- TOP
- Tetsu-to-Hagané
- Vol. 51 (1965), No. 7
Tetsu-to-Hagané Vol. 51 (1965), No. 7
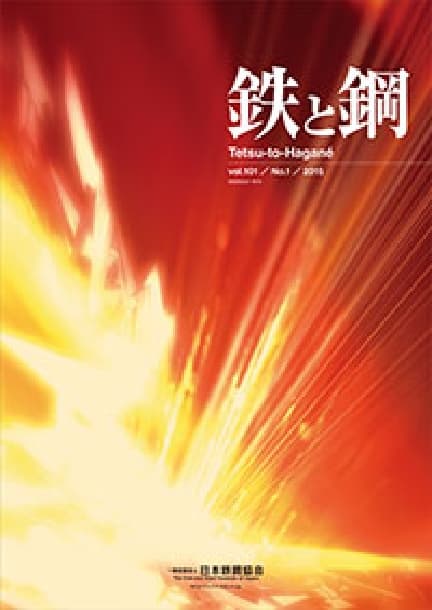
Grid List Abstracts
ONLINE ISSN: | 1883-2954 |
PRINT ISSN: | 0021-1575 |
Publisher: | The Iron and Steel Institute of Japan |
Backnumber
-
Vol. 111 (2025)
-
Vol. 110 (2024)
-
Vol. 109 (2023)
-
Vol. 108 (2022)
-
Vol. 107 (2021)
-
Vol. 106 (2020)
-
Vol. 105 (2019)
-
Vol. 104 (2018)
-
Vol. 103 (2017)
-
Vol. 102 (2016)
-
Vol. 101 (2015)
-
Vol. 100 (2014)
-
Vol. 99 (2013)
-
Vol. 98 (2012)
-
Vol. 97 (2011)
-
Vol. 96 (2010)
-
Vol. 95 (2009)
-
Vol. 94 (2008)
-
Vol. 93 (2007)
-
Vol. 92 (2006)
-
Vol. 91 (2005)
-
Vol. 90 (2004)
-
Vol. 89 (2003)
-
Vol. 88 (2002)
-
Vol. 87 (2001)
-
Vol. 86 (2000)
-
Vol. 85 (1999)
-
Vol. 84 (1998)
-
Vol. 83 (1997)
-
Vol. 82 (1996)
-
Vol. 81 (1995)
-
Vol. 80 (1994)
-
Vol. 79 (1993)
-
Vol. 78 (1992)
-
Vol. 77 (1991)
-
Vol. 76 (1990)
-
Vol. 75 (1989)
-
Vol. 74 (1988)
-
Vol. 73 (1987)
-
Vol. 72 (1986)
-
Vol. 71 (1985)
-
Vol. 70 (1984)
-
Vol. 69 (1983)
-
Vol. 68 (1982)
-
Vol. 67 (1981)
-
Vol. 66 (1980)
-
Vol. 65 (1979)
-
Vol. 64 (1978)
-
Vol. 63 (1977)
-
Vol. 62 (1976)
-
Vol. 61 (1975)
-
Vol. 60 (1974)
-
Vol. 59 (1973)
-
Vol. 58 (1972)
-
Vol. 57 (1971)
-
Vol. 56 (1970)
-
Vol. 55 (1969)
-
Vol. 54 (1968)
-
Vol. 53 (1967)
-
Vol. 52 (1966)
-
Vol. 51 (1965)
-
Vol. 50 (1964)
-
Vol. 49 (1963)
-
Vol. 48 (1962)
-
Vol. 47 (1961)
-
Vol. 46 (1960)
-
Vol. 45 (1959)
-
Vol. 44 (1958)
-
Vol. 43 (1957)
-
Vol. 42 (1956)
-
Vol. 41 (1955)
Keyword Ranking
06 Sep. (Last 30 Days)
Tetsu-to-Hagané Vol. 51 (1965), No. 7
On the Agglomeration, Re-oxidation and Abnormal Phenomena in the Kiln
Hideo ARAKAWA
pp. 1227-1239
Abstract
This is the fourth report in a series of studies which have been concerned with pre-reduction of iron sand with a rotary kiln. In this paper we deal with agglomeration of fine are and with re-oxidation of sponge in the rotary kiln which has influence on the adhesion'troubles.
