- TOP
- Tetsu-to-Hagané
- Vol. 59 (1973), No. 3
Tetsu-to-Hagané Vol. 59 (1973), No. 3
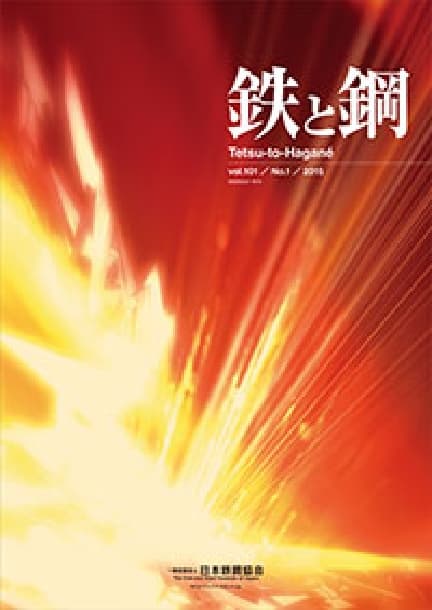
Grid List Abstracts
ONLINE ISSN: | 1883-2954 |
PRINT ISSN: | 0021-1575 |
Publisher: | The Iron and Steel Institute of Japan |
Backnumber
-
Vol. 111 (2025)
-
Vol. 110 (2024)
-
Vol. 109 (2023)
-
Vol. 108 (2022)
-
Vol. 107 (2021)
-
Vol. 106 (2020)
-
Vol. 105 (2019)
-
Vol. 104 (2018)
-
Vol. 103 (2017)
-
Vol. 102 (2016)
-
Vol. 101 (2015)
-
Vol. 100 (2014)
-
Vol. 99 (2013)
-
Vol. 98 (2012)
-
Vol. 97 (2011)
-
Vol. 96 (2010)
-
Vol. 95 (2009)
-
Vol. 94 (2008)
-
Vol. 93 (2007)
-
Vol. 92 (2006)
-
Vol. 91 (2005)
-
Vol. 90 (2004)
-
Vol. 89 (2003)
-
Vol. 88 (2002)
-
Vol. 87 (2001)
-
Vol. 86 (2000)
-
Vol. 85 (1999)
-
Vol. 84 (1998)
-
Vol. 83 (1997)
-
Vol. 82 (1996)
-
Vol. 81 (1995)
-
Vol. 80 (1994)
-
Vol. 79 (1993)
-
Vol. 78 (1992)
-
Vol. 77 (1991)
-
Vol. 76 (1990)
-
Vol. 75 (1989)
-
Vol. 74 (1988)
-
Vol. 73 (1987)
-
Vol. 72 (1986)
-
Vol. 71 (1985)
-
Vol. 70 (1984)
-
Vol. 69 (1983)
-
Vol. 68 (1982)
-
Vol. 67 (1981)
-
Vol. 66 (1980)
-
Vol. 65 (1979)
-
Vol. 64 (1978)
-
Vol. 63 (1977)
-
Vol. 62 (1976)
-
Vol. 61 (1975)
-
Vol. 60 (1974)
-
Vol. 59 (1973)
-
Vol. 58 (1972)
-
Vol. 57 (1971)
-
Vol. 56 (1970)
-
Vol. 55 (1969)
-
Vol. 54 (1968)
-
Vol. 53 (1967)
-
Vol. 52 (1966)
-
Vol. 51 (1965)
-
Vol. 50 (1964)
-
Vol. 49 (1963)
-
Vol. 48 (1962)
-
Vol. 47 (1961)
-
Vol. 46 (1960)
-
Vol. 45 (1959)
-
Vol. 44 (1958)
-
Vol. 43 (1957)
-
Vol. 42 (1956)
-
Vol. 41 (1955)
Keyword Ranking
04 Sep. (Last 30 Days)
Tetsu-to-Hagané Vol. 59 (1973), No. 3
Spouted Bed Reduction of Iron Ore
Masaya OZAWA
pp. 361-371
Abstract
The most serious problem inherent to the fluidized bed reduction of iron ore is sintering. One of the solution to this problem is to use relatively coarse powder of iron ore. Spouted bed is a technique of processing relatively coarse granular materials. The purpose of the present investigation is to try spouted bed reduction with relatively coarse powder of iron ore and to know characteristics and feasibility of this technique.
