- TOP
- Tetsu-to-Hagané
- Vol. 70 (1984), No. 7
Tetsu-to-Hagané Vol. 70 (1984), No. 7
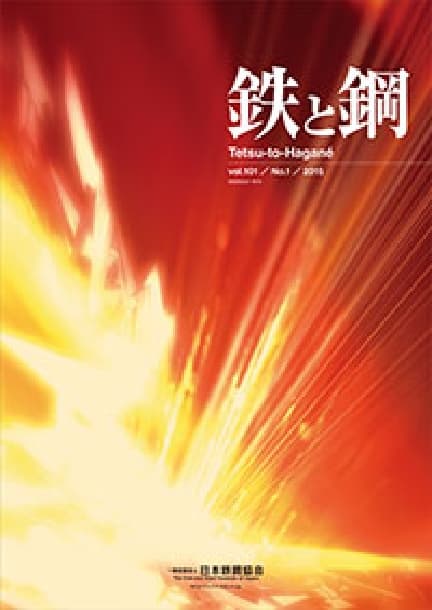
Grid List Abstracts
ONLINE ISSN: | 1883-2954 |
PRINT ISSN: | 0021-1575 |
Publisher: | The Iron and Steel Institute of Japan |
Backnumber
-
Vol. 111 (2025)
-
Vol. 110 (2024)
-
Vol. 109 (2023)
-
Vol. 108 (2022)
-
Vol. 107 (2021)
-
Vol. 106 (2020)
-
Vol. 105 (2019)
-
Vol. 104 (2018)
-
Vol. 103 (2017)
-
Vol. 102 (2016)
-
Vol. 101 (2015)
-
Vol. 100 (2014)
-
Vol. 99 (2013)
-
Vol. 98 (2012)
-
Vol. 97 (2011)
-
Vol. 96 (2010)
-
Vol. 95 (2009)
-
Vol. 94 (2008)
-
Vol. 93 (2007)
-
Vol. 92 (2006)
-
Vol. 91 (2005)
-
Vol. 90 (2004)
-
Vol. 89 (2003)
-
Vol. 88 (2002)
-
Vol. 87 (2001)
-
Vol. 86 (2000)
-
Vol. 85 (1999)
-
Vol. 84 (1998)
-
Vol. 83 (1997)
-
Vol. 82 (1996)
-
Vol. 81 (1995)
-
Vol. 80 (1994)
-
Vol. 79 (1993)
-
Vol. 78 (1992)
-
Vol. 77 (1991)
-
Vol. 76 (1990)
-
Vol. 75 (1989)
-
Vol. 74 (1988)
-
Vol. 73 (1987)
-
Vol. 72 (1986)
-
Vol. 71 (1985)
-
Vol. 70 (1984)
-
Vol. 69 (1983)
-
Vol. 68 (1982)
-
Vol. 67 (1981)
-
Vol. 66 (1980)
-
Vol. 65 (1979)
-
Vol. 64 (1978)
-
Vol. 63 (1977)
-
Vol. 62 (1976)
-
Vol. 61 (1975)
-
Vol. 60 (1974)
-
Vol. 59 (1973)
-
Vol. 58 (1972)
-
Vol. 57 (1971)
-
Vol. 56 (1970)
-
Vol. 55 (1969)
-
Vol. 54 (1968)
-
Vol. 53 (1967)
-
Vol. 52 (1966)
-
Vol. 51 (1965)
-
Vol. 50 (1964)
-
Vol. 49 (1963)
-
Vol. 48 (1962)
-
Vol. 47 (1961)
-
Vol. 46 (1960)
-
Vol. 45 (1959)
-
Vol. 44 (1958)
-
Vol. 43 (1957)
-
Vol. 42 (1956)
-
Vol. 41 (1955)
Keyword Ranking
04 Sep. (Last 30 Days)
Tetsu-to-Hagané Vol. 70 (1984), No. 7
Characterization of Passive Films on Stainless Steels Using Modern Surface Analysing Techniques
Katsuhisa SUGIMOTO
pp. 637-649
Emission Spectrometry with Inductively Coupled Plasma as Light Source
Tsutomu TAKAHASHI, Osamu KUJIRAI
pp. 650-656
Melting Model of Iron Ore Sintering
Shun SATO, Takazo KAWAGUCHI, Minoru ICHIDATE, Mayumi YOSHINAGA
pp. 657-664
Abstract
A fundamental study was carried out on melting process and its primary controlling factors in the iron ore sintering. Melting properties of sinter feed were evaluated by the volume ratio of the melted portion to the substantial solid of sinter, "melting ratio". From sinter pot test, the corelation between the melting ratio and the sinter operational conditions was studied. The melting process in sintering depended on the holding time in high-temperature zone, are particle size, its chemical composition, and porosity after dehydration. On the basis of the obtained information, a model simulation of sinter melting process was developed and was discussed by comparing the observed values and the calculated ones by the model. The calculated values were in good agreement with the observed values. This melting model for sintering process can be applied to the estimation of sinter feed and analysis of sinter quality.
