- TOP
- Tetsu-to-Hagané
- Vol. 74 (1988), No. 3
Tetsu-to-Hagané Vol. 74 (1988), No. 3
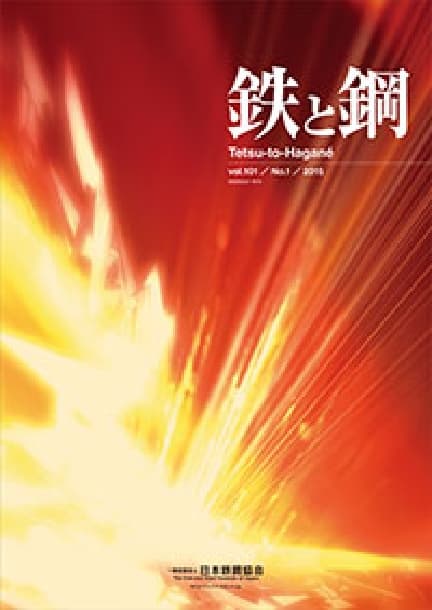
Grid List Abstracts
ONLINE ISSN: | 1883-2954 |
PRINT ISSN: | 0021-1575 |
Publisher: | The Iron and Steel Institute of Japan |
Backnumber
-
Vol. 111 (2025)
-
Vol. 110 (2024)
-
Vol. 109 (2023)
-
Vol. 108 (2022)
-
Vol. 107 (2021)
-
Vol. 106 (2020)
-
Vol. 105 (2019)
-
Vol. 104 (2018)
-
Vol. 103 (2017)
-
Vol. 102 (2016)
-
Vol. 101 (2015)
-
Vol. 100 (2014)
-
Vol. 99 (2013)
-
Vol. 98 (2012)
-
Vol. 97 (2011)
-
Vol. 96 (2010)
-
Vol. 95 (2009)
-
Vol. 94 (2008)
-
Vol. 93 (2007)
-
Vol. 92 (2006)
-
Vol. 91 (2005)
-
Vol. 90 (2004)
-
Vol. 89 (2003)
-
Vol. 88 (2002)
-
Vol. 87 (2001)
-
Vol. 86 (2000)
-
Vol. 85 (1999)
-
Vol. 84 (1998)
-
Vol. 83 (1997)
-
Vol. 82 (1996)
-
Vol. 81 (1995)
-
Vol. 80 (1994)
-
Vol. 79 (1993)
-
Vol. 78 (1992)
-
Vol. 77 (1991)
-
Vol. 76 (1990)
-
Vol. 75 (1989)
-
Vol. 74 (1988)
-
Vol. 73 (1987)
-
Vol. 72 (1986)
-
Vol. 71 (1985)
-
Vol. 70 (1984)
-
Vol. 69 (1983)
-
Vol. 68 (1982)
-
Vol. 67 (1981)
-
Vol. 66 (1980)
-
Vol. 65 (1979)
-
Vol. 64 (1978)
-
Vol. 63 (1977)
-
Vol. 62 (1976)
-
Vol. 61 (1975)
-
Vol. 60 (1974)
-
Vol. 59 (1973)
-
Vol. 58 (1972)
-
Vol. 57 (1971)
-
Vol. 56 (1970)
-
Vol. 55 (1969)
-
Vol. 54 (1968)
-
Vol. 53 (1967)
-
Vol. 52 (1966)
-
Vol. 51 (1965)
-
Vol. 50 (1964)
-
Vol. 49 (1963)
-
Vol. 48 (1962)
-
Vol. 47 (1961)
-
Vol. 46 (1960)
-
Vol. 45 (1959)
-
Vol. 44 (1958)
-
Vol. 43 (1957)
-
Vol. 42 (1956)
-
Vol. 41 (1955)
Keyword Ranking
04 Sep. (Last 30 Days)
Tetsu-to-Hagané Vol. 74 (1988), No. 3
Recent Progress of Analytical Technique about Injection Molding Processes
Takashi ICHIYANAGI, Hiroyuki NAKA
pp. 427-434
Report on Activity of Subcommittee for Sensor Technology
Kazuhiro Sylvester GOTO
pp. 435-440
Kinetics of Nitrogen Disorption from Low Nitrogen Liquid Iron by Blowing Ar and Reducing Gas Mixture or by Top Injection of Iron Ore Powder under Reduced Pressure
Kazuumi HARASHINIA, Shozo MIZOGUCHI, Hiroyuki KAJIOKA
pp. 441-448
Abstract
The effects of blowing Ar and reducing gas mixture or top injection of iron ore powder on the rate of nitrogen removal from liquid iron under reduced pressure have been studied using a vacuum induction furnace containing 12 kg metal at 1 600°C.
