- TOP
- Tetsu-to-Hagané
- Vol. 54 (1968), No. 13
Tetsu-to-Hagané Vol. 54 (1968), No. 13
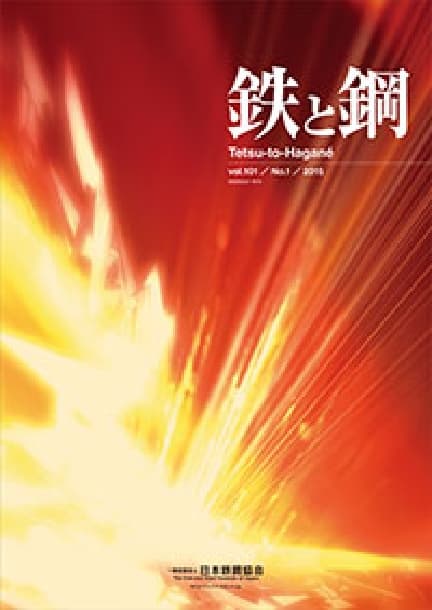
Grid List Abstracts
ONLINE ISSN: | 1883-2954 |
PRINT ISSN: | 0021-1575 |
Publisher: | The Iron and Steel Institute of Japan |
Backnumber
-
Vol. 111 (2025)
-
Vol. 110 (2024)
-
Vol. 109 (2023)
-
Vol. 108 (2022)
-
Vol. 107 (2021)
-
Vol. 106 (2020)
-
Vol. 105 (2019)
-
Vol. 104 (2018)
-
Vol. 103 (2017)
-
Vol. 102 (2016)
-
Vol. 101 (2015)
-
Vol. 100 (2014)
-
Vol. 99 (2013)
-
Vol. 98 (2012)
-
Vol. 97 (2011)
-
Vol. 96 (2010)
-
Vol. 95 (2009)
-
Vol. 94 (2008)
-
Vol. 93 (2007)
-
Vol. 92 (2006)
-
Vol. 91 (2005)
-
Vol. 90 (2004)
-
Vol. 89 (2003)
-
Vol. 88 (2002)
-
Vol. 87 (2001)
-
Vol. 86 (2000)
-
Vol. 85 (1999)
-
Vol. 84 (1998)
-
Vol. 83 (1997)
-
Vol. 82 (1996)
-
Vol. 81 (1995)
-
Vol. 80 (1994)
-
Vol. 79 (1993)
-
Vol. 78 (1992)
-
Vol. 77 (1991)
-
Vol. 76 (1990)
-
Vol. 75 (1989)
-
Vol. 74 (1988)
-
Vol. 73 (1987)
-
Vol. 72 (1986)
-
Vol. 71 (1985)
-
Vol. 70 (1984)
-
Vol. 69 (1983)
-
Vol. 68 (1982)
-
Vol. 67 (1981)
-
Vol. 66 (1980)
-
Vol. 65 (1979)
-
Vol. 64 (1978)
-
Vol. 63 (1977)
-
Vol. 62 (1976)
-
Vol. 61 (1975)
-
Vol. 60 (1974)
-
Vol. 59 (1973)
-
Vol. 58 (1972)
-
Vol. 57 (1971)
-
Vol. 56 (1970)
-
Vol. 55 (1969)
-
Vol. 54 (1968)
-
Vol. 53 (1967)
-
Vol. 52 (1966)
-
Vol. 51 (1965)
-
Vol. 50 (1964)
-
Vol. 49 (1963)
-
Vol. 48 (1962)
-
Vol. 47 (1961)
-
Vol. 46 (1960)
-
Vol. 45 (1959)
-
Vol. 44 (1958)
-
Vol. 43 (1957)
-
Vol. 42 (1956)
-
Vol. 41 (1955)
Keyword Ranking
07 Sep. (Last 30 Days)
Tetsu-to-Hagané Vol. 54 (1968), No. 13
Some Chemical Engineering Aspects of R-H Degassing Process
Hideo WATANABE, Koichi ASANO, Tsuyoshi SAEKI
pp. 1327-1342
Abstract
The degassing mechanism in the R-H degassing equipment was investigated by analyzing the degassing action by single bubble as a model, and these results were utilized to estimate the rate of the circulation flow and the decarburizatipn curve.
Of the total volume of CO reaction, one-third occurs within the up-leg and two-thirds within the vacuum chamber. This ratio, however, varies depending on the concentrations of carbon and oxygen in the liquid metal. If the concentrations are rather high, more reaction occurs within the up-leg, while higher ratio of the reaction is noted within the vacuum chamber at lower concentrations.
In deoxidizing low carbon steel, it is necessary to inject a substantial amount of argon in order to attain a below 100ppm level without using any deoxidizing agent. Although the inner pressure fo the vacuum chamber generally has much effect upon the degassing, significant effect is no longer shown at a pressure as low as minus 1 torr. In removing the hydrogen from killed steel, care should be taken to obtain much splash in the vacuum chamber.
