- TOP
- Tetsu-to-Hagané
- Vol. 49 (1963), No. 11
Tetsu-to-Hagané Vol. 49 (1963), No. 11
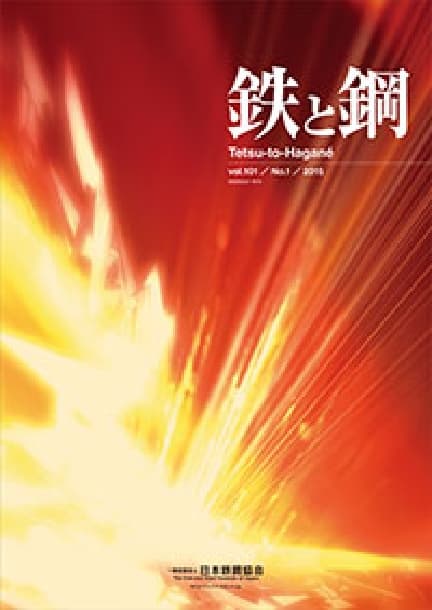
Grid List Abstracts
ONLINE ISSN: | 1883-2954 |
PRINT ISSN: | 0021-1575 |
Publisher: | The Iron and Steel Institute of Japan |
Backnumber
-
Vol. 111 (2025)
-
Vol. 110 (2024)
-
Vol. 109 (2023)
-
Vol. 108 (2022)
-
Vol. 107 (2021)
-
Vol. 106 (2020)
-
Vol. 105 (2019)
-
Vol. 104 (2018)
-
Vol. 103 (2017)
-
Vol. 102 (2016)
-
Vol. 101 (2015)
-
Vol. 100 (2014)
-
Vol. 99 (2013)
-
Vol. 98 (2012)
-
Vol. 97 (2011)
-
Vol. 96 (2010)
-
Vol. 95 (2009)
-
Vol. 94 (2008)
-
Vol. 93 (2007)
-
Vol. 92 (2006)
-
Vol. 91 (2005)
-
Vol. 90 (2004)
-
Vol. 89 (2003)
-
Vol. 88 (2002)
-
Vol. 87 (2001)
-
Vol. 86 (2000)
-
Vol. 85 (1999)
-
Vol. 84 (1998)
-
Vol. 83 (1997)
-
Vol. 82 (1996)
-
Vol. 81 (1995)
-
Vol. 80 (1994)
-
Vol. 79 (1993)
-
Vol. 78 (1992)
-
Vol. 77 (1991)
-
Vol. 76 (1990)
-
Vol. 75 (1989)
-
Vol. 74 (1988)
-
Vol. 73 (1987)
-
Vol. 72 (1986)
-
Vol. 71 (1985)
-
Vol. 70 (1984)
-
Vol. 69 (1983)
-
Vol. 68 (1982)
-
Vol. 67 (1981)
-
Vol. 66 (1980)
-
Vol. 65 (1979)
-
Vol. 64 (1978)
-
Vol. 63 (1977)
-
Vol. 62 (1976)
-
Vol. 61 (1975)
-
Vol. 60 (1974)
-
Vol. 59 (1973)
-
Vol. 58 (1972)
-
Vol. 57 (1971)
-
Vol. 56 (1970)
-
Vol. 55 (1969)
-
Vol. 54 (1968)
-
Vol. 53 (1967)
-
Vol. 52 (1966)
-
Vol. 51 (1965)
-
Vol. 50 (1964)
-
Vol. 49 (1963)
-
Vol. 48 (1962)
-
Vol. 47 (1961)
-
Vol. 46 (1960)
-
Vol. 45 (1959)
-
Vol. 44 (1958)
-
Vol. 43 (1957)
-
Vol. 42 (1956)
-
Vol. 41 (1955)
Keyword Ranking
29 Aug. (Last 30 Days)
Tetsu-to-Hagané Vol. 49 (1963), No. 11
Influence of Ore Size and Contact Time on Ore Reduction
Tanekazu SOMA
pp. 1645-1651
Abstract
With the progress in blast furnaces and direct methods of steel making, it has become necessary to make clear the mechanism of are reduction in bed. There are few data available for calculation of the reduction speed.
Thereupon the auther measured the reduction speed of are bed under the following conditions;
Temperature: 900°C
Ore: Self-fluxing sinter, Indian ore and Korean ore,
Weight: 200, 100, 50, 25, 12·5g.
Size: 1-2·5, 2·5-5, 5-10, 10-20, 20mm up
Bed; Dia: 4, 27, 20mm.
Thick: About 5, 10, 20, 40, 80mm.
Reducing gas. ; CO flow 0·25, 0·5, 1, 2, 3·2 Nl/mn.
