- TOP
- Tetsu-to-Hagané
- Vol. 72 (1986), No. 6
Tetsu-to-Hagané Vol. 72 (1986), No. 6
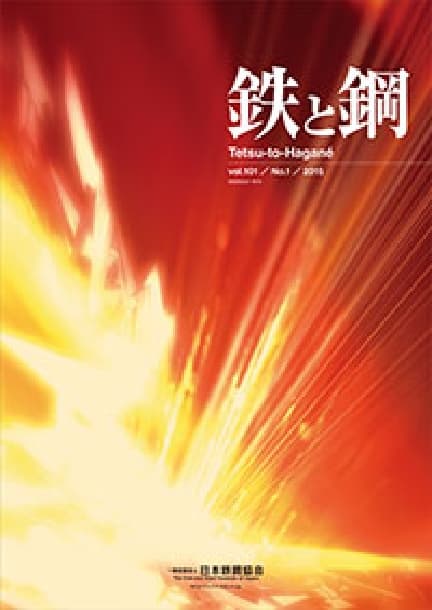
Grid List Abstracts
ONLINE ISSN: | 1883-2954 |
PRINT ISSN: | 0021-1575 |
Publisher: | The Iron and Steel Institute of Japan |
Backnumber
-
Vol. 111 (2025)
-
Vol. 110 (2024)
-
Vol. 109 (2023)
-
Vol. 108 (2022)
-
Vol. 107 (2021)
-
Vol. 106 (2020)
-
Vol. 105 (2019)
-
Vol. 104 (2018)
-
Vol. 103 (2017)
-
Vol. 102 (2016)
-
Vol. 101 (2015)
-
Vol. 100 (2014)
-
Vol. 99 (2013)
-
Vol. 98 (2012)
-
Vol. 97 (2011)
-
Vol. 96 (2010)
-
Vol. 95 (2009)
-
Vol. 94 (2008)
-
Vol. 93 (2007)
-
Vol. 92 (2006)
-
Vol. 91 (2005)
-
Vol. 90 (2004)
-
Vol. 89 (2003)
-
Vol. 88 (2002)
-
Vol. 87 (2001)
-
Vol. 86 (2000)
-
Vol. 85 (1999)
-
Vol. 84 (1998)
-
Vol. 83 (1997)
-
Vol. 82 (1996)
-
Vol. 81 (1995)
-
Vol. 80 (1994)
-
Vol. 79 (1993)
-
Vol. 78 (1992)
-
Vol. 77 (1991)
-
Vol. 76 (1990)
-
Vol. 75 (1989)
-
Vol. 74 (1988)
-
Vol. 73 (1987)
-
Vol. 72 (1986)
-
Vol. 71 (1985)
-
Vol. 70 (1984)
-
Vol. 69 (1983)
-
Vol. 68 (1982)
-
Vol. 67 (1981)
-
Vol. 66 (1980)
-
Vol. 65 (1979)
-
Vol. 64 (1978)
-
Vol. 63 (1977)
-
Vol. 62 (1976)
-
Vol. 61 (1975)
-
Vol. 60 (1974)
-
Vol. 59 (1973)
-
Vol. 58 (1972)
-
Vol. 57 (1971)
-
Vol. 56 (1970)
-
Vol. 55 (1969)
-
Vol. 54 (1968)
-
Vol. 53 (1967)
-
Vol. 52 (1966)
-
Vol. 51 (1965)
-
Vol. 50 (1964)
-
Vol. 49 (1963)
-
Vol. 48 (1962)
-
Vol. 47 (1961)
-
Vol. 46 (1960)
-
Vol. 45 (1959)
-
Vol. 44 (1958)
-
Vol. 43 (1957)
-
Vol. 42 (1956)
-
Vol. 41 (1955)
Keyword Ranking
07 Sep. (Last 30 Days)
Tetsu-to-Hagané Vol. 72 (1986), No. 6
Electronic Structure and Phase Stability of Titanium Alloys
Masahiko MORINAGA, Natsuo YUKAWA, Hirohiko ADACHI
pp. 555-562
Abstract
The alloying effect has been investigated on the electronic structure of both bcc Ti and hcp Ti by the DV-Xα cluster method. The two alloying parameters which are the metal d-orbital level (Md) and the bond order between atoms (Bo), were determined theoretically. The Md is related to the electronegativity and metallic radius of elements. The Bo is a measure of the strength of the covalent bond between titanium and alloying elements. Both the Md and the Bo change remarkably with alloying elements.
