- TOP
- Tetsu-to-Hagané
- Vol. 47 (1961), No. 5
Tetsu-to-Hagané Vol. 47 (1961), No. 5
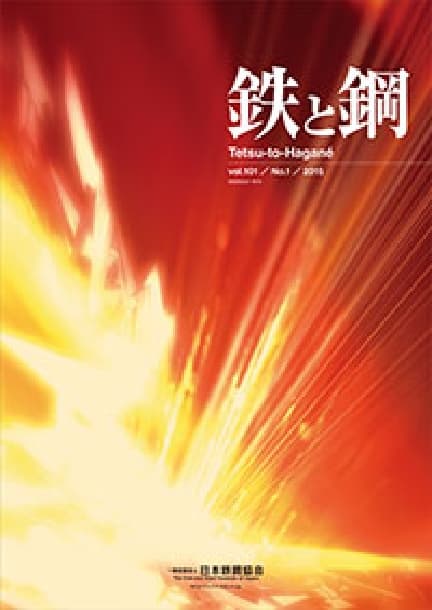
Grid List Abstracts
ONLINE ISSN: | 1883-2954 |
PRINT ISSN: | 0021-1575 |
Publisher: | The Iron and Steel Institute of Japan |
Backnumber
-
Vol. 111 (2025)
-
Vol. 110 (2024)
-
Vol. 109 (2023)
-
Vol. 108 (2022)
-
Vol. 107 (2021)
-
Vol. 106 (2020)
-
Vol. 105 (2019)
-
Vol. 104 (2018)
-
Vol. 103 (2017)
-
Vol. 102 (2016)
-
Vol. 101 (2015)
-
Vol. 100 (2014)
-
Vol. 99 (2013)
-
Vol. 98 (2012)
-
Vol. 97 (2011)
-
Vol. 96 (2010)
-
Vol. 95 (2009)
-
Vol. 94 (2008)
-
Vol. 93 (2007)
-
Vol. 92 (2006)
-
Vol. 91 (2005)
-
Vol. 90 (2004)
-
Vol. 89 (2003)
-
Vol. 88 (2002)
-
Vol. 87 (2001)
-
Vol. 86 (2000)
-
Vol. 85 (1999)
-
Vol. 84 (1998)
-
Vol. 83 (1997)
-
Vol. 82 (1996)
-
Vol. 81 (1995)
-
Vol. 80 (1994)
-
Vol. 79 (1993)
-
Vol. 78 (1992)
-
Vol. 77 (1991)
-
Vol. 76 (1990)
-
Vol. 75 (1989)
-
Vol. 74 (1988)
-
Vol. 73 (1987)
-
Vol. 72 (1986)
-
Vol. 71 (1985)
-
Vol. 70 (1984)
-
Vol. 69 (1983)
-
Vol. 68 (1982)
-
Vol. 67 (1981)
-
Vol. 66 (1980)
-
Vol. 65 (1979)
-
Vol. 64 (1978)
-
Vol. 63 (1977)
-
Vol. 62 (1976)
-
Vol. 61 (1975)
-
Vol. 60 (1974)
-
Vol. 59 (1973)
-
Vol. 58 (1972)
-
Vol. 57 (1971)
-
Vol. 56 (1970)
-
Vol. 55 (1969)
-
Vol. 54 (1968)
-
Vol. 53 (1967)
-
Vol. 52 (1966)
-
Vol. 51 (1965)
-
Vol. 50 (1964)
-
Vol. 49 (1963)
-
Vol. 48 (1962)
-
Vol. 47 (1961)
-
Vol. 46 (1960)
-
Vol. 45 (1959)
-
Vol. 44 (1958)
-
Vol. 43 (1957)
-
Vol. 42 (1956)
-
Vol. 41 (1955)
Keyword Ranking
29 Aug. (Last 30 Days)
Tetsu-to-Hagané Vol. 47 (1961), No. 5
Heat Transfer during the Sintering Process
Koji SANBONGI, Nobunao NISHIDA
pp. 687-692
Abstract
By charging a small sintering pan with Goa hematite or Larap magnetite as raw materials, the speed of heat transfer in non-sintered or sintered layers Were measured and the following results were obtained:
i) Difference between the heat front speed in non-sintered layers, which were very slow, and the flame front speed were more increased with increase of the air flow through the bed.
ii) There was a small difference between the heat front speed in sintered layers, which were more rapid than that in non-sintered layers, and the flame front speed.
iii) When the difference between the heat front speed in non-sintered layers and the flame front speed were large, the temperatures of combustion zones rose slowly. On the contrary, in the case when that difference between the heat front speed in sintered layers and the flame front speed were large, the temperature of combustion zone dropped slowly.
