- TOP
- Tetsu-to-Hagané
- Vol. 50 (1964), No. 13
Tetsu-to-Hagané Vol. 50 (1964), No. 13
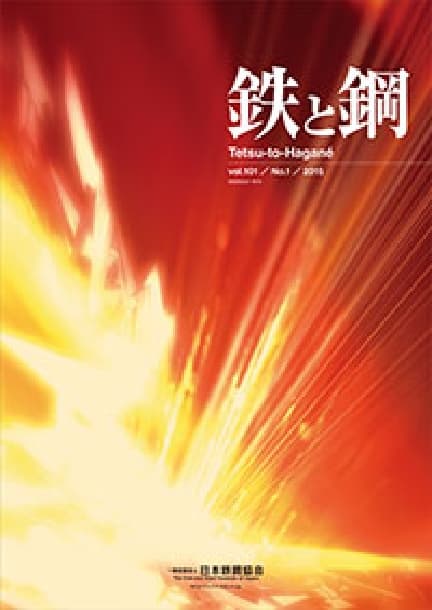
Grid List Abstracts
ONLINE ISSN: | 1883-2954 |
PRINT ISSN: | 0021-1575 |
Publisher: | The Iron and Steel Institute of Japan |
Backnumber
-
Vol. 111 (2025)
-
Vol. 110 (2024)
-
Vol. 109 (2023)
-
Vol. 108 (2022)
-
Vol. 107 (2021)
-
Vol. 106 (2020)
-
Vol. 105 (2019)
-
Vol. 104 (2018)
-
Vol. 103 (2017)
-
Vol. 102 (2016)
-
Vol. 101 (2015)
-
Vol. 100 (2014)
-
Vol. 99 (2013)
-
Vol. 98 (2012)
-
Vol. 97 (2011)
-
Vol. 96 (2010)
-
Vol. 95 (2009)
-
Vol. 94 (2008)
-
Vol. 93 (2007)
-
Vol. 92 (2006)
-
Vol. 91 (2005)
-
Vol. 90 (2004)
-
Vol. 89 (2003)
-
Vol. 88 (2002)
-
Vol. 87 (2001)
-
Vol. 86 (2000)
-
Vol. 85 (1999)
-
Vol. 84 (1998)
-
Vol. 83 (1997)
-
Vol. 82 (1996)
-
Vol. 81 (1995)
-
Vol. 80 (1994)
-
Vol. 79 (1993)
-
Vol. 78 (1992)
-
Vol. 77 (1991)
-
Vol. 76 (1990)
-
Vol. 75 (1989)
-
Vol. 74 (1988)
-
Vol. 73 (1987)
-
Vol. 72 (1986)
-
Vol. 71 (1985)
-
Vol. 70 (1984)
-
Vol. 69 (1983)
-
Vol. 68 (1982)
-
Vol. 67 (1981)
-
Vol. 66 (1980)
-
Vol. 65 (1979)
-
Vol. 64 (1978)
-
Vol. 63 (1977)
-
Vol. 62 (1976)
-
Vol. 61 (1975)
-
Vol. 60 (1974)
-
Vol. 59 (1973)
-
Vol. 58 (1972)
-
Vol. 57 (1971)
-
Vol. 56 (1970)
-
Vol. 55 (1969)
-
Vol. 54 (1968)
-
Vol. 53 (1967)
-
Vol. 52 (1966)
-
Vol. 51 (1965)
-
Vol. 50 (1964)
-
Vol. 49 (1963)
-
Vol. 48 (1962)
-
Vol. 47 (1961)
-
Vol. 46 (1960)
-
Vol. 45 (1959)
-
Vol. 44 (1958)
-
Vol. 43 (1957)
-
Vol. 42 (1956)
-
Vol. 41 (1955)
Keyword Ranking
07 Sep. (Last 30 Days)
Tetsu-to-Hagané Vol. 50 (1964), No. 13
Study on the Phenomenon of Iron Escaping from Cinder Notch of Blast Furnace
Kozo MORINAGA, Yoshimitsu JOMOTO, Bunji ETO, Yoshio OKUNO
pp. 2149-2157
Abstract
Customarily the phenomenon of iron escaping is explained as the result of build-up of viscous slag bearing reduced titanium compound and Salamander in the hearth.
However, it seems that the quantity of iron escaping from cinder notch in case of a certain blast furnace is rather related to the low permeability of furnace column rather than to titanium content in burden.Thereupon, we examined the cause of the phenomenon by measuring slag viscosity and analyzing permeability of column.
As the result, the phenomenon is found to result not from the elevation of slag viscosity by titanium compound, but from the reduction of raceway by low permeability of column.
This is thought due to the irregularity of slag temperature around the core and a narrowing of space between the inner wall and the core by reduction of raceway.
