- TOP
- Tetsu-to-Hagané
- Vol. 57 (1971), No. 5
Tetsu-to-Hagané Vol. 57 (1971), No. 5
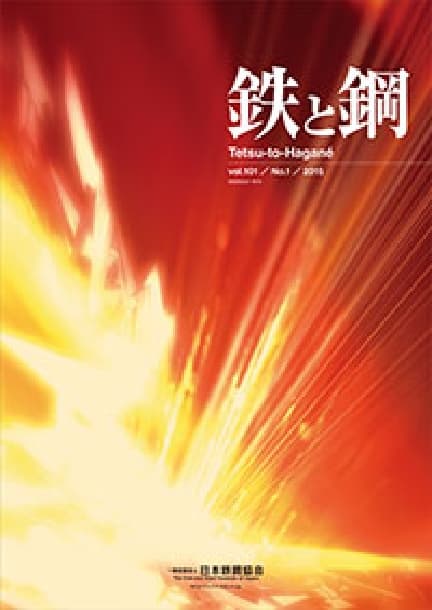
Grid List Abstracts
ONLINE ISSN: | 1883-2954 |
PRINT ISSN: | 0021-1575 |
Publisher: | The Iron and Steel Institute of Japan |
Backnumber
-
Vol. 111 (2025)
-
Vol. 110 (2024)
-
Vol. 109 (2023)
-
Vol. 108 (2022)
-
Vol. 107 (2021)
-
Vol. 106 (2020)
-
Vol. 105 (2019)
-
Vol. 104 (2018)
-
Vol. 103 (2017)
-
Vol. 102 (2016)
-
Vol. 101 (2015)
-
Vol. 100 (2014)
-
Vol. 99 (2013)
-
Vol. 98 (2012)
-
Vol. 97 (2011)
-
Vol. 96 (2010)
-
Vol. 95 (2009)
-
Vol. 94 (2008)
-
Vol. 93 (2007)
-
Vol. 92 (2006)
-
Vol. 91 (2005)
-
Vol. 90 (2004)
-
Vol. 89 (2003)
-
Vol. 88 (2002)
-
Vol. 87 (2001)
-
Vol. 86 (2000)
-
Vol. 85 (1999)
-
Vol. 84 (1998)
-
Vol. 83 (1997)
-
Vol. 82 (1996)
-
Vol. 81 (1995)
-
Vol. 80 (1994)
-
Vol. 79 (1993)
-
Vol. 78 (1992)
-
Vol. 77 (1991)
-
Vol. 76 (1990)
-
Vol. 75 (1989)
-
Vol. 74 (1988)
-
Vol. 73 (1987)
-
Vol. 72 (1986)
-
Vol. 71 (1985)
-
Vol. 70 (1984)
-
Vol. 69 (1983)
-
Vol. 68 (1982)
-
Vol. 67 (1981)
-
Vol. 66 (1980)
-
Vol. 65 (1979)
-
Vol. 64 (1978)
-
Vol. 63 (1977)
-
Vol. 62 (1976)
-
Vol. 61 (1975)
-
Vol. 60 (1974)
-
Vol. 59 (1973)
-
Vol. 58 (1972)
-
Vol. 57 (1971)
-
Vol. 56 (1970)
-
Vol. 55 (1969)
-
Vol. 54 (1968)
-
Vol. 53 (1967)
-
Vol. 52 (1966)
-
Vol. 51 (1965)
-
Vol. 50 (1964)
-
Vol. 49 (1963)
-
Vol. 48 (1962)
-
Vol. 47 (1961)
-
Vol. 46 (1960)
-
Vol. 45 (1959)
-
Vol. 44 (1958)
-
Vol. 43 (1957)
-
Vol. 42 (1956)
-
Vol. 41 (1955)
Keyword Ranking
29 Aug. (Last 30 Days)
Tetsu-to-Hagané Vol. 57 (1971), No. 5
On the Production of Cast Iron Rolls and Cast Steel Rolls
Kakunosuke MIYASHITA
pp. 696-724
Readers Who Read This Article Also Read
Tetsu-to-Hagané Vol.57(1971), No.1
Tetsu-to-Hagané Vol.79(1993), No.2
Tetsu-to-Hagané Vol.59(1973), No.13
On the Application Results and the Properties of Forged White Cast Iron Roll
Yuichiro SATO, Hiroshi KOHIRA
pp. 738-751
Abstract
A great progress has recently been made in Japanese steel rolling equipments with the increase of production capacity and the improvement in the quality of products. And there are requirements for better roll materials. The forged iron roll whose trade name is N-T roll is the one having an entirely new material property, manufactured by carrying out a special hot forging on white cast iron body which has a composition range of high purity hypoeutetic pig iron. This report describes the characteristic properties of this roll, focusing upon the results of hot rolling of various steels by this roll.
