- TOP
- Tetsu-to-Hagané
- Vol. 68 (1982), No. 1
Tetsu-to-Hagané Vol. 68 (1982), No. 1
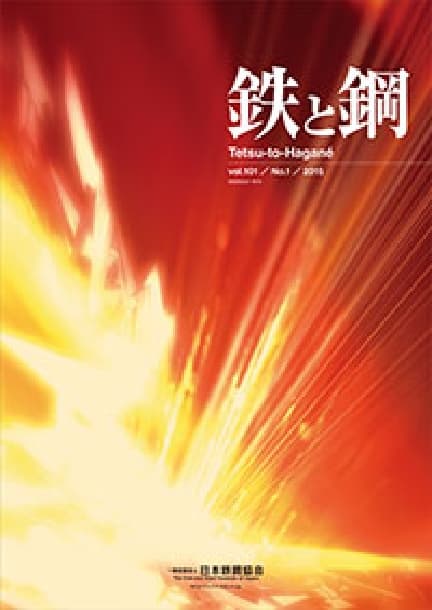
Grid List Abstracts
ONLINE ISSN: | 1883-2954 |
PRINT ISSN: | 0021-1575 |
Publisher: | The Iron and Steel Institute of Japan |
Backnumber
-
Vol. 111 (2025)
-
Vol. 110 (2024)
-
Vol. 109 (2023)
-
Vol. 108 (2022)
-
Vol. 107 (2021)
-
Vol. 106 (2020)
-
Vol. 105 (2019)
-
Vol. 104 (2018)
-
Vol. 103 (2017)
-
Vol. 102 (2016)
-
Vol. 101 (2015)
-
Vol. 100 (2014)
-
Vol. 99 (2013)
-
Vol. 98 (2012)
-
Vol. 97 (2011)
-
Vol. 96 (2010)
-
Vol. 95 (2009)
-
Vol. 94 (2008)
-
Vol. 93 (2007)
-
Vol. 92 (2006)
-
Vol. 91 (2005)
-
Vol. 90 (2004)
-
Vol. 89 (2003)
-
Vol. 88 (2002)
-
Vol. 87 (2001)
-
Vol. 86 (2000)
-
Vol. 85 (1999)
-
Vol. 84 (1998)
-
Vol. 83 (1997)
-
Vol. 82 (1996)
-
Vol. 81 (1995)
-
Vol. 80 (1994)
-
Vol. 79 (1993)
-
Vol. 78 (1992)
-
Vol. 77 (1991)
-
Vol. 76 (1990)
-
Vol. 75 (1989)
-
Vol. 74 (1988)
-
Vol. 73 (1987)
-
Vol. 72 (1986)
-
Vol. 71 (1985)
-
Vol. 70 (1984)
-
Vol. 69 (1983)
-
Vol. 68 (1982)
-
Vol. 67 (1981)
-
Vol. 66 (1980)
-
Vol. 65 (1979)
-
Vol. 64 (1978)
-
Vol. 63 (1977)
-
Vol. 62 (1976)
-
Vol. 61 (1975)
-
Vol. 60 (1974)
-
Vol. 59 (1973)
-
Vol. 58 (1972)
-
Vol. 57 (1971)
-
Vol. 56 (1970)
-
Vol. 55 (1969)
-
Vol. 54 (1968)
-
Vol. 53 (1967)
-
Vol. 52 (1966)
-
Vol. 51 (1965)
-
Vol. 50 (1964)
-
Vol. 49 (1963)
-
Vol. 48 (1962)
-
Vol. 47 (1961)
-
Vol. 46 (1960)
-
Vol. 45 (1959)
-
Vol. 44 (1958)
-
Vol. 43 (1957)
-
Vol. 42 (1956)
-
Vol. 41 (1955)
Keyword Ranking
06 Sep. (Last 30 Days)
Tetsu-to-Hagané Vol. 68 (1982), No. 1
Chemical Consideration of Slag Basicity
Toshio YOKOKAWA
pp. 26-33
Readers Who Read This Article Also Read
Tetsu-to-Hagané Vol.49(1963), No.14
Tetsu-to-Hagané Vol.69(1983), No.6
Tetsu-to-Hagané Vol.69(1983), No.10
Trend of High Speed Tool Steel
Kingo KIYONAGA, Hideki NAKAMURA, Norimasa UCHIDA
pp. 34-41
Energy Saving and Change of Energy Structure at Steel Works/Evaluation of Standard Samples for Instrumental Analysis by X-ray Fluorescence Spectrometry-Japanese Standards of Iron and Steel Low Alloy Steel Series A-
Tetsuya YAMAMOTO, Hiroshi YASUDA
pp. 49-71
Readers Who Read This Article Also Read
Tetsu-to-Hagané Vol.78(1992), No.8
Tetsu-to-Hagané Vol.82(1996), No.5
Tetsu-to-Hagané Vol.82(1996), No.5
Rate of Transfer of Manganese from MnO-(CaO+FetO+MgO)-SiO2 Slag to Liquid Iron
Nobuya SHINOZAKI, Katsumi MORI, Yasuji KAWAI
pp. 72-80
Abstract
The rate of transfer of manganese from slag to liquid iron was investigated by measuring the change of manganese and oxygen contents of liquid iron under MnO-(CaO+FetO +MgO)-SiO2 slag in a magnesia crucible. Experiments were carried out with slags of basicity from 0.66 to 1.19 at 1 600°C.