1) In the case of blowing Ar and reducing gas mixture, the value of chemical reaction rate constant, kr, was slightly greater than that in the case of only Ar blowing. Even in the former case, kr depended strongly on sulfur content in metal in the range of low oxygen content.
2) In the case of blowing Ar and hydrocarbon gas mixture, especialy, oxygen content in metal decreased and the rate of nitrogen removal increased remarkably.
3) In the case of top injection of iron ore powder, the rate of nitrogen removal was lower than that without the powder, when the decarburization rate, Vc, was lower than the critical decarburization rate, VCa. However, the rate of nitrogen removal increased with the increase of when VC was greater than VCa. VCa increased with the decrease of sulfur content.
4) The reason of why the rate of nitrogen removal increased by top injection iron ore powder was attributable to the increase of gas/metal interfacial area by CO gas evolution.
Kinetics of Decaburization of Low Carbon Liquid Iron under Reduced Pressures
Kazuumi HARASHIMA, Shozo MIZOGUCHI, Hiroyuki KAJIOKA
pp. 449-456
Abstract
The kinetics of decarburization of liquid iron by blowing Ar-CO-CO2 gas mixtures under reduced pressure have been studied using a vacuum induction furnace containing 12 kg metal at 1 600°C.
The results obtained are as follows:
1) In low carbon concentration range, the behavior of decarburization reaction was divided into three types.
(a) In the range of carbon content higher than about 200 ppm, the rate of decarburization was described as the zeroth order reaction with respect to [C]. "Region-0".
It was concluded that the rate-determining step was decomposition of CO2 chemisorped at liquid iron surface. Then, the apparent rate constant of the reaction was equal to 2.5×10-3 [mol/cm2·s]=0.43[cm·%/s·atm].
(b) In the range of carbon content between 10 ppm and 200 ppm, the rate of decarburization was described as the first order reaction with respect to [C]. "Region-I".
As the rate constant decreased with increase in [S] content, it was concluded that the rate of decarburization was controlled by mass transfer of carbon in diffusion boundary layer in the metal and the chemical reaction of CO gas formation at the metal surface.
(c) In the case of carbon content less than 10 ppm, the rate of decarburization was less than that in "Region-I". "Region- II ".
2) In each region, the adsorption coefficients of sulfur at 1 600°C were given as follows,
"Range-0": κs=65, "Range-I": κs= 5063
Characteristics of Rapidly Solidified Tool Steel
Chisato YOSHIDA, Hiroyuki YASUNAKA, Teruhiko NOZAKI
pp. 457-464
Abstract
The rapid solidification of high speed steel was investigated by using water-cooled chill block apparatus, which was simulated to function similarly to a caterpillar-type caster or roll caster. The secondary dendrite arm spacing near the surface was 4 μm in every cast ingot. By increasing the thickness of the ingot, the dendrite arm spacing at the center also increased. By analyzing the relationship between the dendrite arm spacing and cooling rate, the cooling rate near the surface was estimated at 103°C/s and that at the center of 40 mm-thick cast ingot was 100°C/s. The size of eutectic carbide decreased with the thickness of the cast ingot. The cast ingots were heat treated at 1 150°C for 2 h. Lamellar eutectic carbide changed to the spheroidal one by heat treatment.
Furthermore, plates of carbon tool steel were made by the twin roll test caster. Casting speed was 510 m/min. The size of cast plate was 12.5 mm in thickness and 260 mm in width. The carbon tool steel plate was heat-treated at 690°C for 150 h. The spheroidal cementite structure was obtained by the heat treatment. The plates of high speed steel were also made by the twin roll test caster. Fine eutectic carbide was observed in the cast plate by the heat treatment.
Analysis of the Rate of Crystallization and Precipitation of MnS in the Resulphurized Free-cutting Steel
Yoshiyuki UESHIMA, Kohichi ISOBE, Shozo MIZOGUCHI, Hirobumi MAEDE, Hiroyuki KAJIOKA
pp. 465-472
Abstract
It is necessary to investigate the behavior of MnS formation on the solidification of steel quantitatively, in order to improve machinability of resulphurized free-cutting steel. From this viewpoint, a mathematical model analyzing MnS formation on the solidification of steel was developed on the basis of the method for analyzing interdendritic microsegregation. Furthermore, analysis by this mathematical model and directional solidification tests were carried out to investigate this behavior and the effect of cooling rate on it.
