- TOP
- Tetsu-to-Hagané
- Vol. 57 (1971), No. 8
Tetsu-to-Hagané Vol. 57 (1971), No. 8
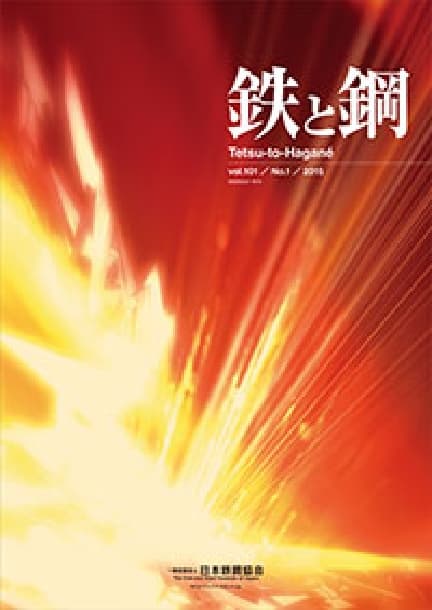
Grid List Abstracts
ONLINE ISSN: | 1883-2954 |
PRINT ISSN: | 0021-1575 |
Publisher: | The Iron and Steel Institute of Japan |
Backnumber
-
Vol. 111 (2025)
-
Vol. 110 (2024)
-
Vol. 109 (2023)
-
Vol. 108 (2022)
-
Vol. 107 (2021)
-
Vol. 106 (2020)
-
Vol. 105 (2019)
-
Vol. 104 (2018)
-
Vol. 103 (2017)
-
Vol. 102 (2016)
-
Vol. 101 (2015)
-
Vol. 100 (2014)
-
Vol. 99 (2013)
-
Vol. 98 (2012)
-
Vol. 97 (2011)
-
Vol. 96 (2010)
-
Vol. 95 (2009)
-
Vol. 94 (2008)
-
Vol. 93 (2007)
-
Vol. 92 (2006)
-
Vol. 91 (2005)
-
Vol. 90 (2004)
-
Vol. 89 (2003)
-
Vol. 88 (2002)
-
Vol. 87 (2001)
-
Vol. 86 (2000)
-
Vol. 85 (1999)
-
Vol. 84 (1998)
-
Vol. 83 (1997)
-
Vol. 82 (1996)
-
Vol. 81 (1995)
-
Vol. 80 (1994)
-
Vol. 79 (1993)
-
Vol. 78 (1992)
-
Vol. 77 (1991)
-
Vol. 76 (1990)
-
Vol. 75 (1989)
-
Vol. 74 (1988)
-
Vol. 73 (1987)
-
Vol. 72 (1986)
-
Vol. 71 (1985)
-
Vol. 70 (1984)
-
Vol. 69 (1983)
-
Vol. 68 (1982)
-
Vol. 67 (1981)
-
Vol. 66 (1980)
-
Vol. 65 (1979)
-
Vol. 64 (1978)
-
Vol. 63 (1977)
-
Vol. 62 (1976)
-
Vol. 61 (1975)
-
Vol. 60 (1974)
-
Vol. 59 (1973)
-
Vol. 58 (1972)
-
Vol. 57 (1971)
-
Vol. 56 (1970)
-
Vol. 55 (1969)
-
Vol. 54 (1968)
-
Vol. 53 (1967)
-
Vol. 52 (1966)
-
Vol. 51 (1965)
-
Vol. 50 (1964)
-
Vol. 49 (1963)
-
Vol. 48 (1962)
-
Vol. 47 (1961)
-
Vol. 46 (1960)
-
Vol. 45 (1959)
-
Vol. 44 (1958)
-
Vol. 43 (1957)
-
Vol. 42 (1956)
-
Vol. 41 (1955)
Keyword Ranking
06 Sep. (Last 30 Days)
Tetsu-to-Hagané Vol. 57 (1971), No. 8
Theoretical Analysis of LD Converter Operation by Mathematical Model Considered Scrap-Melting Process
Shigeo ASAI, Iwao MUCHI
pp. 1331-1339
Abstract
In order to predict the behaviors of process veriables which may be caused by the melting process of scrap fed into LD converter, a mathematical model for the scrap-melting process has been involved into the mathematical model of LD converter proposed by the authors previously, and concerning the relations between the temperature of steel bath and the carbon concentration in molten steel under various operating conditions, numerical calculations have been conducted with the aid of digital computer, and the calculated results of the transitional variations of these two variables have been illustrated on the T-C diagram. From the comparisons of the calculated results with the operating results obtained by the other investigators in LD converter, it may be considered that the model presented in this paper is applicable for the prediction of the behaviors of process variables even in the operations of the comparatively high value of scrap ratio.
