- TOP
- Tetsu-to-Hagané
- Vol. 76 (1990), No. 5
Tetsu-to-Hagané Vol. 76 (1990), No. 5
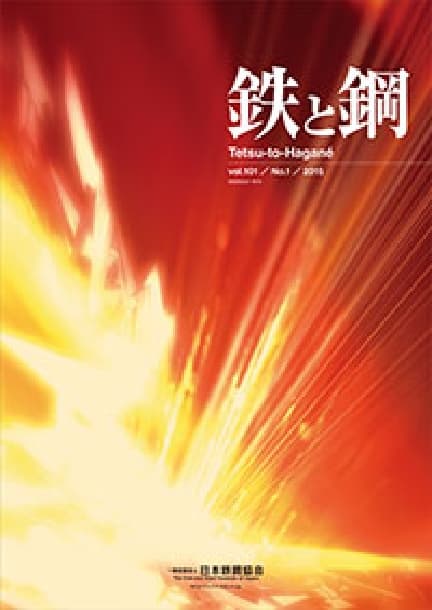
Grid List Abstracts
ONLINE ISSN: | 1883-2954 |
PRINT ISSN: | 0021-1575 |
Publisher: | The Iron and Steel Institute of Japan |
Backnumber
-
Vol. 111 (2025)
-
Vol. 110 (2024)
-
Vol. 109 (2023)
-
Vol. 108 (2022)
-
Vol. 107 (2021)
-
Vol. 106 (2020)
-
Vol. 105 (2019)
-
Vol. 104 (2018)
-
Vol. 103 (2017)
-
Vol. 102 (2016)
-
Vol. 101 (2015)
-
Vol. 100 (2014)
-
Vol. 99 (2013)
-
Vol. 98 (2012)
-
Vol. 97 (2011)
-
Vol. 96 (2010)
-
Vol. 95 (2009)
-
Vol. 94 (2008)
-
Vol. 93 (2007)
-
Vol. 92 (2006)
-
Vol. 91 (2005)
-
Vol. 90 (2004)
-
Vol. 89 (2003)
-
Vol. 88 (2002)
-
Vol. 87 (2001)
-
Vol. 86 (2000)
-
Vol. 85 (1999)
-
Vol. 84 (1998)
-
Vol. 83 (1997)
-
Vol. 82 (1996)
-
Vol. 81 (1995)
-
Vol. 80 (1994)
-
Vol. 79 (1993)
-
Vol. 78 (1992)
-
Vol. 77 (1991)
-
Vol. 76 (1990)
-
Vol. 75 (1989)
-
Vol. 74 (1988)
-
Vol. 73 (1987)
-
Vol. 72 (1986)
-
Vol. 71 (1985)
-
Vol. 70 (1984)
-
Vol. 69 (1983)
-
Vol. 68 (1982)
-
Vol. 67 (1981)
-
Vol. 66 (1980)
-
Vol. 65 (1979)
-
Vol. 64 (1978)
-
Vol. 63 (1977)
-
Vol. 62 (1976)
-
Vol. 61 (1975)
-
Vol. 60 (1974)
-
Vol. 59 (1973)
-
Vol. 58 (1972)
-
Vol. 57 (1971)
-
Vol. 56 (1970)
-
Vol. 55 (1969)
-
Vol. 54 (1968)
-
Vol. 53 (1967)
-
Vol. 52 (1966)
-
Vol. 51 (1965)
-
Vol. 50 (1964)
-
Vol. 49 (1963)
-
Vol. 48 (1962)
-
Vol. 47 (1961)
-
Vol. 46 (1960)
-
Vol. 45 (1959)
-
Vol. 44 (1958)
-
Vol. 43 (1957)
-
Vol. 42 (1956)
-
Vol. 41 (1955)
Keyword Ranking
30 Aug. (Last 30 Days)
Tetsu-to-Hagané Vol. 76 (1990), No. 5
Recent Contributions of Work and Tool Materials for Cold Forged Products
Hiromu SAWABE
pp. 649-659
Readers Who Read This Article Also Read
Tetsu-to-Hagané Vol.73(1987), No.2
Tetsu-to-Hagané Vol.76(1990), No.7
Tetsu-to-Hagané Vol.76(1990), No.4
Progress of Metal Powder Injection Molding
Hideki NAKAMURA
pp. 660-666
Readers Who Read This Article Also Read
Tetsu-to-Hagané Vol.76(1990), No.1
Tetsu-to-Hagané Vol.76(1990), No.2
Tetsu-to-Hagané Vol.76(1990), No.4
High Productivity Operation at Chiba No.4 Sinter Plant
Hiroshi OBATA, Hiroyasu TAKAHASHI, Masaru NAKAMURA, Toshihiko NATSUMI, Kiyoshi KOMAMURA
pp. 667-674
Abstract
To meet the demand for production increase, high productivity operation has been carried out based on the following targets at Chiba No. 4 Sinter Plant :
(1)Maintenance of high bed height operation by ensuring and stabilizing permeability of sinter bed.
