- TOP
- Tetsu-to-Hagané
- Vol. 77 (1991), No. 8
Tetsu-to-Hagané Vol. 77 (1991), No. 8
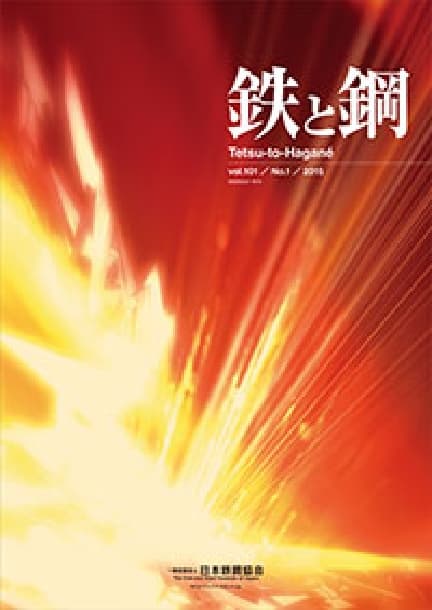
Grid List Abstracts
ONLINE ISSN: | 1883-2954 |
PRINT ISSN: | 0021-1575 |
Publisher: | The Iron and Steel Institute of Japan |
Backnumber
-
Vol. 111 (2025)
-
Vol. 110 (2024)
-
Vol. 109 (2023)
-
Vol. 108 (2022)
-
Vol. 107 (2021)
-
Vol. 106 (2020)
-
Vol. 105 (2019)
-
Vol. 104 (2018)
-
Vol. 103 (2017)
-
Vol. 102 (2016)
-
Vol. 101 (2015)
-
Vol. 100 (2014)
-
Vol. 99 (2013)
-
Vol. 98 (2012)
-
Vol. 97 (2011)
-
Vol. 96 (2010)
-
Vol. 95 (2009)
-
Vol. 94 (2008)
-
Vol. 93 (2007)
-
Vol. 92 (2006)
-
Vol. 91 (2005)
-
Vol. 90 (2004)
-
Vol. 89 (2003)
-
Vol. 88 (2002)
-
Vol. 87 (2001)
-
Vol. 86 (2000)
-
Vol. 85 (1999)
-
Vol. 84 (1998)
-
Vol. 83 (1997)
-
Vol. 82 (1996)
-
Vol. 81 (1995)
-
Vol. 80 (1994)
-
Vol. 79 (1993)
-
Vol. 78 (1992)
-
Vol. 77 (1991)
-
Vol. 76 (1990)
-
Vol. 75 (1989)
-
Vol. 74 (1988)
-
Vol. 73 (1987)
-
Vol. 72 (1986)
-
Vol. 71 (1985)
-
Vol. 70 (1984)
-
Vol. 69 (1983)
-
Vol. 68 (1982)
-
Vol. 67 (1981)
-
Vol. 66 (1980)
-
Vol. 65 (1979)
-
Vol. 64 (1978)
-
Vol. 63 (1977)
-
Vol. 62 (1976)
-
Vol. 61 (1975)
-
Vol. 60 (1974)
-
Vol. 59 (1973)
-
Vol. 58 (1972)
-
Vol. 57 (1971)
-
Vol. 56 (1970)
-
Vol. 55 (1969)
-
Vol. 54 (1968)
-
Vol. 53 (1967)
-
Vol. 52 (1966)
-
Vol. 51 (1965)
-
Vol. 50 (1964)
-
Vol. 49 (1963)
-
Vol. 48 (1962)
-
Vol. 47 (1961)
-
Vol. 46 (1960)
-
Vol. 45 (1959)
-
Vol. 44 (1958)
-
Vol. 43 (1957)
-
Vol. 42 (1956)
-
Vol. 41 (1955)
Keyword Ranking
07 Sep. (Last 30 Days)
Tetsu-to-Hagané Vol. 77 (1991), No. 8
First-principles Calculation of Thermodynamic Quantities and Phase Diagrams of Binary Alloys
Tetsuo MOHRI, Satoshi TAKIZAWA
pp. 1223-1233
Recent Developments and Possibilities of Computational Fluid Dynamics in Materials Processing
Ikuo SAWADA, Masahiro TANI, Julian SZEKELY, Olusegun Johnson ILEGBUSI
pp. 1234-1242
Analysis of Steam Flow in Coke Oven Chamber
Kiyoshi MIURA, Keizou INOUE, Kouji TAKATANI, Kunihiko NISHIOKA
pp. 1243-1250
Abstract
The deviation in the carbonization rate in the coke oven chamber has been investigated by use of test coke ovens and a two-dimensional mathematical model.
