- TOP
- Tetsu-to-Hagané
- Vol. 46 (1960), No. 4
Tetsu-to-Hagané Vol. 46 (1960), No. 4
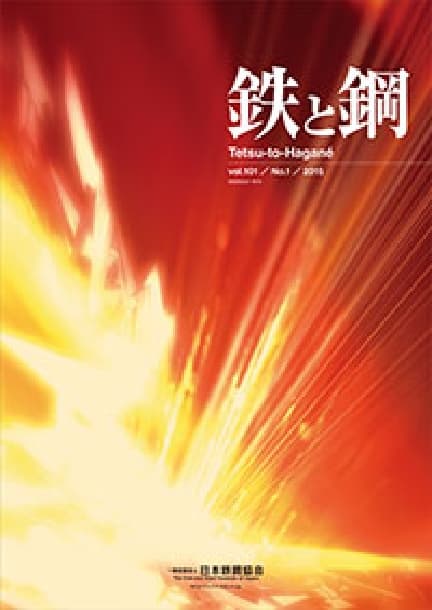
Grid List Abstracts
ONLINE ISSN: | 1883-2954 |
PRINT ISSN: | 0021-1575 |
Publisher: | The Iron and Steel Institute of Japan |
Backnumber
-
Vol. 111 (2025)
-
Vol. 110 (2024)
-
Vol. 109 (2023)
-
Vol. 108 (2022)
-
Vol. 107 (2021)
-
Vol. 106 (2020)
-
Vol. 105 (2019)
-
Vol. 104 (2018)
-
Vol. 103 (2017)
-
Vol. 102 (2016)
-
Vol. 101 (2015)
-
Vol. 100 (2014)
-
Vol. 99 (2013)
-
Vol. 98 (2012)
-
Vol. 97 (2011)
-
Vol. 96 (2010)
-
Vol. 95 (2009)
-
Vol. 94 (2008)
-
Vol. 93 (2007)
-
Vol. 92 (2006)
-
Vol. 91 (2005)
-
Vol. 90 (2004)
-
Vol. 89 (2003)
-
Vol. 88 (2002)
-
Vol. 87 (2001)
-
Vol. 86 (2000)
-
Vol. 85 (1999)
-
Vol. 84 (1998)
-
Vol. 83 (1997)
-
Vol. 82 (1996)
-
Vol. 81 (1995)
-
Vol. 80 (1994)
-
Vol. 79 (1993)
-
Vol. 78 (1992)
-
Vol. 77 (1991)
-
Vol. 76 (1990)
-
Vol. 75 (1989)
-
Vol. 74 (1988)
-
Vol. 73 (1987)
-
Vol. 72 (1986)
-
Vol. 71 (1985)
-
Vol. 70 (1984)
-
Vol. 69 (1983)
-
Vol. 68 (1982)
-
Vol. 67 (1981)
-
Vol. 66 (1980)
-
Vol. 65 (1979)
-
Vol. 64 (1978)
-
Vol. 63 (1977)
-
Vol. 62 (1976)
-
Vol. 61 (1975)
-
Vol. 60 (1974)
-
Vol. 59 (1973)
-
Vol. 58 (1972)
-
Vol. 57 (1971)
-
Vol. 56 (1970)
-
Vol. 55 (1969)
-
Vol. 54 (1968)
-
Vol. 53 (1967)
-
Vol. 52 (1966)
-
Vol. 51 (1965)
-
Vol. 50 (1964)
-
Vol. 49 (1963)
-
Vol. 48 (1962)
-
Vol. 47 (1961)
-
Vol. 46 (1960)
-
Vol. 45 (1959)
-
Vol. 44 (1958)
-
Vol. 43 (1957)
-
Vol. 42 (1956)
-
Vol. 41 (1955)
Keyword Ranking
06 Sep. (Last 30 Days)
Tetsu-to-Hagané Vol. 46 (1960), No. 4
On the Making of Self-Fluxing Sinter
Keiji Tsujihata, Shozo Miyakawa, Shigeru Otsubo, Shigeharu Ono, Isao Hanaki
pp. 455-460
Abstract
In line with the starting of experiments on the use of self-fluxing sinter in blast furnaces, the experimental production of lime sinter using 5-10% of lime stone was conducted at Kukioka D. L. Sintering Plant since May, 1958, and from the operation data the following, items were inferred: -
1) Although in lime sinter the mean grain size was getting smaller, the amount of the fine fraction (minus five millimeter fraction) became rather decreased than in normal sinter, from which it was inferred that lime sinter was more improved in point of grain distribution.