The following characteristics of the roll were confirmed by the rolling application.
(1) Rolling tonnage per dressing is remarkably increased.
(2) The cycle of roll exchange for dressing is made unexpectedly longer and it contributed greatly to the increase of productivity.
(3) Rolling cost is decreased.
(4) Accuracy of dimention of rolled products is increased.
(5) Surface of the rolled products becomes more beautiful.
Studies on the Work Roll Life and its Materials of Hot Strip Mill Roughing Stands
Yasuo ARIMURA, Ryoji KURATSU, Ichiro FUKUNAGA
pp. 752-760
Abstract
This paper presented some experiences of work roll life and roll materials of hot strip mill roughing stands in the Chiba Works of Kawasaki Steel Co. First we tried the similar roll materials as slabbing mill for the two high roughing stand. After tried several typcs of roll such as alloy cast steel and ductile cast steel rolls, we find the work roll conditions are much more severe than the slabbing mill. Either double poured cast steel rolls or light forged adamit cast steel rolls has been used now, and having relatively long work roll life.
Similar trials were done for the work rolls of four high roughing stands, and high hardness adamite cast steel work rolls has been used.
Work Rolls in Hot Strip Mills
Hidemaro KAWAHARA
pp. 761-772
Abstract
The work roll materials in hot strip mills and the damages of rolls which arise in rolling operation are discussed in this paper.
As for the rolls in stands of the first half of a roughing mill train, wear and heat cracking are most important problems. The double-poured hard cast steel rolls give excellent rolling performances in these stands. As scale banding and surface deterioration of the rolls are maintroubles in stands of second half of the roughing train and in stands of the first half of finishingtrain, new adamite rolls with fine metallic structures give good results. Wear of roll surface, cracks, and surface spallings due to the rolling of cobbled sheet are main roll damages in the stands of the second half of the finishing train. In oder to prevent these damages, new double-poured alloyed grain rolls made by centrifugal casting method are used for these stands.
Readers Who Read This Article Also Read
Tetsu-to-Hagané Vol.74(1988), No.10
ISIJ International Vol.32(1992), No.11
ISIJ International Vol.32(1992), No.11
Experience in the Application of Work Rolls for Hot Strip Mill
Kozo YAMADA, Shuko MATSUMOTO, Kunio NUMATA
pp. 773-780
Abstract
The quality of rolls for hot strips has a significant effect on the surface condition of the strip and the productivity of hot strip mill. In addition, the roll cost is an important part of the total production cost of the strip. For the achievement of a more economical production, it is essential to improve the quality of rolls and use the rolls more effectively.
This paper presents some of the measures taken for this purpose and results of application of hot strip mill work rolls.
Studies on Strength of Plate Mill Roll Wobbler
Masao KONDO, Hideo NAKAMURA
pp. 781-784
Abstract
Following the fast development of mill drives, working conditions of plate mill roll wobbler becomes more severe than ever before. This paper presented studies of strength of roll wobblers from stand point of fatigue strength. It was found the tensile strength of roll wobbler material should be at least 22kg/cm2for the case of the 4.7m plate mill of Nagoya Works, Nippon Steel Corp.
Durabilities and Materials of Rolls for Cold Strip Mill
Tadashi SHIMEGI, Haruhiko HIROSE
pp. 785-794
Abstract
The most important characterisitics required for forged hardened steel rolls for cold strip mill are high wear and abrasion resistibility, high resistibility against heat cracking caused by rolling accidents and an enough depth of fully hardened layer.
In case of a dull surfaced roll, an important factor is that the roll works effectively for easy dull surfacing and keeps a long life.