In the measurement using a 250 kg test coke oven, there observed deviation of plastic layer in many points during the carbonization in the case of a wet coal charge, but in the case of a dry coal charge, three was no point of delay in carbonization and the carbonization progressed uniformly. It was considered that the deviation of the carbonization arises from localized flow of steam through the plastic layers and coke layers.
In order to evaluate flow pattern and heat transfer caused by the steam and the decomposition gas during carbonization, a two-dimensional gas flow mathematical model was developed. This model consists of mass, energy and momentum balance equations in both the gas and solid phases. It was confirmed that temperature change, changes in gas pressure and steam flow pattern in a test coke oven with the upper heating wall were estimated by this model. In the model calculation, the coke fissures affected the steam flow and caused a deviation in the carbonization rate.
Readers Who Read This Article Also Read
Tetsu-to-Hagané Vol.78(1992), No.7
Tetsu-to-Hagané Vol.78(1992), No.7
Tetsu-to-Hagané Vol.77(1991), No.10
Change of Sinter Minerals and Final Fractional Reduction in the Reduction Stage from Hematite to Magnetite with CO-CO2-N2 Gas Mixture
Tateo USUI, Munekazu OHMI, Nobukazu KITAGAWA, Shinji KANEDA, Hirotoshi KAWABATA, Zen-ichiro MORITA
pp. 1251-1258
Abstract
To examine the reduction behavior of commercial sinter in the initial stage, the following analyses were done : Quantitative analysis of sinter before reduction was done by EPMA and the contents of hematite, calcium ferrite (CF), magnetite and slag were determined. Comparison between EPMA surface analyses of sinter before reduction and reduced to magnetite stage at 1 133 K suggests that CF breaks up into magnetite and slag during reduction. Quantitative analysis of sinter minerals during reduction to magnetite stage was done by the X-ray internal standard method using the above-stated contents. Variations in the amount of hematite, CF and magnetite with fractional reduction are revealed ; CF is reduced to magnetite at 1 033 and 1 133 K but is not at 933 nor 983 K. Microstructures of samples reduced up to magnetite stage show that CF is reduced at 1 033 K but not at 983 K. Final fractional reduction in the hematite to magnetite stage under rising temperature conditions up to 1 173 K, Ff', was measured after measuring the one at a predetermined temperature, Ff; below about 1 003 K, CF is hardly reduced and Ff_??_0.7 when oxygen reducible in this stage is assumed to come from hematite and CF. The ratio Ff/Ff' is given as a function of reduction temperature.
Readers Who Read This Article Also Read
Tetsu-to-Hagané Vol.78(1992), No.7
Tetsu-to-Hagané Vol.78(1992), No.7
Tetsu-to-Hagané Vol.77(1991), No.10
An Analysis on Exergy Consumption and CO2 Discharge in Ironmaking Systems
Tomohiro AKIYAMA, Jun-ichiro YAGI
pp. 1259-1266
Abstract
Exergy and CO2 analyses were carried out for three ironmaking systems of blast furnace with pulverized coal injection, SC system proposed by Smitomo Metal and smelting reduction. Blast furnace and SC ironmaking systems were analysed based on operating data reported. For smelting reduction system, operating data was calculated by using the kinetic mathematical model under the various condition of prereduction degree, rate of post combustion and heat recovery efficiency. The exergy loss among the systems have been compared for obtaining detail information on the system evaluation from the point of view of energy consumption. Emission of carbon dioxide discharged from the systems were also compared for environmental preservation.