2) Lime sinter had almost the same degree of strength as normal sinter.
3) By adding 5-10% of lime stone, the output of sinter was increased by 4-6.5%. When calculated in terms of iron, the output, however, was almost constant.
4) In case of using the burden of 100% lime sinter, operation was carried out with special attention paid to the control of basicity, and for that purpose such measures as the use of foreign fine ores divided into the three classes according to SiO2 content, etc. were enforced, and, as the result, the sinter that could almost satisfy the requirements of blast furnaces was able to be produced.
5) Cost of sinter production was decreased by 2% and 5.5% by the addition of 5% and 10% of lime stone, respectively, but the cost in terms of iron was almost unchanged.
For these reasons it was concluded that lime sinterwas superior to normal sinter.
Influence of the Reducing Conditions on the Chemical Composition of Pig Iron
Akira Murakami, Kiyoshi Takai, Yuichiro Sato
pp. 460-466
Abstract
The fundamental studies on the reducing smelting of iron are and iron sand were researched by many authors. However in these researches, ores of solid state were reduced with reducing agent of gaseous state, it seemed to be not yet reported in details on the reducing smelting in molten state of these.
The authors reduced are and flux in molten state and studied on influence of the reducing conditions on the chemical composition of pig iron. When iron are and iron sand were redu. ced in various reducing conditions, the results were summarized as follows:
1) With increase of reducing temperature, Si, Mn and Ti content of pig iron were increased, S content decreased and P and V content did not change.
2) With increase of slag basicity (%ΣCaO/%ΣSiO2), Si and S content of pig iron were decreased, Mn content was increased, Ti content was increased gradually and V content did not change.
3) With increase ofΣTiO2 content in slag, Si, Mn and S content of pig iron was decreased gradually and Ti content was increased to the constant value on the same conditions but did not increase more than its value.
4) When the reduction of iron sand in comparison with iron are at the same conditions, in general, the one obtains high C and low Si content of pig iron and the other obtains low C and high Si content of pig iron.
5) Constituent range indicates the lowest melting temperature (1260. 1310.) of TiO2 containing slag exists between ΣTiO2 content in slag=20-25% and slag basicity %ΣCaO/ΣSiO2=0. 7. -0.8.
A New Scale of Basicity in Oxide Slags and the Basicity of the Slags Containing Amphoteric Oxides
Kazumi Mori
pp. 466-473
Abstract
The well-known fact, that γ=Fe3+/ (Fe2++Fe3+) is increased by additions of basic oxides and decreased by acidic oxides under the constant oxygen pressure, has been selected to measure the basicity of slags. If the concentration of the slag, whose basicity is to be determined, is represented by C=ΣM/ (ΣFe+ΣM), where ΣFe= Fe2++ Fe3+and ΣM=Ca2++ Si4++Ti4++Al3+. c. c, and γ of the pure iron oxide by γo, the new scale of basicity is given by the equation B { (γ-γo) /C } x10.
The studied slags are (1) pure oxides CaO, SiO2, TiO2 (2) binary slags CaO-SiO2, CaO-TiO2, SiO2-TiO2, CaO-Al2O3, SiO2-Al2O3, and (3) ternary slags CaO-SiO2-TiO2, CaO-SiO2-Al2O3. Samples used in the experiment are of iron oxide with additions of the slag, whose basicity is to be determined. The slag sample is equilibrated under an atmosphere of CO2/CO=133 at a temperature of 1480°C. The basicity (B) was determined from the results of analyses for Fe2+ and Fe3+.
The values of B for CaO, SiO2 and TiO2 are such as would be expected from the metaloxygen bond strength. In the systems CaO-5102 and CaO-TiO2, B changes approximately linearly with mol %, but in the system SiO2-TiO2 a maximum appears. The basicity of CaO is decreased by the additions of Al2O3, while that of SiO2 is increased.