Readers Who Read This Article Also Read
ISIJ International Vol.38(1998), No.1
ISIJ International Vol.47(2007), No.2
ISIJ International Vol.55(2015), No.12
Evaluation of Softening Properties of Sinter and Gas Flow in the Blast Furnace
Teruhisa SHIMODA, Koichi KURITA, Yuji IWANAGA
pp. 665-671
Abstract
The softening test under the simulated conditions in a real blast furnace and the gas permeability test through the softened sinter were carried out. An attempt was made to express the pressure drop through the softened sinter bed by the pressure drop equation including the terms of first- and second-order of velocity.
From the view point of blast furnace operation, high temperature properties of sinter were evaluated by applying the test results to the mathematical gas flow model.
The main results obtained are as follows.
1) When the gas flow resistance obtained from the softening test at high temperatures is increased, the radial gas flow in the cohesive zone becomes predominant and the permeability in the blast furnace becomes worse.
2) When the high temperature properties of sinter become worse, the formation of inverse V-shaped cohesive zone prevents the increase of the total gas pressure loss in the blast furnace.
Manganese Equilibrium between Molten Iron and MgO-saturated CaO-FetO-SiO2-MnO-P2O5 Slags
Hideaki SUITO, Ryo INOUE
pp. 672-679
Abstract
Manganese distribution between liquid iron and MgO-saturated CaO-FetO-SiO2-MnO slags containing P2O5 or S has been obtained in the temperature range from 1550° to 1650°Cby use of magnesia crucibles. The manganese distribution ratio was found to increase with increasing SiO2 content and decreasing temperature. The close relationship between activity coefficients of MnO or equilibrium quotient kMn(=(%MnO)/{[%Mn]· (%FetO)}) and the slag basicity B (=[(%CaO)+0.3(% MgO)]/[(% SiO2)+(%P2O5)]) value was observed.
Refining Characteristics of Stainless Steel in Top and Bottom Blown Converter
Tsuyoshi KAI, Fumio HOSHI, Yoshioki KAMIDATE, Tetsuya YAMAGAMI
pp. 680-686
Abstract
The refining characteristics of stainless steel in top and bottom blown converter was studied by using a 45 ton LD converter in LD-VAC process where the bottom was equipped with two tuyeres blowing Ar and N2 gases. The results obtained are as follows:
1) The perfect mixing time (τs) shown in eq. (2) is effectively available to evaluate agitating and mixing characteristics of the top and bottom blown converter even in the refining of stainless steel through the consideration on the relations between [C] and (Cr2O3) at blow end and the carburization rate. The index of BOG is also available to use even if the oxide mainly formed is not FeO but Cr2O3.