The results obtained are as follows ;
1) Exergy loss in a conventional ironmaking system of 10 000 t/d was decreased from 9.3 GJ/thm to 8.0 GJ/thm by injecting 110 kg/thm pulverized coal.
2)Exergy loss in SC system of 2 400 t/d was 7.1 GJ/thm.
3)Exergy loss in smelting reduction system depended remarkably on prereduction degree in a shaft furnace or a fluidized bed. As prereduction degree increased from 0 to 80%, exergy loss in the system decreased from 11.8 GJ/thm to 6.2 GJ/thm.
4) Conventional ironmaking system discharged about 520 kg-C/thm, while CO2 emitted from the smelting reduction system depended considerably on ratio post combustion and heat efficiency.
Readers Who Read This Article Also Read
Tetsu-to-Hagané Vol.78(1992), No.7
Tetsu-to-Hagané Vol.78(1992), No.7
Tetsu-to-Hagané Vol.77(1991), No.10
Two-dimensional Analysis on the Flow Characteristics of Powders around Cohesive Zone in a Blast Furnace
Koichiro SHIBATA, Masakata SHIMIZU, Shin-ichi INABA, Reijiro TAKAHASHI, Jun-ichiro YAGI
pp. 1267-1273
Abstract
For clarifying the aerodynamical behavior of unburnt coals in the cohesive zone in a blast furnace with high coal injection rate, two dimensional flow characteristics of powders in packed beds were analyzed by using a mathematical model. Following results were obtained.
(1)Unburnt coals tended to be concentrated at the lower part of cohesive zone. They deposited nearer the wall for reverse-V shaped cohesive zone compared to W shaped cohesive zone.
(2)As a results of the sedimentation of unburnt coals in the furnace, peripheral gas flow was suppressed in reverse-V profile and enhanced in W profile.
(3)Blockade occured in the lower part of cohesive zone and the shape of cohesive zone affected the pulverized coal injection rate at which blockade occured.
Readers Who Read This Article Also Read
Tetsu-to-Hagané Vol.78(1992), No.7
Tetsu-to-Hagané Vol.78(1992), No.7
Tetsu-to-Hagané Vol.77(1991), No.10
Deoxidation Equilibrium of Silicon in Liquid Ni-Cr, Ni-Mo and Ni-W Alloys
Fujio ISHII, Shiro BAN-YA
pp. 1274-1279
Abstract
In order to understand the effects of the various alloying elements on the equilibrium constant of deoxidation of liquid nickel, the deoxidation of nickel based alloys with silicon has been studied at temperature range between 1550°C and 1650°C by the use of silica crucible.
In nickel-chrominium alloy, the deoxidation product, logK'Si(Ni-Cr), which drastically increased by the addition of chromium up to 20 pct chromium, was empirically represented to be.
logK'Si(Ni-Cr)=log K'Si(Ni) + 0.347[%Cr]-0.010[%Cd]2
Cr<15%, 0.65 % Si, 1550°C1650°C
while the deoxidation product in nickel-molybdenum alloy, logK'Si(Ni-Mo), which also lineally increased with increasing molybdenum content, was given by the expression :
log K'Si(Ni-Mo) = log KSi(Ni)+0.047[%Mo]
Mo<16%, 0.65% Si, 1550°C1650°C
In nickel-tungsten alloy, the value of log K'Si(Ni-W) was found to be as follows :
log K'Si(Ni-W) = log KSi(Ni)+ 0.007[%W]
Mo<11%, 0.4% Si, 1550°C1650°C
For the effect of the alloying elements on the activity coefficient of oxygen in nickel, the following parameters were obtained :
logfCrO(Ni) = -0.171 [%Cr] Cr<5%
log fMoO(Ni)=-0.025[%Cr] Mo<16%
logfWO(Ni)=-0.004[ %Cr] W<11%
Deformation Analysis of Angle Steel Rolling in the Butterfly Roll Pass System
Ping XIN, Junji KIHARA, Tatsuhiko AIZAWA
pp. 1280-1287
Abstract
Butterfly roll pass system in the actual angle steel rolling is evaluated by deformation mode method developed recently for three dimensional rolling deformation analyses. In the deformation mode method, both 2D rigid-plastic FEM evaluating the velocity fields in the cross-section of billet, and the deformation modes modeling the velocity distribution in the rolling direction are coupled based on the energy theorem to deal with 3D steady state deformation in rolling process. Two types of mode functions with unknown parameters are employed to express the velocity distribution in the rolling direction : the power and the cubic interpolations in the cross-sectional area ratio. To be noted, unknown parameters are determined by optimization of plastic energy, independently of each subregion, into which the whole analytical region is divided. Through the present analysis is found that (1) the features in rolling behaviors can be discussed by these calculated metal flow and strain distribution for the splitting, the butterfly and the finishing passes in the whole roll pass system, and (2) the numerically estimated cross-sectional figures after rolling are in fairly good agreement with the experimental measurements in the actual processing.
