- TOP
- Tetsu-to-Hagané
- Vol. 69 (1983), No. 3
Tetsu-to-Hagané Vol. 69 (1983), No. 3
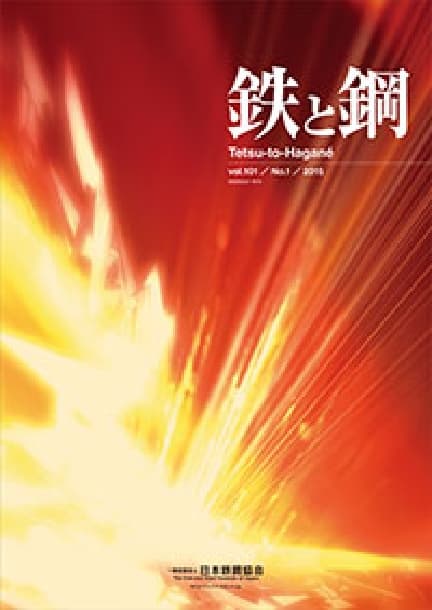
Grid List Abstracts
ONLINE ISSN: | 1883-2954 |
PRINT ISSN: | 0021-1575 |
Publisher: | The Iron and Steel Institute of Japan |
Backnumber
-
Vol. 111 (2025)
-
Vol. 110 (2024)
-
Vol. 109 (2023)
-
Vol. 108 (2022)
-
Vol. 107 (2021)
-
Vol. 106 (2020)
-
Vol. 105 (2019)
-
Vol. 104 (2018)
-
Vol. 103 (2017)
-
Vol. 102 (2016)
-
Vol. 101 (2015)
-
Vol. 100 (2014)
-
Vol. 99 (2013)
-
Vol. 98 (2012)
-
Vol. 97 (2011)
-
Vol. 96 (2010)
-
Vol. 95 (2009)
-
Vol. 94 (2008)
-
Vol. 93 (2007)
-
Vol. 92 (2006)
-
Vol. 91 (2005)
-
Vol. 90 (2004)
-
Vol. 89 (2003)
-
Vol. 88 (2002)
-
Vol. 87 (2001)
-
Vol. 86 (2000)
-
Vol. 85 (1999)
-
Vol. 84 (1998)
-
Vol. 83 (1997)
-
Vol. 82 (1996)
-
Vol. 81 (1995)
-
Vol. 80 (1994)
-
Vol. 79 (1993)
-
Vol. 78 (1992)
-
Vol. 77 (1991)
-
Vol. 76 (1990)
-
Vol. 75 (1989)
-
Vol. 74 (1988)
-
Vol. 73 (1987)
-
Vol. 72 (1986)
-
Vol. 71 (1985)
-
Vol. 70 (1984)
-
Vol. 69 (1983)
-
Vol. 68 (1982)
-
Vol. 67 (1981)
-
Vol. 66 (1980)
-
Vol. 65 (1979)
-
Vol. 64 (1978)
-
Vol. 63 (1977)
-
Vol. 62 (1976)
-
Vol. 61 (1975)
-
Vol. 60 (1974)
-
Vol. 59 (1973)
-
Vol. 58 (1972)
-
Vol. 57 (1971)
-
Vol. 56 (1970)
-
Vol. 55 (1969)
-
Vol. 54 (1968)
-
Vol. 53 (1967)
-
Vol. 52 (1966)
-
Vol. 51 (1965)
-
Vol. 50 (1964)
-
Vol. 49 (1963)
-
Vol. 48 (1962)
-
Vol. 47 (1961)
-
Vol. 46 (1960)
-
Vol. 45 (1959)
-
Vol. 44 (1958)
-
Vol. 43 (1957)
-
Vol. 42 (1956)
-
Vol. 41 (1955)
Keyword Ranking
04 Sep. (Last 30 Days)
Tetsu-to-Hagané Vol. 69 (1983), No. 3
Development of Various Methods of Shape and Crown Control in Strip Rolling
Takao KAWANAMI, Hiromi MATSUMOTO
pp. 348-356
Readers Who Read This Article Also Read
Tetsu-to-Hagané Vol.56(1970), No.11
Tetsu-to-Hagané Vol.89(2003), No.2
Tetsu-to-Hagané Vol.88(2002), No.2
Multi stage Zone-reaction Model with Solid-state Diffusion for the Hydrogen Reduction of Porous Hematite Pellets
Munekazu OHMI, Masaaki NAITO, Tateo USUI
pp. 363-370
Abstract
A mathematical model is presented for describing the hydrogen reduction of porous basic hematitepellets which show extremely low reduction-rate in the final stage at relatively high temperatures.