Experiments were performed with transparent models and spouting conditions were determined. Effects of reduciant gas flow rate, cone angle, particle size distribution on the spouted bed reduction were investigated. It was turned out that the spouted bed reduction was effective to relatively coarse granules of iron ore. Rate of reduction was proportional to the flow rate of reductant gas fed to the bed. Sintering tendency was less with spouted bed than with usual fluidized bed in a low gas velocity region.
Critical flow rate and reducing temperature causing sintering were shown. A discussion was made on the relation between the results obtained with model experiments and with high temperature reduction.
Simultaneous Absorption of Nitrogen, Oxygen and Carbon of Liquid Iron from N2-CO2and Ar-CO2Gas Mixtures
Takao CHOH, Fujio KUZE, Michio INOUYE
pp. 372-386
Abstract
The rates of simultaneous absorption of nitrogen and oxygen in liquid iron from argon-carbon dioxide and nitrogen-carbon dioxide gas mixtures were measured.
Carbon dioxide has little influence on the rate of absorption of nitrogen in liquid iron when the gas phase containes carbon dioxide lower than 7·2vol pct. However, above 10vol pet, the absorption rate of nitrogen decreases due to the oxygen concentrated layer at gas-metal interface.
The results show that the rate of absorption of oxygen from carbon dioxide increases with increasing partial pressure of carbon dioxide. On the other hand, it is also observed that the concentration of carbon in liquid iron increases at early period of reaction, and then decreases after several minutes for every gas mixture.
Considering the dissociation of CO2into CO and atomic oxygen, the rate limiting steps of oxygen absorption may be gaseous diffusion control below 3 vol pct carbon dioxide, chemical reaction control at the interface in the range between 3 and 15vol pct, and diffusion control in liquid iron above 15vol pct. There are practically no difference between the mechanism of absorption of oxygen by nitrogen-carbon dioxide and argon-carbon dioxide gas mixtures.
The behavior of carbon in liquid iron may be determined by combining the carbon absorption from carbon monoxide with the decarburization by gaseous oxygen atom.
Simultaneous Absorption of Oxygen and Hydrogen in Liquid Iron from Water Vapour
Takao CHOH, Michio INOUYE
pp. 387-394
Abstract
On the assumption that water vapour should dissociate into gaseous oxy gen and hydrogen at gas-metali nterface and also their partial pressures are in equilibrium, the rates of absorption of oxygen in liquid iron rom water vapour between 0·1 and 0·0032atmpH2o is considered to be controlled by the activation process of adsorbed oxygen atom, namely chemical reaction, and be proportional to(pH2oi/PHi)2.
The hydrogen absorption of liquid iron may be also predicted by combining the dissolution p rocess of dissociated hydrogen atom with the oxidization process of hydrogen in liquid iron by adsorbed oxygen atom.
It is generally estimated that the concentration of hydrogen in liquid iron increases at early period of reaction, and then decreases with increasing oxygen concentration in liquid iron as already shown in the carbon absorption from carbon dioxide, because of the simultaneous absorption of oxygen from water vapour. At higher partial pressure of water vapour, for example, 0·1atmpH2O, liquid iron will contain less hydrogen than at lower partial pressure.
If the rate of absorption of oxygen is constant independent of partial pressure of water vapour, the concen-tration of hydrogen increases with increasing partial pressure of water vapour in gas phase. On the other hand, if the concentration of oxygen in liquid iron decreases, the hydrogen dissolution occurs more markedly.
The Deoxidation of Steel with Al-Si Alloy
Takaji KUSAKAWA, Chisato YOSHIDA, Yoshiaki TAMURA, Hajime ONO
pp. 395-404
Abstract
The mechanism on the deoxidation of molten ironwith Al and Al-Si alloy deoxidizer was investigated by using induction furnace and Tammann furnace.
The experimental results were summarized as follows.
1) The deoxidation of molten iron with Al was not effective in air. But under the Ar atmosphere, the decrease of total oxygen content was remarkable.