The results are as follows :
1) The equilibrium between liquid iron and slag was attained after about 30 min.
2) The rate of reaction and manganese content of final liquid iron increased with decrease of oxygen potential of the system and with increase of manganese oxide content of initial slag.
3) The experimental results were interpreted by the rate equation derived from the assumptions that the reaction rate was controlled by the transfer of Mn, O, (MnO) and (FeO) in the boundary layers and that the distribution-ratio of manganese and oxygen varied with proceeding of the reaction. Values of mass-transfer-coefficient of (MnO) were nearly the same with those obtained in the previous study on the rate of oxidation of manganese in liquid iron at the same temperature.
Readers Who Read This Article Also Read
Tetsu-to-Hagané Vol.61(1975), No.1
Tetsu-to-Hagané Vol.74(1988), No.1
Tetsu-to-Hagané Vol.85(1999), No.9
Bloating Mechanism of Water Glanulated Blast Furnace Slag
Izumi MON-NA, Akira OKAMOTO, Syohei SUZUKI, Yoshikazu NAGAO, Hideyuki TOKUMARU, Sei-ichi MYOZIN
pp. 81-89
Abstract
Investigation was made concerning with a bloating mechanism of water granulated blast furnace slag and the effect of granulating conditions on the density of it. Gases, evolved from molten slag droplets while they were cooled in water, consisted of hydrogen and nitrogen, and also gases existing in the closed pores of the granulated slag mainly consisted of hydrogen and nitrogen of which ratio was of about 1.8. Increase of nitrogen content dissolved in molten slag, made the granulated slag more bloating, and this showed that the dissoved nitrogen causes the evolution of hydrogen and nitrogen gases. Cooling water dissolved into molten slag droplet for a short period until its solidification.
From above mentioned results, it is considered that the bloating of the granulated slag is due to the formation of hydrogen and nitrogen according to the following reaction;
2N 3-+3H2O=3H2+N2+3O2-
Effect of granulating conditions (i.e., water volume, water jet velocity, water temperature and slag temperature) on the apparent specific gravity of the granulated slag was clarified. These conditions influence the reaction time or the reaction temperature for gas forming.
Readers Who Read This Article Also Read
Tetsu-to-Hagané Vol.68(1982), No.1
Tetsu-to-Hagané Vol.68(1982), No.1
Observation of Gas Jets Injected into a Thin Sheet of Liquid Metal
Yasuhisa OZAWA, Kazumi MORI
pp. 90-97
Abstract
A study has been made of the behavior of gas jet injected into a thin sheet of mercury (i.e., a "two-di-mensional" environment). The vessel was made of acrylate resins. The sheet of mercury was 0.5 cm in thickness. Nitrogen gas (5803 200 cm3/s) was injected into the mercury bath through an orifice of 0.2 cm in diameter. The gas jet behavior was observed by using a high speed camera.
It is observed that, when jetting occurs, many tiny droplets are formed in the gas jet at the orifice exit. The present result for bubbling-jetting transition agrees well with the previous data obtained by three dimensional bath. It is shown that the jetting behavior is determined exclusively by the gas-flow velocity. The injected gas does not form a continuous gas channel even in the sonic velocity region. The injected jet breaks up at some distance from the orifice exit, leaving a gas jet residual. The minimum length of the gas jet residual is fixed for each gas-flow velocity. Thus, it has been found that the gas phase forms a small continuous jet extending from the orifice exit to the top of the jet residual.