From the fact that the reduction rate in the final stage depends on the amount and diameter of wüstite particles encircled with dense iron, such slow rate is considered to be controlled by the rate of solid-state diffusion of oxygen through the recrystallizing iron layer. To take into account the solid-state diffusion, the multi-stage zone-reaction model presented previously is partly modified, i.e., cross section of a pellet is devided into the following four reaction zones: hematite-magnetite, magnetite-wüstite, wüstite-iron layer in which wüstite particles are dotted with iron nuclei, and the other wüstite-iron layer composed of wüstite particles encircled with dense iron. In the former three layers, chemical reaction and gaseous diffusion proceed simultaneously. In the last layer, the reduction rate of wüstite particles is controlled by the rate of solid-state diffusion mentioned above.
The calculated results agree well with experimental data up to the final stage of reduction.
The values of oxygen permeability through iron layer show good agreement with those reported previously.
Gases in Blast Furnace Slags
Tasuku FUWA, Shiro BAN-YA, Yasutaka IGUCHI, Fujio ISHII
pp. 371-377
Abstract
The contents of gases dissolved in blast furnace slags, such as hydrogen (water), nitrogen and carbon, have been studied for the samples taken systematically from several blast furnaces in operation. Vacuum fusion method was applied to determine total gases, and the aluminum reduction-vacuum fusion method for hydrogen, Kjeldahl method for nitrogen and the combustion method for carbon were applied, respectively.
(1) Hydrogen contents in blast furnace slags are about 10 ppm independently of the furnace operation, but hydrogen in slags increases rapidly by the contact with water vapor or water after slag-off.
(2) Nitrogen and carbon contents in slags increase with increasing silicon contents in hot metal.
(3) Nitrogen and carbon contents in slags with hot metal for steelmaking are 200300 ppm, but nitrogen and carbon contents in the slags with hot metal for foundry are determined as 8001000 ppm and 9001100 ppm respectively.
(4) Nitrogen and carbon dissolved in slags in blast furnaces are reduced by forming N2, H2 and CO through the reaction with water dissolved in slags in the step after slag-off. This formation of N2, H2 and CO from slags results in the pores in solidified slags.
Readers Who Read This Article Also Read
ISIJ International Vol.53(2013), No.3
ISIJ International Vol.43(2003), No.1
Activities of Iron Oxides in the Na2O-Na2CO3-SiO2-FeO-FeO1.5 System
Nobuo SANO
pp. 378-383
Abstract
The activities of FeO and FeO1.5 in the Na2O-Na2CO3-SiO2-FeO-FeO1.5 system in contact with solid iron were measured, equilibrating with CO-CO2 gas mixtures. The isoactivity contours of FeO were shown to be similar to those in the CaO-SiO2-FeO system, having the noses approximately at the line joining the compositions of FeO and 0.4Na2O-0.6SiO2. The addition of P2O5 to this system enhances the activities of both iron oxides. The activity of FeO1.5 was observed to have a maximum at the same composition as the basicity varies.
These results were interpreted qualitatively by the regular solution model for FeO and the amphoteric property for FeO1.5.
The result indicates that the significantly low oxygen potential prevailing at the metal-slag interface rather than the possibly singular thermodynamic property of FeO in this system accounts for the relatively small oxidation loss of iron on the soda ash treatment of hot metals for simultaneous removal of sulphur and phosphorus.