A new approach based on the electronic theory has been developed for understanding the phase stability of titanium alloys. With using Md and Bo parameters, titanium binary phase diagrams are interpreted consistently, and various commercial alloys are classified into the three groups of the α, α+β and βalloys. The β transus and the Ms temperature for the martensitic toansformation are predicted from alloy compositions. Furthermore, the activation energy for the impurity diffusion in bcc Ti is estimated in terms of the Bo.
Readers Who Read This Article Also Read
Tetsu-to-Hagané Vol.72(1986), No.6
Martensitic Transformation and Internal Structure of the TiPd and TiPd-Fe Alloys
Kazuyuki ENAMI, Hiroshi SEKI, Soji NENNO
pp. 563-570
Abstract
The crystal structures, internal structure and shape memory effect of the TiPd and TiPd-Fe martensitic alloys were investigated by electron microscopy and tensile testing. The B19(2H) martensite which was found in the earlier X-ray investigation was found to exist in both the TiPd alloy and the TiPd-Fe alloys. The internal structure of this martensite was found to be (111)2H twin. By substituting palladium by iron (the content of titanium is fixed at 54 at%), the Ms temperature decreases with increasing iron content. In the iron added alloys with 4, 5 and 6 at%Fe, a new martensite phase with 9R structure was found to exist in addition to the twinned B19(2H) martensite. In the alloys with 7 and 8 at%Fe, an "intermediate phase" which is very similar to the "incommensurate phase" in TiNi alloys was found to exist. Additional "superlattice" diffraction spots of this phase lie on 0.3n {110} B2 (7at%Fe), and 0.28n {110} B2 (8 at%- Fe), (n: integer). The shape memory effect and pseudoelastic behaviour of the polycrystalline specimens of the 54Ti-39Pd-7Fe and 54Ti-38Pd-8Fe alloys were investigated by tensile testing. Recoverable strain by shape memory effect was about 1% (percentage of recovery 100%) and pseudoelastic strain 3%, in both the alloys.
Readers Who Read This Article Also Read
Tetsu-to-Hagané Vol.72(1986), No.6
Effects of Thermo-mechanical Treatment on the Shape Memory Effect and the Pseudoelasticity of Ti-50.2Ni and Ti-47.5Ni-2.5Fe Alloys
Toshio SABURI, Soji NENNO, Yasunori NISHIMOTO, Makoto ZENIYA
pp. 571-578
Abstract
Effects of thermo-mechanical treatment on the shape memory effect and the pseudoelasticity of a near equiatomic Ti-50.2Ni (at%) and a ternary Ti-47.5Ni-2.5Fe (at%) alloy were investigated by tensile tests for specimens which were cold rolled and subsequently annealed at temperatures between 400°C and 600°C. It has been found that at least 20% of cold working followed by 400°C annealing is necessary for perfect pseudoelasticity to occur in the Ti-50.2Ni (at%) at temperatures above Af. By optical and electron microscope observations, it has been found that a high density of dislocations introduced by cold working and rearranged by annealing below the recrystallization temperature is effective to raise the critical stress for slip deformation and thus to improve the shape memory effect and the pseudoelasticity.
It has been found for the ternary Ti-47.5Ni-2.5Fe (at%) alloy that the thermo-mechanical treatment improves the shape memory effect associated with the R-phase.
Readers Who Read This Article Also Read
Tetsu-to-Hagané Vol.72(1986), No.3
Tetsu-to-Hagané Vol.72(1986), No.6
Tetsu-to-Hagané Vol.72(1986), No.5
Heat Transfer during Melting of Titanium Alloy in Vacuum Arc Furnace by Consumable Electrode
Hiroyuki ICHIHASHI, Akihiro YAMANAKA, Ryoji BABA, Takami IKEDA
pp. 579-586
Abstract
The molten metal pool in vacuum arc melting furnace has much influence on the quality of ingots. Its influence is much more pronounced in melting titanium alloys from the compacted electrode than in other metals. During melting titanium alloy in vacuum arc melting furnace, the shape and temperature profile of molten metal pool and temperature in water-cooled copper mold were measured.