The experimental data on the effects of alloy elements as dissolved in matrix show that, a roll-steel of the following chemical composition gives most excellent properties for the above-mentioned requirements; 0.8% C-1.0% Si-2.2% Cr-0.25% Mo-1.5% Co. Shore hardness reading on the roll surface always varies depending on residual stress. Therefore, much attention should be given to compressive because it has a serious effect on the hardness of a forged hardened roll regarding its dull surfacing work.
Some Considerations on the Life of Work Rolls for Cold Rolling
Satoshi IKETAKA, Kaoru NOHARA
pp. 795-807
Abstract
The life of work rolls for cold rolling has a very important role on productivity.
Factors affecting the life of the work rolls are considered in three categories;(1) resistibility to cracking, (2) thickness of the hardened layer, and (3) resistibility to spalling.
The results of this investigation are as follows;(1) The frequency of the “burning” when the strip was broken reaches 13.5% of the total times of roll changing, and the sum of ground thickness attributable to the cause of burning amount up to about 70% of the total ground thickness.(2) The improvement of the quality of rolls by changing the chemical composition and the heat treatment resulted in the reduction of the average grinding loss to 60% and the increase ofrolling tonnage to twice.(3) The roll with thicker hardened layer shows better rolling tonnage and good surface quality of strip and button marks, nonmetallic inclusions, dendrite structure, etc. are minimized.(4) The spalling phenomena of rolls are different by the type of the rolling mill. Band-type fatigue fracture is chiefly seen in cold rolling and in rather large diameter roll, and on the other hand, shell-type fatigue fracture is seen in temper rolling and in small diameter roll. Moreover, the spalling occurs easily in winter and especially in thermally by unequivalent conditions when the roll is warmed up in operation and when the roll is cooled down after operation.
Some Properties of Work Rolls for Cold Rolling Mill, Hardened by Progressive Double Frequencies Induction
Yosimasa KUBO, Taira NAKANO, Masao IKENO, Yasusiro HAYASI
pp. 808-817
Abstract
The increment of hardened depth is effective as one of the means for prolongingthe life of work rolls for cold rolling. From this point of view, efforts have been made to increase the hardened depth. In the case of induction heating, the depth depends mainly upon its frequencies.Recently, lower frequencies have been applied rather than higher frequencies.
This paper reports some properties of work rolls for cold rolling hardened by progressive induction hardening method using double frequencies of 60 and 1 200 cycles.
Readers Who Read This Article Also Read
Tetsu-to-Hagané Vol.50(1964), No.12
Tetsu-to-Hagané Vol.60(1974), No.4
Tetsu-to-Hagané Vol.64(1978), No.4
The Residual Deflection of Sleeved Back-up Rolls
Saburo TUTUMI, Senri HARA, Shozo YOSHII
pp. 818-822
Abstract
The residual deflection of sleeved back-up rolls for four high mills is described.
At first the mechanism and the cause of the residual deflection are described. Furthermore, the investigation how to prevent the residual deflection are discussed. It is confirmed that applying the fluid pressure on shrink-fitted surface is most effective.
Readers Who Read This Article Also Read
Tetsu-to-Hagané Vol.52(1966), No.1
Tetsu-to-Hagané Vol.57(1971), No.1
Tetsu-to-Hagané Vol.50(1964), No.12
On the Work Roll Banding of the Hot Strip Mill Finishing Stand
Toshio SHIRAIWA, Fumio MATSUNO, Hajime TAGASHIRA
pp. 823-835
Abstract
An adamite work roll used in the hot strip finishing mill was examined to investigate the banding of work roll. Defects observed on the roll surface are heat cracks, pits and shallow hollows. The banded surface is dense aggregation of pits and shallow hollows.
Heat cracks are observed at all roll surface and they are about 100-200μdeep. It is ascertained from their fracture surface that they are formed by thermal fatigue.
Pits are about 100-120μ deep and it is considered that heat cracks and large cementites cause the local crumbling which develops into pits.
Shallow hollows are observed only in the banding zone and moreover the greater parts of the banding zone are occupied by them. They are about 0.2-0.5mm wide, 0.5-2.0mm long and less than 20μ deep. The observation by electron scanning microscope shows that they are formed by the abrasion by hard substances. It is suggested from the hardness measurements at high temperature that large cementites in the roll and magnetites in the scales of hot strips may be abrasive substances.