By means of various measurements on the operating kiln, it has been shown that moderate re-oxidation near the discharge end of kiln may contribute to agglomeration of material, while excessive re-oxidation may cause a heavy adhesion of material called‘dam-ring’(coagulate in the shape of a narrow ring) on the brick wall of kiln. The heavy agglomeration of material growing into a big lump is a troublesome phenomenon for the operation of rotary Inn, and it has been regarded as an abnormal agglomeration such as a snowball, the nucleus of which is a spall of self-coating, and which stays long in the furnace because of the serious dam-ring. The longer the dam-ring and heavy agglomeration are kept in the furnace, the more steady they become, and consequently the more difficult to remove. In the rotary kiln, materials have tendency to segregate in such form as belt type or striped cycles because Gf different repose angles between iron sand and reducing agent, and the segregations disappear in the reduction zone under the normal condition of furnace. But the segregation will-hold on through the reduction zone in some occcasional accidents or especially at the starting time for operation, and may cause a serious coagulation of dam-ring.
When the rotary kiln is employed as a reducing device, the dam-ring trouble becomes a fatal obstruction. Therefore, we need some operational improvements to prevent an adhesion'trouble and keep the operation constant and secure.
On Measurements of Oxidation-Reduction Rate of Iron and of Oxygen Pressure in Oxide Melts
Kazuhiro GOTO, Yukio MATSUSHITA
pp. 1240-1252
Abstract
The change of oxygen pressure in the waste gas of CO-CO2 mixture after the oxidation or reduction of iron or iron oxides has been continuously measured. From this change, the rate of oxidation or reduction has been calculated, knowing the initial gas composition of CO-CO2 mixture flown into the reaction chamber.
It is shown that the oxygen concentration cells or the oxygen gauge can be used for the continuous measurement of the change in the gas compositon. Thus, the rates of the reactions relating to the change of oxygen pressure, in general, can be determined by the oxygen concentration cells with a solid electrolyte, Zr02 CaO. The used cell is:_??_
The equilibrium oxygen pressure in a liquid PbO-Si02 binary solution equilibrated with liquid lead has been measured at 800°C, 900°C, 1000°C, and 1100°C by the following cell:_??_EMF
The equilibrium oxygen pressure in the PbO-SiO2 binary solution increased at higher temperatures, and decreased with anincrease in the silica content of the solution.
The chemical activity of PbO was calculated from the equilibrium oxygen pressure.
The activity of PbO deviated in a negative direction from the Raoultian law, with the deviation increasing with a lowering temperature. The activity of SiO2 was determined by the Gibbs-Duhem equation.
The activity of SiO2 deviates in a negative direction from ideality if the silica content is less than 0.38 mole fraction, above which the activity of silica deviates in a positive direction. The deviation becomes less at higher temperatures.
The free energy of mixing of PbO-Si02 system has minimum values at Nsio2 0.38, asΔFmix=-2.2Kcal/mole, -2.3Kcal/mole, and -2.45Kcal/mole at 900°C, 1000°C, and 1100°C, respectively.
The minimum enthalpy of mixing is about-700 Cal/mole at Nsio2=0.32 and the maximum entropy of mixing is about 1.3 entropy units/mole at Nsio2=0.38.
Oxidation of Molten Iron Alloys with Atmosphere
Koin ITO, Kokichi SANO
pp. 1252-1259
Abstract
When molten iron or steel fully deoxidized with hydrogen or carbon contacts with such oxidizing gas as air, it is observed that an oxide layer or particles appear on the surface of molten metals before the oxygen content in the molten iron reaches the saturated value, [O] sat. We oxidized iron alloys with H20-Ar gas and studied the relations between oxidation conditions and oxygen content, [O] for carbon content, [C] f at the time, tf, when an oxide begins to form on the surface of molten metals, and time dependence of oxygen content.
Results obtained are as follows:
1) For carbon-free iron and its alloys, _??_is derived, where kf [O] sat/K, K is the equilibrium constant of reaction, H20=H2+O, Dm/δG and Do/δL are transport coefficient of H2O in gas and of O in liquid-side diffusion layer, respectively; M is atomic weight of oxygen and p is density of molten metal. Eq. 5 indicates that in accordance with an increase of Pi-120 and with a decrease of oxygen solubility in iron by the addition of alloying elements, [O] f decreases.
2) For carbon-containing iron and its alloys, [C] f is expressed by_??_where M'is atomic weight of carbon and Dc/l2 is transport coefficient of C in liquid-sidediffusion layer. From Eq. 12, it is considered that with an increase of PH2O in atmosphere, [C] f becomes higher and that when [O] sat decreases by the addition of other alloying elements [C] f becomes higher.
