- TOP
- Tetsu-to-Hagané
- Vol. 53 (1967), No. 14
Tetsu-to-Hagané Vol. 53 (1967), No. 14
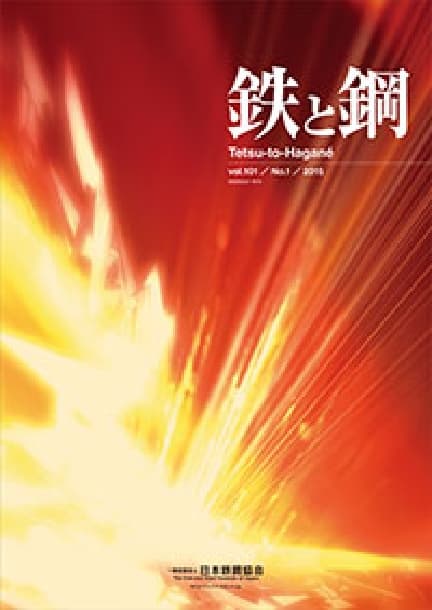
Grid List Abstracts
ONLINE ISSN: | 1883-2954 |
PRINT ISSN: | 0021-1575 |
Publisher: | The Iron and Steel Institute of Japan |
Backnumber
-
Vol. 111 (2025)
-
Vol. 110 (2024)
-
Vol. 109 (2023)
-
Vol. 108 (2022)
-
Vol. 107 (2021)
-
Vol. 106 (2020)
-
Vol. 105 (2019)
-
Vol. 104 (2018)
-
Vol. 103 (2017)
-
Vol. 102 (2016)
-
Vol. 101 (2015)
-
Vol. 100 (2014)
-
Vol. 99 (2013)
-
Vol. 98 (2012)
-
Vol. 97 (2011)
-
Vol. 96 (2010)
-
Vol. 95 (2009)
-
Vol. 94 (2008)
-
Vol. 93 (2007)
-
Vol. 92 (2006)
-
Vol. 91 (2005)
-
Vol. 90 (2004)
-
Vol. 89 (2003)
-
Vol. 88 (2002)
-
Vol. 87 (2001)
-
Vol. 86 (2000)
-
Vol. 85 (1999)
-
Vol. 84 (1998)
-
Vol. 83 (1997)
-
Vol. 82 (1996)
-
Vol. 81 (1995)
-
Vol. 80 (1994)
-
Vol. 79 (1993)
-
Vol. 78 (1992)
-
Vol. 77 (1991)
-
Vol. 76 (1990)
-
Vol. 75 (1989)
-
Vol. 74 (1988)
-
Vol. 73 (1987)
-
Vol. 72 (1986)
-
Vol. 71 (1985)
-
Vol. 70 (1984)
-
Vol. 69 (1983)
-
Vol. 68 (1982)
-
Vol. 67 (1981)
-
Vol. 66 (1980)
-
Vol. 65 (1979)
-
Vol. 64 (1978)
-
Vol. 63 (1977)
-
Vol. 62 (1976)
-
Vol. 61 (1975)
-
Vol. 60 (1974)
-
Vol. 59 (1973)
-
Vol. 58 (1972)
-
Vol. 57 (1971)
-
Vol. 56 (1970)
-
Vol. 55 (1969)
-
Vol. 54 (1968)
-
Vol. 53 (1967)
-
Vol. 52 (1966)
-
Vol. 51 (1965)
-
Vol. 50 (1964)
-
Vol. 49 (1963)
-
Vol. 48 (1962)
-
Vol. 47 (1961)
-
Vol. 46 (1960)
-
Vol. 45 (1959)
-
Vol. 44 (1958)
-
Vol. 43 (1957)
-
Vol. 42 (1956)
-
Vol. 41 (1955)
Keyword Ranking
07 Sep. (Last 30 Days)
Tetsu-to-Hagané Vol. 53 (1967), No. 14
On the Special Slag Bonding Mechanism in the Pellets of Some Sorts of Ores
Minoru SASAKI, Takao NAKAZAWA, Shinichi KONDO
pp. 1553-1560
Abstract
In spite of adding no flux to the raw materials, the pellets of some kinds of ores were beoded with low melting slags by firing under an oxidizing condition. These slag formations were assorted into two cases. As seen in Marcona pellets of both hematite and magnetite ores, one was caused by the reaction between the gangue mineral and ferrous oxide, dissociated from ferric oxide by the promoting effect of MgO in actinolite. The firing temperature changed the volume and fluidity of the liquid slag and brought about the various forms of bonding. At nearly 1150°C the aggregates of the fine gangue and iron oxide particles combined the coarse ones, at 1200°C the liquid slag was formed at the contact points between the coarse gangue and iron oxide particles and combined them firmly, and above 1200°C the liquid phase sintering proceeded predominantly in the pellet.
The other occured typically in the firing of the pellet of Hanaoka pyrite cinder. Up to 1050°C the porous are particles were bonded with hematite. Above 1100°C, however, the molten slag formed from the gangue minerals (as sericite, chlorite etc) combined firmly the iron oxide particles.