Scales on the surface and in the cracks are studied by X-ray diffraction and electron probe microanalyser. The scale on the surface are considered to be attached ones from hot strips and these in the cracks are considered to be oxides of the roll material.
Readers Who Read This Article Also Read
Tetsu-to-Hagané Vol.57(1971), No.1
Tetsu-to-Hagané Vol.79(1993), No.2
Tetsu-to-Hagané Vol.59(1973), No.13
Some Investigations on the Thermal Shock Crack of Cold Strip Mill Work Roll Materials
Kiyozo SAKABE, Hirosuke TABE
pp. 836-848
Abstract
Slipping, pitching and other behaviors of roll for cold strip mill, especially work roll bring about thermal shock cracks on this surface in their service condition, which will affect roll life.
This paper discribes on the investigation as to the influence of material compositions and heat treatment cunditions on the thermal shock crack depth and shows the superior of 3-5 % Cr-Mo steel containing more chromium than ordinal 1-2 % Cr-Mo Steel. The practical rolling mill use of new type roll of 3-5 % Cr-Mo steel proved the extremely extended roll life.
A thermal shock testing machine which utilizing frictional heat generated by contacting rotating disc and test specimen was developed for the present investigation and qauntitative measure of crack depth in the test specimen due to the thermal shock was introduced for the evaluation of roll materials.
Studies on the Surface Wear of Work Roll of Cold Strip Mill
Hidemitsu TAKEUCHI, Seiichi YAZAKI, Masuo HAYASHI
pp. 849-866
Abstract
A defect called“orange skin” of“rippling” is often found on the surface of work rolls of cold strip mill after 300-500 tons of steel strip have been rolled.
We observed the roll surface by photo-and electron-microscope after these defects had developed.Also, we investigated the effects of hardness, micro-segregation, and microstructure on the wear of roll materials. The results are summarized as follows:
(1) The cause of the defect formation is due to the microsegregation of roll surface.
(2) In this case the segregation index Is, which shows the degree of micro-segregation, is about 1.4from the line analysis of Cr by EPMA.
(3) To obtain higher homogeneity of the is lower than 1.2, the dendrite arm spacing after forging should be kept lower than 200. It is very difficult to obtain this condition.
(4) We could expect that, if the segregation index is 1.1 or 1.2, the defect formed on roll surface will be avoided by homogeneous carbide distribution and higher hardness by adopting suitable heat treatment.
Readers Who Read This Article Also Read
Tetsu-to-Hagané Vol.59(1973), No.11
Tetsu-to-Hagané Vol.59(1973), No.4
Tetsu-to-Hagané Vol.90(2004), No.12
Article Access Ranking
29 Aug. (Last 30 Days)
-
Perspectives on the Promising Pathways to Zero Carbon Emissions in the Steel Industry toward 2050
ISIJ International Vol.65(2025), No.2
-
Growth, Removal, and Agglomeration of Various Type of Oxide Inclusions in Molten Steel
Tetsu-to-Hagané Vol.111(2025), No.11
-
Copper removal of liquid steel containing 0.25 % carbon using Fe2O3-CaCl2-SiO2 flux
ISIJ International Advance Publication
-
Finite Element Analysis of Bubble Growth and Particle Swelling during Coal Pyrolysis
ISIJ International Vol.65(2025), No.9
-
Corrosion Behavior of Carbon Steel under Soil Drying Conditions
ISIJ International Advance Publication
-
Cold Spot Joining of 980 MPa-class Ultra-high Strength Steel
Tetsu-to-Hagané Advance Publication
-
Factors Affecting Generation of Iron Fines in Cold Sheet Rolling of Steel
ISIJ International Vol.65(2025), No.9
-
Experimental Study on Heat Transfer Characteristics of a Moving Single-Nozzle Jet Impingement
ISIJ International Vol.65(2025), No.9
-
Combination Effect of Premixing Conditions and Iron Ore Size Distribution in Sintered Ore Granulation Process with Intensive Mixer
ISIJ International Advance Publication
-
Evaluation of Feature Selection Methods for Oxygen Supply Prediction in BOF Steelmaking
ISIJ International Advance Publication
You can use this feature after you logged into the site.
Please click the button below.