Readers Who Read This Article Also Read
Tetsu-to-Hagané Vol.68(1982), No.1
Tetsu-to-Hagané Vol.68(1982), No.1
Characteristics of Jetting in Gas Injection into Liquid
Yasuhisa OZAWA, Kazumi MORI
pp. 98-104
Abstract
The present study is concerned with jetting behavior of gas jets injected into water bath. Nitrogen gas (20010 000 cm3/s) was injected into the water bath through an orifice of 0.10.3 cm in diameter located at the bottom. The gas jet behavior was observed directly by using a high speed cinecamera. The frequency of the bubble knocking at the bottom was measured with a microphone.
It is found that the bubbling-jetting transition of gas jets injected into water begins to occur when the gas-flow velocity at the exit of an orifice exceeds the sonic velocity. This phenomenon is similar to the behavior of gas jets in mercury bath. In the sonic region the frequency of bubble knocking decreases with increasing gas-flow velocity. At the highest gas-flow velocity explored in the present study perfect jetting is found to occur. The injection pressure in this case is 30 kgf/cm2. The initial expansion angle of jet increases with increasing gas-flow velocity and agrees well with theoretical calculation. From this, it is presumed that the speed of a gas jet which is equal to the sonic velocity at the exit of the orifice exceeds the sonic velocity just beyond the exit.
Readers Who Read This Article Also Read
Tetsu-to-Hagané Vol.68(1982), No.1
Tetsu-to-Hagané Vol.68(1982), No.1
Thermal Stress Formula for Estimation of Spalling Strength of Rectangular Refractories
Ichiro KATO, Yoshiyasu MORITA, Fuminori HIKAMI
pp. 105-112
Abstract
For the purpose of designing a long life furnaces, much efforts toward preventing thermal spalling attack of inner lining refractories have been made. The present study has been undertaken to investigate the quantitative effect of the size, heating conditions, and external constrains on the thermal stresses in duced in a rectangular refractory heated from one end.
The main results obtained are as follows :
1) According to the result of F.E.M. calculations, a large tensile stress (σz) perpendicular to the hot face which may cause thermal spalling cracking is induced along the center axis of a refractory heated from one end.
2) σz can be well approximated by the sum of two 2-dim. solutions, each corresponding to the analysis on the x-z plane and y-z plane.
3) The maximum thermal stress (σMZ) perpendicular to the hot face is approximately obtained using nondimensional functions Hstress, Hstrain, which are monotonously increasing functions.
σMZ≅α ·E · T{ζx·Hstress (a /√ kt) + ζy · Hstrain (b/:√ kt) }
Here, α : Thermal expansion coefficient, E : Young's Modulus, T: Temperature of hot face, a, b : widths of hot face, k : thermal diffusivity, t : elapsed time, ζx, ζz : parameters representing external constrains.
Through this Eq. effects of sizes, heating condition, external constraints on the thermal spalling can be obtained quantitatively. It also explains the experimental results fairly well.
Reaction between S35C and Liquid Zinc
Hideto KOGA, Yasuo UCHIYAMA, Kosuke TSUCHIDA
pp. 113-119
Abstract
To study the effect of alloying element in steel on the reaction between solid iron and liquid zinc, S35C samples were immersed into pure molten zinc for 60-6 000 s in the temperature range of 713 K-873 K. Structure and thickness of alloy layers were examined. Iron mass loss, iron dissolved into the zinc bath and iron remained in the alloy layer, were measured. The results are as follows :
(1) The alloy layer consists mainly of (i) ζ layer at 713 K-753 K, (ii) (δ1+η) mixture layer at 773 K-813 K, and (iii) δ1, layer at 833 K-873 K. In the alloy layer, rows of Fe3ZnC particles are found in the direction perpendicular to the steel/alloy layer interface.
(2) In the temperature range of above-mentioned (i) and (ii), the alloy layer thickness decreases as immersion temperature increases. In these temperature range, the alloy layer contains liquid zinc and grows faster.
(3) Iron remained in the alloy layer depends on the alloy layer phase, and iron dissolved into the zinc bath depends on the "drop off" of the alloy layer. The total loss of iron in determined by combination of these two reactions with zinc depending on immersion temperature.
(4) Though alloying elements in steel do not affect the Fe-Zn reaction in the temperature range of 773 K-873 K, they affect the formation and growth of the ζ layer and make the Fe-Zn reaction active below 753 K.
Readers Who Read This Article Also Read
ISIJ International Vol.39(1999), No.4
Tetsu-to-Hagané Vol.71(1985), No.2
Tetsu-to-Hagané Vol.70(1984), No.5
Effect of Hot Corrosion on the Creep Rupture Properties of a Nickel-Base Superalloy
Masayuki YOSHIBA, Ohmi MIYAGAWA, Tsuneaki SAKAKI, Dai FUJISHIRO
pp. 120-129
Abstract
The creep rupture tests of a nickel-base superalloy Inconel 751 were carried out at 800°C in static air for the specimens with or without coating of synthetic ash mixture composed of 90% Na2SO4 plus 10% NaCl and the effect of hot corrosion on the creep rupture properties was investigated.
