- TOP
- Tetsu-to-Hagané
- Vol. 53 (1967), No. 8
Tetsu-to-Hagané Vol. 53 (1967), No. 8
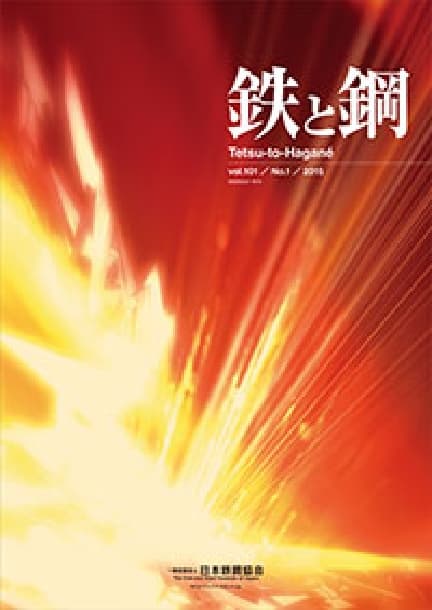
Grid List Abstracts
ONLINE ISSN: | 1883-2954 |
PRINT ISSN: | 0021-1575 |
Publisher: | The Iron and Steel Institute of Japan |
Backnumber
-
Vol. 111 (2025)
-
Vol. 110 (2024)
-
Vol. 109 (2023)
-
Vol. 108 (2022)
-
Vol. 107 (2021)
-
Vol. 106 (2020)
-
Vol. 105 (2019)
-
Vol. 104 (2018)
-
Vol. 103 (2017)
-
Vol. 102 (2016)
-
Vol. 101 (2015)
-
Vol. 100 (2014)
-
Vol. 99 (2013)
-
Vol. 98 (2012)
-
Vol. 97 (2011)
-
Vol. 96 (2010)
-
Vol. 95 (2009)
-
Vol. 94 (2008)
-
Vol. 93 (2007)
-
Vol. 92 (2006)
-
Vol. 91 (2005)
-
Vol. 90 (2004)
-
Vol. 89 (2003)
-
Vol. 88 (2002)
-
Vol. 87 (2001)
-
Vol. 86 (2000)
-
Vol. 85 (1999)
-
Vol. 84 (1998)
-
Vol. 83 (1997)
-
Vol. 82 (1996)
-
Vol. 81 (1995)
-
Vol. 80 (1994)
-
Vol. 79 (1993)
-
Vol. 78 (1992)
-
Vol. 77 (1991)
-
Vol. 76 (1990)
-
Vol. 75 (1989)
-
Vol. 74 (1988)
-
Vol. 73 (1987)
-
Vol. 72 (1986)
-
Vol. 71 (1985)
-
Vol. 70 (1984)
-
Vol. 69 (1983)
-
Vol. 68 (1982)
-
Vol. 67 (1981)
-
Vol. 66 (1980)
-
Vol. 65 (1979)
-
Vol. 64 (1978)
-
Vol. 63 (1977)
-
Vol. 62 (1976)
-
Vol. 61 (1975)
-
Vol. 60 (1974)
-
Vol. 59 (1973)
-
Vol. 58 (1972)
-
Vol. 57 (1971)
-
Vol. 56 (1970)
-
Vol. 55 (1969)
-
Vol. 54 (1968)
-
Vol. 53 (1967)
-
Vol. 52 (1966)
-
Vol. 51 (1965)
-
Vol. 50 (1964)
-
Vol. 49 (1963)
-
Vol. 48 (1962)
-
Vol. 47 (1961)
-
Vol. 46 (1960)
-
Vol. 45 (1959)
-
Vol. 44 (1958)
-
Vol. 43 (1957)
-
Vol. 42 (1956)
-
Vol. 41 (1955)
Keyword Ranking
30 Aug. (Last 30 Days)
Tetsu-to-Hagané Vol. 53 (1967), No. 8
Consideration on Decarburization Reaction in an Oxygen Converter and Possibility of the Computing Control on its Basis
Takehiko FUJII, Taiji ARAKI, Katsukiyo MARUKAWA
pp. 973-982
Abstract
Considerations and analyses were done on the mechanism of decarburization reaction in the oxygen steelmaking process by the data obtained from the laboratory work, the open hearth furnace, and the oxygen converter.
Authors found that the blowing time of an oxygen converter could be specified into the three periods according to the characteristics of decarburization reaction which takes place in the vessel. Authors connected it with a control system for the converter practice, and named it “Decarburization Model System.”
As the result of many trials, authors pointed out a possibility of computing control of bath carbon and temperature in this direction.
Dissolution of Steel Cylinder into Liquid Fe-C Alloy
Mineo KOSAKA, Susumu MINOWA
pp. 983-997
Abstract
Dissolution of solid steel cylinder into molten Fe-C alloy was investigated at the temperature from 1300°C to 1500°C.
In this paper, the viscosity and the density of the melt and the diffusion coefficient of carbon were estimated from the literatures at the solid-liquid interface i. e. at the liquidus concentration of carbon, CL.