Examining these data results in the following conclusions.
(1) Temperature in arcing area is not affected by melting current and it is about 2 000°C.
(2) Surface temperature of molten metal is estimated at about 2 200°C and the temperature under the surface decreases by approximately 200°C/cm. The temperature distribution in the upper part of molten metal pool is not affected by melting current.
(3) Heat transfer coefficient is 0.04 cal/cm2·s°C at the top of ingot and less than 0.02 cal/cm2·s°C under 30 mm from the ingot top.
(4) Metal pool depth is influenced mainly by melting current. The metal pool shape has been allowed to estimate by analysis of heat transfer with boundary conditions investigated.
Hot Workability of Ti-6Al-4V Alloys
Hirowo G. SUZUKI, Takeo ASHIURA, Koshiro AOYAGI, Hideki FUJII, Kohji TANABE
pp. 587-594
Abstract
Hot workability of Ti-6Al-4V alloys was examined by a hot stage tensile test and hot rolling using a bench scale bar mill. As-cast as well as (α+β) rolled materials were used. Embrittlement occurs between 700 and 950°C in the coarse grain specimens possibly due to the existence of low stress level of β phase along prior β grain boundary. Lateral spread coefficient of this alloy during a pass rolling is larger than Si-Mn steel and shows unique temperature dependence.
Deformation Resistance in Plate Rolling of Commercially Pure Titanium and Ti-6Al-4V Alloy
Sadahiro YAMAMOTO, Chiaki OUCHI
pp. 595-602
Abstract
Hot deformation resistance of commercially pure (C.P.) titanium and Ti-6 Al-4 V alloy was investigated by uni-axial compression and plain strain compression tests. For both titanium plates, mill load and rolling temperatures during hot rolling in a wide plate mill were measured, and mean hot deformation resistance was calculated based on the rolling theory and heat transfer model. Reheating temperatures of C.P.Ti and Ti-6Al-4V alloy were 850°C and 950°C respectively, and the finish-rolling temperature of Ti-6Al-4V alloy was aimed to be reduced below 750°C. The true stress-true strain curve of C.P.Ti was that of dynamic recovery type, which was characterized by work hardening with straining, followed by steady state flow stress. On the other hand, the S-S curve of Ti-6Al-4V alloy exhibited high temperature yielding at a small strain, followed by softening and steady state flow behavior. The mean deformation resistance obtained by plain strain compression testing was higher by 1.5 to 3 times than that from uniaxial compression testing. Hot deformation resistance equations established by analysis of mill load and rolling temperature were well consistent to that from plain strain compression testing in which residual strain was taken into consideration. The residual strain in C.P.Ti and Ti-6Al-4V alloy started to take place at the rolling temperatures of 750°C and 850°C respectively, and hot deformation resistance in both titanium plates markedly increased below these temperatures due to strain accumulation.
Workability and Heat Treatment Characteristics of β Titanium Alloy, Ti-15V-3Cr-3Sn-3Al
Yoshikatsu TSUMORI, Toshio MATSUMOTO, Yuji KOYAMA
pp. 603-609
Abstract
Ti-15V-3Cr-3Sn-3Al alloy sheets 1.6 to 7 mm thick were produced from a 100 kg ingot to study characteristics of manufacturing workability and heat treatability of the alloy.
It was proved that the alloy had higher hot working deformation resistance than Ti-6Al-4V alloy, the most widely used titanium alloy, but was superior in cold rollability and bending workability to Ti-6Al-4V. As the alloy was prone to pick up hydrogen during manufacturing processes, the problem of hydrogen contaminant must be fully considered in the processing.
β phase was completely retained throughout the thickness in the plate as thick as 14mm even by air cooling after solution heating.
The growth rate of β grain was comparatively low in the temperature range of 750 to 900°C tested. After solution treatment and aging, the coarser the β grain was, the lower the ductility became. When aging temperature was lower, precipitated, α phase was finer and strength became higher.
Tensile strength as high as 150 kg/mm2 could be attained by a suitable condition of cold rolling and subsequent aging.