N2 0, 70%. CO2 0, 10, 20%.
(The italics indicate the standard conditions.)
To indicate the reduction speed, it is advantageous to use “Reduction degree-CO2/ (CO+CO2) curve” for each contact time. At equilibrium, this curve has the steps whose heights indicate CO2/ (CO+CO2) of the equilibrium mixture over Fe-FeO, FeO-Fe3O4, and Fe3O4-Fe2O3.
At any contact time, the curve deviates lower than these steps. With charging are size and contact time, this curve follows the relation of potential function. At the same contact time, this curve is slightly affected by gas speed. But when its speed exceeds a certain value, the curve seems to be little affected by the speed.
Even with CO+N2 mixed gas, these relations hold. CO2 in CO gas little affects these relations in the range of 20% and at the contact time 0·23 second.
Readers Who Read This Article Also Read
Tetsu-to-Hagané Vol.49(1963), No.11
Tetsu-to-Hagané Vol.49(1963), No.12
Tetsu-to-Hagané Vol.50(1964), No.5
Dissolution Velocity of Oxygen from H2O-Ar Atmosphere into Molten Iron
Koin ITO, Kokichi SANO
pp. 1652-1658
Abstract
In order to study the kinetics of reaction between atmosphere and molten iron, we investigated the rate and mechanism of oxygen dissolution from H2O-Ar atmospheres into molten iron. Results are as follows:
The mechanism of reaction is supposed to occur in three steps. At first, H2O molecules from the atmosphere diffuse on the gas/molten iron interface, and the diffusion rate equation may be expected to be dm/dt=DmFM (PH2O-PH2Oi) /δG (1). At the gas/molten iron interface, the chemical equilibrium, H2O (g) =H2 (g) +O, is always attained. At the last step, O diffuses from the surface of molten iron into the core, and the corresponding equation may be dm/dt =DLFρ ([O] i- [O]) /VδL (3). When Eq. (1) is larger than Eq. (3), O is accumulated on the surface of molten iron and an oxide layer forms.
On the basis of the kinetic theory of gas molecules, it was confirmed that the chemical reaction between H2O and Fe hardly proceeded in a gaseous phase of the lack of Fe vapor, and it was supposed that the chemical reaction took place only at the gas/molten iron interface.
Experimental data seem to show that the rate determining step of the reaction is the diffusion of H2O through the diffusion layer in the gaseous phase at the gas/molten iron interface in cases where no oxide laye-rs appear at the surface of molten iron. In these cases, the rate of reaction is approximately proportional to the partial pressure of H2O in atmosphere. When an oxide layer appears on the surface of molten iron, the reaction becomes one of gas/slag/molten iron and the rate determining step is the transport of O from the surface of molten iron into the core.
Readers Who Read This Article Also Read
Tetsu-to-Hagané Vol.49(1963), No.11
Tetsu-to-Hagané Vol.49(1963), No.12
Tetsu-to-Hagané Vol.50(1964), No.5
Application of the Quick Immersion Technique for Temperature Measurement of Steel Bath in Ladle
Shinsaku ONODERA, Yutaka ARAKIDA, Noboru HIRAOKA
pp. 1658-1662
Abstract
Much data of measurements by the continuous immersion pyrometry in the steel making process are treated by the statistical method. It is shown that a considerable scattering exists in the values of temperature drop from tapping to pouring. So it would be difficult to predict the bath temperature at certain time from the tapping temperature only. This scattering is produced mainly by the tapping operation. The quick immersion technique in ladle is developed as a supplementary method to the continuous immersion pyrometry. The results obtained by this technique support our previous conclusions.
On Non-metallic Inclusions and Their Distributions in Low Carbon Rimmed Steel Ingots by Slime Method
Kozo MORINAGA, Atsushi OBA, Yukiyoshi ITOH
pp. 1663-1668
Abstract
From the metallurgical point of view, it is important to make clear the relation between the distribution of inclusions in rimmed steel ingots and the rimming action of the liquid steel in the mold. With the object of investigating on inclusions in rimmed steel ingot, the liquid steel in a ladle was teemed into two 15t ingot molds, with varied addition of aluminum in the mold. Inclusions in these ingots were extracted by the electrolytic procedure-the slime method, and their quantities, distribution, compositions and microstructures were investigated. From the core of the ingots, many small duplex inclusions of MnS (FeS) and MnO (FeO) were extracted. Inclusions extracted from the bottom are of rather larger size and contain higher Al2O3 and SiO2. Comparing the quantities and distributions of inclusions in the two ingots, the duplex inclusions in the core are distributed more uniformly in the ingot added with more aluminum in the mold, but the larger inclusions in the bottom increase.