Furthermore, an theoretical analysis concerning the effects of the process of scrap melting on the transitional variations of the process variables in the converter has been developed in this paper.
Stress Corrosion Cracking of 18-8 Austenitic Stainless Steel in Sulfuric Acid
Mitsuo ASAWA
pp. 1340-1349
Abstract
Weight loss and fracture time measurements of 18-8 stainless steel were performed with 4N H2SO4 solution containing sodium halides of various concentrations in the temperature range 25°C-98°C.
Crackings of the tensile specimens occurred within the temperature range 60°C-98°C in the acid solution containing chloride, bromide, or iodide, concentrations of which were about 2×10-25×10-1N, 10-4-10-3N, or 5×10-6-5×10-5N respectively. The effect of temperature on the time to fracture caused in the chloride containing solution was identical with that in the iodide containing solution within the temperature range 45×C-98×C and was also identical with that in the bromide containing solution within the temperature range 60×C-80×C. In the acid solution with chloride, applied anodic current made the time to fracture shorter and cathodic current made it longer.
Although observed crackings were closely related to the inhibiting property of halogen ions, yet they may be not stress sorption cracking but stress corrosion cracking, where the halogen ions may act as passivating species on slightly deformed areas and as activating species on heavily deformed areas of the steel. Rate-termining mechanism of these crackings may not change in the temperature range 6×C-80×C.
On the Determinations of Gases in Iron and Steel by Vacuum Fusion Method Using Graphite Capsule
Yoshihiko ABE, Shintaro TAKAZAWA
pp. 1350-1359
Abstract
In order to eliminate the disadvantages occured on vacuum fusion method using graphite crucible for determining the gases in iron and steel, the technique using graphite capsule was investigated in this report.
The content of gas in graphite capsule are minimized by previous de-gassing and the following storage in vacuum, so that the oxygen and nitrogen in iron are satisfactorily determined. On the other hand, numerous experiments have been carried out to estimate the effects of the elements dissolved in iron, and the following advantages are detected for the capsule method:
1. The getterings of oxygen and nitrogen by dissolved metals having high vapor pressure do not occur.
2. The gases such as CO2, COS and SO2, which are formed in carbon-saturated melt containing S or volatile oxide, are converted into CO.
3. As the formation of viscous melt due to the growth of precipitated graphite in flake form is disturbed, the extraction rate of gas is promoted.
In addition, as the increase in the solubility of gas in the melt does not concern with incomplete degassing of the gas in its melt on wide concentration range of steels, vacuum fusion method using graphite capsule is suitable for a routine analysis of oxygen in commercial steels.
Readers Who Read This Article Also Read
Tetsu-to-Hagané Vol.57(1971), No.1
Tetsu-to-Hagané Vol.79(1993), No.2
Tetsu-to-Hagané Vol.59(1973), No.13
State Analysis of Small Amount of Aluminium in Carbon Steel and Low Alloy Steel
Shigeo WAKAMATSU
pp. 1360-1371
Abstract
A simple and reliable method has been developed for the state analysis of small amount of aluminum in steel. The procedure is as follows: 1. Separation of aluminum compound
(a) The steel sample covered with close-texture filter peper as a diaphragm, connected as an anode, is dissolved into 130ml of 1% NaCl-5% EDTA electrolyte (pH 6-7) with current density of 50mA/cm2 for 2hr. Remove the anode, and residue is collected into filter paper using methanol. Add 50ml of 4% iodine methanol solution to the residue and warm at 60× for 30 min.