The results are as follows:
1) The MnS particles in the low carbon resulphurized free-cutting steel are formed by crystallization and precipitation on cooling.
2) The rate of crystallization of MnS is regulated by the diffusion rate of solute Mn from center of dendrite to interdendrite region.
3) The rate of precipitation of MnS is regulated by the diffusion rate of solute Mn in the region of the order of several μm from the surface of precipitating MnS.
4) The amount of MnS is effectively increased by increase of Mn content and decrease of cooling rate on solidification.
Readers Who Read This Article Also Read
Tetsu-to-Hagané Vol.75(1989), No.10
Tetsu-to-Hagané Vol.73(1987), No.1
Tetsu-to-Hagané Vol.75(1989), No.11
The Fully Continuous Descaling and Cold Rollig Mill
Hiroyasu YUASA, Toshinobu NAKANISHI, Tadayoshi TAKENO, Mamoru TABUTI, Kazuaki YAMAMOTO, Tomio KOMATU
pp. 473-480
Abstract
Mizushima works has remodeled the existing pickling line (No. 2CPL) and the batch type cold tandem mill (No. 1TM) into a fully continuous line in June 1985. Some necessary technologies for combining a pickling line with a cold tandem mill have been developed for a continuous operation; highly efficient descaling technique through introducing tension leveller and mechanical descaler, continuously width changeable trimmer, and advanced flying-gauge changing technology. Improvement in product quality and material yield, increase in productivity, shortened of production time, and labor saving have been obtained. We can produce cold rolled strip using only two processes, which are KM-CAL installed in February 1984 and the fully continuous descaling and cold rolling mill.
Now the operation of the new system is smooth and the benefits are as expected.
Development of High-accuracy Thickness and Crown Control in Hot Strip Mill
Yuichi TSUJI, Satoshi SHIMAZU, Yuichi HIRAISHI, Kenya FUKUSHIMA, Katsuhiro KATO, Kazuo HIRASE
pp. 481-488
Abstract
The construction of the new hot strip mill of 1 840 mm in width was started to replace the old one in June, 1982 and was completed on its commercial operation on August 1, 1984, in Nippon Steel's Hirohata Works. The computer control systems of the mill have enabled us to achieve high-accuracy quality controls.
First, we have developed absolute mode AGC system which gives the high accuracy of strip thickness for full strip length. The system is composed of four main functions as described below.
(1) Quick-response AGC with hydraulic screw down system
(2) Compensating control for mass flow balance
(3) Decoupling control of bender and screw down systems for gauge, crown and shape of strip
(4) Set up function for control parameters
Secondly, we have developed crown and shape control system which has high capability by adopting "pair cross roll system" for the first time in the world and work roll bender system of servo-valve drive type. The main functions are described below.
(1) Pre-set function of roll cross angles corresponding to crown schedule for each strip
(2) Feedback crown and shape control of work roll bender system within each strip
Fabrication of Unidirectional Long Carbon Fiber Reinforced Carbon (C/C) Composites Using Hot Press Process and Their Strengths
Tong Shik CHANG, Akimitsu OKURA
pp. 489-496
Abstract
Carbon fiber-carbon matrix (C/C) composites were fabricated using a simple hot press process. The matrix was prepared from a fine pulverized coke mixed with a carbonaceous bulk mesophase (BM). The fibers were epoxy-resin-impregnated unidirectional long carbon fibers (UD fibers). The maximum temperature and pressure in the hot press process were 600°C and 49MPa, respectively.
The resalts were as follows :
(1) When one type of fiber (UD-1) was used, the maximum strength was 119 MPa at a BM content of 70% in the matrix and the volume fraction of the fiber, Vf=30%. When reinforced by another type of fiber (UD-2), the maximum strength reached 130 MPa at a BM content of 80% and a Vf=46.4%. Both the strengths exceeded that of a commercial C/C composite.
(2) The composites reinforced by UD-2 showed a maximum strength which decreased to 80 MPa after a secondary heat treatment at 700°C to 1 500°C.
Fabrication of Cloth Weaved Carbon Fiber Reinforced Carbon (C/C) Composites Using Hot Press Process and Strength Effects of Impregnated Resins
Tong Shik CHANG, Chengshan JIN, Akimitsu OKURA
pp. 497-504
Abstract
Carbon fiber-carbon matrix (C/C) composites were fabricated using a simple hot process. The reinforcements were carbon cloth prepreg sheets impregnated with three kinds of resin, that is, coal tar pitch, epoxy and phenol. The matrix was a fine pulverized coke mixed with a carbonaceous bulk mesophase (BM) for a binder. The maximum temperature and pressure during the hot-press were 600°C and 49 MPa, respectively.