Isobasicity lines of the ternary systems are shown in the ternary diagrams, and einpirical equations of basicity were obtained for the concentration range CaO/SiO2=1/3-4 and TiO2 (or Al2O3) =0-35%. At a certain CaO/SiO2 the basicity does not change with additions of TiO2 or Al2O3. The basicity corresponding to this CaO/SiO2 is termed the isoelectric point (Bi). At lower ratios of CaO/SiO2 B is increased and at higher ratios decreased by additions of TiO2 or Al2O3. Thus by the term of isoelectric point the amphoteric behaviour of slag constituents can be discussed quantitatively. It was found that Bi is decreased with increase of the metal-oxygen bond strength.
The Mechanism of Decarbonization
Takehiko Fujii
pp. 473-480
Abstract
From the many results of reports, (I)-(IV), the mechanism of decarbonization was considered, firstly in a high-frequency induction furnace in which slag did not exist and secondly in an open hearth furnace in which slag existed. The following results were obtained:
(1) In a high-frequency induction furnace in which slag did not exist, the inclination of moving velocity of molten steel by stir under free surface was small, and the boundary layer could be neglected. But there existed thin layer in which C was gradually decreased by reaction of oxygen during a flow along a free surface.
(2) Above the free surface, there existed Fe-O reaction phase. This phase was a thin layer in which existed (a) vapour of iron (this vapour pressure (1mmHg, 1600°C) decreased gradually as becoming more distant from the free surface.), (b) FeO molecules and FeO drops formed by association of FeO molecules, (e) oxygen moleeules, partial pressure of which was lower than above, and (d) CO and CO2 molecules which were reaction products of C and gaseous oxygen; and this phase showed resistance to encroach of oxygen to molten steel.
(3) In a high-frequency induction furnace in which slag did not exist, the decarbonization occurred mainly at the above-stated free surface, through which oxygen from gas phas and C in molten steel reacted, and reaction product, CO escaped immediately to gas phase. And so, the rate of decarbonization was controlled by arriving velocity of gaseoup oxygen when arriving velocity of C was higher and byarriving velocity of Cwhenarriving velocity of C was lower.
(5) In an open hearth furnace, oxy supplied through slag, and decarbonization. proceeded only by formation and escape of Co bubbles. Accordingly, in a high-frequency induction furnace, C-O relation was along Vacher & Hamilton's curve, but on the contrary, C-O relation was upper than Vacher & Hamilton's curve in the open hearth furnace.
(6) In the open hearth furnace, the tate determined steps were (a) movement of oxygen through the boundary layer between slag and molten steel, and (b) diffusion and escape of CO through the boundary layer between molten steel and gas phase of CO bubbles or crevices in the hearth.
Accelerating Combustion in the Open Hearth Furnace by Auxiliary Jets
Hidefumi Hasimoto
pp. 480-483
Abstract
Formerly1), the author pointed out that the burner jet is an important constituent of the open-hearth furnace and the combustion is controlled by changing the quantity of the atomizing agent.
The present paper deals essentially with changing flow patterns in furnaces by auxiliary jets. Flow patterns are changed, reinforced and corrected by a jet from the roof or the side walls.
An eddy spot appears behind the jet, the jet makes a temporary wall which is invisible aerodynamic), flexible (controllable) and free from wear.
It is not the jet quantity but the jet momentum that makes the jet effective. The auxiliary jet with smaller quantity and higher velocity is preferable, and either the kind of jet gas (air, oxygen of stream) or the temperature of it is of no significance.
On the Deterioration of Quenching Oils by Heat Decomposition
Masayosi Tagaya, Imao Tamura, Mitsugu Tanaka
pp. 483-487
Abstract
In N2 atmosphere, a Ni-Cr wire coil which was resistance-heated to about 900°C is repeatedly, and quenched into. the quenching oils every 60 s.. The heating coil of 30mm dia., and 40mm length was made of a 3. 2mm dia., 800mm long Ni-Cr wire.
This testing apparatus was newly deviced and built in oder to carry this experiment efficiently and reasonably in the condition nearest to the practical hardening operation.
The examined oils were (1) pure mineral oil (2) fatty oil and (3) mineral oil added with 10% polymerized heavy hydrocarbon to increase the cooling ability. The quenching oil bath contained 2l of oil to be examined, which was circulated at the rate of 10l/mn. through the cooling system and the oil temperature was held at about 30°C. After the repeated quenching tests of 4, 6, 10, 20, 30, 60 and 90 h, the properties of oils were determined.