(2) Achievement of high productivity and sinter production cost saving through improvement of sinter yield.
(3)Maintenance of low SiO2 operation under high productivity operation.
From application of coutermeasures for targets above mentioned, the following results were obtained :
(1)A high productivity operation of 1.8 t/hm2 without adding any binder was obtained.
(2)The total amount of return fine has been decreased from 400450 kg/t-s to 260300 kg/t-s.
(3) Sinter production cost has been decreased and cost minimum point has shifted to high productivity side.
Readers Who Read This Article Also Read
Tetsu-to-Hagané Vol.76(1990), No.1
Tetsu-to-Hagané Vol.76(1990), No.2
Tetsu-to-Hagané Vol.76(1990), No.4
Estimation of Deterioration of Coke Strength by CO2 Reaction
Tetsu NISHI, Hiroshi HARAGUCHI, Toshiaki OKUHARA
pp. 675-682
Abstract
The deterioration of coke in the blast furnace has been evaluated as the change in coke size due to reaction between coke and CO2 gas. To clarify the deterioration mechanism, a series of experiment has been carried out at each reaction temperature by using an apparatus for high temperature CO2 reaction.
The main results obtaind are as follows.
1) Based on the findings mentioned above, a model was developed for estimating the deterioration of coke strength by CO2 reaction.
2) The model contained the influence of alkali in coke on deterioration of coke strength in the blast furnace.
3) The deterioration of coke strength estimated by the model closely agreed with that measured at different reaction temperatures by using an apparatus for high temperature CO2 reaction.
4) The influences of coke properties, operation condition in the blast furnace and alkali in coke on the deterioration of coke strength were discussed by using this model.
Readers Who Read This Article Also Read
Tetsu-to-Hagané Vol.76(1990), No.1
Tetsu-to-Hagané Vol.76(1990), No.2
Tetsu-to-Hagané Vol.76(1990), No.4
Properties of Sinter Produced from Mini-Pellets Consisting of Coarse Iron Ore Particles and Adhering Fine Mixtures Having Quaternaly Calcium Ferrite Composition
Takaho OTOMO, Noboru TAGUCHI, Eiki KASAI, Yasuo OMORI
pp. 683-690
Abstract
A wide range of sintering experiments were carried out in order to use a large quantity of fine iron ore for the sintering process and to improve the properties of product sinter. Modeled mini-pellets (named duplex pellets) which consisted of coarse iron ore particles as cores and fine mixture, of which chemical composition was specified to a quaternary (CaO-SiO2-Al2O3-Fe2O3) calcium ferrite, as shell layer were used in the present experiments.
The effect of ratio of shell in pellet and of iron ore characteristics on the sintering process and metallurgical properties of the product sinter were examined. The results obtained are as follows ;
1)The maximum bed temperature decreased with increasing ratio of shell in pellet from 50 to 80 mass%, however, the permeability of the sintering bed was not significantly affected.
2)Reduction degradation property of product sinter was able to be improved with increasing ratio of shell in pellet as the strength and reducibility of product sinter were kept in high values. These were due to both that the matrix was changed from glassy silicate to acicular calcium ferrite and that the amount of matrix was increased.
3) When the ratio of shell in pellet was 80 mass%, reduction degradation property of product sinter was improved by the use of fine iron ore with good reactivity with limestone, although strength and reducibility of product sinter were not significantly affected.
Readers Who Read This Article Also Read
Tetsu-to-Hagané Vol.76(1990), No.6
Tetsu-to-Hagané Vol.76(1990), No.9
Tetsu-to-Hagané Vol.76(1990), No.2
Effect of Pulverized Coal Injection on the Distribution of Pressure, Temperature and Fine Particle Fraction around Blast Furnace Raceway
Mikio DEGUCHI, Kouichirou SHIBATA, Masayoshi FUKUOKA
pp. 691-698
Abstract
Pulverized Coal Injection (PCI) tests were carried out by using a coke-filled test furnace to clear the combustion behaviour of Pulverized Coal (PC) in a blast furnace and its effects on the furnace phenomena.