Readers Who Read This Article Also Read
Tetsu-to-Hagané Vol.62(1976), No.1
ISIJ International Vol.54(2014), No.10
Tetsu-to-Hagané Vol.79(1993), No.7
Facility and Characteristics of 100% Hydrogen Atmosphere Annealing Furnace
Shigeru TAJIMA, Kazuaki KOMINE, Toshio SHIBASHITA, Masaki SHIROUZU
pp. 1288-1295
Abstract
The new type batch annealing furnace, which utilized high convection in the inner cover with 100%H2 atmosphere, was developed in early 1970's in Austria for brass industry. The technology was converted for steel industry at the end of 1970's. These annealing furnaces were introduced first in Europe for higher productivity and better surface for automobile panels. The performance is evaluated excellent.
This type of annealing furnace was installed at Wakayama Steel Works for the first time in Japan for estimation. The main facilities and fundamental characteristics are reported here in detail.
The results so far are quite satisfactory in productivity, uniformity, running cost and safety.
Effect of Rough Rolling Condition on the Formability and Ridging of 17% Cr Stainless Steel Sheet
Jirou HARASE, Tetsurou TAKESHITA, Yakitirou KAWAMO
pp. 1296-1303
Abstract
The ridging quality of the 17% Cr stainless steel sheet was found to be closely associated with the rough rolling schedule in the hot rolling process.
When the rough rolling is carried out in the temperature region where no substantial α→γ transformation occurs immediately after the final rough rolling pass, namely final rough rolling is carried out in α single phase or in γ + α dual phases before and after final pass in the rough rolling with the inter-pass time of about 30 s, the static recrystallization in the rough rolling process is promoted and the ridging of the final annealed sheet is remarkably improved even processed without hot band annealing. The riding quality is not improve when α→γ transformation occurs immediately after the rough rolling as the static recrystallization after rough rolling is suppressed by the transformation even with inter-pass time longer than 30 s.
Base on this finding, the new hot rolling method referred as "IRP" ( Inter-pass Recrystallization Process) has been developed.
Retained Austenite in 0.4%C-Si-1.2%Mn Steel Sheet Annealed in Intercritical Range and Austempered
Osamu MATSUMURA, Yasuharu SAKUMA, Hiroshi TAKECHI
pp. 1304-1311
Abstract
To clarify the formation process of the retained austenite in 0.4%C-Si-1.2%Mn steel intercritically annealed followed by austempering, changes in fraction of reained austenite (Vγ), solute carbon content in retained austenite (Cγ) and microstructure with isothermal holding time at 350450°C were examined by X-ray diffraction measurement and electron microscopic observation.
It was concluded that blocky retained austenite grains with less than 23μm dia. found in the above steel and the interlath retained austenite films having been reported by others in the higher carbon (≥0.6C)-Si-Mn steel annealed at single austenite range and austempered, were the same in chemical stability of austenite by carbon enrichment, in spite of differences in site and morphology. Formation of blocky retained austenite may be attributed to the smaller austenite grain size obtained by cold rolling and intercritical annealing. Addition of Si may cause decreasing of carbide precipitation and increasing Vγ at the holding time the maximum of Cγ(Cγmax) is reached, with Cγmax unchanged.
