- TOP
- Tetsu-to-Hagané
- Vol. 53 (1967), No. 6
Tetsu-to-Hagané Vol. 53 (1967), No. 6
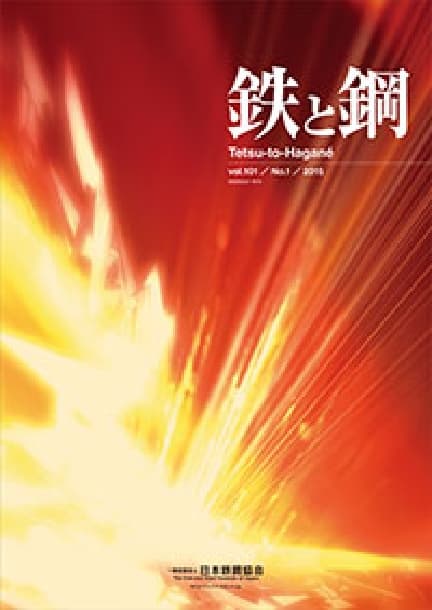
Grid List Abstracts
ONLINE ISSN: | 1883-2954 |
PRINT ISSN: | 0021-1575 |
Publisher: | The Iron and Steel Institute of Japan |
Backnumber
-
Vol. 111 (2025)
-
Vol. 110 (2024)
-
Vol. 109 (2023)
-
Vol. 108 (2022)
-
Vol. 107 (2021)
-
Vol. 106 (2020)
-
Vol. 105 (2019)
-
Vol. 104 (2018)
-
Vol. 103 (2017)
-
Vol. 102 (2016)
-
Vol. 101 (2015)
-
Vol. 100 (2014)
-
Vol. 99 (2013)
-
Vol. 98 (2012)
-
Vol. 97 (2011)
-
Vol. 96 (2010)
-
Vol. 95 (2009)
-
Vol. 94 (2008)
-
Vol. 93 (2007)
-
Vol. 92 (2006)
-
Vol. 91 (2005)
-
Vol. 90 (2004)
-
Vol. 89 (2003)
-
Vol. 88 (2002)
-
Vol. 87 (2001)
-
Vol. 86 (2000)
-
Vol. 85 (1999)
-
Vol. 84 (1998)
-
Vol. 83 (1997)
-
Vol. 82 (1996)
-
Vol. 81 (1995)
-
Vol. 80 (1994)
-
Vol. 79 (1993)
-
Vol. 78 (1992)
-
Vol. 77 (1991)
-
Vol. 76 (1990)
-
Vol. 75 (1989)
-
Vol. 74 (1988)
-
Vol. 73 (1987)
-
Vol. 72 (1986)
-
Vol. 71 (1985)
-
Vol. 70 (1984)
-
Vol. 69 (1983)
-
Vol. 68 (1982)
-
Vol. 67 (1981)
-
Vol. 66 (1980)
-
Vol. 65 (1979)
-
Vol. 64 (1978)
-
Vol. 63 (1977)
-
Vol. 62 (1976)
-
Vol. 61 (1975)
-
Vol. 60 (1974)
-
Vol. 59 (1973)
-
Vol. 58 (1972)
-
Vol. 57 (1971)
-
Vol. 56 (1970)
-
Vol. 55 (1969)
-
Vol. 54 (1968)
-
Vol. 53 (1967)
-
Vol. 52 (1966)
-
Vol. 51 (1965)
-
Vol. 50 (1964)
-
Vol. 49 (1963)
-
Vol. 48 (1962)
-
Vol. 47 (1961)
-
Vol. 46 (1960)
-
Vol. 45 (1959)
-
Vol. 44 (1958)
-
Vol. 43 (1957)
-
Vol. 42 (1956)
-
Vol. 41 (1955)
Keyword Ranking
29 Aug. (Last 30 Days)
Tetsu-to-Hagané Vol. 53 (1967), No. 6
On the Mechanism of Formation of Oxide Inclusions at the Addition of Deoxydizer
Yasushi KOJIMA, Kiichi TAKAHASHI, Hiroshi SAKAO, Kokichi SANO
pp. 589-598
Abstract
By adding various deoxidizers to the liquid iron which was heated in the high frequency induction furnace, the dissolved state and growth of inclusions were observed at 1600°C. The results obtained are summarizedas follows.