3) Accordingly, the time required for appearance of oxide on the surface, tf, is calculated approximately by Eqs. 15 or 16._??_where [O] o and [C] o are the initial contents at time t=0.
4) Present data were explained by the above equations qualitatively, but because of the lack of data on reaction kinetics, quantitative treatment could not be achieved.
Some data by other investigators on the oxidation of molten steels by air in teeming process were also explained by the application of present results.
The Short Cutting of Spheroidizing Duration of the Ball Bearing Steel by Austempering Annealing
Eiji MIYOSHI
pp. 1260-1267
Abstract
As the requirements for the ball bearing steel in Japan are quite severe, its manufacturing is one of the most expensive, though its components are cheap.In this thesis, the shortening of spheroidizing process and its effect in actual service are reported. The shortening of spheroidizing time is realized by austempering annealing. Spheroidizing can be finished in less than 30min by this new process. The properties of the steel made by this new process were investigated by static flattening test and life test. The former test shows the'static strength of material and the latter its dynamic properties. The life test was conducted using the accelerated life test equipment invented by the Government Mechanical Laboratories in Japan. The results show no difference between the steels made by the conventional process and by this new short process except a little increase of hardness. But this higher hardness can be neglected in cutting by lathe. Consequently the new process will be. able to contribute to cost reduction.
Readers Who Read This Article Also Read
Tetsu-to-Hagané Vol.62(1976), No.7
Tetsu-to-Hagané Vol.62(1976), No.9
Tetsu-to-Hagané Vol.75(1989), No.12
Identification of Non-metallic Inclusions in Steels by the Polished Thin Section and X-Ray Microanalys
Minoru SASAKI, Riichiro KUSAKA, Hiroki HAMADA, Shoji MUROTA
pp. 1267-1274
Abstract
For the research of fine minerals in rocks, a “polished thin section” began to beused as a new method. In this paper this technique was applied to metals containing non metallic inclusions. The metal sample was stuck to a slide glass, polished with emery paper to microns in thickness, and scratches on the surface of the inclusions were removed by polishing on cloth with alumina abrasive suspended in oil. Under a petrographic microscope the reflected and transmitted color, transparency, crystal shape, extinction and retardation of the non-metallic inclusions in the thin section were observed. From the optical properties the minerals in the inclusions were identified fairly well. Then, each of minerals was analysed with X-ray microanalyser. When the thin section was 7-8 microns in thickness, it was confirmed that the slide glass had no influence upon the X-ray microanalysis. By this method coarse non-metallic inclusions in the cold-rolled strips of rimmed steel made in openhearth furnace were examined. By considering both the optical properties and the result of X-ray microanalysis of the inclusions, the minerals in the inclusions were identified without difficulty and the state of coexistence of minerals was clarified in detail.
On the High-Temperature Strength and Structural Change of Type 316 Austenite Stainless Steel Castings
Yukishige FUKASE, Shoichi KATOH, Nobuhiro OKUBO, Kanetoshi IWAMOTO
pp. 1274-1282
Abstract
High-temperature tensile test, creep-rupture test up to 10, 000hr at 650°C, aging treatment under various levels of stress at 650°C and stress-free aging treatment up to 6, 400hr at 650°C were carried out on the Type 316 and Type 316L stainless steel castings, and the structural changes daring these tests were observed in order to study the relations between high-temperature properties and structural changes of both alloys.
Carbide and σ-phase were identified by the following means.
(1) The electrolytic etching with concentrated strong hydrooxide solutions (10N. KOH, to color the a-phase; concentrated NH4OH, to color the carbide).
(2) X-ray diffraction analysis of the residues obtained by the electrolytic extraction with 10% HC1 alcohol solution and HOC6H2 (NO2) 3, 5% HC1 alcohol solution.
(3) Examination of Fe, Ni, Cr distributions in carbide and a-phase decomposed from 6-fer rite by X -ray microanalyzer.
The short and long time high-temperature strength of Type 316 is a little superior to that of Type 316L. The superiority of Type 316 is attributed to the solid solution hardening effect of carbon and the more uniform distributions of fine carbide and σ-phase in the austenite matrix than in Type 316L. But the high-temperature long time load-carrying ability of both alloys seems to be fairly good.
There is a little difference between Type 316 and 316L in their structural changes during the tests. They take place generally in the following sequence:
(1) 8-ferrite decomposes into r-phase, carbide and a-phase.