Readers Who Read This Article Also Read
Tetsu-to-Hagané Vol.49(1963), No.2
Tetsu-to-Hagané Vol.54(1968), No.9
Tetsu-to-Hagané Vol.53(1967), No.7
On the Interior Temperature Distribution of Ingots during Heating Process
Takahiro HARA
pp. 1669-1675
Abstract
When high-carbon steel or high-carbon-chromium steel ingots of comparatively large size are heated in a reheating furnace, cracks are often observed in their inside.
Author has studied experimentally and theoretically the conditions under which these ingots develop cracks under thermal stress during the heating process. This report describes the method of calculating the interior temperature distribution in the ingots to calculate their internal thermal stress.
With steels, generally thermal properties (thermal conductivity, specific heat and total heat) will change with temperature, so it is not easy to calculate heat transmission briefly.
Thus considering these thermal properties he devised a finite-difference equation by which we can calculate the heat transmission with comparative ease. And he recognized that the calculated value thus obtained accords perfectly with the observed value in a reheating furnace.
The following facts have been discovered through this theoretical calculation;
(1) During the heating process of an ingot the temperature difference between surface and core (i. e. surface-center temperature difference) reaches a maximum when the ingot undergoes a transformation, because of the heat absorption for the transformation.
With low-carbon steels the surface-center temperature difference becomes greatest, long before the core of the ingot completes the transformation. But with high-carbon steels (especially with hypereutectoid steels) the surface-center temperature difference becomes greatest just before the time of completion of transformation.
(2) The maximum surface-center temperature difference at which the core of a highcarbon chromiun steel ingot completes the transformation is determined only by the mean surface temperature elevating rate within the transformation range. To control this temperature difference t he surface temperature elevating rate has only to be controlled in this transformation range.
A Study on a Continuous Wire Rod Rolling
Saburo DAZAI
pp. 1676-1681
Abstract
The continuous wire rod mill is the most progressive apparatus for high quality wire rod production considering the productivity, close tolerance of products and so forth. In this paper, some fundamental studies, which have been carried out in a mill plant, are treated on the conditions of continuous wire rod rolling.
In continuous wire rod rolling, any tension must be avoided between the adjacent stands as far as posssible. When a tension exerts in rolling, the wear of a roll pass decreases proportionally with the tension at the stand subjected to the forward pull, but it is not affected by it at the stand subjected to the backward pull. For a certain degree of tension the rolling torque and power consumption decrease at the stand subjected to the forward pull and increase at the stand subjected to the backward pull, but the sum of power consumptions of both stands is constant.
The deformation of materials in the roll pass is affected by many factors, particularly by the resistance to deformation of materials due to the temperature. For the oval pass the radius of curvature of the pass must be determined in the optimum range.
It is necessary to be careful about the rapid fall of the rolling temperature at a slow rolling speed. After rolling, the quality of materials is improved with selection of the adequate reeling temperature. To control this reeling temperature, the cooling guide tubes, which serve as the heat treating facilities, are satisfactorily installed.
Study on Improvement in the Hot Workability of High-Alloy Steels
Taira NAKANO, Hisashi TAKADA, Kiichi NARITA, Kazuyoshi UKIHASHI
pp. 1681-1686
Abstract
Stainless steels which acquire γ+a mixed structure at high temperature tend to crack during hot working, because the deformation by working concentrates upon the ferrite parts that have a small flow stress. To improve the hot workability of stainless steels of (γ+a) structure at high temperature, we have selected typical stainless steels of the duplex structure 20Cr-12Ni-2Mo, 20Cr-9Ni-0·9Nb and 24Gr-13Ni steel, and investigated the effect of high temperature homogenizing treatment, and addition of rare earth and nitrogen upon the hot workability of the ingot of these stainless steels by means of high temperature torsion test.
The results obtained are as follows:
(1) The high temperature homogenizing treatment is effective to improve the hot workability for all these steels tested, and above all, the effect upon 20Cr-12Ni-2Mo steel is remarkable. Homogenizing treatment at 1200°C for 50h is the best to improve the hot workability of these steels.
(2) The effect of rare earth (misch metal and lantan alloy) addition on the hot workability of these steels is recognized and an addition of 0·25% is the most effective.
The difference of hot workability among the tested steels is almost negligible, and lantan alloy addition is a little less effective than misch metal addition.
(3) The effect of nitrogen addition upon the hot workability for these steels is remarkable except 20Cr-12Ni-2Mo steel that naturally has little δ ferrite. However the weldability of the steel containing nitrogen is not good, therefore it is not advisable to make nitrogen addition to improve the hot workability of these steels, if good weldability is required.