1) Metallic chromium dissolved very slowly into the liquid iron. That is, the distribution of chromiumat the boundary between chromium and molten iron is considered a rate-determining step of this dissolution.
Inclusions were formed at a slower rate than the rate of dissolution, because they formed in the regionof 26%Cr.
2) Fe-Mn alloy dissolved into the liquid iron as a laminar flow. Inclusions of MnO are formed aroundfine particles of Al2O3 as nuclei in this flow.
3) Ti, Si and Al were made to dissolve into the liquid iron by stirring with thermal convection due to the heat of mixing at the boundary between the deoxidizer and the molten iron. Cloudy inclusions wereobserved for these deoxidizers in this case.
On the basis of the nucleation theory, these phenomena were considered and the conclusions were drawnas follows.
4) Homogeneous necleation occurred at the dissolving step for the elements Si, Ti and Al which had ahigh deoxidizing power and cloudy inclusions were formed at the initial period of deoxidation.
5) Contrary to the above, homogeneous nucleation did not occur for the elements Cr, and Mn whichhad a low deoxidizing power. These inclusions were formed through heterogeneous nucleation.
Readers Who Read This Article Also Read
Tetsu-to-Hagané Vol.49(1963), No.2
Tetsu-to-Hagané Vol.54(1968), No.9
Tetsu-to-Hagané Vol.53(1967), No.7
The Investigation of the Deformation Processes of Hot Caliber Rolling of Steel Using Plasticine as a Model Material
Isao GOKYU, Yoshihiro SAITO
pp. 599-610
Abstract
Three typical passes i. e. square-oval pass, square-dia. pass and box-pass for caliber rolling were designed which had concave-, convex-and normal shapes of projected contact surface respectively. Model billetsbuiltup of alternate layers of gray and white plasticine were prepared and part-rolled between smooth plastercast rolls using CaCO3 powder as lubricant whose condition was well known to give a good simulationof hot rolling of steel and the deformation patterns were analyzed so as to reveal the deformation processof caliber rolling.
The results were as follows:
(1) The deformations of equidistant lines perpendicular to the direction of rolling on the billet surfaceare characterized by the shape of contact surface, i. e. in square-oval pass of concave-shaped contact surfacethe lines bend backward. In square-dia. pass of convex-shaped contact surface, however, bending is forwardinstead of backward. There is no bending in box-pass of normal contact surface.
(2) The elastic wedge in the material at the entry side shortens its length or eventually vanishes if itslocation is near the middle of billet for square-oval pass or near the edge for square dia. pass. This effectmeans that there is such interaction between the parts of long contact-arc and short one that the deformation of the former facilitates the deformation of the latter. In other words, the deformation of the formeris restrained by the latter.
(3) In all cases, adhesion of material to the rolls occurs over a wide area of contact surface except narrowzones near entry and exit.
(4) The neutral point for caliber rolling can be determined from normal strain distribution in the directionof rolling because at the neutral point the velocities of roll-surface and the material are equal, thusnormal strains along the arc of contact and along the center line of material must be equal. This point approximatelycoincides with the point of maximum bending of line perpendicular to the direction of rollingin the plane normal to the roll axis. The neutral lines in both caliber rollings except box-pass are slightlybent backward.
(5) The normal strain in the direction of spreading along the horizontal center line of the cross-sectionof rolled billet is relatively small and uniform in square-dia. pass. In square-oval pass, however, it isextremely large near the edge and small in the middle.
Readers Who Read This Article Also Read
MATERIALS TRANSACTIONS Vol.56(2015), No.12
ISIJ International Vol.53(2013), No.3
ISIJ International Vol.51(2011), No.5
Some Consideration on the Premature Failure of Fully Hardened Roll
Kiyozo SAKABE
pp. 611-628
Abstract
Four high cold strip mill work rolls are fully hardened forged steel rolls which are made of high carbonchromium steel with an ordinary composition of 0.8-1.15 percent carbon and 0.8-2.6 percent chromium, subjected to water quenching and low temperature-stress relief at 100-250°C. They have residualstresses caused by the above mentioned heat treatment, so they are very liable to have troubles in rollingoperations.