Experiments on the Powder-coal Injection into 1-ton Blast Furnace
Mitsuru TATE, Chihu NAKANE, Cheoul Woo KIM, Kichiya SUZUKI
pp. 2157-2166
Abstract
In August, 1962, powder-coal injection tests were executed at the experimental blast furnace (about 05m3 inner volume 0.5m hearth diameter about 2m effective height) of the Institute of Industrial Science, Tokyo University. The furnace, ordinarily, was operated with 100% self-fluxing sinter (3-10mm size, CaO/SiO2=1.2) and consumed about 1.8t coke per day of 10-20mm size containing 88'1% fixed carbon and 10'9% ash. About 470kg coal per day of -1mm size, which contained 45% carbon, 39.5% volatile matter and 11.9% ash was injected through the 4 tuyeres by cold compressed air (about 0.45Nm3/min). For heat compensation, blast temperature was raised from 575°C (at normal operation period) to 670°C and oxygen was enriched so as to make its concentration in the blast about keeping total oxygen volume blown into the furnace per unit time the same as that at normal operation period.
Coke rate decreased from 1.478t/t (at normal operation) to 1.091t/t (by 26%), and pig output increased by 15%. Gasification ratio of coal was calculated to be only about 75%; nevertheless, apparent replacement ratio of unit coal was 1.13 unit of coke. This result is explained mainly by the remarkable decrease of solution loss caused by the reducing action of H2 contained in the coal: this enabled an increase of burden ratio, and therefore, that of pig output, which diminished relative heat losses due to top gas and radiation of furnace.
Coke equivalent of this heat economy, as well as that of carbon contained in the coal, was calculated, the sum of which was found to have nearly the same value as the obtained replacement ratio.
Readers Who Read This Article Also Read
Tetsu-to-Hagané Vol.70(1984), No.11
Tetsu-to-Hagané Vol.60(1974), No.14
Tetsu-to-Hagané Vol.45(1959), No.11
On Iron Oxide Coolants in the LD Process
Etsuro HONMA, Shizuo OKUBO, Tatsuo OYA, Hisashi MATSUNAGA
pp. 2166-2175
Abstract
In the LD process, the operation, using sintered ore, briquet, iron sand, and Marcona pellet as iron-oxide coolants, was investigated about the following items comparing with mill scale operation: slopping conditions, total iron contents in the final slag, dephosphorization and desulphurization during the blowing, the metallic yield, oxygen consumption and. the cooling effects.
This article shows the results obtained from the test blowing charged with the abovementioned coolants.
1) These coolants slightly increase slopping.
2) The addition of iron sand or pellet increases the total Fe content in slag by about 2% respectively, and improves dephosphorization efficiency.
3) The use of briquet reduces desulphurization efficiency.
4) The use of sintered ore, iron sand and pellet lowers the metallic yield by 04%, 1.1% and 0.3% respectively.
5) Oxygen consumption is the same as in the normal operation.
6) The relative cooling coefficients of sintered ore, briquet, iron sand and pellet to scrap are 26, 18, 22 and 28 respectively.
Considering the handling troubles, the cost of these coolants and the amounts of domestic. supply of mill scale, 0k/t-ingot sintered ore and 10 to 15kg/t-ingot mill scale are now used our LD shop.
Relations between Freezing Rate of Ingot and Segregations of Sulphur, Phosphorus, Oxygen and Nitrogen
Yoshitaka NAKAGAWA, Akitsugu MOMOSE
pp. 2175-2181
Abstract
In this report, relations between freezing rate and segregation of sulphur, phosphorus, oxygen and nitrogen on Fe-S, Fe-P, Fe-O and Fe-N systems were studied, and it was shown that in order to present segregation, freezing rates should be above 1.2mm/min, in case of oxygen and1.8mm/min, in cases of sulphur, phosphorus and nitrogen.
Calculation from measured results shows that the value of K0 is 0.15 which is larger than old data, and σ/Ds=1.6-3.8×103sec/cm, σ/Dp=1.1-3.4×103sec/cm, σ/DO=1.94×103sec/cm and σ/DN=1.15-103sec/cm.
Effects of Mn, Al, Ti, Zr, V, Nb and Cr on Fe-S System
Toyosuke TANOUE, Takami IKEDA
pp. 2182-2189
Abstract
Most part of sulfur in steel precipitates as sulfide inclusions and it has remarkable effects; on the various properties of steel.
In order to reveal the effects of Mn, Al, Ti, Zr, V, Nb and Cr addition upon steel which contains up to 0.30%S, authors studied the crystal structures, the optical properties, the distribution, the etching behavior and the hot deformation characteristics of sulfide inclusions in steels containing one of those alloying elements.