In ash-coated specimens the rupture strength was extremely low and showed large difference from each other. The rupture ductility also lowered remarkably as a result of brittle fracture mode due to hot corrosion.
The creep fracture of specimens without coating of ash mixture occurred as a result of the growth and the coalescence of a large number of grain boundary cracks, as usually observed. In ash-coated specimens, on the other hand, only a few aggressive intergranular penetration of sulfides, which had already initiated during apparent a steady-state creep stage, opened in an accelerated creep stage, propagated rapidly as a main crack and consequently a premature fracture resulted in. These results indicate that hot corrosion could essentially alter the creep fracture mechanism.
From the observation of the density and the length of aggressive intergranular penetrations existing in ruptured or unruptured specimens, it was also suggested that in hot corrosive environment the rupture life of Inconel 751 was mostly determined by the initiating process of only a few aggressive intergranular penetration.
Hot Corrosion Behavior of Intermetallic Compounds of Ni-Al System in Fused 75% Na2SO4-25% NaCl Salt
Ken-ichi ONISAWA, Mitsuo CHIGASAKI, Ko SOENO
pp. 130-139
Abstract
Hot corrosion behavior of intermetallic compounds NiAl, Ni3Al, Ni3(Al, Ti) and NiAl+Cr in a fused 75% Na2SO4-25% NaCl salt has been investigated in the temperature range from 700° to 1 000°C in comparison with that of Ni and Ni-base superalloy IN-738LC.
The results obtained are as follows :
(1) The corrosion loss in weight of Ni3Al and Ni3(Al, Ti) is much larger than that of NiAl, Ni and IN738LC. For NiAl and IN-738LC, the peak of corrosion loss is observed at 800°C.
(2) Oxide layers such as α-Al2O3 and Cr2O3 formed on the surface of NiAl and IN-738LC above 850°C cause a decrease of corrosion loss. These oxides, however, are not protective completely, and the internal degradation such as oxidation and sulfidation is observed.
(3) On the surface of NiAl+ (2040) % Cr, α-Al2O3 forms even at a low temperature (700°C) and restrains the permeation of the fused salt especially the sulfur into the specimens so that the corrosion loss and the internal degradation is reduced.
Effect of Hardness and Hydrogen Concentration on Critical Stress of Cold Cracking in Welded Joint
Toshio TERASAKI, Kunihiko SATOH
pp. 140-146
Abstract
The implant cold cracking test has been made to investigate the effect of the residual diffusible hydrogen content, which remained in the specimen subjected to thermal cycle, and the maximum hardness in the neighbourhood of fusion boundary in heat affected zone on the critical stress of weld cold cracking. The relation between critical stresses and the common logarithm of residual diffusible hydrogen content was indicated by two straight lines. When the residual hydrogen became under 2 ppm, the change of hydrogen content effected extremely on the critical stress. However, when the residual hydrogen became above 3 ppm, the change had some influence on the critical stress. When the residual diffusible hydrogen con tent remained unchangeable, the critical stress was related with the linear equation of the maximum hardness. Equations for estimation of the critical stress of the cold cracking were derived from the maximum hardness, cooling time and fused metal hydrogen content.
Influence of Macro Non-metallic Inclusions on Flanging Cracks of Drawn and Ironed Can
Kazunaga MISONOH, Teruaki FUJII, Ryoichi FUKUMOTO, Atsushi NAKAJIMA
pp. 147-154
Abstract
In the manufacture of DI can made of tinplate, macro non-metallic inclusions(NMIs) which exist on the flanging area of DI can cause cracks in flanging. It is difficult to observe NMIs on the surface of tinplate because they usually exist in the inner part of the steel sheet. The magnetic-particle testing can detect NMIs, but it is difficult to determined the size of NMIs quantitatively.
This paper describes the quantitative determination of the size of NMIs by using the magnetic leakage flux testing, and the influence of NMIs on the flanging cracks. Flanging crack ratio in continuous DI canmaking test are in proportion to numbers of NMIs obtained in this test is in good agreement with the theoretical results. Conclusively, the number of NMIs per unit area detected on the part of the coil by the magnetic leakage flux testing enable us to estimate the flanging crack ratio of the coil before DI canmaking.