Effects of Pulverized Coal Injection Rate (PCR) and charged sinter on pressure drop, temperature and fine particle fraction distribution in the test furnace were studied. On the basis of these experimental results, carbon solution loss reaction rates of unburnt PC and fine coke was measured with "in-situ" analysis of high temperature gas. The results obtained are as follows.
(1) Increase in blast pressure with PCI is much dependent on the increase in blast velocity by PC combustion in the blow pipe.
(2) As unburnt PC accumulated in the furnace is gasified with CO2 much faster than fine coke, it has no harmful influence on the pressure drop in the furnace.
(3)As descending velocity of solid at the peripheral part in blast furnace bosh decreases with increase in PCR, furnace heat loss increases.
Readers Who Read This Article Also Read
Tetsu-to-Hagané Vol.76(1990), No.4
Tetsu-to-Hagané Vol.74(1988), No.6
Tetsu-to-Hagané Vol.76(1990), No.9
The Flow Field in Air-Water Vertical Bubbling Jets in a Cylindrical Vessel
Manabu IGUCHI, Hiroaki TAKEUCHI, Zen-ichiro MORITA
pp. 699-706
Abstract
Bubble frequency and gas holdup in bubbling jets were measured by means of an electro-resistivity probe. The axial, radial and tangential velocity and fluctuation components of water were measured with a Laser Doppler Velocimeter. On the basis of these results, air-water vertical bubbling jet in a cylindrical vessel was classified into four regions, i.e., the momentum, transition, buoyancy, and surface regions from the nozzle exit toward the bath surface. The profiles of gas holdup, axial velocity and root mean square value of axial velocity fluctuation in each region were discussed in detail. Also, the flow rate, momentum and kinetic energy of rising water were determined, being necessary for refining previous theoretical models predicting the fluid flow behavior induced by bubbles.
Readers Who Read This Article Also Read
Tetsu-to-Hagané Vol.88(2002), No.5
Tetsu-to-Hagané Vol.95(2009), No.6
Tetsu-to-Hagané Vol.73(1987), No.5
Development of Melt Treatment Process for Obtaining High Undercooling for a Low Carbon Steel
Tadayoshi TAKAHASHI, Jun-ichi TANAKA, Masayuki KUDOH, Ken-ichi OHSASA
pp. 707-713
Abstract
High undercooling up to 98 K has been obtained by a cycle of melting and freezing. A specimen of 0.23 wt% carbon steel weighing 1.5 kg was melted in a fused alumina crucible set in a tammann furnace and it was kept at 1 893 K. Then, the granular mish metal (REM) of 18 g, which corresponds to the quantity of 1.2 wt% to the weight of the melt, was intermittently injected into the melt with Ar gas through a mulite tube which had been immersed into the melt, followed by cooling to 1 853 K. In order to promote the reaction among molten metal, mulite tube and REM, the molten metal was intermittently stirred while being kept at that temperature and then cooled in the furnace.
The Effects of Carbon Content and Cooling Rate on the Development of Columnar Austenitic Grains in As-cast Steel
Kiyotaka MATSUURA, Youichi ITOH, Kaichi MATSUBARA
pp. 714-721
Abstract
Steels containing 0.01 to 0.49 mass% carbon were melted and then cooled at rates of 0.3 to 40°C/s to investigate the condition favorable for the formation of columnar austenitic grains.
The results were summarized as folllows.
1) Large columnar grains were most remarkably developed in 0.1-0.3 mass%C region.
2) The region of the carbon content favorable for the development of columnar grains extended with increasing coiling rate.
The computer simulation of the cooling process of the ingots was carried out to investigate the formation mechanism of the coulmnar grains. From the experiment and the simulation, it was concluded that the formation of columnar austenitic grains was attributable to the steep temperature gradient at the δ→γtransformation front.
