- TOP
- Tetsu-to-Hagané
- Vol. 55 (1969), No. 4
Tetsu-to-Hagané Vol. 55 (1969), No. 4
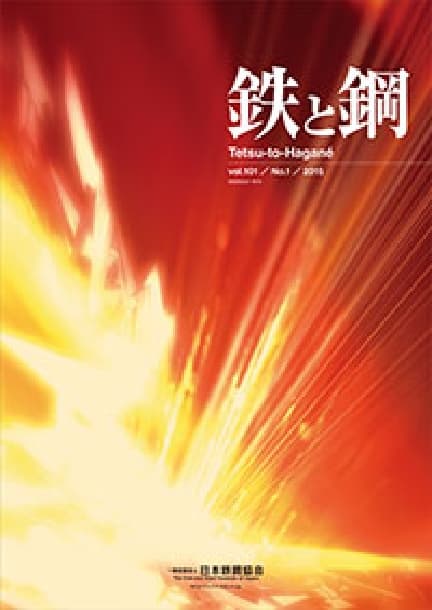
Grid List Abstracts
ONLINE ISSN: | 1883-2954 |
PRINT ISSN: | 0021-1575 |
Publisher: | The Iron and Steel Institute of Japan |
Backnumber
-
Vol. 111 (2025)
-
Vol. 110 (2024)
-
Vol. 109 (2023)
-
Vol. 108 (2022)
-
Vol. 107 (2021)
-
Vol. 106 (2020)
-
Vol. 105 (2019)
-
Vol. 104 (2018)
-
Vol. 103 (2017)
-
Vol. 102 (2016)
-
Vol. 101 (2015)
-
Vol. 100 (2014)
-
Vol. 99 (2013)
-
Vol. 98 (2012)
-
Vol. 97 (2011)
-
Vol. 96 (2010)
-
Vol. 95 (2009)
-
Vol. 94 (2008)
-
Vol. 93 (2007)
-
Vol. 92 (2006)
-
Vol. 91 (2005)
-
Vol. 90 (2004)
-
Vol. 89 (2003)
-
Vol. 88 (2002)
-
Vol. 87 (2001)
-
Vol. 86 (2000)
-
Vol. 85 (1999)
-
Vol. 84 (1998)
-
Vol. 83 (1997)
-
Vol. 82 (1996)
-
Vol. 81 (1995)
-
Vol. 80 (1994)
-
Vol. 79 (1993)
-
Vol. 78 (1992)
-
Vol. 77 (1991)
-
Vol. 76 (1990)
-
Vol. 75 (1989)
-
Vol. 74 (1988)
-
Vol. 73 (1987)
-
Vol. 72 (1986)
-
Vol. 71 (1985)
-
Vol. 70 (1984)
-
Vol. 69 (1983)
-
Vol. 68 (1982)
-
Vol. 67 (1981)
-
Vol. 66 (1980)
-
Vol. 65 (1979)
-
Vol. 64 (1978)
-
Vol. 63 (1977)
-
Vol. 62 (1976)
-
Vol. 61 (1975)
-
Vol. 60 (1974)
-
Vol. 59 (1973)
-
Vol. 58 (1972)
-
Vol. 57 (1971)
-
Vol. 56 (1970)
-
Vol. 55 (1969)
-
Vol. 54 (1968)
-
Vol. 53 (1967)
-
Vol. 52 (1966)
-
Vol. 51 (1965)
-
Vol. 50 (1964)
-
Vol. 49 (1963)
-
Vol. 48 (1962)
-
Vol. 47 (1961)
-
Vol. 46 (1960)
-
Vol. 45 (1959)
-
Vol. 44 (1958)
-
Vol. 43 (1957)
-
Vol. 42 (1956)
-
Vol. 41 (1955)
Keyword Ranking
29 Aug. (Last 30 Days)
Tetsu-to-Hagané Vol. 55 (1969), No. 4
Activities in the Iron-Oxide Silica Slags
Haruhiko FUJITA, Shigeaki MARUHASHI
pp. 249-260
Abstract
The distribution of oxygen between molten iron and silica-iron oxide slags was determined at 1560°C and the results were used to determine the activities of the components in the iron oxide-silica system.
The activity of iron oxide changes from positive deviation from ideality at low silica concentration to negative deviation beyond 0.28 mole fraction of silica.
At the silica saturated composition, a value of 0.455 for the iron oxide activity was obtained.
The activity of silica, which is calculated from GIBBS-DUHEM equation, shows considerable positive deviation from ideal behavior for any composition where silica concentration is greater than about 0.1 mole fraction.
The free energy of formation of liquid fayalite in the melt was calculated through the activity data.
These activity data give a value of -5.45 kcal/mol at 1560°C-a result which is in agreement with some other investigators'.
From the phase diagram, and the thermal data for Wustit, the activities of iron oxide in the melt were deduced over the range where the liquid is in equilibrium with solid Wustit and the results were compared with the values obtained from the slag-metal equilibrium study. It was showed that the estimated values lie close to experimental results.
The “excess stability” curve was constructed from the activity diagram. The curve has the maximum value at 2FeO·SiO2 composition, Which is in agreement with the DARKEN'S finding for the similar system studied by SCHUHAMANN et al.
The theories on the ionic structure of the iron oxide-silica melts were discussed.