2) The refining characteristics are improved by the top and bottom blowing when the rate of bottom blowing gas increase up to 0.06 Nm3/t·min at which τs is corresponding to 60 sec. The apparent partial pressure PCO becomes 0.9 to 1.0 and the C-O reaction seems to be equilibrium. On the other side, the apparent PCO in the conventional top blowing converter is more than unity and the reaction as a whole melt seems not to be equilibrium.
3) Nitrogen can sufficiently be used as a agitating gas, although the amount of ten to twenty percent of blowing nitrogen is absorbed into melt.
Improvement of Surface Quality of Continuously Cast Stainless Steel Slabs
Hidemaro TAKEUCHI, Shogo MATSUMURA, Takashi YANAI, Yasunobu IKEHARA
pp. 687-693
Abstract
The effect of continuous casting conditions on surface quality of austenitic stainless steel slabs have been investigated in order to roll slabs without surface conditioning.
Development of new continuous casting techniques such as high frequency-short stroke mould oscillation, low viscosity-carbonless mould powder, tundish refractories, one piece immersion nozzle and so on, made it possible to improve slab surface quality and to roll slabs without surface conditioning.
Development of Air-atomizing Mist Nozzles and Mist Cooling System for Continuous Casting
Masashi MITSUTSUKA, Yozo FUKUHISA, Makoto WAKE, Masaki OKAJIMA, Nagao MIYASHITA, Yasuo TAKEDA
pp. 694-700
Abstract
The use of air atomizing mist nozzle for the secondary cooling of continuous casting machine results in the following advantages over the conventional water spray nozzle: less longitudinal surface cracks and higher temperature of cast slabs, wide control range of cooling, and prevention of nozzle cloggings. The air injection to the water spray nozzle is also good for preventing nozzle cloggings.
The authors have developed a few types of air atomizing nozzles and their application techniques, including the air injection technique, for the secondary cooling system of the slab casters.
Discussed here are structual and fluidic features of the newly developed mist nozzles and the air injection type water spray nozzle with reference to some technical points concerning the new cooling system and the operational results.
Toughness Deterioration of 13Cr-3.8Ni Cast Steel in the Process of Tempering
Yoshitaka IWABUCHI
pp. 701-708
Abstract
In order to explain the toughness degradation of 13Cr-3.8Ni cast steel due to tempering, a systematic study on the effect of heating temperature and subsequent cooling on mechanical properties has been, carried out. When as quenched martensite is tempered, toughness reaches a minimum at about 550°C and increases with increasing temperature, and then decreases above 650°C as the result of thermal deformation of austenite reverted into martensite during cooling from tempering temperature. The low toughness at about 550°C seems to be due to temper embrittlement. In addition, it is observed that the toughness is deteriorated with the increase of strength when the specimen is cooled at slow rates after tempering.
Readers Who Read This Article Also Read
Tetsu-to-Hagané Vol.67(1981), No.1
Tetsu-to-Hagané Vol.71(1985), No.2
Tetsu-to-Hagané Vol.70(1984), No.5
The Effect of Microstructure on the Toughness and High-temperature Strength of 0.2C-3Ni-3Mo Precipitation Hardening Hot Work Alloy Tool Steel
Toshio OKUNO
pp. 709-716
Abstract
The effects of microstructure on toughness and high temperature strength of the 0.2C-3Ni-3Mo steel were investigated.
(1) The granular upper bainite structure, which was obtained by quenching at the rate of the half temperature time of 60 min, provides the following differences in properties compared with the martensite structure.
(a) After tempering at 400°C;
(i) The plane strain fracture toughness was lower but the difference was small. (ii) The fatigue crack propagation rate was smaller. (iii) The uniform elongation in tensile testing was higher.
(b) After tempering at precipitation hardening temperature of 550600°C, the plane strain fracture toughness and Charpy impact value were lower but the differences were small.
(c) The high-temperature strengths at the temperature higher than 600650°C were higher.
(2) Followings are microstructural factors relating to the above three behaviors ((a)(c)), respectively.
(a); (i) Larger effective grain size. (ii) Formation of excessively stable retained austenite located both along grain boundaries and in grains. (iii) Suppressed precipitation of M3C.