Segregation of Cr and Ni in the Initial Solidification Layer of Steel Ingots
Hideo MIZUKAMI, Yutaka NAGAKURA, Susumu IZUMI, Takaji KUSAKAWA
pp. 722-727
Abstract
18-8 stainless steel ingots were made with water cooled copper mold under four Reynolds number conditions. The existence of the initial solidification layer near surface of the ingot was verified. In the initial solidification layer, primary structure consisted of austenitic cells. In the initial cell region, concentration of Cr was high and that of Ni was low. Contrary to it, in the residual δ-ferrific intercell region, concentration of Cr was low and that of Ni was high. Result of segregation measurement of Cr and Ni in the initial solidification layer was opposite to that at conventional solidification. At the boundary of the initial solidification layer, transformation of primary structure from austenite to δ-ferrite occurred. At the boundary of the initial solidification layer, the peak value of segregation ratio(C max/C min ) appeared. Segregation of Cr and Ni was larger under the low Reynolds number condition and increased as the distance from surface increased. Segregation ratio of Ni was larger than that of Cr.
Readers Who Read This Article Also Read
ISIJ International Vol.35(1995), No.11
ISIJ International Vol.52(2012), No.1
QUARTERLY JOURNAL OF THE JAPAN WELDING SOCIETY Vol.9(1991), No.1
Simulation for Progress of Solid-Liquid Coexisting Zone in Continuous Casting of Carbon Steels
Tadayoshi TAKAHASHI, Ken-ichi OHSASA, Noriyuki KATAYAMA
pp. 728-734
Abstract
The solid-liquid coexisting zone of a solidifying alloy was classified into three zones of q2, q1 and p by the fluidity of the interdendritic liquid. In the q2 zone, primary crystals and liquid can flow concurrently, whereas in the q1 zone only the interdendritic liquid can flow between the dendrites, and in the p zone the liquid is entrapped by the solids and cannot flow.
In the present study, the progress of solid-liquid coexisting zones in continuous casting of carbon steels was investigated by numerical computation. Two dimensional heat transfer in a bloom continuous casting having 400 mm × 400 mm cross section was calculated by using finite difference method. The effect of electromagnetic stirring on the extent of the solid-liquid coexisting zones was estimated by considering effective thermal conductivity in the liquid, q2 and q1 zones. Results obtained were considered to be effective for predicting the location of segregations, extent of equiaxed crystal zone and optimum timing for soft reduction technique in continuous casting process.
Hot Pressing of TiAl Alloy Powder Produced by Plasma Rotating Electrode Process and the Mechanical Properties of the Hot Pressed Compacts
Kazuo ISONISHI, Shinji KIDO, Masaharu TOKIZANE
pp. 735-742
Abstract
High quality TiAl powder was produced by Plasma Rotating Electrode Process (PREP). Two kinds of powders, the as-PREPed and the Ball Milled (PREP-BM) powders, were consolidated by Vacuum Hot Pressing (VHP). A compact having high relative density (>99%) was obtained from the PREP-BM powder by VHP at 1 223 K and 200 MPa. In order to produce such a dense compact from the as-PREPed powder, it was necessary to carry out VHP at 1 323 K and 100 MPa. The compact made from the PREP-BM powder showed superior compressive strength and ductility at room temperature to that made from the as-PREPed powder. A positive temperature dependence of 0.2% proof stress was clearly observed in each compact. It was noticeable that the strength of the compacts at elevated temperature such as 973-1 123 K was considerably higher than that of the as-cast specimen of TiAl alloy produced by conventional melting process.
Sintering Properties of Cu Coated W Composite Powders
Takahiro FUJII, Kiyoshi TAKATSU, Eiki TAKESHIMA, Akira SAKAKURA
pp. 743-750
Abstract
30 mass%Cu coated W composite powders were produced by fluidized bed electroplating process. The sintering properties and the hardness of sintered compacts were investigated in comparison with mixed powders of tungsten and copper powders.
Tungsten powders of 0.7, 8 and 25 μm were prepared and each particle was coated with copper by the above process. The same tungsten powders and a pure copper powder of less than 43μm were mixed in order to compare the properties with those of composite powders. The powders were compacted at 294 MPa and sintered for 1 h at 1 173 K or 1 423 K in hydrogen. The relative density of compacts was investigated in relation to tungsten particle size and source powders ; i.e., composite or mixed powder. The microstructure of sintered compacts was investigated by EPMA and the hardness was measured.
Composite powder compacts sintered at 1 423 K showed higher relative density and much larger densification parameter than mixed powder compacts. The microstructure of composite powder compacts contained more homogeneously and finely dispersed copper than that of mixed powder compacts. Composite powder compacts showed higher hardness than mixed powder compacts.