2) In the beginning of deoxidation with Al-Si alloy in air, the reaction between Al and O was much faster than the reaction between Si and O.
Al was consumed immediately, but Si was remained sufficiently as soluble Si at that time. Subsequently Si reacted with oxygen in air and protected the reoxidation of molten iron by the formation of SiO2particles.
3) The yield of Al in the beginning of deoxidation was increased by Si. Flake like primary a in Al-Si alloy protected Al-Si eutectic against consumption of Al, when the deoxidizer was added into molten iron.
Readers Who Read This Article Also Read
Tetsu-to-Hagané Vol.58(1972), No.6
Tetsu-to-Hagané Vol.58(1972), No.14
Tetsu-to-Hagané Vol.60(1974), No.9
Gaseous Oxidation Rates of Liquid Lead and Solid Iron through Molten Oxide Layer and Effects of Applied Current Flows
Hiroshi ITAYA, Kazuhiro GOTO
pp. 405-413
Abstract
A certain quantity of liquid PbO, PbO-SiO2, Na2O-B2O3or Na2O-GeO2has been put on liquid lead or solid iron in a crucible suspended from a thermobalance and then oxidized under air or O2-Ar mixtures at 900 to 1 000°C. The effect of supplied currents upon the rates has also been determined by the thermobalance.
The following results were obtained. When no current was supplied, the oxidation rate of liquid lead obeyed the parabolic law. The rate was increased with increase of temperature and the partial pressure of oxygen in gases and decreased with the increase of SiO2content in PbO-SiO2melts. When solid iron was oxidized through Na2O-B2O3and Na2O-GeO2, no change in weight could be measured because of very small oxidation rate.
When liquid lead covered with PbO-SiO2and solid iron covered with Na2O-B2O3were oxidized with galvanostatic currents, the rates were accelerated by the currents and satisfied Faraday's relation at 900 to 1000°C and with the currents less than 400mA. At lower temperature, however, the rates deviated from Faraday's relation even with smaller currents.
Studies of NRIM Continuous Steelmaking Process
Ryuichi NAKAGAWA, Shiro YOSHIMATSU, Takuya UEDA, Tatsro MITSUI, Akira FUKUZAWA, Akira SATO, Tsuyoshi OZAKI
pp. 414-430
Abstract
The fundamental aspect of the development of the NRIM multi-stage trough type continuous steelmaking process and the results of its recent operations are presented in this paper. Though the scale of the plant used was small (hot metal flow rate 7.8t/hr), a suitable separation of the steelmaking reactions to each stage of the continuous steelmaking furnace and the know-how of its operation were satisfactorily obtained. The industrialization of this process is confirmed to be feasible. As the result of the separation, that is, silicon and phosphorus were mostly removed in the first stage so that the final carbon level was controlled mainly in the second stage, the product with phosphorus as low as 0.005%(dephosphorization ratio 96%) was obtained with comparable amount of lime to that of the conventional batch type steelmaking processes.
The Mechanism of Formation of the V Segregation in Steel Ingot
Koreaki Suzuki, Takehiro MIYAMOTO
pp. 431-445
Abstract
According to many studies on the formation of the V segregation, the formation seems to be affected by the following three factors; the thermal state, the gravitational action, and the dendrite morphology. In order to show how the V segregation would be influenced when each factor was varied independently or mutually, some investigations were made on sand-cast ingots.
The results obtained are summarized as follows:
1) The V segregation appeared in the acceralated solidification area of small ta pered ingots with a large ratio of height to diameter; the area did not suffer the both end and riser effects.
2) The gravity itself did not have any direct effect on the V segregation, but the shape of the segregation was rather influenced by the change of dendrite morphology and the distributio n of chemical compositions which were caused by the gravity action.
3) The V segregation tended to disappear with an increase of the amount of taper. With the great taper, the concentrated melts to become the V segregation was found to be squeezed from the area corresponding to the V segregation zone toward the feeder head with the progress of solidification.
A discussion was made on the formation mechanism of the V segregation based upon the results described above, and the theory of the suction by the volume shrinkage of molten steel on solidification could well explain the experimental results.