Effects of Retained Austenite on Formabilities of High Strength Sheet Steels
Osamu MATSUMURA, Yasuharu SAKUMA, Yoshio ISHII, Zhao JINFU
pp. 1312-1319
Abstract
Effects of retained austenite on press-formabilities were investigated, using autempered 0.4C-Si-1.2Mn sheet steels with high tensile strength more than 100 kgf/mm2.
The results showed plausible relationships between formabilities and initial fraction of retained austenite (Vγ0). As Vγ0 increased, height of stretch forming increased linearly to the maximum at 0.2 Vγ0, and bendability as well as hole expandability of mechanically grinded hole were gradually improved to the best at 0.150.2 Vγ0. On the other hand, hole expandability of punched hole decreased slightly in less than 0.150.2 Vγ0 with Vγ0 increasing. More than 0.2 or 0.150.2 Vγ0, all of these formabilities decreased extraordinarily.
It was concluded that these effects of retained austenite on pressformabilities can be clearly understood in terms of Vγ0 and κ: a rate constant relating rate of deformation-induced transformation with uniaxial tensile strain, as a parameter showing stability of retained austenite in press-forming.
Readers Who Read This Article Also Read
Tetsu-to-Hagané Vol.73(1987), No.5
Effect of Prior-austenite Grain Size on Hydrogen Attack of 2 1/4Cr-1Mo Steel
Hirooki NAKAJIMA, Hirofumi MIYAJI, Shigeo YAMAMOTO
pp. 1320-1327
Abstract
The effect of the prior-austenite grain size on the hydrogen attack of 2 1/4 Cr-1Mo steel was studied. Austenite grain size was varied by alloying of V, Nb, Ta, Ti or Al up 0.05 mass% to 2 1/4Cr-1Mo steel and by a change of the austenitizing temperature between 950°C and 1250°C. Steels were quenched and tempered, then exposed to hydrogen at 600°C and 29.4 MPa for 1000 h.
The volume of bubbles per unit volume and the number of bubbles along prior austenite grain boundaries per unit area of polished surfaces were decreased by raising of the austenitizing temperature, and furthermore by coarsening of austenite grains. They were little affected by the addition of V, Nb, Ta and Ti, but increased by Al addition.
A small addition of Nb, Ta and Ti and the lowering of the austenitizing temperature decreased the volume of bubbles per unit area of prior austenite grain boundaries and the number of bubbles per unit length of prior austenite grain boundaries. This result is considered to be originated from the refining of austenite grains. On the other hand, the addition of Al increased them, and in Al alloyed steels the lowering of the austenitizing temperature was inffective for the decrease of them. The latter behavior was due to the acceleration in bubble formation by the unidissolved AlN at the lower austenitizing temperature.
Effects of C, Nb, Mn on Soluble Nb and Mechanical Properties of Nb Treated Hot Rolled Steel Sheet
Kazuaki SATO, Masayoshi SUEHIRO
pp. 1328-1335
Abstract
The effects of carbon, niobium and manganese on the precipitation behavior of Nb in deformed austenite were investigated in a series of micro-alloyed steels. The steels were hot rolled in a five pass schedule on laboratory scale mills to define the effect of holding time at 950°C prior to forth pass on the rolling load, tensile properties and quantitatively analyzed soluble Nb( Sol. Nb).
The increase in amount of C and Nb accelerates the precipitation of Nb and tensile strength (TS) decreases with the decrease of Sol. Nb. These results indicates that in the specified rolling conditions TS of the steel with lower C or Nb content is larger than that with higher C or Nb content.
It is found that soluble Nb increases the rolling load. Therefore, the precipitation behavior of Nb can be estimated by the change in the rolling load.
The addition of Mn retards the precipitation of Nb and therefore enhances the strength of the Nb treated steel.