Readers Who Read This Article Also Read
ISIJ International Vol.52(2012), No.6
Effect of Uranium on the Properties of Steel
Kiichi NARITA, Atsusi MIYAMOTO, Eiji TAKAHASHI
pp. 1686-1694
Abstract
The authors show that, up to approx. 0·2% addition, Uranium as an alloying element has little improving effect on the properties of carbon steel.
Uranium, however, can be used as a great effective deoxidizer or refiner of molten steel, improving the final deoxidation and the steel ingot-making procedures properly, because it has great affinities with oxygen and sulphur, and the specific gravities of it's oxides and sulphides are greater than that of molten steel.
For the practical application of uranium in steel making, the authors point out that it is necessary (1) to establish the detailed regulations for handling radioactive substances from the standpoint of practical operation, (2) to develop the method of uranium addition, (3) to clarify the chemical reaction between refractories and uranium, (4) to investigate the deoxidizing and desulphurizing reactions with uranium in molten steel and (5) to establish the manual on disposal and treatment of the refractories worn out, slag and steel scraps.
Influence of Nitrogen on Properties of 18-7 Stainless Steels
Masazo OKAMOTO, Ryohei TANAKA, Rokuro FUJIMOTO
pp. 1694-1700
Abstract
An experimental study was made on the influence of nitrogen content up to about 0·7% on the properties of 18%Cr-7%Ni stainless steels prepared by the high-pressure melting process in nitrogen atmosphere. Main results obtained were as follows.
1. It was necessary to heat for 1/2h at 1200°C for the solution-treatment of the steels with high nitrogen concentration. Stability of austenite to martensite transformation was markedly increased with an increasing nitrogen concentration in the steels; both Ms and Md were lowered considerably with an increasing nitrogen content. The Ms of the lowest nitrogen steel 1Mn-0·04N was found to exist at about 60°C, and the steel solution-quenched was found to contain a considerable amount of isothermal component of austenite-martensite transformation at room temperature.
2. During ageing at temperatures between 700°C and 900°C, peculiar lamellar precipitates consisting of chromium nitride and austenite depleted in both chromium and nitrogen appeared around the austenite grain boundaries due to the so-called grain boundary reaction.
It was often found that the depleted austenite, formed by the reaction described above, transforms into martensite during cooling from the ageing temperatures.
3. The strength increased markedly with an increasing nitrogen concentration, but in the steel with low nitrogen content higher strength was often obtained than in the steels of medium nitrogen content due to the martensitization of unstable austenite in the former steels either by subzero-treatment, by cold-rolling or even by plastic deformation during tensile tests. A good combination of tensile strength and elongation or reduction of area, however, was found to be obtained especially in the steels with high nitrogen concentration.
4. It was found from the high-temperature tensile creep-rupture test at 700°C that the highest value is obtained at the nitrogen concentration around 0·32%, while the creep-resistance is deteriorated by the higher nitrogen concentration in the steels.
Report of Inspection on the Iron and Steel Industry in West Europe
Tokushichi MISHIMA
pp. 1701-1713
特許記事
pp. 1738-1744
Readers Who Read This Article Also Read
Tetsu-to-Hagané Vol.49(1963), No.9
Tetsu-to-Hagané Vol.50(1964), No.3
Tetsu-to-Hagané Vol.50(1964), No.4
Article Access Ranking
29 Aug. (Last 30 Days)
-
Perspectives on the Promising Pathways to Zero Carbon Emissions in the Steel Industry toward 2050
ISIJ International Vol.65(2025), No.2
-
Growth, Removal, and Agglomeration of Various Type of Oxide Inclusions in Molten Steel
Tetsu-to-Hagané Vol.111(2025), No.11
-
Copper removal of liquid steel containing 0.25 % carbon using Fe2O3-CaCl2-SiO2 flux
ISIJ International Advance Publication
-
Finite Element Analysis of Bubble Growth and Particle Swelling during Coal Pyrolysis
ISIJ International Vol.65(2025), No.9
-
Corrosion Behavior of Carbon Steel under Soil Drying Conditions
ISIJ International Advance Publication
-
Cold Spot Joining of 980 MPa-class Ultra-high Strength Steel
Tetsu-to-Hagané Advance Publication
-
Factors Affecting Generation of Iron Fines in Cold Sheet Rolling of Steel
ISIJ International Vol.65(2025), No.9
-
Experimental Study on Heat Transfer Characteristics of a Moving Single-Nozzle Jet Impingement
ISIJ International Vol.65(2025), No.9
-
Combination Effect of Premixing Conditions and Iron Ore Size Distribution in Sintered Ore Granulation Process with Intensive Mixer
ISIJ International Advance Publication
-
Evaluation of Feature Selection Methods for Oxygen Supply Prediction in BOF Steelmaking
ISIJ International Advance Publication
You can use this feature after you logged into the site.
Please click the button below.