Readers Who Read This Article Also Read
Tetsu-to-Hagané Vol.63(1977), No.1
Behavior of Aluminum Nitride, Austenite Grain Size, and Its Coarsening Temperature in Low Alloy Steels
Shushi KINOSHITA, Takeshi UEDA, Akira SUZUKI
pp. 446-453
Abstract
The austenite grain coarsening temperature of low carbon alloy steels has been studied for various conditions of heat treatment, and the results are discussed in terms of the effects of particle size of aluminum nitride and the initial grain size of austenite.
It is found that the preheat treatment of the isothermal reaction type with regard to aluminum nitride has an influence on the austenite grain coarsening temperature through its effect on the particle size of aluminum nitride, whereas the quench and temper type of heat treatment has an effect both on the particle size of aluminum nitride and the initial grain size of austenite.
The effect of the microstructure and the prior grain size of austenite on the initial austenite grain size have also been investigated.
Readers Who Read This Article Also Read
Tetsu-to-Hagané Vol.57(1971), No.1
Tetsu-to-Hagané Vol.79(1993), No.2
Tetsu-to-Hagané Vol.59(1973), No.13
The Strength and Ductility of Two-phase Iron Alloys
Imao TAMURA, You TOMOTA, Yukio YAMAOKA, Saburo KANATANI, Masatoshi OZAWA, Akira AKAO
pp. 454-468
Abstract
The strength and ductility of two-phase iron alloys with a ductile second phase were studied. The alloys used in this investigation were classified in three groups, that is, Fe-Cr-Ni alloys composed of austenite and ferrite, Fe-Ni-C alloys composed of austenite and martensite, and Fe-C alloys composed of ferrite and martensite; these phases had various volume fractions.
The main results obtained are as follows:
(1) In case of Fe-Cr-Ni alloys having different volume fractions of phases, when the same heat treatment was given, the better combination of strength and elongation was obtained in two-phase alloys than in single-phase alloys of austenite or ferrite. The main cause of this behavior was the difference in grain size. The coarsening of grains in two-phase alloys was much slower than that in single-phase alloys.
(2) The effects of grain size on strength were shown by Petch type relations even in two-phase alloys as well as in single phase ones.
(3) The effect of the volume fraction of phases on tensile properties with nearly the same grain size depended on the difference between the tensile properties of the second phase and the matrix. As the ratio of the 0.2% proof stress of the second phase to that of the matrix became larger than about 3, the relationb etween 0.2% proof stress and the volume fraction became to deviate from a linear relationship; this is known as the law of mixture. This may be caused by the difference of strains in the second phase and the matrix which becomes larger with an increase of the ratio.
On the Drawability and Recrystallization Texture of Low Carbon Sheets Containing Carbide Forming Elements
Ichiro KOKUBO, Masatoshi SUDO, Katsumi KAMENO, Shun'ichi HASHIMOTO, Ichiro TSUKATANI, Takafusa IWAI
pp. 469-492
Abstract
An investigation has been carried out to clarify the effect of carbide forming elements as Ta, Nb and Zr on the drawability and the recrystallization texture of cold-rolled low carbon steel sheets. Prior to cold rolling, a reheating treatment of hot bands is given so that C and N in solution in steel may precipitate as carbide and nitride.
The results obtained are as follows:
1. The addition of Ta, Nb, Ti, and Zr is so effective to improve γ value of low carbon steel sheets.
2. When a proper reheating treatment in given prior to cold rolling, the γ value increase remarkably with an increase of the atomic ratio of Ta to (C+N) and shows a maximum at the ratio of about 1·1.
3. As to the recrystallization texture, the (111) fiber texture develops remarkably in the sheet containing no carbon in solution while the (111) texture becomes weak with an increase of carbon content. A study of the effect of carbide size on the recrystallization texture shows that carbide larger than about 500Å increase (200) and decrease (222) pole intensities.
4. The cold rolling texture has a close relationship with the concentration of carbon in solution. The absence of carbon and tantalum in solution develops in the cold-rolled sheet the {211}‹011› texture which is considered preferable for the development of the near {111}‹112› texture during the recrystallization process.