The observed decrease of Sol. Nb with the holding time is larger than that estimated by the decrease of rolling load. This result suggests that the growth of Nb precipitates takes place mainly during cooling subsequent to hot rolling.
Improvement of Wear Resistance of Titanium by the Dispersion of Carbides
Wataru TAKAHASHI, Minoru OKADA, Yoshiaki SHIDA, Mutsuo NAKANISHI
pp. 1336-1343
Abstract
Titanium alloys have various excellent characteristics, such as good corrosion-resistance and high specific strength. However, they have not been applied to the sliding parts of machine because of the lack of wear resistance.
In this study, in order to improve the wear resistance of titanium, the effects of the kind and quantity of carbide on wear resistance of a carbide dispersed titanium alloy have been investigated using the Plasma Transferred Arc (PTA) process and Ar arc melting.
Results obtained through this study are :
(1)[Ti-6Al-4V W2C] and [Ti-6Al-4V + Cr3C2] alloys showed wear resistance superior to a Co-based alloy ( Stellite) under the sliding wear test. It was also confirmed that they scarcely wore opposing steel.
(2) The excellent wear resistance of these carbide dispersed alloys is attributed to the microstructure which consists of fine TiC particles dispersed uniformly and a tough and hard matrix of the βTi phase formed by the addition of β-stabilizer, that is, W or Cr during the PTA process and Ar arc melting.
Consequently, wear resistance of the alloys containing the carbides (NbC, TiC) which do not transform the titanium matrix into the βTi phase is not improved.
Development of High Speed Black Electroplating Process
Katsushi SAITO, Yujiro MIYAUCHI, Kazumi SHIBATA
pp. 1344-1351
Abstract
High speed black electroplating process was developed. The black coatings are deposited on cathode surface by electrolysis in acid solution containing Zn2+, Ni2+, Cr3+ and No3-. Quantity of electricity to obtain the black surface is only 2×103 C/m2.
The black coatings are mainly composed of hydrated oxides, metallic Zn and Zn-Ni alloy.
The blacked Zn-Ni alloy plated steel sheet with chromate and resin coat has excellent properties, for example, scratch resistance, corossion resistance and weldability.
Effect of Kind of Lubricants on Press Forming Ability of Galvannealed Steel Sheets
Sakae SONODA, Yasuo OKUMURA
pp. 1352-1358
Abstract
Effect of kind of lubricants on press forming ability of galvannealed steel sheets, which is susceptible to powdering, was investigated by cylindrical shell draw test, drawbead test and Bowden's friction test.
The lubricity was found highest in the case of using phosphate coating + soap, followed by press lubricants, solid lubricants, resin and rust preventive oil in this order.
The correlation coefficients between the results obtained by each test were found to be relatively high and the influence of powdering on lubricity was not observed.
Development of Polyester Resin-Colloidal Silica-Ethylene Tetrafluoride Lublication Film Coating Steel
Hisao ODASHIMA, Ikuo KIKUCHI
pp. 1359-1366
Abstract
A newly developed lubrication film coating steel of polyester 40-colloidal silica 30-ethylene tetrafluoride 6 ( Parts by weights) has excellent forming ( Lublication ) property and scratch resistance. The coating steel has excellent continuous forming, too. Furthermore, excellent corrosion resistance after forming and paint adhesion are maintained, too. When fine-grained colloidal silica of 8 nm under is used, excellent scratch resistance of film yields as a result of rising of film intensity. The excellent lubrication of film and scratch resistance at high temperature is maintained by ethylene tetrafluoride. Corrosion resistance of the lublication film coating steel yields as a result of film formation of polyester, fairly rising of film intensity due to fine-grained colloidal silica and scratch resistance due to lubrication of ethylene tetrafluoride. Excellent paint adhesion of the lubrication film yields as a result of maintenance of excellent paint adhesion of polyester resin at wide temperature.