The results were as follows:
(1) The strengths of the composites were significantly affected by three factors: the kinds of impregnated resin, the fiber volume fraction (Vf), and the BM content in the matrix. The maximum strength of 83 MPa was attained in the composite reinforced with the coal tar pitch prepreg sheets at a BM content of 50% and a Vf=40%. With the other types of prepreg sheets, the maximum strengths were much less than 83 MPa regardless of Vf.
(2) The maximum strengths of the composites reinforced with the coal tar pitch and epoxy resin prepreg sheets were decreased by a secondary heat treatment at 800°C to 1 500°C.
Ferrite Grain Refinement through Accelerated Cooling after Controlled Rolling in Low Carbon Steels
Takashi ABE, Koshiro TSUKADA, Isao KOZASU
pp. 505-512
Abstract
To make clear the ferrite grain refinement behavior of low carbon steels through accelerated cooling after controlled rolling, study was focussed on the transformation behavior and the ferrite nucleation behavior in continuous and isothermal transformation. Combination of strain imposed in unrecrystallization region and increase in supercooling by accelerated cooling caused remarkable increase of intragranular nucleation which resulted in ferrite grain refinement. Even small strain which could not produce deformation band and deformed annealing twin caused intragranular ferrite nucleation. The number of intragranular nuclei decreased as recovery and recrystallization progressed before transformation. It was suggested that intragranular nucleation sites were dislocation, cell structure, sub-grain boundary and inclusions which could not act as nucleation site under condition of controlled rolling. It was concluded that accelerated cooling brought about ferrite grain refinement by promotion of intragranular nucleation on the proper sites and suppression of grain growth.
Readers Who Read This Article Also Read
ISIJ International Vol.30(1990), No.7
Tetsu-to-Hagané Vol.74(1988), No.10
Tetsu-to-Hagané Vol.82(1996), No.11
Effects of Mo and W Contents on Creep Rupture Strength and Toughness of a 10% Cr Heat Resistant Steel
Xing-yang LIU, Toshio FUJITA
pp. 513-520
Abstract
With the Mo equivalents (wt%Mo+1/2 wt%W) being within the range of 1.2-1.6%, the effects of Mo and W contents on creep rupture strength and toughness have been investigated for a 10 Cr heat resistant steel.
(1) With the Mo equivalent being a constant of 1.2, variation in W and Mo contents shows little effect on the toughness and on the creep rupture properties at under 600°C as well as on the short-term side of higher temperatures, but the steel containing more W shows higher creep rupture strength on the long-term side of 700°C.
(2) The steels containing more Mo or W show lower toughness when heated at 600°C, but increased creep rupture strength at 600°C as well as on the short-term side of higher temperatures. The change is related to the fact that the increase in Mo or W content enhances both solution hardening and precipitation hardening under the conditions mentioned above. However, the increase in Mo or W content has no any beneficial effect on the long-term creep rupture strength at above 650°C. The increased coarsening tendecy of precipitates resulting from the increase in Mo or W content was considered the factor detrimental to the creep rupture strength on the long-term side at above 650°C.
(3) The steels developed in this study show a extrapolated 105 h creep rupture strength of as high as 15-20 kgf/mm2 at 600°C and 7-9 kgf/mm2at 650°C. It is evaluated that these steels would be applicable at up to 621°Cas the rotor material.
Hot Ductility and Fracture of an Eutectoid Carbon Steel in the Austenite Range
Masayuki Ohashi, Takao ENDO, Taku SAKAI
pp. 521-526
Abstract
The hot ductility and fracture behaviour of an eutectoid carbon steel in the austenite range were studied by tensile tests in a wide range of strain rates from 10-5 s-1 to 1 s-1. Flow curves and ductility (elongation to failure εf) were expressed uniquely by a parameter Z=ε·exp (Q/RT) or stress peak σp, Where R and T have usual meanings and Q is 270 kJ/mol. The εf versus σp (or Z) curve showed a remarkable transition from low to high ductility in a range of σp between 55 MPa and 80 MPa. This result is associated critically with the relative difference between the nucleation strain of intergranular crack εc, and that of dynamic recrystallization εr. In the range of low ductility, where εc<<εr, intergranular cracks can be nucleated at the initial grain boundaries and propagated easily along them. In the transition range from low to high ductility, where εc_??_εr, the initiations of cracks and dynamic recrystallization take place simultaneously and then cracks become isolated apart from the new grain boundaries and can not grow, leading to increasing ductility. In the range of high ductility, where εc>>εr, dynamic recovery and subsequent dynamic recrystallization can make initial grain boundaries serrated and cause the sliding of them to prevent, leading to no crack initiation in low strains.