Readers Who Read This Article Also Read
Tetsu-to-Hagané Vol.49(1963), No.7
Tetsu-to-Hagané Vol.48(1962), No.12
Tetsu-to-Hagané Vol.48(1962), No.1
On Gas Contents in Molten Slag
Yoshihiko ABE
pp. 693-698
Abstract
When behaviors of gases in molten steel on steelmaking practice is studied, the knowledge of molten slag has an important role.Based on this information, in this paper the author studied the variations of hydrogen content and the total iron oxide content in molten slag with different water-vapor pressures in air.
Then, as hydrogen content in molten slag could be determined by vacuum-fusion method which consisted in heating the sample at 1450-1500°C in a Mo crucible, the author firstly experimented the relations of gas contents in synthetic slag and the water-vapor pressure in atmosphere in equilibrium state, and led the following conclusions on both slag of basic highfrequency heat and slag of basic electric heat.
1) Hydrogen content in slag just before tap is proportional to the square root of the water-vapor pressure in air, but not to the hydrogen pressure in air.
2) Hydrogen content in slag is increased with rising CaO/SiO2 ratio in slag, and its increasz ratio becomes gradually larger when the water-vapor pressure in air is higher.
3) Hydrogen content in slag becomes gradually smaller when bath temperature is higher.
4) Total iron oxide content in slag just before tap is proportional to the water-vapor pressure in air, and is not influenced by the composition of slag and by the bath temperature.
The Influence of Cementite Particle Dispersion on the Strength Indices of Tempered Carbon Steels
Genjiro MIMA
pp. 699-706
Abstract
The relationships between strength indices (yield strength, tensile strength and hardness) and parameters of microstructure in two commercial plain carbon martensitic steels (0.7% and 1. 1% C) have been studied after varying isothermal tempering treatments at 690°C.
The size-frequency distributions of cementite particle diameter on a polished cross-sections of the specimens which tempered at 690°C for various periods of time (6mn. to 400h) and the number of ferrite grains per unit area for the specimens after times in excess of 10h have been measured by the use of an optical and an electron-microscope, and from these results, the mean diameter of cementite particles, the mean free ferrite paths, and the ferrite grain size of the specimens after 10h or longer tempering.
The various relationship which have been proposed between parameters of the microstructure and strength indices are confirmed with the present data. The results which were confirmed the linearity of the relationship derived by Gensamer and co-workers are showed a fairly large experimental scatter and the reverse-(Japanese He) type curve. The strength indices as a function of the mean diameter of cementite particles have been shown the discontinuity at the corresponding values for the tempering time between 1h and 3h. From the present results, it is suggested that the strength indices of the tempered steel containing non-coherent particles of cementite depend upon the development of minute ferrite grains which are bound by the low energy boundary, the transition from the construction of low energy boundary to that of ordinary grain boundary, and the growth of ferrite grains whichare bounded by the ordinary boundary.
On the Configuration of Titanium Sulphide in Steels
Toshio SAITO
pp. 707-714
Abstract
Effect of Ti/S ratio on the distribution, shape and structure of titanium sulphide in steel were studied. In Ti/S ratio range less than 0.35, sulphide inclusions in cast steels were randomly distributed in globular shapes and had a wide range of sizes as type I. At about 0.5 Ti/S ratio, they appeared on primery grain boundaries as type II, and in Ti/S ratio range over 1.3, they were formed as Fe-TiS eutectic as type II. FeS films in caststeels were changed in to globular shapes by addition of titanium. These were explained by solution of titanium sulphides in FeS. Thus, the low melting point of FeS were raised and the hot warkability of steels were improved by solution of titanium sulphides.