(b); (i) Not a large increase of tendency of carbide precipitation along the grain boundaries of prior austenite. (ii) Existing of retained austenite to some extent.
(c); Suppressed agglomeration of M2C carbides to higher temperature.
(3) This steel is superior in room temperature toughness and inferior in high temperature strength to the 0.2C-3Cr-W-Mo-V-Co steel.
The Effects of Microstructure and Texture on Toughness of Control-rolled Steel Bars
Yasuhiro MAEHARA, Fukukazu NAKASATO, Yasuya OHMORI, Fukunaga TERASAKI
pp. 717-724
Abstract
Texture and mechanical properties of low carbon microalloyed steel bars control-rolled in an oval/round process have been studied. Strength can be increased by decreasing rolling temperature without any ductility loss. This can be explained in terms of the refinement of ferrite grains as well as the work hardening by rolling in the γ/α duplex phase region. Ductile /brittle transition temperature (VTS) in Charpy impact test is also remarkably decreased by lowering rolling temperature, e. g, VTS<-196°C for the material with the finishing rolling temperature of 644°C. Such a marked improvement of toughness mostly arises from the refinement of microstructure although a significantly strong texture development promotes the occurrence of separations as well. The main and suborientations of texture developed are an unusual {100} <001> and a {111}{211} <011>, respectively. Fractographic examinations revealed that cleavage cracks either perpendicular to rolling direction or parallel to the rolling plane initiate within relatively coarse grains of the cube orientation elongated to rolling direction and that the propagation of such cracks is arrested by the surrounding extremely fine grained area of different orientations such as {111}{211} <011>. The initiation of separations cannot be explained by the CHAO'S model considering the plastic anisotropy due to the above textures.
Recrystallization Behaviour of Al and Al-Ti Containing 17Cr Ferritic Stainless Steel during Hot Rolling
Mitsuo ISHII, Hirofumi YOSHIMURA, Michio WAKAMATSU, Tadashi SAWATANI
pp. 725-732
Abstract
To investigate the recrystallization behaviour of Al and Al-Ti containing 17Cr ferritic stainless steel during hot rolling, the precipitation behaviour of AlN and Ti(C, N) in heated east slab was examined, and then wedge shaped specimens taken from the slab were hot rolled at 1173K to 1453K in single pass manner and hardness test and optical microscopic observation were conducted. The results are as follows.
When heating the slab of Al containing steel, AlN precipitates most easily at about 1273K; this gives the nose in precipitation behaviour.
With Al-Ti containing steel, almost all of Ti precipitated as Ti (C, N) in the as-solidified state, and this prevented precipitation of AlN.
The Al containing steel hot rolled at relatively lower heating temperature near 1173K exhibited deformation structure with deformation bands. The deformation band initiated at ferrite grain boundaries and dispersed AlN precipitates. The deformation structure changed into partial recrystallization structure with raising heating temperature to 1273K and increasing rolling reduction. In relatively higher heating temperature, recovery structure which contained many fine sub-boundaries was attained. Therefore the nose in recrystallization behaviour existed at near 1273K. It is considered that recrystallization structure is statically formed after hot rolling and recovery structure is dynamically formed in hot rolling.
Nearly the same results were obtained in Al-Ti containing steel. A peculiarity was found of the Al-Ti containing steel in structural changes during hot rolling, that is relatively coarse recrystallized grains existed in the recovered structure. This is considered attributable to dynamical recrystallization.
Readers Who Read This Article Also Read
Tetsu-to-Hagané Vol.63(1977), No.5
Tetsu-to-Hagané Vol.63(1977), No.5
Antioxidation Mechanism of an Oxidation Inhibitor Composed of Refractory Powder-SiO2-Al-Synthetic Mica-Colloidal Silica-Coking Bond
Hisao ODASHIMA, Minoru KITAYAMA, Shigeyoshi MAEDA
pp. 733-740
Abstract
Antioxidation mechanism of a newly developed oxidation inhibitor composed of a refractory powder-SiO2-aluminum-synthetic mica-colloidal silica-coking bond has been investigated.