Readers Who Read This Article Also Read
Tetsu-to-Hagané Vol.67(1981), No.8
Tetsu-to-Hagané Vol.70(1984), No.4
Tetsu-to-Hagané Vol.75(1989), No.8
Development of Automatic Jominy Test Apparatus
Masakatsu UENO, Katsuji NAKAMURA, Kametaro ITO, Hiroyuki MINEMATSU
pp. 155-161
Abstract
A full-automatic-Jominy test apparatus has been developed, the characteristics of which are as follows :
(1) Adoption of the smaller test specimen (conventional : 25 mm new-type : 10 mm), which enables application of Jominy test method to the thinner products so far extremely difficult.
(2) Adoption of induction heating method, resulting in rapid heating rate so far unattainable.
(3) Adoption of the present control system, by which desired heating pattern simulating the actual heating conditions can be obtained.
(4) Adoption of the full-automatic sequence control system, by which end-quench test for harden-ability of steel can be carried out without an operator.
In this article, the details of development and characteristics of the new-type Jominy test apparatus are shown.
State Analysis of Ca in Steel by Electrochemical Separation Technique
Yoshio YOSHIDA, Yoshiko FUNAHASHI, Yoshikazu KAMINO
pp. 162-171
Abstract
An investigation has been made on the electrochemical behavior of various compounds as non-metallic inclusion in steel, in order to separate calcium sulfide from calcium oxide.
A method developed for the state analysis of Ca in steel, was summerized as follows : (1) Ca as inclusion : Steel sample is dissolved electrolytically in the methanol solution containing 3% methyl salicylate, 1% salicylic acid and 1% tetramethylammonium chloride, and the amount of Ca in the obtained electrolytic residue is determined. (2) Ca dissolved in steel : Calculated by subtracting the amount of Ca as inclusion from total amount of Ca in steel. (3) Ca as oxide : Electrolytically extracted residue from steel is mixed with Cu powder, and pressed into a disk. The disk was electrolysed in the methanol solution containing 10% acetylacetone and 1% tetramethylammonium chloride, and the amount of Ca in the insoluble residue is determined. Fe3C and MnS extracted from steel are decomposed by this secondary electrolysis procedure. (4) Ca as sulfide : Calculated by subtracting the amount of Ca as oxide from the amount of Ca as inclusion.
Readers Who Read This Article Also Read
Tetsu-to-Hagané Vol.49(1963), No.14
Tetsu-to-Hagané Vol.69(1983), No.6
Tetsu-to-Hagané Vol.69(1983), No.10
Ironmaking and Metallurgical Education in the Later Tokugawa Regime
Morito NAKAZAWA
pp. 172-177
Quality of the Ancient Iron Sword, Shichishi-To
Minoru SASAKI
pp. 178-184
Readers Who Read This Article Also Read
Tetsu-to-Hagané Vol.67(1981), No.1
Tetsu-to-Hagané Vol.71(1985), No.2
Tetsu-to-Hagané Vol.70(1984), No.7
Article Access Ranking
06 Sep. (Last 30 Days)
-
Perspectives on the Promising Pathways to Zero Carbon Emissions in the Steel Industry toward 2050
ISIJ International Vol.65(2025), No.2
-
Growth, Removal, and Agglomeration of Various Type of Oxide Inclusions in Molten Steel
Tetsu-to-Hagané Vol.111(2025), No.11
-
Finite Element Analysis of Bubble Growth and Particle Swelling during Coal Pyrolysis
ISIJ International Vol.65(2025), No.9
-
Interface behavior leading to Al/Cu dissimilar metal bonding formation with high-speed eutectic reaction induced by applying current
QUARTERLY JOURNAL OF THE JAPAN WELDING SOCIETY Vol.43(2025), No.2
-
Corrosion Behavior of Carbon Steel under Soil Drying Conditions
ISIJ International Advance Publication
-
Cold Spot Joining of 980 MPa-class Ultra-high Strength Steel
Tetsu-to-Hagané Advance Publication
-
Combination Effect of Premixing Conditions and Iron Ore Size Distribution in Sintered Ore Granulation Process with Intensive Mixer
ISIJ International Advance Publication
-
A preliminary study on reduction degradation of iron ore sinter using sinter analogue and X-ray micro-computed tomography (MCT)
ISIJ International Advance Publication
-
Copper removal of liquid steel containing 0.25 % carbon using Fe2O3-CaCl2-SiO2 flux
ISIJ International Advance Publication
-
Evaluation of Feature Selection Methods for Oxygen Supply Prediction in BOF Steelmaking
ISIJ International Advance Publication
You can use this feature after you logged into the site.
Please click the button below.