The results are as follows:
(1) The formation of FeS, α-MnS, TiS, Zr3S4 or ZrS2, VS, CbS and “CrS” was respectively observed, and aluminum sulfide considered to be Al2S3, was observed.
(2) The crystal structure of sulfide inclusions was closely connected with their optical anisotropy. TiS, CbS and “CrS” were strongly anisotropic.
(3) The etching behaviors of sulfide inclusions were different from one another. TiS, VS, NbS and “CrS” were not chemically attacked by 20% HF×10min etching.
(4) a-MnS, “CrS” and sulfide in Al-added steel were deformed during hot-working. TiS, Zr3S4, ZrS2 and VS, however, showed no deformation. Fe-S steel and Nb-added steel were not forgeable.
Niobium Steel for Glass Lining Use
Kiichi NARITA, Atsusi MIYAMOTO, Koshi MIYAZAKI
pp. 2189-2198
Abstract
We prepared a niobium steel for glass lining use by utilizing outstanding: chemical and metallurgical properties of niobium on the basis of the results of its investigation as reported in our previous paper which was published as a part of our studies of special elements having effects on steel. As the result of our examination, we have found that as compared with titanium steel heretofore in use, niobium steel is free from difficulties in melting and accordingly it is possible to develope niobium steel having eminent properties as a material for glass lining use.
The following are the results of our study on niobium steel.
1. The surface of niobium steel ingot is much better than that of titanium steel and fatal surface defects such as sand marks, sand bites, slag bites, etc. are extremely few in it as compared with titanium steel. In the case of titanium steel, there is the tendency that surface defects will be remarkably increased with an increase of titanium content, but such a phenomenon can not be observed in the case of niobium steel. Accordinglly, it is possible to produce rolled or forged materials with less surface defects for glass lining by using niobium steel instead of titanium steel.
2. Titanium is easily oxidizable and in consequence, its recovery in molten steel is extremely low. It is, therefore, rather difficult to add an exactly constant quantity of titanium to molten steel. On the other hand, niobium is not so easily oxidizable as titanium and yet its recovery in molten steel is high;for example, it is more than 90% in killed steel and in most cases niobium can be added to molten steel in an almost perfectly constant quantity.
3. Most of oxide inclusions found in titanium steel are crystalline titanium oxides and such oxide inclusions have a tendency to increase with an increase of the quantity of titanium contained in steel. On the contrary, oxides found in niobium steel are glassy compounds composed of SiO2 and Al2O3, and niobium oxides are comparatively scarce.
4. With an increase of titanium addition the cleanliness of steel generally tends to be lost, but such a phenomenon can not happen in the case of niobium steel.
5. By adding titanium or niobium to steel, austenitic grain of steel is refined very much, but in either case of titanium or niobium, this grain tends to become coarsened when the quantity of titanium or niobium contained in steel is increased over a certain extent.
6. By adding titanium or niobium to steel, the point of transformation of steel has a tendency to rise and the coefficient of thermal expansion of steel has a tendency to fall. The coefficient of thermal expansion at 100 to 300°C is a little greater in niobium steel than in titanium steel.
7. As to the blister phenomenon in the surface of the glass coating of titanium or niobium steel material in its firing process, it has a tendency to decrease as the ratio of Ti/C or Nb/C in steel increases, and this tendency is very remarkable in niobium steel.
8. Regarding the adherence of the fire-coated glass to the surface of the test piece material of steel at normal temperature, it is the best when steel contains 0.25% titanium or 0.44 % niobium there in. It has, however, a tendency to become worse if the quantity of titanium or niobium contained in steel is increased over the aforesaid percentage.
9. Niobium steel is much better than titanium steel in respect of the thermal shock resistance at 200°C and 220°C of the glass coating on the surface of the test piece material of steel.
Improvement in Forgeability of N-155 Type Alloys by Addition of Manganese
Renpei YODA, Heitaro YOSHIDA, Kisaburo KOIKE
pp. 2198-2205
Abstract
N-155 alloy and the same alloy with 10% Ni replaced with equal amount of Mn were selected as the base composition and about twenty alloys containing various amounts of carbon and nitrogen were melted.
The reasons why not only the forgeability is improved by the addition of manganese, but also an excellent high temperature property is obtained by the addition of proper amounts of carbon and nitrogen were explored.
Results obtained were as follows.
(1) If the carbon and nitrogen contents are nearly equal, the solidifying temperature and the solution temperature of the precipitates drop, the deformation resistance becomes lower and the cast structure more easily disappears in the high manganese alloys than in N-155 type alloys.
The reasons why the high manganese alloys are more easily forged than the N-155 type alloys, lie in these facts.
(2) The fact that the softening resistance property of the high manganese alloys is more excellent than that of the N-155 type alloys, is due to the fact that the age hardening property of the former is superior to that of the latter.