Effect of Degree of Cold Working and Aging Temperatures on Mechanical Properties of Aged Ti-13V-11Cr-3Al Alloy
Makio GUNJI, Kouji KITANO, Naotake NIWA, Kunio ITO
pp. 610-616
Abstract
This study deals with the effects of cold work and aging after solution treatment on the mechanical properties of Ti-13V-11Cr-3Al alloy in order to get better strength ductility relationship through varying the state of alpha phase precipitation. The alloy was cold worked with 30%-90% reduction and aged at temperatures of 600 K-750 K. Specimens were then tensile tested at room temperature and their microstructures and fracture surfaces were observed.
Strength has increased with increasing the degree of cold working, while ductility has decreased. The ductility has, however, also been improved by cold working in the sense that the ductility of more cold worked specimens is superior to that of less cold worked ones, when compared at the same strength level. Lower aging temperatures have yielded better strength and ductility combination than higher ones. The variation in the mechanical properties is explained by the change of alpha phase precipitation from the preferential one on the grain boundaries in the solution treated and aged specimens, to uniform one in the matrix in the cold worked and aged specimens.
Cold work improves the mechanical properties, but it accelerates precipitation of TiCr2 in aging.
The Effect of Heat Treatment on the Mechanical Properties of Ti-10V-2Fe-3Al
Kazuo TOYAMA, Takashi MAEDA
pp. 617-624
Abstract
The effect of heat treatment on strength and fracture toughness of Ti-10V-2Fe-3Al, a near β titanium alloy, was studied. Fatigue properties were also investigated using heat treated specimens specified by Aerospace Material Specifications.
(1) Aging at 490°C for 8 h after solution treatment at 760°C gives the best combination of strength and fracture toughness. However, aging under the same conditions after solution treatment at 785°C decreases ductility. This is considered to have occurred because the treatment at 785°C produces small amounts of primary α phase, which contributes to ductility, than that at 760°C, resulting in a larger amounts of secondary α phase, which contributes to strength.
(2) Agings treatments at 400°C for 8 h and 600°C for 8 h after solution treatment at 760°C cause embrittlement and overaging, respectively. The embrittlement caused by 400°C aging may not come from ω phase but rather from the existence of very fine secondary α particles.
(3) Fracture toughness obtained under as-solution treated condition is lower than that estimated from the relationship between strength and fracture toughness for materials produced with aging after solution treatment. Therefore, an adequate aging is indispensable for obtaining the high strength and high fracture toughness expected from this alloy.
(4) By aging at 490°C for 8 h, a fatigue strength as high as 666 MPa can be obtained. Low cycle fatigue strength is given by the equation;
Δεt=4.589(Nf)-1.24+0.0514(Nf)-0.136
Fatigue crack growth rate is given by the equation
da/dN=3.54×10-9(ΔK)3.62
and ΔKth is 4.4 MPm.
The Effect of Microstructures on Mechanical Properties of the β rich α-β Titanium Alloy Ti-6Al-2Sn-4Zr-6Mo
Yoshimasa ITO, Yasuo MORIGUCHI, Takashi NISHIMURA
pp. 625-632
Abstract
The effect of microstructures in mechanical properties of β rich α-β titanium alloy Ti-6Al-2Sn-4Zr-6Mo was investigated. The β phase formed at the solution temperature above 900°C transformed into the α''(orthorhombic martensite) phase with retained β phase by quenching treatment, but transformed into the acicular α phase with the retained β phase after slow cooling. Solution treatment in the temperature range between 825°C and β transus temperature (952°C) and aging (STA) improved the tensile properties. But STA materials showed the lower fracture toughness than 80 kgf/mm3/2 on account of the presence of the fine acicular α grains between primary α grains. Double solution treatment and aging (STSTA) improved the fracture toughness. The volume fraction of primary a grains was optimized by first solution treatment and second solution treatment controlled the shape of the secondary acicular α grains. The higher fracture toughness in the STSTA materials appeared to be dependent upon the morphology of the secondary acicular α grains. The materials which were double solution treated at 940°C for 1 h oil quenching (OQ) and at 830°C for 2 h air cooling (AC) and aged at 590°C for 6 h AC, possessed the following properties.