(2) Carbide and σ-phase precipitate at austenite grain boundary.
(3) Carbide and a-phase precipitate in austenite matrix.
(1) Decomposition of 6-ferrite and (2) precipitation at austenite grain boundary are accomplished within 10, 100hr, but (3) precipitation in austenite matrix occurs gradually, taking long time.
Therefore it is probable that the precipitation of fine carbide and a-phase in austenite-matrix influences mainly the long time high -temperature strength of these alloys, and that Type 316L, is a little superior to Type 316L, since the precipitates of fine carbide and c-phase are dispersed uniformly in the austenite matrix of Type 316, while the precipitation in the austenite matrix of Type 316L occurs only round the region which has been formerly occupied by 6-ferrite.
Readers Who Read This Article Also Read
ISIJ International Vol.57(2017), No.11
ISIJ International Vol.60(2020), No.5
Report of Inspection on the Iron and Steel in West Europe and America
Tokushichi MISHIMA
pp. 1283-1297
Conference for Application of the Fundamental Principles of Thermodynamics to Metallurgical Process.
Tasuku FUWA
pp. 1298-1311
Some Consideration on the Mechanism of Deoxidation Reaction of Molten Steel
Kazuteru SENDA
pp. 1317-1318
Abstract
The mechanism of deoxidation reation of molten steel was studied. Both macroscopic oxide inclusions in solid steel, which was enriched with oxygen and silicon added, were situated on boundary of cells. The result shows that all of inclusions found in solid steel are precipitated from melt during solidification of the steel, and that there are no suspended deoxidation products in melt. It was observed that deoxidation products were precipitated on the inner surface of crucible during holding in melt. In some case, the deoxidation products were dendritic. From above experimental results, the following conclusions were introduced.
(1) When adding deoxidant in molten steel was enriched with oxygen, dessolved oxygen and deoxidant would react rapidly to produce an oxide dissolved in monomolecule state, but. not to be grown to oxide particles.
(2) Dissolved monomolecular oxides in steel wonld diffuse to inersurface between melt and crucible, and form oxide phase only on the inner surface of crucible. Consequently oxygen content in steel should be decreased slowly.
Rate of oxygen drop after addition of silicon in iron melt enriched with oxygen was measured. The experimental results were consistent with theoretical result introduced by the above model of deoxidation reaction.
Readers Who Read This Article Also Read
Tetsu-to-Hagané Vol.49(1963), No.2
Tetsu-to-Hagané Vol.54(1968), No.9
Tetsu-to-Hagané Vol.53(1967), No.7
Retrospection of Production and Technique Centering Steel Ingot in Yawata Works
pp. 1319-1327
Abstract
[in Japanese]
Article Access Ranking
06 Sep. (Last 30 Days)
-
Perspectives on the Promising Pathways to Zero Carbon Emissions in the Steel Industry toward 2050
ISIJ International Vol.65(2025), No.2
-
Growth, Removal, and Agglomeration of Various Type of Oxide Inclusions in Molten Steel
Tetsu-to-Hagané Vol.111(2025), No.11
-
Finite Element Analysis of Bubble Growth and Particle Swelling during Coal Pyrolysis
ISIJ International Vol.65(2025), No.9
-
Interface behavior leading to Al/Cu dissimilar metal bonding formation with high-speed eutectic reaction induced by applying current
QUARTERLY JOURNAL OF THE JAPAN WELDING SOCIETY Vol.43(2025), No.2
-
Corrosion Behavior of Carbon Steel under Soil Drying Conditions
ISIJ International Advance Publication
-
Cold Spot Joining of 980 MPa-class Ultra-high Strength Steel
Tetsu-to-Hagané Advance Publication
-
Combination Effect of Premixing Conditions and Iron Ore Size Distribution in Sintered Ore Granulation Process with Intensive Mixer
ISIJ International Advance Publication
-
A preliminary study on reduction degradation of iron ore sinter using sinter analogue and X-ray micro-computed tomography (MCT)
ISIJ International Advance Publication
-
Copper removal of liquid steel containing 0.25 % carbon using Fe2O3-CaCl2-SiO2 flux
ISIJ International Advance Publication
-
Evaluation of Feature Selection Methods for Oxygen Supply Prediction in BOF Steelmaking
ISIJ International Advance Publication
You can use this feature after you logged into the site.
Please click the button below.