Titanium sulphides appeared pink-gray globular shapes in microscopic light field. Thier particles were about 0.3-0.5μ size, but grown up to about 3.5μ size or changed into a rod shape in accordance with solubilities of other inclusions, such as nitrides or oxides. It was considered that titanium carbides were primarily formed and secondarily titanium sulphides, and then titanium nitrides and titanium oxides were formed in the process of solidification of titanium steels. This order was contrary for heat formation of each titanium compound, and, in particle size of each inclusions, titanium carbides were of the most fine particle and suc-cessively followe din size titanium sulphides, nitrides and oxides. It was confirmed that titanium sulphides in steels were TiS and the structure were of a hexagonal B 8 modified type as dete-rmined by X-ray diffraction methods of residues.
Readers Who Read This Article Also Read
Tetsu-to-Hagané Vol.44(1958), No.6
Tetsu-to-Hagané Vol.47(1961), No.7
Tetsu-to-Hagané Vol.48(1962), No.13
Study of Degassing from Iron-Base and Nickel-Base Alloys Containing Chromium by Vacuum-Induction Melting
Masao KAWAHATA, Tetsuya WATANABE
pp. 715-720
Abstract
The growing interest in vacuum melting for production of alloys has promoted investigation of the variables in the process. One of the advantage of vacuum melting is the opportunity for reduction of oxygen content of the melt by the use of hydrogen or carbon, and reaction products of those are gas phases. This investigation dealt with the carbon-and hydrogen refining phases of the process in vacuum induction melting of iron-base and nickelbase alloys containing 0-20% chromium which are major composition of heat-resisting steel. Attainable limit of gas content in vacuum melting has also been investigated with standard commercial alloys, AISI type 304 and Inconel.
Electrolytic materials weighting about 2 to 5kg were melted in an Al203 crucible by using a laboratory-scale vacuum induction apparatus.
In the case of carbon reduction, 0-0.30% of granular graphite was added into the melt after the charge had been completely melted down, and the melt which was kept in vacuum during an hour for boiling and degassing.
In the case of hydrogen reduction, the melt was impinged for an hour with a stream of dry hydrogen, the dew point of which was varied in a range from -30°C to-70°C. During deoxidation processes of both cases, the molten metal was kept at 1570-1620°C.
Results were as follows:
1. Attainable oxygen level in nickel-base alloy was considered to be lower than in ironbase alloy in any reduction practice. The amount of oxygen attainable after reduction practice was increased by addition of chromium.
2. The oxygen and the nitrogen of standard commercial alloys finally attained by carbon treatment were respectively below 0.0010% and 0.0030% which were some tenths of hose by the conventional method.
3. Deoxidation by dry hydrogen was incapable for reducing oxygen content in the alloys and metals except in pure nickel regardless of the dew point of hydrogen used.
4. The oxygen and nitrogen values obtained experimentally were extremely higher than the equilibrium values theoritically calculated. Therefore it may be presumed that, regarding the degassing by vacuum induction melting, the process of CO gas bubble formation and crucible reaction should be studied in conjunction with a study of the phenomenon from the kinetic point of view.
Effect of Deformation Temperature on Anneal-Hardening of Type 304L Stainless Steel
Yuzo HOSOI
pp. 721-727
Abstract
The relation between deformation temperature and anneal-hardening of type 304L stainless steel was investigated. Specimens were rolled at several temperatures ranging between -60° and 600°C and subsequently annealed up to 900°C.Amount of anneal-hardening was estimated by measuring the change of mechanical properties.
The results were summarized as follows:
(1) Anneal-hardening occured at 400-500°C before recrystallization when specimens were rolled at a deformation temperature below 600°C and subsequently annealed. Amount of anneal-hardening was increased with falling deformation temperatures. The specimen deformed at 600°C did not show any hardening phenomenon during annealing.
(2) Retrogression phenomenon was observed with the specimen anneal-hardened at 400°C after 38% deformation at -60°C. It was presumed that the mechanism of anneal-hardening of type 304L stainless steel was very similar to that of α-brass in consideration of this retrogression phenomenon.