主要資源の対外依存度と各国の世界輸入に対するシェア(1980年)/東欧での雑感/21世紀にかけての人口と資源の見通し/製管の歴史(7)-リン酸塩被膜潤滑法の発展-
佐野 信雄, 加藤 健三
pp. 383-383,391
Reducing Rate of Iron Oxide in Molten Slag by Carbon in Iron Melt
Akira SATO, Goro ARAGANE, Fumio HIROSE, Ryuichi NAKAGAWA, Shiro YOSHIMATSU
pp. 384-391
Abstract
In the research of a continuous ironmaking process from a reduced iron, or a pre-reduced iron ore, the reducing rate of iron oxide in molten slag by carbon in iron melt was investigated to know the optimum reducing condition. Mixture consisted of, mainly, 40 g master slag and 17.1 g iron oxide was added onto the iron melt in a graphite crucible, the copper melt in a graphite crucible, or the iron melt in an alumina crudible to measure the amount of CO gas evolved at 13201620°C. The following results were obtained;
(1) The reducing rate of iron oxide in molten slag was proportional to the second power of iron oxide content in molten slag except for the starting and the ending period of experiment.
(2) The rate constant and the apparent activation energy of the reduction of iron oxide in molten slag by carbon in iron melt were obtained from data of experiment with a graphite crucible-iron melt and a graphite crucible-copper melt.
(3) The rate constant of reduction of iron oxide in molten slag by the carbon in iron melt, or a solid graphite was greatest at CaO/SiO2=1.5 of molten slag.
Fundamental Study of the Penetration and Dispersion of Powder and the Mixing Characteristics in Powder Injection Refining
Kiichi NARITA, Takehisa MAKINO, Hiroshi MATSUMOTO, Kanehiro OGAWA
pp. 392-400
Abstract
Behaviours of injected powder and characteristics of mixing in the powder injection refining have been investigated by water model experiments. The results obtained are as follows.
(1) The critical velocity of a particle for the penetration into liquid could be expressed by Engh's equation.
(2) The penetration distance of a particle is given by the parameter which is the ratio of the kinetic energy of a particle to the turbulent shearing force.
(3) The behaviour of floatation or sedimentation is decided by the parameter which is the ratio of the buoyancy force of a particle to the turbulent shearing force.
(4) Time for dispersion of particles is a function of stirring power and liquid volume, and is about a twentieth of mixing time.
(5) The formula for mixing time is affected by the method of tracer addition and the method of stirring. Mixing time is expressed as a function of stirring power for the tracer injection and as a function of both stirring power and liquid volume for the gas bubbling with tracer addition onto the liquid surface.
Smelting Reduction for the Direct Production of Stainless Steels by Using a Plasma Arc Furnace
Kyojiro KANEKO, Nobuo SANO
pp. 401-406
Abstract
Smelting reduction of chromium are with coke by using a plasma jet furnace was investigated to produce 18%-Cr steels.
The operation of the plasma furnace was controllable and stable for the reduction of chromium ore. Chromium ores were successfully reduced to produce 18%-Cr steels (1.03.0%C, 0.0140.019%P, 0.050.09%S) with 9295% of chromium yield where the excess iron was supplied as steel scrap.
The thermal energy released from the transfer-type plasma jet was effectively transferred to reactants and significantly enhanced the chemical reaction rate. It was observed that sulfur in are and coke were substantially removed to gas phase with the proportion of 4050% out of the total input, presumably because CO gas evolving on the reduction carried away sulfur bearing gases from the system.
Critical Oxygen Concentration for the Ceasing of CO Macroblowhole Growth during Solidification of Iron
Masashi HASHIURA, Hiroyuki NOMURA, Yasuji FUKUI, Kazumi MORI
pp. 407-411
Abstract
The iron containing about 0.1% C was solidified unidirectionally to obtain the basic information on the ceasing of growth of CO macroblowholes. Experiments were done for the two solidification rates of 5 and 10 mm/min. Blowhole growth was examined by X-ray radiography.
The critical oxygen concentration for the ceasing of blowhole growth at the solidification rate of 5 and 10 mm/min were 0.00280.0045% (C 0.100.11%) and 0.00340.0050% (C 0.110.12%), respeclively. These critical concentrations agree with those obtained from the calculation on the basis of the model of steady growth of cylindrical blowholes.