Readers Who Read This Article Also Read
Tetsu-to-Hagané Vol.73(1987), No.2
Tetsu-to-Hagané Vol.76(1990), No.7
Tetsu-to-Hagané Vol.76(1990), No.4
Reduction Rate and Efficiency of Fe3+ Ion to Fe2+ Ion in Iron Plating Bath by Iron Particles in a Rotary Drum Reactor
Shigeo MATSUBARA, Yukimi MIWA, Kazuhiro TAKAGI, Takashi OMI, Kei MIYANAMI
pp. 751-758
Abstract
A rotary drum reactor has been applied to the reduction of Fe3+ (2.532g/l) in a chloride bath for iron plating with metallic iron particles (0.110mm). The rotary drum reactor used has a hexagonal cross section of 260 mm in inscribed circle diameter, 300 mm in length and total inner volume of 161.
The rate-determining step in the reduction of Fe3+ was assumed to be the diffusion process of Fe3+ in the iron plating bath toward the surface of iron particles. The performance of the reactor was evaluated in terms of an apparent mass transfer coefficient. It was found that the mass transfer coefficient increases as the rotational speed and inclination of reactor increase. The reduction efficiency was found to be independent of these operating conditions of the reactor. An applicability of the rotary drum reactor to the reduction process of Fe3+ in a chloride bath for iron plating has been demonstrated.
Effect of Copper Content on Mechanical Properties of Continuously Annealed Extra-low-carbon Titanium-added Steel Sheets
Koji KISHIDA, Osamu AKISUE
pp. 759-766
Abstract
The Effects of copper content and coiling temperature after hot-rolling on the mechanical properties of continuously annealed extra-low-carbon titanium-added IF steel sheets were studied in order to develop deep drawable sheet steels having tensile strength higher than 45 kgf/mm2. Tensile strength of the 1.36%, copper added steel can be increased by about 15 kgf/mm2 by holding for 5 min at 550°C after recrystallization annealing. The recrystallization texture and γ-value are affected not only by the copper content but also by the coiling temperature. The γ-value of the 1.36% copper added steel sheet is kept high only when the steel is coiled at extremely low temperature by keeping copper in solution prior to cold rolling.
Readers Who Read This Article Also Read
Tetsu-to-Hagané Vol.73(1987), No.2
Tetsu-to-Hagané Vol.76(1990), No.7
Tetsu-to-Hagané Vol.76(1990), No.5
Grain Boundary Precipitation Strengthening due to γ' Phase in High Temperature Creep of a Ni-base Superalloy
Abdel Monem ELBATAHGY, Takashi MATSUO, Makoto KIKUCHI
pp. 767-774
Abstract
The creep resistance of Nimonic 80A subjected to prior aging at 1 273 K for various periods of time between 30 and 3 000 h was measured by a constant stress creep test at 1 273 K-49 MPa, to confirm the existence of a so-called grain boundary precipitation strengthening due to γ' phase.
The minimum creep rate increased with prior aging time : from 3.1 × 10-2h-1for 30 h aging to 1.1 × 10-1 h-1 for 3 000 h aging. This increase in the minimum creep rate could not be correlated with a decrease in a density of intragranular precipitates of γ' phase. The minimum creep rate had a good correlation with the grain boundary area fraction covered with intergranular precipitates of γ' phase. The ratios of the minimum creep rate of the speciments subjected to prior aging to that of an idealized specimen without any intergranular precipitate were equal to the free grain boundary area fraction from the intergranular precipitates of γ' phase. This confirms the intergranular precipitation strengthening previously found in Ni-Cr-W based alloys due to α2-W precipitates (T. MATSUO et al.: J. Mater. Sci., 22 (1987), p. 1901).
Creep-Fatigue Life Prediction Method Using Diercks Equation for Cr-Mo Steel
Keiji SONOYA, Isamu NONAKA, Masaki KITAGAWA
pp. 775-782
Abstract
For dealing with the situation that creep-fatigue life properties of materials do not exist, a development of the simple method to predict creep-fatigue life properties is necessary.
A method to predict the creep-fatigue life properties of Cr-Mo steels is proposed on the basis of D. DIERCKS equation which correlates the creep-fatigue lifes of SUS 304 steels under various temperatures, strain ranges, strain rates and hold times. The accuracy of the proposed method was compared with that of the existing methods. The following results were obtained.