Major troubles occurring in the early period of the life of these rolls are fracture taking with time lag afterquenching in storage and fatigue fracture originating at the center bore surface in rolling operation. Thesetroubles are, it seems, ascribable to their manufacturing conditions. However, as the occurrence of thesefractures is not so frequent, the differences in properties between fractured rolls and sound rolls have not beenclarified yet. Common understanding was that delayed fracture would most likely bethe result of quenchcracking due to heavy residual stresses developed during the quenching process of the roll, while the fatiguefracture might be caused by defects existing in the vicinity of the bore.
A study on the manufacturing processes, properties and residual stresses of the roll has produced thefollowing result which conflicts with the conventional understanding.
1) The phenomenon of a fracture occurring in the roll with time lag after quenching is a delayedfailure caused by the hydrogen in the material under the influence of tensile residual stresses. It is nota simple quench cracking. And the occurrence of the fracture is very frequent in the winter time.
This is not because the temperature was low, but because fractured rolls which had been east in summer whenhumidity was high and hydrogen content in molten steel was increased accordingly, were subjected toquenching treatment in cold winter.
The delayed failure is likely to happen in a roll whose steel contains 3.5ppm or more of hydrogen attapping.
Some rolls of this steel may incur fracture, but others do not, possibly because of nonuniform distributionof hydrogen, excessive segregation and varied situation of micro defects from which fracture may originate.
2) Fatigue fracture at bore takes place even if there is no defect. The cause of fracture is that fatiguestrength is lowered by tensile residual stress acting as a mean stress against working stress in rolling operation.And it is inferred that tensile residual stress at bore is caused through insufficient cooling in bore underquenching treatment.
Investigation of Niobium Containing Structural Steel
Susumu GOHDA, Hisashi GONDOH, Isao KIMURA
pp. 629-640
Abstract
A high yield stress structural steel which has good notch toughness even for heavy sections, has beendeveloped by addition of a small amount of niobium to a semi-killed steel.
Selection of heating temperature before hot rolling and subsequently the control of the amount ofniobium-precipitates in the steel, were found to be very important to the manufacturing process.
The steel thus developed has a yield stress greater than 36kg/mm2, good notch toughness by V-Charpyimpact value of over 3.5kg-m/cm2 at 0°C and high fatigue strength over 30kg/mm2 by repeated bendingtests.
The steel has good weldability comparable to conventional manganese-silicon steels with equivalent tensilestrengths, and can be welded either by manual or automatic welding processes.
Development and Recent Technical Problems in Steel Tube Making Processes
Kaoru HARADA
pp. 641-660
Article Access Ranking
29 Aug. (Last 30 Days)
-
Perspectives on the Promising Pathways to Zero Carbon Emissions in the Steel Industry toward 2050
ISIJ International Vol.65(2025), No.2
-
Growth, Removal, and Agglomeration of Various Type of Oxide Inclusions in Molten Steel
Tetsu-to-Hagané Vol.111(2025), No.11
-
Copper removal of liquid steel containing 0.25 % carbon using Fe2O3-CaCl2-SiO2 flux
ISIJ International Advance Publication
-
Finite Element Analysis of Bubble Growth and Particle Swelling during Coal Pyrolysis
ISIJ International Vol.65(2025), No.9
-
Corrosion Behavior of Carbon Steel under Soil Drying Conditions
ISIJ International Advance Publication
-
Cold Spot Joining of 980 MPa-class Ultra-high Strength Steel
Tetsu-to-Hagané Advance Publication
-
Factors Affecting Generation of Iron Fines in Cold Sheet Rolling of Steel
ISIJ International Vol.65(2025), No.9
-
Experimental Study on Heat Transfer Characteristics of a Moving Single-Nozzle Jet Impingement
ISIJ International Vol.65(2025), No.9
-
Combination Effect of Premixing Conditions and Iron Ore Size Distribution in Sintered Ore Granulation Process with Intensive Mixer
ISIJ International Advance Publication
-
Evaluation of Feature Selection Methods for Oxygen Supply Prediction in BOF Steelmaking
ISIJ International Advance Publication
You can use this feature after you logged into the site.
Please click the button below.