The rate of the circulation flow is proportional to the 1·5th power of the inner diameter of the circulation legs and to the 0·33rd power of the argon injection rate. The rate of circulation flow in the treatment of undeoxidized steel attains its maximum when a certain rate of argon injection, which depends upon the leg size, is applied.
The Effects of Grain Size and Precipitates on Strength of Nb Treated Steels
Yunoshin IMAI, Yoshio SHONO
pp. 1343-1352
Abstract
Relationship between the strength and the change of grain size and precipitation behavior of NbC by various heat treatments was examined with pure 0.2% carbon steels containing 0.02-0.09% Nb.
The results were summarized as follows:
1. Though NbC particles precipitated in Nb treated steels tend to coalesce with increase of austenitizing temperature, they remain in steel and prevent the grain coarsening of austenite because of its small solubility and dissolving rate in austenite.
2. The highest strength was obtained when the cooling rate from austenitizing temperature to room temperature was 25°C/min.
When Nb treated steel is continuously cooled after full solution treatment for long time at sufficiently high temperature such as 1250°C, NbC seems to precipitate not only at lower temperatures than A3 point but also at the temperature range of austenite, and the precipitation from austenite will cause less strengthening effect than that from ferrite.
3. Strengthening effect by Nb treatment may be explicable on the assumption that both effects of grain refinement and dispersion of fine particles of NbC are additive; that is, an increase of strength in Nb treated steels austenitized at lower temperatures than about 1050°C is due mainly to refining of ferrite grain size and that at higher temperatures is due mainly to fine precipitation of NbC.
Readers Who Read This Article Also Read
Tetsu-to-Hagané Vol.54(1968), No.13
Effect of Metallographical Factors on the Rolling Fatigue Life of Ball Bearing Steel
Saburo SHIKO, Kazuo OKAMOTO, Shozo WATANABE
pp. 1353-1366
Abstract
Effect of metallographical factors on the rolling fatigue life of 1%C-1.5%Cr bearing steel was investigated, and the most profitable component for the bearing life was discussed.
The results obtained are as follows:
(1) Metallographical factors affected on the rolling fatigue life of bearing steel were not amount and size of residual cementite but the chemical compositions soluted in fhe matrix.
(2) The most effective factor affected on the rolling fatigue life was carbon content soluted in the matrix and the most desirable carbon content in the matrix was about 0.5 percent.
(3) It was recognized that the mechanism of flaking was related to the third stage of the tempering of martensite. This was deduced from the observation of the micro-structure of cyclic stressed area by the transmission electron microscopy and the result of bearing life test of a new type steel with higher silicon of which the starting temperature of the third stage was rised by silicon.
Readers Who Read This Article Also Read
Tetsu-to-Hagané Vol.49(1963), No.2
Tetsu-to-Hagané Vol.56(1970), No.1
Tetsu-to-Hagané Vol.53(1967), No.1
Some Exercises of Thermochemistry and Thermodynamics of Iron and Steel Making
Masayasu OHTANI
pp. 1381-1407
Article Access Ranking
07 Sep. (Last 30 Days)
-
Perspectives on the Promising Pathways to Zero Carbon Emissions in the Steel Industry toward 2050
ISIJ International Vol.65(2025), No.2
-
Growth, Removal, and Agglomeration of Various Type of Oxide Inclusions in Molten Steel
Tetsu-to-Hagané Vol.111(2025), No.11
-
Finite Element Analysis of Bubble Growth and Particle Swelling during Coal Pyrolysis
ISIJ International Vol.65(2025), No.9
-
Interface behavior leading to Al/Cu dissimilar metal bonding formation with high-speed eutectic reaction induced by applying current
QUARTERLY JOURNAL OF THE JAPAN WELDING SOCIETY Vol.43(2025), No.2
-
Copper removal of liquid steel containing 0.25 % carbon using Fe2O3-CaCl2-SiO2 flux
ISIJ International Advance Publication
-
Corrosion Behavior of Carbon Steel under Soil Drying Conditions
ISIJ International Advance Publication
-
Cold Spot Joining of 980 MPa-class Ultra-high Strength Steel
Tetsu-to-Hagané Advance Publication
-
Combination Effect of Premixing Conditions and Iron Ore Size Distribution in Sintered Ore Granulation Process with Intensive Mixer
ISIJ International Advance Publication
-
A preliminary study on reduction degradation of iron ore sinter using sinter analogue and X-ray micro-computed tomography (MCT)
ISIJ International Advance Publication
-
Viscosity Measurement of Foam with High Gas Volume Fraction Using Sphere Pull-up and Dam-break Experiments
ISIJ International Advance Publication
You can use this feature after you logged into the site.
Please click the button below.