as an upper grade were developed. These FRMs showed good wear resistance, well as higher thermal conductivity and lower thermal expansion than conventional "Niresist" cast iron as the piston ring groove.
In the next step, corresponding to the demands for lower cost with higher strength and superior wear resistance, "ALSILON®" FRM was developed in 1987. The "ALSILON® " (crystalized alumina-silica short fiber) FRM gives both as good performance as "SAFFILL® " FRM and as low cost as "KAOWOOL® " FRM.
In the 3rd step, a new type of MMC has been developed in 1988 to improve higher temperature durability. The MMC is composed of hybrid reinforcements of the "ALSILON® " and NiAl3 intermetallic compound particulates uniformly dispersed in the aluminum matrix. The NiAl3 particulates are formed by in-situ procesing and exhibits excellent adhesive wear resistance.
Thus, the MMC pistons have made a steady progress in the field of material and processing technology and their mass, production scale has successfully increased up to more than 200 000 pieces/month (2.4 million pistons/year).
Readers Who Read This Article Also Read
Tetsu-to-Hagané Vol.73(1987), No.2
Tetsu-to-Hagané Vol.76(1990), No.7
Tetsu-to-Hagané Vol.76(1990), No.5
Noise Reduction Effect of Damping Steel Sheets for Building Roofs, V-Deck D 88
Hiroyuki NAGAI, Toshiaki SHIOTA, Hiroshi NISHIKAWA, Shigeyoshi SUGIYAMA
pp. 1798-1804
Abstract
The noise reduction effect of the damping steel sheets has been studied by a single ball impact test and an artificial shower test for building roofs. The shape of test specimens were flat sheet and V-Deck D88. This study has resulted in the following 4 points.
(1) The noise reduction effect of damping steel steet was very large (about 6 dB) in the case of V-Deck D88, and that was not so large (about 2 dB) in the case of flat sheet.
(2) The noise reduction effect of damping steel sheets, as same as the logarithmic decrement, increases as the frequency hightens.
(3) The difference of the noise reduction effect between flat sheet and V-Deck D88 can be explained by the frequency dependency of sound pressure level, i.e. in the case of V-Deck D88, sound pressure level is large at the higher frequency region where the noise reduction effect is large, but in the case of flat sheet it is not so large at this region.
(4) The effect of nozzle diameter in the artificial shower test is not so large on the noise reduction effect of damping steel sheets.
Floor Impact Sound Control by Composite Damping Floor Structure Composed of Damping Steel Plates and Concrete Slab in Multiple-dwelling Buildings
Atsushi NINOMIYA, Minoru HIROTA, Norio CHIBA
pp. 1805-1812
Abstract
The composite damping floor structure (CDFS) has been developed for the control of the floor impact sound against the Heavy-Impact-Sound-Source designated by JIS A1418 in multiple-dwelling buildings. CDFS has the three-layer sandwich configuration by attaching rectangular damping steel plates (DSP) to the concrete slab. The first layer is the constraining steel plate (the upper steel), the second is the vis-co-elastic resin, and the third is the basic plate (the lower steel and concrete slab).
The traditional vibration damping theory for such sandwich configuration structure was extended in order to introduce the effect of the unit width of each rectangular DSP. The extended theoretical analysis explained the vibration loss factors obtained on the floor model tests and on the site tests with good agreement.
And also the test results of the floor impact sound radiation were explained theoretically by evaluating the effect of the loss factor on the vibration response of CDFS.
Finally the optimum design approach of CDFS was proposed focussing on the unit width and thickness arrangement of each DSP and on the mechanical properties of the resin through the parametric study based on the extended vibration damping theory.
Article Access Ranking
07 Sep. (Last 30 Days)
-
Perspectives on the Promising Pathways to Zero Carbon Emissions in the Steel Industry toward 2050
ISIJ International Vol.65(2025), No.2
-
Growth, Removal, and Agglomeration of Various Type of Oxide Inclusions in Molten Steel
Tetsu-to-Hagané Vol.111(2025), No.11
-
Finite Element Analysis of Bubble Growth and Particle Swelling during Coal Pyrolysis
ISIJ International Vol.65(2025), No.9
-
Interface behavior leading to Al/Cu dissimilar metal bonding formation with high-speed eutectic reaction induced by applying current
QUARTERLY JOURNAL OF THE JAPAN WELDING SOCIETY Vol.43(2025), No.2
-
Copper removal of liquid steel containing 0.25 % carbon using Fe2O3-CaCl2-SiO2 flux
ISIJ International Advance Publication
-
Corrosion Behavior of Carbon Steel under Soil Drying Conditions
ISIJ International Advance Publication
-
Cold Spot Joining of 980 MPa-class Ultra-high Strength Steel
Tetsu-to-Hagané Advance Publication
-
Combination Effect of Premixing Conditions and Iron Ore Size Distribution in Sintered Ore Granulation Process with Intensive Mixer
ISIJ International Advance Publication
-
A preliminary study on reduction degradation of iron ore sinter using sinter analogue and X-ray micro-computed tomography (MCT)
ISIJ International Advance Publication
-
Viscosity Measurement of Foam with High Gas Volume Fraction Using Sphere Pull-up and Dam-break Experiments
ISIJ International Advance Publication
You can use this feature after you logged into the site.
Please click the button below.