Effects of Coloring Conditions on the Properties of the Film for Colored Stainless Steels
Yuji SONE, Keiichi YOSHIOKA, Misao TOCHIHARA, Osamu HASHIMOTO
pp. 1367-1372
Abstract
Colored films on the stainless steel, formed by the alternating current electrolyzing (ACE) method and the conventional one (INCO method), have been studied to clarify the differences in the structure, rub resistance and polarization resistance of them. In the ACE method, the effects of electrolyzing patterns on the color tone and polarization resistance of the film have been investigated.
The results obtained are as follows:
(1) The film formed by the ACE method has the higher Cr content, the more uniform Cr dispersion and the better rub resistance than that of the conventional one.
(2) The polarization resistance of the film measured by AC impedance method is proportional to its thickness, and is higher in the ACE method than that in the conventional one.
(3) The growth behaviour of the film by the ACE method depends on the electrolyzing condition for coloring; increasing type of electrolysis current leads to thinner thickness and higher polarization resistance of the film in comparison with those obtained by the decreasing pattern.
Readers Who Read This Article Also Read
ISIJ International Vol.31(1991), No.8
Effects of Cr and Free C on the Structure and the Corrosion Resistance of Chromium Diffusion Coatings on Cr Alloy Steels
Toshiro ANRAKU, Hiroshi TERANISHI
pp. 1373-1380
Abstract
The effects of C and Cr on the chromium diffusion layer formation by pack cementation process on Cr alloy steels ( Cr : 2.25 mass%-12 mass%) were examined. The following results were obtained.
(1)The structure of chromium diffusion coating on alloys which contained free C consisted of two layers independent of Cr content on alloys. The outer layer was chromium carbide film consisting of Cr23C6 and Cr7C3. The inner layer was Cr diffusion layer whose Cr content ranged from 25 mass% to 13 mass%.
(2) The thickness of Cr diffusion coating significantly depended on the free C and Cr content in alloy. The thickness of chromium carbide film, increased with increasing C content in alloy. On the other hand, the thickness of Cr diffusion layer increased with decreasing C content and increasing Cr content in alloy.
(3) The outer chromium carbide film and inner Cr diffusion layer exhibited good oxidation resistance in super heated steam environment due to the formation of Cr2O3 scale on both layers.
Readers Who Read This Article Also Read
Tetsu-to-Hagané Vol.73(1987), No.2
Tetsu-to-Hagané Vol.76(1990), No.7
Tetsu-to-Hagané Vol.76(1990), No.4
Article Access Ranking
07 Sep. (Last 30 Days)
-
Perspectives on the Promising Pathways to Zero Carbon Emissions in the Steel Industry toward 2050
ISIJ International Vol.65(2025), No.2
-
Growth, Removal, and Agglomeration of Various Type of Oxide Inclusions in Molten Steel
Tetsu-to-Hagané Vol.111(2025), No.11
-
Finite Element Analysis of Bubble Growth and Particle Swelling during Coal Pyrolysis
ISIJ International Vol.65(2025), No.9
-
Interface behavior leading to Al/Cu dissimilar metal bonding formation with high-speed eutectic reaction induced by applying current
QUARTERLY JOURNAL OF THE JAPAN WELDING SOCIETY Vol.43(2025), No.2
-
Copper removal of liquid steel containing 0.25 % carbon using Fe2O3-CaCl2-SiO2 flux
ISIJ International Advance Publication
-
Corrosion Behavior of Carbon Steel under Soil Drying Conditions
ISIJ International Advance Publication
-
Cold Spot Joining of 980 MPa-class Ultra-high Strength Steel
Tetsu-to-Hagané Advance Publication
-
Combination Effect of Premixing Conditions and Iron Ore Size Distribution in Sintered Ore Granulation Process with Intensive Mixer
ISIJ International Advance Publication
-
A preliminary study on reduction degradation of iron ore sinter using sinter analogue and X-ray micro-computed tomography (MCT)
ISIJ International Advance Publication
-
Viscosity Measurement of Foam with High Gas Volume Fraction Using Sphere Pull-up and Dam-break Experiments
ISIJ International Advance Publication
You can use this feature after you logged into the site.
Please click the button below.