As the conclusion, through the all kinds of oils examined, concerning to the cooling ability of quenching oil, the deterioration was remarkably less than that by oxidation and polymerization previously reported by the author but the lowering of the flash point was characteristically remarkable.
Effect of Mo, W, V and Nb on the Properties of 38% Ni Heat-Resisting Alloy
Sadao Koshiba, Tsuneo Kunou
pp. 487-492
Abstract
The Ni-Cr-Co-Mo heat resisting alloy which contains Ti and Al except for Mo, W, V and Nb shows superior heat-resistance due to precipitation of both intermetallic compounds of Ni and Ti, Al and carbides of Cr and Mo.
This report concerned the effect of Mo, W, V and Nb on the various properties of this alloy, and contained the experimental results on hardness as solution-treated and as aged, mechanical properties at room and high temperature, rupture strength, oxidation resistance and resultant microstructures.
The results obtaind were as follows:
(1) As the added element was increased, hardness after solution-treatment, as-aged hardness, tensile strength at room and high temperature, and then rupture strength was increased.
(2) Elongation, reduction of area, Charpy impact value and oxidation resistance were gradually decreased in parallel with the increase of added elements.
(3) Among the added elements, Nb was the most effective and Mo was the next, but the effect of W and V was hardly observed.
Determination of P, Cr and V in Basic Slag
Shigeo Wakamatszt
pp. 492-497
Abstract
This investigation was undertaken to a find a rapid and accurate chemical method for the analysis of basic slag. In the report (Pi), a simple spectrophotometric methods was des -cribed for determination of the P2O5, Cr2O3 and V which were contained in basic slag.
Determination of P2O5: Dissolve the sample (0. 5g.) with HCl and HClO4, and evaporate to fume. Dilute, and transfer the solution to a 250 ml volumetric flask, filtering off any residue. Dilute to the mark. Pipet an aliquot 25 to 50ml of solution into a 100ml volumetric flask. Add vanadate and molybdate. Dilute to the mark and mix well. After 5mn., measure the absorbance at 430m μ against the water.
Determination of Cr2O3: 2g. of sample mixed with 20g. of Na2O2 is fused, the product is extracted with water. Make up to 100ml with water. Pipet an aliquot 5to 10ml of solution into a 100ml volumetric flask. Dilute to the mark and mix well. Measure the absorbance. at 380m. μ against the water.
Determination of V: pipet an aliquot 10ml of solution from among 100ml of solution of the sample described above. Neutralize any excess base with HClO4. Add (NH4) 2S2O8, PAN, and acetone. Ajust to pH 3. 0 to 3. 5 with HClO4 or ammonium acetate. Transfer the solution to a 50ml volumetric flask and dilute to the mark. After 5mn, measure the absorbance at 560m. μ against the blank.
Article Access Ranking
06 Sep. (Last 30 Days)
-
Perspectives on the Promising Pathways to Zero Carbon Emissions in the Steel Industry toward 2050
ISIJ International Vol.65(2025), No.2
-
Growth, Removal, and Agglomeration of Various Type of Oxide Inclusions in Molten Steel
Tetsu-to-Hagané Vol.111(2025), No.11
-
Finite Element Analysis of Bubble Growth and Particle Swelling during Coal Pyrolysis
ISIJ International Vol.65(2025), No.9
-
Interface behavior leading to Al/Cu dissimilar metal bonding formation with high-speed eutectic reaction induced by applying current
QUARTERLY JOURNAL OF THE JAPAN WELDING SOCIETY Vol.43(2025), No.2
-
Corrosion Behavior of Carbon Steel under Soil Drying Conditions
ISIJ International Advance Publication
-
Cold Spot Joining of 980 MPa-class Ultra-high Strength Steel
Tetsu-to-Hagané Advance Publication
-
Combination Effect of Premixing Conditions and Iron Ore Size Distribution in Sintered Ore Granulation Process with Intensive Mixer
ISIJ International Advance Publication
-
A preliminary study on reduction degradation of iron ore sinter using sinter analogue and X-ray micro-computed tomography (MCT)
ISIJ International Advance Publication
-
Copper removal of liquid steel containing 0.25 % carbon using Fe2O3-CaCl2-SiO2 flux
ISIJ International Advance Publication
-
Evaluation of Feature Selection Methods for Oxygen Supply Prediction in BOF Steelmaking
ISIJ International Advance Publication
You can use this feature after you logged into the site.
Please click the button below.