Nondimensional correlation for the mass-transfer was analysed using above estimated physical properties and diffusion coeff.
Correlation for the rotated or static cylinder was obtained as follows:
JD= (k/U)(Sc) 2/3=0⋅064 (Re) -0.25
102<Re<104: rotated cylinder
Sh=0⋅11 (Gr.m×Sc) 1/3
109<Gr·m × Sc<1011: static cylinder
Utilizing the nondimensional correlation of a model test by benzoic acid-water system, the unknown ratesof stirring of molten Fe-C alloy melted by some laboratorial H. F. furnace could be roughly estimated from the rates of dissolution of steel cylinder.
On the Variations of the Components in the Inclusion
Yasushi KOJIMA, Kokichi SANO
pp. 997-1006
Abstract
After the equilibrium between molten iron and the systems FeO-MnO-SiO2 and FeO-MnO-CrO-SiO2 was established in the silica crucible at 1650°C, the temperature was lowered rapidly to 1550°C and this temperature maintained till the equilibrium was attained again. The variations of the concentration of the components in the liquid iron and slag were measured. The results obtained are summarized as follows:
1) MnO and FeO were reduced in the system FeO-MnO-SiO2 slag by the excess silicon due to the lowering temperature at more than 0⋅18%, manganese in the liquid iron. The relation between reduction ratio of MnO and the concentration of silica was estimated. Up to 0⋅18% manganese, this excess silicon, however, was not sufficient to deoxidize, MnO was not reduced in this case.
2) FeO, MnO and CrO were reduced in the system FeO-MnO-CrO-SiO2 slag by the excess silicon same as the system FeO-MnO-SiO2 in the case of 5%Cr. But in cases of 9% and 14% Cr, the reduction of these oxides did not occur. It was considered that the new phase was formed at the boundary of both phases.
3) It was anticipated from the experimental results obtained above that the equilibrium between inclusion and molten iron was established fast. The mechanism of the formation of oxide inclusions composed of FeO-MnO-SiO2 system were examined experimentally by addition of deoxidizers. The results showed that if the processes of formation of oxide inclusions composed of FeO-MnO-SiO2 system were examined experimentally by addition of deoxidizers. The results showed that if the processes of formation of inclusions could be known, based on the equilibrium data, the components of inclusion could be evaluated from the concentration of dissolved elements in the liquid iron.
Effect of Impurities on the Secondary Recrystallization in Silicon Iron
Takashi MATSUOKA
pp. 1007-1023
Abstract
An investigation has been made on the effects of impurities on the development of (110)[001] secondary recrystallization texture in silicon iron. While dispersed inclusions, TiC, VN, NbC, and A1N, were observed to have the ability to promote secondary recrystallization, BN and ZrC, have not. Necessary amounts of impurity elements were found to be 0.04% Ti, 0.07% V, and 0.02% Nb, respectively. The solubility products [%M][%C] or [%M][%N](M: impurity element) of effective inclusions were estimated to be from 10-3 to 10-5 at the secondary recrystallization temperature. Inclusions of the order of 0.1 micron in size were observed to be dispersed more densely than 1012 particles/cm3 in final gauge strips in which secondary recrystallization occurred appreciably.
Crystal Structures of Nonmetallic Inclusion in Iron and Steel, and its Homologue
Kiichi NARITA
pp. 1024-1055
Readers Who Read This Article Also Read
Tetsu-to-Hagané Vol.53(1967), No.11
Tetsu-to-Hagané Vol.52(1966), No.9
Tetsu-to-Hagané Vol.51(1965), No.2
Article Access Ranking
30 Aug. (Last 30 Days)
-
Perspectives on the Promising Pathways to Zero Carbon Emissions in the Steel Industry toward 2050
ISIJ International Vol.65(2025), No.2
-
Growth, Removal, and Agglomeration of Various Type of Oxide Inclusions in Molten Steel
Tetsu-to-Hagané Vol.111(2025), No.11
-
Copper removal of liquid steel containing 0.25 % carbon using Fe2O3-CaCl2-SiO2 flux
ISIJ International Advance Publication
-
Finite Element Analysis of Bubble Growth and Particle Swelling during Coal Pyrolysis
ISIJ International Vol.65(2025), No.9
-
Corrosion Behavior of Carbon Steel under Soil Drying Conditions
ISIJ International Advance Publication
-
Cold Spot Joining of 980 MPa-class Ultra-high Strength Steel
Tetsu-to-Hagané Advance Publication
-
Factors Affecting Generation of Iron Fines in Cold Sheet Rolling of Steel
ISIJ International Vol.65(2025), No.9
-
Experimental Study on Heat Transfer Characteristics of a Moving Single-Nozzle Jet Impingement
ISIJ International Vol.65(2025), No.9
-
Combination Effect of Premixing Conditions and Iron Ore Size Distribution in Sintered Ore Granulation Process with Intensive Mixer
ISIJ International Advance Publication
-
Evaluation of Feature Selection Methods for Oxygen Supply Prediction in BOF Steelmaking
ISIJ International Advance Publication
You can use this feature after you logged into the site.
Please click the button below.