Tensile strength : 121 kgf/mm2
Tensile elongation : 14.4%
Fracture toughness : 113 kgf/mm3/2
Toughness and Microstructural Factor of Ti-6Al-4V Alloy
Mitsuo NIINOMI, Toshiro KOBAYASHI, Nobuyuki SASAKI
pp. 633-640
Abstract
Instrumented Charpy impact test, dynamic fracture toughness test and static fracture toughness test by DC electrical potential method were carried out on Ti-6Al-4V alloys with various microstructures to investigate the effect of microstructural factors including fractographic measurements on various toughness criteria, i.e., Charpy absorbed energy (Et: total absorbed energy, Ei: apparent crack initiation energy, Ep: apparent crack propagation energy), dynamic fracture toughness ( Jd), static fracture toughness ( JIC or KQ), static crack propagation resistance curve ( JR curve), and static tearing modulus (Tmat).
Evaluated toughness of Ti-6Al-4V alloy appeared different between Charpy test and dynamic toughness test mainly because the microstructural unit which controls the fracture may be different between these tests. Evaluated toughness by JR curve or Tmat did not necessarily coincide with that by JIC. Thus, it is necessary to use a proper toughness criterion according to the method of design. It was found that microstructure had a more significant role in influencing the Tmat rather than JIC. Further, the relationships between microstructural factors, i.e., areal fraction of primary α, mean free path of primary a, depth of dimples, prior β grain size, and block size, and various toughness criteria mentioned above are clearly defined.
Fatigue Fracture of Ti-5Al-2. 5Sn ELI Alloy at Liquid Helium Temperature
Kotobu NAGAI, Toshio OGATA, Tetsumi YURI, Keisuke ISHIKAWA, Takashi NISHIMURA, Takao MIZOGUCHI, Yoshimasa ITO
pp. 641-648
Abstract
S-N curves of Ti-5Al-2.5Sn ELI alloy were determined at liquid helium temperature (4 K) for both the base and the welded materials.
The base material had longer fatigue life at 4 K than at 77 K. Welding deteriorated the fatigue property at 4 K. Internal crack initiation was seen at the lower cyclic stress for both the base and the welded material. For the base material, the internal initiation occurred only at 4 K and there were no defects near the initiation sites. On the other hand, fatigue cracks generally initiated at blow holes for the weldment. Internal crack initiation is considered one of the causes to scatter or shorten the fatigue life.
High frequency brought about large temperature increase inside the specimen and it made the testing temperature uncertain in fatigue tests at cryogenic temperature.
Stretchability of Commercially Pure Titanium Thin Sheet
Masayoshi OGAYA, Masaru KISAICHI, Seishi ISHIYAMA
pp. 649-656
Abstract
Stretchability of the commercially pure titanium thin sheet which is used for plate type heat exchanger was determined in comparison with the tensile properties.
In stretch forming the strain hardenability in the transverse direction, in which the maximum principal strain is oriented to the transverse direction, is greater than that in the longitudinal direction, while in uniaxial tension the strain hardenability is much smaller in the transverse direction than that in the longitudinal direction. Thus, the stretchability is controlled by the poorer ductility resulting from the smaller strain hardenability in stretch forming in the longitudinal direction.
In the longitudinal direction the strain hardenability increases with increasing grain size in both uniaxial tension and stretch forming. Therefore, the stretchability is improved since the longitudinal ductility in stretch forming increases with increasing grain size.
The behavior of strain hardening is satisfactorily explained by the amount of the twins produced during plastic deformation. Namely, higher density of deformation twin produced in both longitudinal uniaxial tension and stretch forming in the transverse direction results in greater strain hardenability. Moreover, the density of twin produced in both deformation modes increases with increasing grain size in the longitudinal direction.
Calculation Model for r-value of Commercially Pure Titanium Sheet
Osamu AKISUE, Koji KISHIDA
pp. 657-662
Abstract
A calculation model for predicting the plastic strain ratio (r-value) of commercially pure titanium sheet with hcp structure is developed. It is assumed that the sheet deforms only by basal, prism and pyramidal slips and not by twinning at the early stage of tension test. From consideration of the relative values of the critical resolved shear stresses (CRSS) for the three slip planes which are also affected by the interstitial impurity, in this model the CRSS is expressed by the critical Schmid factor of each slip plane. According to this model, the effects of slip planes and interstitial elements on the r-values can be evaluated.