Evaluation of SCC Resistance of Alloy 600 in High Temperature Pressurized Water Environments by the High Stress Ratio Cyclic Crack Growth Tests
Hiroo NAGANO, Katsuyuki TOKIMASA, Kenichi TANAKA, Hiroyuki TSUGE
pp. 527-534
Abstract
SCC resistance of nickel-base alloy, Alloy 600, in high temperature pressurized water environments was evaluated by the cyclic crack growth tests of high stress ratio.
Three kinds of materials with different heat treatments namely annealed, sensitized and thermally treated alloys were tested and it was found that the effect of enviroment on the fatigue crack propagation rate became remarkable under a high stress ratio (R) and that sensitized and annealed materials showed higher crack growth rates compared to the thermally treated one.
The fracture mode of the materials tested was intergranular when the effect of environment on the fatigue crack growth rate was observed. From these results the effect of environments can be considered to be caused by SCC. Cyclic KISCC values evaluated made clear that the thermally treated material gave a higher KISCC. value compared to the annealed and sensitized materials.
With the high stress ratio cyclic crack growth test in the environment, the SCC resistance of nickel base alloy can be estimated quantitatively within a short period which is less than a fifteenth of the time that is required for the normal double U-bend test.
Readers Who Read This Article Also Read
Tetsu-to-Hagané Vol.73(1987), No.2
Tetsu-to-Hagané Vol.76(1990), No.7
Tetsu-to-Hagané Vol.76(1990), No.5
Influence of Boron and Nitrogen Contents on Strength and Toughness of Controlled-rolled Low Carbon-Boron Steel
Yasufumi FUJISHIRO, Tamotsu HASHIMOTO, Hiroo OHTANI
pp. 535-542
Abstract
An influence of boron and nitrogen contents on the strength and toughness of 0.02%C-1.65%Mn0.04%Nb-0.015%Ti-B steel and 0.03%C-1.50%Mn-0.15%Mo-0.07%V-0.04%Nb-0.02%Ti-B steel finish-rolled at 720°C after heating at 1050°C was studied. It was found that the strength and toughness could be estimated by calculated free-boron (B*).
The microstructure changes from coarse ferrite and degenerated pearlite structure to fine-grained ferrite and isolated martensite structure as boron becomes effective for strengthening, consequently the tensite strength rises 5 to 6 kgf/mm2 and the yield strength to tensile strength ratio decreases. Furthermore, the microstructure changes to bainite structure by the addition of molybdenum and vanadium and the increase of boron in solution, rising the strength. The strength rises mainly because ferrite becomes fine. The critical boron content in solution which effectively increases tensile strength is 8 ppm as B* in 0.02%C-1.65%Mn-0.04%Nb-0.015%Ti-B steel. The critical boron in solution decreases to about 1 ppm by the addition of molybdenum and vanadium. In the region where boron contributes to strengthening, the tensile strength rises linearly with increasing B*. The degree of the strengthening rises by the addition of molybdenum and vanadium.
Readers Who Read This Article Also Read
Tetsu-to-Hagané Vol.73(1987), No.2
Tetsu-to-Hagané Vol.76(1990), No.7
Tetsu-to-Hagané Vol.76(1990), No.5
Effect of Substructure Formed in Prior β Grain on Crack Initiation and Propagation Toughness of Ti-6 Al-2 Sn-4 Zr-6 Mo Alloy
Mitsuo NIINOMI, Ikuhiro INAGAKI, Toshiro KOBAYASHI
pp. 543-550
Abstract
The instrumented Charpy impact test, static and dynamic fracture toughness tests were carried out on Ti-6A1-2Sn-4Zr-6Mo alloy in which the prior, β grain size was variously changed by heat treatments. Then, the effect of microstructure on the toughness was examined.
The elongation, crack initiation and propagation toughness increased with the slight decrease in strength in the specimens with the increased prior β grain size with prolonged solution treatment time in the β region. In particular, the crack propagation toughness increased remarkably. The colony size, width of grain boundary α, width and spacing of widmanstätten α also increased, but the subcolony spacing decreased with the increase in the prior β grain size.