(b) Filter and wash with methanol. Add 10ml of HNO3 and 10ml of HClO4 to the filterate and evaporate to dense white fumes. Cool, dilute to 100ml, and determine aluminum in cementite in accordance with section 2.
(c) Transfer a fifth parts of the electrolyte to a beaker. Add 15ml of HNO3 and 10ml of HClO4 and evaporate to dense white fumes. Cool, dilute to 100ml, and determine aluminum as solid solution in accordance with section 2.
(d) Transfer the paper and residue (paragraph (b)) to a beaker, add 30ml of HNO3 (1: 1) and 5ml of H2O2 and boil for 10min.
(e) Filter and wash with water. Add 10ml of HClO4 to the filterate and evaporate to dense white fumes. Cool, dilute to 100ml, and determine aluminum as AlN in accordance with section 2.
(f) Transfer the paper and residue (paragraph (e)) to a platinum crucible, heat until the carbon is gone. Add 1g of Na2CO3 and ignite for 20min at 900 to 1000×C. Cool, dissolve in 30ml of water containing 5m/ of HCl. Add 10m/ of HClO4 and evaporate to dense white fumes. Cool, dilute to 20ml. Filter through into a 100ml volumetric flask, and wash with water until to the mark, and determine aluminum as oxide in accordance with section 2.
2. Photometric determination of aluminum.
Transfer 5ml of each of the solutions of section 1 (b), (c), (e) and (f) to 50 ml volumetric flasks. To each, add 10 ml of water and 5 ml of 0.1% Eriochrome Cyanine R solution and allow to stand for 2 to 3 min. Add 3 ml of 2% mercaptoacetic acid and 10 ml of buffer solution and dilute to 50 ml. Warm at 80×C for 1min. Cool and measure the absorbance against blank solution at 590 mu.
Developments of On-Line Ultrasonic Testing Apparatus in Iron and Steel Industries
Hitoshi DOMON
pp. 1372-1384
Article Access Ranking
06 Sep. (Last 30 Days)
-
Perspectives on the Promising Pathways to Zero Carbon Emissions in the Steel Industry toward 2050
ISIJ International Vol.65(2025), No.2
-
Growth, Removal, and Agglomeration of Various Type of Oxide Inclusions in Molten Steel
Tetsu-to-Hagané Vol.111(2025), No.11
-
Finite Element Analysis of Bubble Growth and Particle Swelling during Coal Pyrolysis
ISIJ International Vol.65(2025), No.9
-
Interface behavior leading to Al/Cu dissimilar metal bonding formation with high-speed eutectic reaction induced by applying current
QUARTERLY JOURNAL OF THE JAPAN WELDING SOCIETY Vol.43(2025), No.2
-
Corrosion Behavior of Carbon Steel under Soil Drying Conditions
ISIJ International Advance Publication
-
Cold Spot Joining of 980 MPa-class Ultra-high Strength Steel
Tetsu-to-Hagané Advance Publication
-
Combination Effect of Premixing Conditions and Iron Ore Size Distribution in Sintered Ore Granulation Process with Intensive Mixer
ISIJ International Advance Publication
-
A preliminary study on reduction degradation of iron ore sinter using sinter analogue and X-ray micro-computed tomography (MCT)
ISIJ International Advance Publication
-
Copper removal of liquid steel containing 0.25 % carbon using Fe2O3-CaCl2-SiO2 flux
ISIJ International Advance Publication
-
Evaluation of Feature Selection Methods for Oxygen Supply Prediction in BOF Steelmaking
ISIJ International Advance Publication
You can use this feature after you logged into the site.
Please click the button below.