The r-values of three kinds of titanium sheets, which had different amounts of oxygen, were measured and compared with the calculated r-values from this model. The observed and calculated values showed a good agreement.
Effect of Friction Welding Conditions on the Strengths of Joint of Ti-6Al-4V Alloy Bar
Tomio NISHIKAWA, Minoru OKADA
pp. 663-670
Abstract
The friction welding conditions to obtain the good strengths of the joint of Ti-6Al-4V alloy are investigated by evaluating the tensile, bending and Charpy impact properties of them. The friction welding is capable in air under 2 400 rpm of the rotation speed. The strengths are improved to the equivalent strengths to those of mother material when the up-set pressure is increased. In the case of the specimens obtained from the inside of the section of the joint, the up-set pressure to obtain the equivalent property to mother material on Charpy impact value is the highest, and it to obtain that on bending strength is higher than that on tensile strength. In the case of specimens with burr, the up-set pressures to obtain those on tensile and bending strengths are same and higher than those of the specimens without burr, but they are lower than that on Charpy impact property.
Bonding Condition of Rolled Titanium Clad Steels
Seishiro YOSHIWARA, Takao KAWANAMI, Ken'ichi SUZUKI
pp. 671-677
Abstract
Six kinds of rolled titanium clad steels were made by way of trial, and evaluated mechanically and microscopically. Some of these rolled clad steels satisfy the condition which the JIS G 3603 specifies for the exprosively welded clad steels and exprosively welded and rolled clad steels with titanium as cladding metal. These rolled titanium clad steels of high performance are bonded without intermedium and with intermedium of iron foil, nickel foil, SUS 304 wooven wire cloth or SUS 430 wooven wire cloth.
Readers Who Read This Article Also Read
Tetsu-to-Hagané Vol.67(1981), No.1
Tetsu-to-Hagané Vol.71(1985), No.2
Tetsu-to-Hagané Vol.70(1984), No.5
Mechanical Properties of Electron Beam Welded Joint in Solution Treated and Aged Ti-6Al-4V Alloy
Mitsutane FUJITA, Yoshikuni KAWABE, Hirosada IRIE
pp. 678-684
Abstract
The influence of the electron beam welding conditions on the mechanical properties of the welded joint in a solution treated and aged Ti-6Al-4V alloy having a tensile strength of 115 kgf/mm2 has been studied.
The strength of welded joint is equal to that of base metal below the welding heat input of 6 600J/cm. Above this heat input, the strength of the joint is lower than that of base metal, but the strength is not reduced lower than 110 kgf/mm2 in the highest heat input studied. The decrease in the strength of the joint is a result of the decrease of the strength of weld metal, which decreases gradually with the increase in the heat input. As the heat input decreases, the toughness and ductility in weld metal slightly decrease, but the fracture toughness is higher than that of base metal even in the lowest heat input studied. In conclusion, it was found that the solution treated and aged Ti-6Al-4V alloy had the good electron bearm weld-ability.
Improvement of Mechanical Properties of Blended Elemental Ti-6Al-4V Alloy Through Microstructural Modification
Masuo HAGIWARA, Yoshinari KAIEDA, Yoshikuni KAWABE
pp. 685-692
Abstract
Despite the attractiveness of high strength-to-weight ratio of titanium alloys, cost problems limit their use in various industrial applications.
Blended elemental (BE) titanium powder metallurgy, which uses both press and sinter technique and hot isostatic pressing (HIP) for further densification, offers the greatest cost-saving potential, but mechanical properties, particularly fatigue, are inferior to those of prealloyed powder metallurgy and ingot metallurgy materials due to the formation of large alpha-platelet colonies and massive grain boundary alpha phase.
In the present study, an attempt was made to improve mechanical properties of BE Ti-6Al-4V alloy through microstructural modification. The results of investigation show that the beta solution treatment and water quenching, prior to HIP'ing in the alpha + beta region have a strong effect on the structure modification. This new BE method results in relatively small prior beta grains and produces finear and lower aspect ratio alpha plate structure without formation of grain boundary alpha phase. The resultant mechanical properties are markedly improved over those for conventional BE material, and fatigue strength is as good as prealloyed material.