(1) Fatigue strength and creep rupture strength of Cr-Mo steel are different from those of SUS 304 steel. Therefore in order to apply Diercks equation to creep-fatigue prediction for Cr-Mo steel, the difference of fatigue strength was found to be corrected by fatigue life ratio of both steels and the difference of creep rupture strength was found to be corrected by the equivalent temperature corresponding to equal strength of both steels.
(2) Creep-fatigue life can be predicted by the modified Diercks equation within a factor of 2 which is nearly as precise as the accuracy of strain range partitioning method. Required test and analysis procedure of this method are not so complicated as strain range partitioning method.
Role of Fine Carbide Precipitates in the Grain Refining Behavior of 3.5%Ni-Cr-Mo-V Steel
Tsukasa AZUMA, Yasuhiko TANAKA, Tooru ISHIGURO
pp. 783-790
Abstract
Grain refining behavior during austenitizing of 3.5%Ni-Cr-Mo-V turbine rotor shaft steel was investigated. Special attention was paid on the effect of Ni content and role of fine carbide precipitates on the austenite transformation and migration of the acicular austenite grain boundary. The microscopic observation of grain refining behavior reveals the following results.
(1) The grain refining of 3.5%Ni-Cr-Mo-V steels during austenitizing occurs through two stages. The first stage is austenite transformation which γ-phases succeed to the acicular bainitic ferrite structure. The second stage is the formation of equiaxed grain at higher temperatures by the migration of grain boundary of the acicular austenite.
(2) Driving force of the grain boundary migration in the second stage is considered to be the high density defects in the acicular austenite.
(3) Increase of Ni content stabilize the acicular γ-phases up to higher temperatures. This decreases the formation of equiaxed grain due to the migration of acicular austenite grain boundary.
(4) Increase of V content makes the grain refining difficult because the fine carbide precipitate such as VC works as a barrier against the grain boundary migration required for the formation of equiaxed grain.
Strength and Toughness of 12Cr-12Ni-10Mn-5Mo Steel for Cryogenic Structural Application
Junji ISHIZAKA, Ritsu MIURA, Susumu SHIMAMOTO, Hideo NAKAJIMA
pp. 791-798
Abstract
It is well known that austenitic stainless steels are non-magnetic and have good toughness and high strength at low temperature. In this study, the effects of alloying elements such as molybdenum, manganese and nitrogen on the strength and toughness of austenitic steels and the mechanical properties of their large forgings were investigated at low temperature. The obtained results are summarized as follows.
(1)Molybdenum is effective for improving strength and toughness of austenitic steel at low temperature.
(2)A 12Cr-12Ni-10Mn-5Mo steel was developed as a modification of SUS316LN for cryogenic structural material.
(3) At low temperature, the grain refinement is effective for increasing yield strength and the reduction of inclusions is effective for increasing toughness.
(4)An industrial scale forged plate of the newly developed steel was manufactured from a 6 t ESR ingot. The 140 mm thick plate showed very homogeneous mechanical properties through the thickness.
Article Access Ranking
30 Aug. (Last 30 Days)
-
Perspectives on the Promising Pathways to Zero Carbon Emissions in the Steel Industry toward 2050
ISIJ International Vol.65(2025), No.2
-
Growth, Removal, and Agglomeration of Various Type of Oxide Inclusions in Molten Steel
Tetsu-to-Hagané Vol.111(2025), No.11
-
Copper removal of liquid steel containing 0.25 % carbon using Fe2O3-CaCl2-SiO2 flux
ISIJ International Advance Publication
-
Finite Element Analysis of Bubble Growth and Particle Swelling during Coal Pyrolysis
ISIJ International Vol.65(2025), No.9
-
Corrosion Behavior of Carbon Steel under Soil Drying Conditions
ISIJ International Advance Publication
-
Cold Spot Joining of 980 MPa-class Ultra-high Strength Steel
Tetsu-to-Hagané Advance Publication
-
Factors Affecting Generation of Iron Fines in Cold Sheet Rolling of Steel
ISIJ International Vol.65(2025), No.9
-
Experimental Study on Heat Transfer Characteristics of a Moving Single-Nozzle Jet Impingement
ISIJ International Vol.65(2025), No.9
-
Combination Effect of Premixing Conditions and Iron Ore Size Distribution in Sintered Ore Granulation Process with Intensive Mixer
ISIJ International Advance Publication
-
Evaluation of Feature Selection Methods for Oxygen Supply Prediction in BOF Steelmaking
ISIJ International Advance Publication
You can use this feature after you logged into the site.
Please click the button below.