The increase in the crack initiation toughness was mainly caused by the increase in the widmanstätten a lath or lath spaing. The increase in the crack propagation toughness was caused by the deflection of the crack pass, which was brought by the decrease in the intersubcolony spacing. The intersubcolony spacing decreased with the increase in the number of a nucleation during diffusion-controlled α→β transformation; such nucleation sites increased with the increase in the prior, β grain size. In such situation, α nucleated in the interior of the β grain and it increased its number by the introduction of the working strain.
Fatigue Properties of Vibration Damping Steel Sheets
Hiroyuki KAGAWA, Masayoshi KURIHARA, Yuukichi WATANABE
pp. 551-558
Abstract
Fatigue properties of vibration damping sheets of steel-resin lamination type were studied in connection with the effects of shear adhesion strength, tensile strength of steel sheets and thickness of vibration damping sheets. Fatigue tests were carried out under the conditions of shear by tension loading and out-of-plane bending.
Principal results obtained in this study are as follows:
(1) Fatigue strength in shear by tension loading increased in proportion to the increase in shear adhesion strength.
(2) Fatigue strength in out-of-plane bending showed a tendency to increase with increases in shear adhesion strength, tensile strength of steel sheets, and to increase with a decease in thickness of vibration damping sheets.
(3) Separation life under out-of-plane bending condition was estimated using fatigue test data under shear by tension loading. The estimated separation life showed a good agreement with the experimental result.
(4) An analytical method to estimate fatigue failure modes under out-of-plane bending condition, i, e. (1) fractured, (2) separated, and (3) not fractured nor separated, was proposed.
Stress Corrosion Cracking of SUS 304 Stud-Bolt
Shigeru MIZOGUCHI, Kazuo YAMAMOTO, Masahisa YAMADA
pp. 559-566
Abstract
The heat insulating material, fixed by several hundreds of SUS304 stud-bolts to the roof of a heating furnace, fell down. Extensive inspections of the damaged parts revealed that the accident resulted from the chloride stress corrosion cracking (SCC) of the stud-bolts.
It was infered that this SCC was caused by cooling brine which had accidentally leaked out from the skid-pipe and had soaked into the interface between the stud-bolts and the heat insulating material.
The countermeasures to avoid the recurrence of the accident due to SCC were proposed as follows;
1) the use of SUS3IOS stud-bolts
2) the prevention of the brine-leak from the skid-pipe
3) the use of chloride-free heat insulating material.
Readers Who Read This Article Also Read
Tetsu-to-Hagané Vol.73(1987), No.2
Tetsu-to-Hagané Vol.76(1990), No.7
Tetsu-to-Hagané Vol.76(1990), No.5
Transient Load Measurement with Devices Made by High Damping Steel
Namio URABE, Kyusuke MARUYAMA
pp. 567-569
Article Access Ranking
04 Sep. (Last 30 Days)
-
Perspectives on the Promising Pathways to Zero Carbon Emissions in the Steel Industry toward 2050
ISIJ International Vol.65(2025), No.2
-
Growth, Removal, and Agglomeration of Various Type of Oxide Inclusions in Molten Steel
Tetsu-to-Hagané Vol.111(2025), No.11
-
Finite Element Analysis of Bubble Growth and Particle Swelling during Coal Pyrolysis
ISIJ International Vol.65(2025), No.9
-
Interface behavior leading to Al/Cu dissimilar metal bonding formation with high-speed eutectic reaction induced by applying current
QUARTERLY JOURNAL OF THE JAPAN WELDING SOCIETY Vol.43(2025), No.2
-
Corrosion Behavior of Carbon Steel under Soil Drying Conditions
ISIJ International Advance Publication
-
Cold Spot Joining of 980 MPa-class Ultra-high Strength Steel
Tetsu-to-Hagané Advance Publication
-
Combination Effect of Premixing Conditions and Iron Ore Size Distribution in Sintered Ore Granulation Process with Intensive Mixer
ISIJ International Advance Publication
-
A preliminary study on reduction degradation of iron ore sinter using sinter analogue and X-ray micro-computed tomography (MCT)
ISIJ International Advance Publication
-
Copper removal of liquid steel containing 0.25 % carbon using Fe2O3-CaCl2-SiO2 flux
ISIJ International Advance Publication
-
Evaluation of Feature Selection Methods for Oxygen Supply Prediction in BOF Steelmaking
ISIJ International Advance Publication
You can use this feature after you logged into the site.
Please click the button below.