Readers Who Read This Article Also Read
Tetsu-to-Hagané Vol.67(1981), No.1
Tetsu-to-Hagané Vol.71(1985), No.2
Tetsu-to-Hagané Vol.70(1984), No.7
Analysis of Residual Stress in Rolled H-beam
Hiroshi YOSHIDA, Tooru SASAKI, Nobuyuki KONDO, Tommo TANAKA, Takafumi HASHIMOTO
pp. 412-419
Abstract
To analyze residual stress in rolled H-beams, a numerical method for the prediction of temperature and thermal stress has been developed by taking phase transformation into account. Temperature during cooling and residual stress calculated by the present method agree well with the measured ones.
The infulence of finishing temperature and sectional size on residual stress is investigated by using the method. The results obtained are as follows;
(1) The larger the thickness ratio of flange to web (tf/tw) is, the higher the stress is.
(2) The larger the difference in finishing temperature between web and flange (Tfo-Two) is, the higher the stress is.
(3) The larger the ratio of sectional area of flange to web (Sf/Sw) is, the lower the tensile stress in flange is and the larger the compressive in web is.
(4) The smaller the amount of non-transformed phase (austenitc amount) in web is and the larger the amount in flange is at finishing rolling, the higher the stress is.
(5) The larger the compressive stress in web is and the larger the ratio of inner width to thickness in web (Bw/tw) is, the more frequently the web buckling occurs.
Effect of Stress Ratio on Fatigue Crack Growth Rate of 100kgf/mm2 Grade High Yield Strength Steels in Sea Water
Masae SUMITA, Norio MARUYAMA, Iku UCHIYAMA
pp. 420-427
Abstract
The effect of sea water on fatigue crack growth rate of three kinds of 100 kgf/mm2 grade high yield strength steels has been investigated using a parameter γ0.167Hz(≡(da/dN)cor/(da/dN)air), where (da/dN)cor is a fatigue crack growth rate in sea water at the frequency of 0.167 Hz, and (da/dN)air is fatigue crack growth rate in air. Stress ratios of 0.10, 0.50, 0.70, and 0.90 have been used. The results are as follows;
1) In 104 steel, the relationship between the value of γ0.167Hz and ΔK are almost the same at the R-values of 0.10, 0.50, and 0.70. The same trend is also observed in 127 steel. The maximum values of γ0.167Hz of two steels are about 2 and 4, which arise at the ΔK-values of 70 and 48 kgf/mm3/2 respectively. regardless of R within 0.10 to 0.70. The fracture surface shows a transgranular fracture mode with corrosion pits.
2) The degree of the effect of sea water on da/dN, therefore, are controlled by ΔK in 104 and 127 steels.
3) In 123 steel, the maximum value of γ0.167Hz is 5.5 to 7.5 regardless of R. The value of ΔK and Kmax to the maximum value of γ0.167Hz decreases and increases respectively with increase of R-value. The degree of the effect of sea water on da/dN is controlled by ΔK and Kmax. The fracture surface shows intergranular fracture mode due to hidrogen.
4) A lot of secondary cracks (branching) exists in 123 steel, which appear when the plastic deformation size at the crack tip is larger than the prior austenitic grain size. Branching of cracks gives no influences on the fatigue crack growth rates.
5) Dynamic Kscc is controlled by ΔK regardless of fracture mode.
Readers Who Read This Article Also Read
Tetsu-to-Hagané Vol.67(1981), No.1
Tetsu-to-Hagané Vol.71(1985), No.2
Tetsu-to-Hagané Vol.70(1984), No.7
Behaviour of Fatigue Crack Growth of High Yield Strength Steels in Various Kinds of Water Environments
Masae SUMITA, Norio MARUYAMA, Iku UCHIYAMA
pp. 428-436
Abstract
A parameter γ0.167Hz which means the degree of the effect of water environment on fatigue crack growth rate has been evaluated using six kinds of 80120 kgf/mm2 grade steels at the stress ratio of 0.10. γ0.167Hz≡(dadN)cor/(da/dN)air, where (da/dN)cor is fatigue crack growth rate in each water environments at the frequency of 0.167 Hz and 30°C, and (da/dN)air is that in air. Air-bubbling sea water, N2 gas-bubbling pure water, air-bubbling pure water, air-bubbling 3% NaCl solution, and air bubbling 3%, , NaCl solution with zinc sacrificial anode have been used as environments. The following results are mainly obtained.