In high temperature range the porosity of these pellets were increased by the gases generated in the thermal decompositions of ferric oxide in Marcona pellets and of calcium sulfate in Hanaoka.
On the Role of Fine are Particles in Hematite Bonding of Pellet
Minoru SASAKI, Takao NAKAZAWA, Kaoru ITO, Shinichi KONDO
pp. 1561-1568
Abstract
The pulverized Brazilian hematite are and the ground magnetic concentrates of Swedish and Marcona ores were pelletized and fired under various conditions. By investigating the packing states of the are particles in the dry balls and their behavior in firing processes, the followings were clarified. In the pelletizing of the hematite ore, the very fine particles (under 1-2μ), which coated the coarser ones, contributed a great deal to the increase in the density of the green pellet. In firing, the fine particles combined the coarser ones by forming bridges between them and the bridges grew with firing time resulting in strong pellets. After the size of the bridges exceeded several microns, the strength of the pellet increased rapidly without a remarkable decrease in the porosity.
While, the fine particles in the magnetic concentrates were unable to play the important part in pelletizing by reason of the formation of the magnetic flocks, which were not broken up by grinding. The strength of the pellets, in the first stage of the oxidizing firing, depended on the size and number of the hematite bonds (i. e. the oxidation degree of the magnetite and the content of the fine particles). However, the degree of the grain growth of the hematite came to determine the strength in the latter. The formation of the compact hematite shell, which hindered the permeation of oxygen gas into the pellet, was prevented by oxidizing previously the magnetite more than fifty percent at the lower temperature range.
Kinetic Studies on Deoxidation of Steel
Takoho KAWAWA, Masuta OKUBO
pp. 1569-1585
Abstract
Single- and complex-deoxidations with Mn, Si, and Al are practised in steel baths melted by highfrequency induction furnace and Tammann-oven, respectively. Deoxidation-process are analysed on the stand point of kinetics with an eye to quantitative measurement of the separation-rate of primary inclusion. The results of experiments and evaluation are summarized as follows:
(1) Deoxidation-process in transient time just after the addition of deoxidizers is different from that during the stationary time after the transient time.
(2) In transient time just after the addition of deoxidizers they are in course of reaction with oxygen in iron, and produced inclusions have the tendency to coagulate because of (FeO) or (MnO) in the presence of Mn, in inclusions as a component, whose rapid separation brings about deoxidation of steel.
(3) After the transient time deoxidation-product separates from bath in course of time according to the mathematical form C=Co exp (-kt)(t: time) in the stirred bath.
(4) As the separation-rate coefficients k differ in different kinds of crucibles, rate-determing step of separation of primary inclusion in stirred bath is chemical reaction between crucible materials and deoxidation-products.
(5) Contrary to stirred bath separation-rate of primary inclusion in tranquil steel bath is confirmed to follow the theoretical equation which is introduced for the first time, assuming the validity of Stokes' law.
(6) The above theoretical equation can well explain the separation-rate of inclusion in tranquil steel bath when the mathematical distribution form of inclusion radius, which follows N=A exp (-Ar)(γ: Radius of primary inclusion particles) and bath height are given.
(7) Separation of inclusion in tranquil steel bath as in ladle would be promoted by stirring the steel bath.
Readers Who Read This Article Also Read
Tetsu-to-Hagané Vol.53(1967), No.11
Tetsu-to-Hagané Vol.55(1969), No.7
Tetsu-to-Hagané Vol.51(1965), No.2
Brittle Fracture of Steels for Low Temperature Application
Takeshi KANAZAWA
pp. 1605-1627
Article Access Ranking
07 Sep. (Last 30 Days)
-
Perspectives on the Promising Pathways to Zero Carbon Emissions in the Steel Industry toward 2050
ISIJ International Vol.65(2025), No.2
-
Growth, Removal, and Agglomeration of Various Type of Oxide Inclusions in Molten Steel
Tetsu-to-Hagané Vol.111(2025), No.11
-
Finite Element Analysis of Bubble Growth and Particle Swelling during Coal Pyrolysis
ISIJ International Vol.65(2025), No.9
-
Interface behavior leading to Al/Cu dissimilar metal bonding formation with high-speed eutectic reaction induced by applying current
QUARTERLY JOURNAL OF THE JAPAN WELDING SOCIETY Vol.43(2025), No.2
-
Copper removal of liquid steel containing 0.25 % carbon using Fe2O3-CaCl2-SiO2 flux
ISIJ International Advance Publication
-
Corrosion Behavior of Carbon Steel under Soil Drying Conditions
ISIJ International Advance Publication
-
Cold Spot Joining of 980 MPa-class Ultra-high Strength Steel
Tetsu-to-Hagané Advance Publication
-
Combination Effect of Premixing Conditions and Iron Ore Size Distribution in Sintered Ore Granulation Process with Intensive Mixer
ISIJ International Advance Publication
-
A preliminary study on reduction degradation of iron ore sinter using sinter analogue and X-ray micro-computed tomography (MCT)
ISIJ International Advance Publication
-
Viscosity Measurement of Foam with High Gas Volume Fraction Using Sphere Pull-up and Dam-break Experiments
ISIJ International Advance Publication
You can use this feature after you logged into the site.
Please click the button below.