Readers Who Read This Article Also Read
MATERIALS TRANSACTIONS Vol.46(2005), No.6
Tetsu-to-Hagané Vol.56(1970), No.7
Relation between the Viscosity and Conductivity of Molten Slags
Makoto KATO, Susumu MINOWA
pp. 260-286
Abstract
Relation between the visccsity and electrical conductivity was discussed with the molten CaO-SiO2-Al2O3 cr [CaO (43)-SiO2 (43)-Al2O3 (14)]-addition system, from the arrangements of the data which were reported in previous works. The viscosity coefficient and conductivity were related with each other, in the equation log η=a+b·log κ. The calculated viscosity coefficient is in good agreement with observed one. The estimation of the density, surface tension, viscosity coefficient or conductivity from the slag composition was tried on the molten CaO-SiO2-Al2O3 system.
Metallographic Analysis of Titanium in Titanium Treated Steel
Shigeo WAKAMATSU
pp. 287-297
Abstract
A simple accurate method for the metallographic analysis of titanium in titanium treated steel is devised. The procedure is as follows:
1. Separation of titanium:
(a) Dissolve 1 g of sample in 30 ml of HCl (1: 2). Filter and wash with hot HCl (1: 9).
(b) Dilute the filtrate to 50 ml in a volumetric flask, and determine titanium as solid solution continue in accordance with section 2 (a) to (c).
(c) Transfer the paper and residue (Paragraph (a)) to the beaker, add 30 ml of HNO3 (1: 1) and boil for 5 min. Filter and wash with hot water.
(d) Add 2 ml of H2SO4 to the filtrate and evaporate to a sirup. Dissolve salt with 40 ml of HC1 (1: 1), cool, dilute to 100 ml or 200 ml in a volumetric flask, and determine titanium as carbide continue in acordance with section 2 (a) to (c).
(e) Transfer the paper and residue (Paragaph (c)) to the beaker, add 20 ml of HNO3 (1: 1) and 5 ml of H202, and boil for 10 min. Filter and wash with hot water.
(f) Add 2 ml of H2SO4 to the filtrate and evaporate to a sirup. Disslove salt with 10 ml of HCl (1: 1), cool, dilute to 50 ml in a volumetric flask, and determine titanium as nitride continue in accordance with section 2 (a) to (c).
(g) Transfer the paper and residue (Paragraph (e)) to the beaker, add 40 ml of HNO3, 3 ml of HClO4, and 2 ml of H2SO4, and evaporate to a sirup. Dissolve salt with 10 ml of HCl (1: 1), cool, dilute to 50 ml in a volumetric frask, and determine titanium as oxide continue in accordance with section 2 (a) to (c).
2. Photometric determination of titanium:
(a) Sample solution-Transfer 10 ml aliquot of solution Section (b), (d), (f) and (g) to 50 ml volumetric flask, add 5 ml of H2O and 8 ml of ascorbic acid solution (10%) to reduce iron, and then add 5 ml of HCl (1: 1) and 20 ml of diantipyrylmethane solution (1.5%), dilute to the mark.
(b) Reference solution-Carry through all the steps of the procedure as directed in paragraph (a). However, no add diantipyrylmethane solution.
(c) After 20 min, measure the absorbance against reference solution at 385 μ
Technical Review on the Continuous Casting of Steel-Present and Future Trend-
Yoshio SHIMOKAWA
pp. 298-325
Delayed Fracture
Shunji YAMAMOTO
pp. 326-337
Readers Who Read This Article Also Read
Tetsu-to-Hagané Vol.50(1964), No.5
Tetsu-to-Hagané Vol.53(1967), No.11
Tetsu-to-Hagané Vol.54(1968), No.10
Article Access Ranking
29 Aug. (Last 30 Days)
-
Perspectives on the Promising Pathways to Zero Carbon Emissions in the Steel Industry toward 2050
ISIJ International Vol.65(2025), No.2
-
Growth, Removal, and Agglomeration of Various Type of Oxide Inclusions in Molten Steel
Tetsu-to-Hagané Vol.111(2025), No.11
-
Copper removal of liquid steel containing 0.25 % carbon using Fe2O3-CaCl2-SiO2 flux
ISIJ International Advance Publication
-
Finite Element Analysis of Bubble Growth and Particle Swelling during Coal Pyrolysis
ISIJ International Vol.65(2025), No.9
-
Corrosion Behavior of Carbon Steel under Soil Drying Conditions
ISIJ International Advance Publication
-
Cold Spot Joining of 980 MPa-class Ultra-high Strength Steel
Tetsu-to-Hagané Advance Publication
-
Factors Affecting Generation of Iron Fines in Cold Sheet Rolling of Steel
ISIJ International Vol.65(2025), No.9
-
Experimental Study on Heat Transfer Characteristics of a Moving Single-Nozzle Jet Impingement
ISIJ International Vol.65(2025), No.9
-
Combination Effect of Premixing Conditions and Iron Ore Size Distribution in Sintered Ore Granulation Process with Intensive Mixer
ISIJ International Advance Publication
-
Evaluation of Feature Selection Methods for Oxygen Supply Prediction in BOF Steelmaking
ISIJ International Advance Publication
You can use this feature after you logged into the site.
Please click the button below.