1) When the maximum value of γ0.167Hz is less than 34 fracture surface almost shows transgramtlar. When the value is more than 34 fracture surface shows intergranular.
2) The maximum value of γ0.167Hz less than about 2 is not obtained for six kinds of high yield strength steels used and under the above five water environments.
3) Under the zinc sacrificial anode condition, the effect of corrosion control against fatigue crack growth is observed when ΔK<3040 kgf/mm3/2.
However, the value of γ0.167Hz is higher under the condition than under another water environments when ΔK> 3040 kgf/mm3/2. This fact can be explained by hydrogen arised due to cathodic reaction.
4) Under the zinc sacrificial anode condition, the maximum value of γ0.167Hz are 513 depending on prior austenitic grain sizes, which is explained by relating to cyclic plastic deformation size at the tip of crack.
Tensile Properties of Fe-Ni-Al Maraging Steels
Ko SOENO, Masatoshi TSUCHIYA, Kazuo TAGUCHI
pp. 437-442
Abstract
Tensile properties and resistivity changes during isothermal aging have been investigated on Fe-Ni-Al maraging steels with and without about 0.4% molybdenum. Nickel content was varied from 10 to 17.5%, and aluminum contents were about 1.5 and 2.5%.
Cellular precipitation was found to be completely suppressed by the addition of 0.4% molybdenum. When cellular precipitation progressed, strength decreased with the increase in ductility (reduction of area). Ductility tended to increase by the rise in aging temperature, or by lengthening aging time. However, it was found that the increase in ductility became difficult with the increase in aluminum content or with the decrease in nickel content. The lack in ductility was considered to be connected with the difficulty to cross-slip.
Wear Resistance of Borided Drawing Dies
Yoshio SHIBUYA
pp. 443-451
Abstract
Tool steel dies were borided and heat treated. As the drawing materials with borided and unborided dies, aluminium wires of A2011 B, A 1070W and A5356 were used. The drawing characteristics (dimensional change of die and wire, coefficient of friction between wire and die) of the borided and unborided dies were compared. When the A2011B was drawn with borided and unborided dies, roughness, roundness of die and drawn A2011B surfaces with borided die were remarkably better than that of unborided die. The coefficient of friction between wire and die for drawn A2011B and A5356 with the borided die was less than that with unborided die. The boride layer did not show significant improvement for the severe adhesion between wire and die. Accordingly, it is noted that the borided die is useful under the condition of light adhesion occurring between wire and die.
Effects of Al and N on Hardenability and Transformation Characteristics of Low Alloy Case Hardening Steels
Masatsune YOSHIMURA, Hiromasa KOBAYASHI, Tatsuo FUKUZUMI
pp. 452-461
Abstract
The influences of Al and N on the hardenability and the transformation characteristics have been investigated for low alloy case hardening steels (JIS SCM420). Since the contents of Al and N in austenite in solution vary with the Al+N_??_AlN reaction, the amounts of Alγ and Nγ (concentration of Al and N existing as solutes in austenite, respectively) are calculated from solubility product of AlN in austenite given by the following equation:
log[Alγ]·[Nγ]=-6700/T(K)+1.528
It is revealed that these two elements have potent influence on hardenability, and that the multiplying factor of Al is quite large and is about 1.8 around 400 ppm of Alγ. In high Alγ steels, the γ→α proeutectoid ferrite reaction is retarded through the increase in the incubation period of nucleation and through the decrease in the nucleation rate of ferrite and in the diffusion coefficient of C in austenite.
Embrittlement of 5.5% Ni Steels on Slow Cooling from the Final Tempering
Kotobu NAGAI, Koji SHIBATA, Masato MURAKAMI, Toshio FUJITA
pp. 462-469
Abstract
The embrittlement on slow cooling was studied in the intercritically heat treated cryogenic nickel steels which contain reverted austenites. The 5.5% Ni steels with different Mo and Cr contents were QLT treated and reheated at 600°C for 20 min and then slow cooled at a rate of about 0.2 K/min to the temperatures at which the slow cooling was interrupted by water quenching.