During heating, the metallic silicon is formed after the reduction by the metallic aluminum of both mullite (3Al2O3·2SiO2) containing in refractory powder and SiO2. This is oxidized again so as to change gradually to protective amorphous SiO2 layer which acts as an excellent diffusion barrier to oxigen from atmosphere. Aluminum, in turn, is oxidized to form the protective films composed of α-Al2O3 and FeO·Al2O3. In addition, a spinel (FeO·Al2O3) prevents effectively the formation of low melting fayalite (2FeO·SiO2), and consequently the protective films remain stable even after prolonged heating at high temperatures.
On the other hand, a lot of pores are formed by the volume reduction due to the melting of aluminum, the oxidation of aluminum and the reduction of SiO2, by which the diffusion of Fe2+ and O2- is effectively inhibited.
Effects of S and Mn Contents on Pitting Resistance of 18-8 Stainless Steel
Kikuo TAKIZAWA, Yasuhiko SHIMIZU, Yoshihiro HIGUCHI, Imao TAMURA
pp. 741-748
Abstract
The effects of S and Mn contents on pitting corrosion behavior of 18-8 stainless steel have been studied by means of anodic polarization and immersion test in chloride media. The main results obtained are summarized as follows:
In 3% NaCl solution at 0 and 30°C, pitting potential (V'c100) had tendency to become less noble with the increase in S content. This tendency, however, could not be found for the specimens containing S above about 0.01%. On the other hand, V'c100 continuously became less noble with the increase in Mn content. In 3% NaCl solution at 70°C or 3% NaCl acidic (HGl) solution at 30°C, V'c100 depended on S and Mn contents, and it became noble with the decrease in those elements. In 10% FeCl3·6H2O solution at 25°C, the frequency of occurrence or the density of pits increased with the increase of the quantity of sulfide inclusions. On the other hand, the growth tendency of pits depended on the Mn/S ratio, and anodic reaction of specimen was retarded with decrease of the ratio. In all of the specimens, the pit initiation site, was sulfide inclusion/metal interface in the pitting potential region in NaCl and FeCl3·6H2O solution, and pit grew preferentially into the metal matrix.
Article Access Ranking
04 Sep. (Last 30 Days)
-
Perspectives on the Promising Pathways to Zero Carbon Emissions in the Steel Industry toward 2050
ISIJ International Vol.65(2025), No.2
-
Growth, Removal, and Agglomeration of Various Type of Oxide Inclusions in Molten Steel
Tetsu-to-Hagané Vol.111(2025), No.11
-
Finite Element Analysis of Bubble Growth and Particle Swelling during Coal Pyrolysis
ISIJ International Vol.65(2025), No.9
-
Interface behavior leading to Al/Cu dissimilar metal bonding formation with high-speed eutectic reaction induced by applying current
QUARTERLY JOURNAL OF THE JAPAN WELDING SOCIETY Vol.43(2025), No.2
-
Corrosion Behavior of Carbon Steel under Soil Drying Conditions
ISIJ International Advance Publication
-
Cold Spot Joining of 980 MPa-class Ultra-high Strength Steel
Tetsu-to-Hagané Advance Publication
-
Combination Effect of Premixing Conditions and Iron Ore Size Distribution in Sintered Ore Granulation Process with Intensive Mixer
ISIJ International Advance Publication
-
A preliminary study on reduction degradation of iron ore sinter using sinter analogue and X-ray micro-computed tomography (MCT)
ISIJ International Advance Publication
-
Copper removal of liquid steel containing 0.25 % carbon using Fe2O3-CaCl2-SiO2 flux
ISIJ International Advance Publication
-
Evaluation of Feature Selection Methods for Oxygen Supply Prediction in BOF Steelmaking
ISIJ International Advance Publication
You can use this feature after you logged into the site.
Please click the button below.