(3) Sub-boundaries were formed with the specimens anneal-hardened. It seemed that one of the causes of anneal-hardening in this steel was also attributable to a formation of subboundaries.
(4) By measuring magnetic properties of the deformed specimens, it was estimated that Md point of the steel used was about 45°C.
(5) In microstructure of the deformed specimens, many parallel stripes were observed in some of grains. These stripes were increased as the degree of deformation was increased and as the deformation temperature was decreased. It was presumed that this structure was a mixed structure of martensite and strain-marking in the case of specimens deformed at a temperature below Md, whereas it was a strain-marking in the case of specimens deformed at a temperature above Md.
Effect of Al, Al+Ti and W+V+Nb on Properties of Heat-Resisting 38% Ni Alloy
Sadao KOSHIBA, Tsuneo KUNOU, Shin KIMURA
pp. 727-733
Abstract
In the previous study (Tetsu-to-Hagané, Vol.44, 1960, No.4, pp.487-492) the authors reported the effect of Mo, W, V and Nb on properties of heat-resisting 38% Ni alloy. In the present paper, the effect of Al, Al+Ti and W+V+Nb on the hardness as solution-treated and aged, mechanical properties at room temperature and high temperature, rupture strength, oxidation resistance and resultant microstructures were examined.
At the same time, precipitates therein were isolated by electrolysis so as to examine the quality and the form of them.
The results obtained were as follows:
(1) With the alloy containing 0.7-2.32%Al, as the Al was increased, hardness after solution treatment, aging hardness, tensile strength at room temperature and high temperature, rupture strength and oxidation resistance were increased, while the elongation, reduction of area and Charpy impact value were decreased.
(2) As concerns the effect of Al+Ti, the hardness and strength at high temperature were increased. However, the toughness was decreased as the Ti content was increased, when the sum of Al and Ti was constant. The effect of Ti, therefore, was more sensitive than that of Al.
(3) With respect to the influence of W+V+Nb, Nb was most effective, when the alloy contained Nb together with W and V; and by increasing the Nb content, the strength at high temperature was improved. When the V was compared with W, addition of V was better than that of W for raising the strength at high temperature.
Tour of Inspections of Researches on Plastic Working of Metals in Europe and America.(II)
Seita SAKUI
pp. 758-768
Readers Who Read This Article Also Read
Tetsu-to-Hagané Vol.49(1963), No.7
Tetsu-to-Hagané Vol.48(1962), No.12
Tetsu-to-Hagané Vol.48(1962), No.1
Article Access Ranking
29 Aug. (Last 30 Days)
-
Perspectives on the Promising Pathways to Zero Carbon Emissions in the Steel Industry toward 2050
ISIJ International Vol.65(2025), No.2
-
Growth, Removal, and Agglomeration of Various Type of Oxide Inclusions in Molten Steel
Tetsu-to-Hagané Vol.111(2025), No.11
-
Copper removal of liquid steel containing 0.25 % carbon using Fe2O3-CaCl2-SiO2 flux
ISIJ International Advance Publication
-
Finite Element Analysis of Bubble Growth and Particle Swelling during Coal Pyrolysis
ISIJ International Vol.65(2025), No.9
-
Corrosion Behavior of Carbon Steel under Soil Drying Conditions
ISIJ International Advance Publication
-
Cold Spot Joining of 980 MPa-class Ultra-high Strength Steel
Tetsu-to-Hagané Advance Publication
-
Factors Affecting Generation of Iron Fines in Cold Sheet Rolling of Steel
ISIJ International Vol.65(2025), No.9
-
Experimental Study on Heat Transfer Characteristics of a Moving Single-Nozzle Jet Impingement
ISIJ International Vol.65(2025), No.9
-
Combination Effect of Premixing Conditions and Iron Ore Size Distribution in Sintered Ore Granulation Process with Intensive Mixer
ISIJ International Advance Publication
-
Evaluation of Feature Selection Methods for Oxygen Supply Prediction in BOF Steelmaking
ISIJ International Advance Publication
You can use this feature after you logged into the site.
Please click the button below.