The reason why the high manganese alloys have an excellent high temperature property, though they are easily forged, is given by the above-mentioned fact.
Spectrographic Analysis of Boron in Stainless Steel
Takehiko KAWAGUCHI, Yasuo KUDO, Tetsuo MATSUMURA
pp. 2205-2214
Abstract
A rapid and accurate point-to-plane technique has been developed for the spectrographic determination of boron in austenitic stainless steel in the concentration range 0.015 to 0.25%. In this paper, the past literatures reporting on the spectrochemical analysis of boron in steel are cited and full details are given of the experimental procedure.
The data were evaluated by a thorough statistical study.
Volatilization characteristics of boron, iron, and the elements of counter electrodes were investigated by a moving-plate study in various arc sources.
The analysis was performed with a 3.4M Ebert type grating spectrograph using an intermittent a.c. arc operating at 220V, with copper counter electrode, arc current of 6A, and exposure time of 20S after 10s pre-arc.The analytical line pair is Fe12437.06A/B12496.78A.
The relative standard deviation for the determination ranged from 3 to 75%
The analytical results are found to be in good agreement with the results of wet chemical determinations.
An account is also given of thermal effects on boron in boron-steel in the process of sampling and/or arcing.A simple procedure for the selection of analytical line pair and a calibration method using an element in counter electrode as internal standard are proposed.
Transmission Electron Microscopy of Steels
Zenji NISHIYAMA, Kenichi SHIMIZU
pp. 2215-2243
Readers Who Read This Article Also Read
Tetsu-to-Hagané Vol.50(1964), No.5
Tetsu-to-Hagané Vol.53(1967), No.11
Tetsu-to-Hagané Vol.54(1968), No.11
A Rate Equation for the Reduction of Iron Ore
Kazumi MORI
pp. 2259-2260
Abstract
A rate equation has been derived for the gaseous reduction of iron are pellets on the assumption that both chemical reaction and diffusion contribute to the overall reduction rate. It was assumed that there is no resistance of diffusion through the boundary layer outside the pellet and chemical reaction takes place only at the interface between reduced and unreduced layers. Under these conditions the rate equation is given as follows:
(1/k)[1-(1-R) 1.3] + (r0/D)[1/2-R/3-(1-R) 2/3/2] = (C0-Cc) t/r0d0
whereR: fractional reduction k: chemical reaction rate constant
t: time D: effective diffusion coefficient: radius of pellet C0: gas concenration in the bulk gas phase
d0: density of pellet Cc: equilibrium gas concentration
The two terms on the left side of the equation show the relative contribution by chemical reaction and by diffusion of the reducing gas through the reduced metal layer. It was found that the equation agrees with experimental data except towards the completion of reduction.
Equation for the reduction controlled either by chemical reaction or by diffusion could be derived as the limitimg cases of the above-mentioned equation.
参考文献
pp. 2265-2269
Readers Who Read This Article Also Read
ISIJ International Vol.53(2013), No.2
ISIJ International Vol.58(2018), No.10
Article Access Ranking
07 Sep. (Last 30 Days)
-
Perspectives on the Promising Pathways to Zero Carbon Emissions in the Steel Industry toward 2050
ISIJ International Vol.65(2025), No.2
-
Growth, Removal, and Agglomeration of Various Type of Oxide Inclusions in Molten Steel
Tetsu-to-Hagané Vol.111(2025), No.11
-
Finite Element Analysis of Bubble Growth and Particle Swelling during Coal Pyrolysis
ISIJ International Vol.65(2025), No.9
-
Interface behavior leading to Al/Cu dissimilar metal bonding formation with high-speed eutectic reaction induced by applying current
QUARTERLY JOURNAL OF THE JAPAN WELDING SOCIETY Vol.43(2025), No.2
-
Copper removal of liquid steel containing 0.25 % carbon using Fe2O3-CaCl2-SiO2 flux
ISIJ International Advance Publication
-
Corrosion Behavior of Carbon Steel under Soil Drying Conditions
ISIJ International Advance Publication
-
Cold Spot Joining of 980 MPa-class Ultra-high Strength Steel
Tetsu-to-Hagané Advance Publication
-
Combination Effect of Premixing Conditions and Iron Ore Size Distribution in Sintered Ore Granulation Process with Intensive Mixer
ISIJ International Advance Publication
-
A preliminary study on reduction degradation of iron ore sinter using sinter analogue and X-ray micro-computed tomography (MCT)
ISIJ International Advance Publication
-
Viscosity Measurement of Foam with High Gas Volume Fraction Using Sphere Pull-up and Dam-break Experiments
ISIJ International Advance Publication
You can use this feature after you logged into the site.
Please click the button below.