Three types of embrittlement took place on slow cooling, depending on chemical compositions and interrupted temperatures. Intergranular failure was a characteristic feature of the embrittlement in Mo free and 0.4 Mo steels and this was attributable to temper embrittlement. In the cases of 0.2 and 0.8 Mo steels, no intergranular fracture was observed and quasi-cleavage fracture became more dominant with a decrease in the intermediate-quenching temperature. As the cooling proceeded the yield strength decreased or remained in a low level at first and increased gradually and reached a constant level. This may be concerned with the change in the stability of reverted austenite on slow cooling. For 0.6Cr-0.4 and 0.8Mo steels, martensitic transformation of the unstable austenite appeared to occur at low tensile stress level and decrease both yield strength and toughness.
Role of Internal Stress for the Initial Yielding of Ferrite-Martensite Dual Phase Steels
Tsuneaki SAKAKI, Kohichi SUGIMOTO, Toshiro FUKUZATO
pp. 470-479
Abstract
Role of internal stress for the initial yielding and for the masking of Lüders band is discussed as follows:
1) The martensite transformation causes transformation-induced yielding in the ferrite phase. The resultant distribution of the plastic strain in the ferrite surrounding the martensite islands and the distribution of the internal stress in the ferrite and martensite phases are calculated based on the continuum mechanics.
2) There are preferentially yielding zones around each martensite island and initial yielding begins in these zones under very low applied stress compared to the yield strength of the ferrite because the internal stress assists the initial yielding.
3) There are a number of preferentially yielding zones in the dual phase steels, therefore, LUders band is masked as in the case of temper-rolled rimmed steel sheets.
Dephosphorization of Solid High-carbon Ferromanganese by NaOH-NaCl
Kyojiro KANEKO, Nobuo SANO
pp. 480-482
Abstract
Solid ferromanganese particles ranging from 0.59 to 2.38 mm in diameter were dephosphorized using NaOH-NaCl melts at temperatures of 900 to 1000°C. Thermodynamically, the oxidation of phosphorus from ferromanganese without oxidation loss of manganese is very difficult, and hence sodium hydroxide was chosen from the consideration that sodium has strong tendency to form the phosphate. The dephosphorization of 60 to 70% was attained at best with lOg of ferromanganese and 1 gNaOH-2gNaCl mixture at 950°C by 2 hours treatment. Dephosphorization did ont proceed when sodium chloride was not added to sodium hydroxide, in which case only manganese was oxidized.
抄録
高田 至康, 菅原 健, 虎岩 清, 望月 俊男, 升田 博之, 村川 恵美
pp. 503-505
Readers Who Read This Article Also Read
Tetsu-to-Hagané Vol.69(1983), No.1
Article Access Ranking
04 Sep. (Last 30 Days)
-
Perspectives on the Promising Pathways to Zero Carbon Emissions in the Steel Industry toward 2050
ISIJ International Vol.65(2025), No.2
-
Growth, Removal, and Agglomeration of Various Type of Oxide Inclusions in Molten Steel
Tetsu-to-Hagané Vol.111(2025), No.11
-
Finite Element Analysis of Bubble Growth and Particle Swelling during Coal Pyrolysis
ISIJ International Vol.65(2025), No.9
-
Interface behavior leading to Al/Cu dissimilar metal bonding formation with high-speed eutectic reaction induced by applying current
QUARTERLY JOURNAL OF THE JAPAN WELDING SOCIETY Vol.43(2025), No.2
-
Corrosion Behavior of Carbon Steel under Soil Drying Conditions
ISIJ International Advance Publication
-
Cold Spot Joining of 980 MPa-class Ultra-high Strength Steel
Tetsu-to-Hagané Advance Publication
-
Combination Effect of Premixing Conditions and Iron Ore Size Distribution in Sintered Ore Granulation Process with Intensive Mixer
ISIJ International Advance Publication
-
A preliminary study on reduction degradation of iron ore sinter using sinter analogue and X-ray micro-computed tomography (MCT)
ISIJ International Advance Publication
-
Copper removal of liquid steel containing 0.25 % carbon using Fe2O3-CaCl2-SiO2 flux
ISIJ International Advance Publication
-
Evaluation of Feature Selection Methods for Oxygen Supply Prediction in BOF Steelmaking
ISIJ International Advance Publication
You can use this feature after you logged into the site.
Please click the button below.