Readers Who Read This Article Also Read
Tetsu-to-Hagané Vol.67(1981), No.1
Tetsu-to-Hagané Vol.71(1985), No.2
Tetsu-to-Hagané Vol.70(1984), No.5
Processing of ASTM Grade 12 Titanium Alloy and Its Mechanical and Corrosion-Resistant Properties
Yoshikatsu TSUMORI, Kenji NARITA, Yuji KOYAMA, Fumio KAMIKUBO
pp. 693-700
Abstract
A 5 t ingot of ASTM G12 titanium alloy (Ti-0.8Ni-0.3Mo) was melted, and the plates, sheets, coils, bars and thin-all seam-welded tubes were manufactured. The processability of G12 alloy has proved almost similar to that of commercially pure titanium grades. It has been clarified that G12 alloy had several advantages in the mechanical property compared with titanium alloys G7 and G3; (1) higher strength at elevated temperatures which leads to higher maximum allowable stress in materials design, (2) larger Young's Modulus and (3) higher fatigue strength. The crevice corrosion tests for G12 alloy as well as G7 and G2 alloys have revealed that G12 alloy was quite superior to G2 and was close to G7 in the resistance to crevice corrosion in hot chloride solutions. It can be expected that the industrial application of G12 alloy will increase owing to its attractive characteristics.
Readers Who Read This Article Also Read
Tetsu-to-Hagané Vol.72(1986), No.6
Performance and Usage of Titanium Materials Resistant to Crevice Corrosion
Fumio KAMIKUBO, Hiroshi SATOH, Kazutoshi SHIMOGORI
pp. 701-707
Abstract
The crevice corrosion in the chloride solutions at elevated temperatures is one of the important corrosion problems in titanium from the practical point of view. At present, Ti-0.15%Pd alloy, Ti-0.3%Mo-0.8 %Ni alloy and PdO/TiO2-Ti (commercially pure titanium coated with a mixture of PdO and TiO2) have been industrially used as countermeasure against the crevice corrosion. In this report, the crevice corrosion resistances of these three materials have been evaluated by means of immersion tests for crevice corrosion and electrochemical tests. The results have revealed that all of three materials showed a far more excellemt resistance than commercially pure titanium, and that Ti-0.15%Pd alloy and PdO/TiO2-Ti were at the almost same level and a little superior to Ti-0.3%Mo-0.8%Ni alloy. Furthermore, a guideline for the effective usage of these materials, which might enable each material to exhibit its maximum advantage, has been proposed on the basis of the obtained corrosion resistance as well as the mechanical property and the service experience.
Article Access Ranking
07 Sep. (Last 30 Days)
-
Perspectives on the Promising Pathways to Zero Carbon Emissions in the Steel Industry toward 2050
ISIJ International Vol.65(2025), No.2
-
Growth, Removal, and Agglomeration of Various Type of Oxide Inclusions in Molten Steel
Tetsu-to-Hagané Vol.111(2025), No.11
-
Finite Element Analysis of Bubble Growth and Particle Swelling during Coal Pyrolysis
ISIJ International Vol.65(2025), No.9
-
Interface behavior leading to Al/Cu dissimilar metal bonding formation with high-speed eutectic reaction induced by applying current
QUARTERLY JOURNAL OF THE JAPAN WELDING SOCIETY Vol.43(2025), No.2
-
Copper removal of liquid steel containing 0.25 % carbon using Fe2O3-CaCl2-SiO2 flux
ISIJ International Advance Publication
-
Corrosion Behavior of Carbon Steel under Soil Drying Conditions
ISIJ International Advance Publication
-
Cold Spot Joining of 980 MPa-class Ultra-high Strength Steel
Tetsu-to-Hagané Advance Publication
-
Combination Effect of Premixing Conditions and Iron Ore Size Distribution in Sintered Ore Granulation Process with Intensive Mixer
ISIJ International Advance Publication
-
A preliminary study on reduction degradation of iron ore sinter using sinter analogue and X-ray micro-computed tomography (MCT)
ISIJ International Advance Publication
-
Viscosity Measurement of Foam with High Gas Volume Fraction Using Sphere Pull-up and Dam-break Experiments
ISIJ International Advance Publication
You can use this feature after you logged into the site.
Please click the button below.