5. It is concluded that the high γ value obtained in Ta bearing low carbon steel sheets is attributed mainly to the absence of carbon in solution by means of the reheating treatment prior to cold rolling.
The State of Presence of Phosphor in Hamersley Pellet
Kimitaka SATO, Ken'ichi SUZUKI
pp. 493-499
Abstract
There were differences among the 29 analytical values of phosphor in the Hamersley pellet obtained in nine laboratories by means of the JIS M 8216 (1964) method; the values obtained were classified to either 0·050±0·005% or 0·019±0·004%. By the investigation of the cause of the difference, it was made clear that the analytical value of phosphor became about 0·050% when the residues after acid dissol ution were treated by an alkali fusion process, about 60% of the total phosphor in the pellet remained in the residue insoluble with inorganic acids.
In this paper, the process by which the phosphor in Hamersley iron are became insoluble in inorganic acids during firing the pellet was especially investigated by the combined use of chemical and X-ray analyses. It was shown that the phosphor in Hamersley iron ore became soluble into the α-cristobalite formed at high temperature, which then formed stable glass insoluble in inorganic acids together with the elements of Al, Ca, and Fe. There were no other examples which gave an anomalous value except the Hamersley pellet.
Determination of Oxygen by Activation Analysis with 14 MeV Fast Neutrons
Kiichi NARITA, Tetsuo MATSUMURA, Norihito NAGATA
pp. 500-507
Abstract
A method for the determination of oxygen in steel and other metals by the 16O (n, p) 16N reaction with 14MeV neutrons has been investigated. Parameters such as instrumental conditions, sample size, and interferences from other elements can be recognized and their effects are evaluated and experimentally controlled.
The sample size is important to obtain a good precision and accuracy. For the industrial routine analysis a preference is given to cylindrical samples of diameter 12·5mm and thickness 10mm. In order to ensure a reliable pneumatic transport and minimize the error in counting, tolerances on the size must be kept within ± 0·2mm as strictly as possible.
Interferences by B and F on the oxygen analysis are experimentally investigated. B and F of 0·1% correspond to oxygen of 70 and 420ppm, respectively.
The long-term coefficient of variation for analysis of a given sample over a period of 10 days is 4 to 10%.The accuracy of this method is checked by comparison of the results with those of the vacuum fusion method. The agreement of the results obtained by the two methods is satisfactory.
The determination of oxygen in various powder samples such as acid insoluble residue in steel and iron powder is also demonstrated with satisfactory results.
Article Access Ranking
04 Sep. (Last 30 Days)
-
Perspectives on the Promising Pathways to Zero Carbon Emissions in the Steel Industry toward 2050
ISIJ International Vol.65(2025), No.2
-
Growth, Removal, and Agglomeration of Various Type of Oxide Inclusions in Molten Steel
Tetsu-to-Hagané Vol.111(2025), No.11
-
Finite Element Analysis of Bubble Growth and Particle Swelling during Coal Pyrolysis
ISIJ International Vol.65(2025), No.9
-
Interface behavior leading to Al/Cu dissimilar metal bonding formation with high-speed eutectic reaction induced by applying current
QUARTERLY JOURNAL OF THE JAPAN WELDING SOCIETY Vol.43(2025), No.2
-
Corrosion Behavior of Carbon Steel under Soil Drying Conditions
ISIJ International Advance Publication
-
Cold Spot Joining of 980 MPa-class Ultra-high Strength Steel
Tetsu-to-Hagané Advance Publication
-
Combination Effect of Premixing Conditions and Iron Ore Size Distribution in Sintered Ore Granulation Process with Intensive Mixer
ISIJ International Advance Publication
-
A preliminary study on reduction degradation of iron ore sinter using sinter analogue and X-ray micro-computed tomography (MCT)
ISIJ International Advance Publication
-
Copper removal of liquid steel containing 0.25 % carbon using Fe2O3-CaCl2-SiO2 flux
ISIJ International Advance Publication
-
Evaluation of Feature Selection Methods for Oxygen Supply Prediction in BOF Steelmaking
ISIJ International Advance Publication
You can use this feature after you logged into the site.
Please click the button below.