- TOP
- Tetsu-to-Hagané
- Vol. 56 (1970), No. 14
Tetsu-to-Hagané Vol. 56 (1970), No. 14
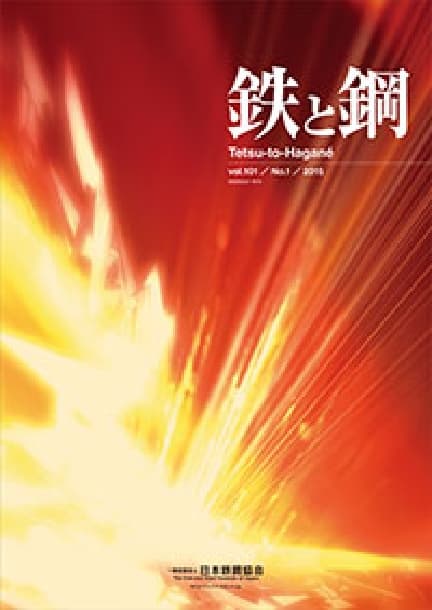
Grid List Abstracts
ONLINE ISSN: | 1883-2954 |
PRINT ISSN: | 0021-1575 |
Publisher: | The Iron and Steel Institute of Japan |
Backnumber
-
Vol. 111 (2025)
-
Vol. 110 (2024)
-
Vol. 109 (2023)
-
Vol. 108 (2022)
-
Vol. 107 (2021)
-
Vol. 106 (2020)
-
Vol. 105 (2019)
-
Vol. 104 (2018)
-
Vol. 103 (2017)
-
Vol. 102 (2016)
-
Vol. 101 (2015)
-
Vol. 100 (2014)
-
Vol. 99 (2013)
-
Vol. 98 (2012)
-
Vol. 97 (2011)
-
Vol. 96 (2010)
-
Vol. 95 (2009)
-
Vol. 94 (2008)
-
Vol. 93 (2007)
-
Vol. 92 (2006)
-
Vol. 91 (2005)
-
Vol. 90 (2004)
-
Vol. 89 (2003)
-
Vol. 88 (2002)
-
Vol. 87 (2001)
-
Vol. 86 (2000)
-
Vol. 85 (1999)
-
Vol. 84 (1998)
-
Vol. 83 (1997)
-
Vol. 82 (1996)
-
Vol. 81 (1995)
-
Vol. 80 (1994)
-
Vol. 79 (1993)
-
Vol. 78 (1992)
-
Vol. 77 (1991)
-
Vol. 76 (1990)
-
Vol. 75 (1989)
-
Vol. 74 (1988)
-
Vol. 73 (1987)
-
Vol. 72 (1986)
-
Vol. 71 (1985)
-
Vol. 70 (1984)
-
Vol. 69 (1983)
-
Vol. 68 (1982)
-
Vol. 67 (1981)
-
Vol. 66 (1980)
-
Vol. 65 (1979)
-
Vol. 64 (1978)
-
Vol. 63 (1977)
-
Vol. 62 (1976)
-
Vol. 61 (1975)
-
Vol. 60 (1974)
-
Vol. 59 (1973)
-
Vol. 58 (1972)
-
Vol. 57 (1971)
-
Vol. 56 (1970)
-
Vol. 55 (1969)
-
Vol. 54 (1968)
-
Vol. 53 (1967)
-
Vol. 52 (1966)
-
Vol. 51 (1965)
-
Vol. 50 (1964)
-
Vol. 49 (1963)
-
Vol. 48 (1962)
-
Vol. 47 (1961)
-
Vol. 46 (1960)
-
Vol. 45 (1959)
-
Vol. 44 (1958)
-
Vol. 43 (1957)
-
Vol. 42 (1956)
-
Vol. 41 (1955)
Keyword Ranking
29 Aug. (Last 30 Days)
Tetsu-to-Hagané Vol. 56 (1970), No. 14
Sintering Mechanism of Self-fluxed Sinter with Basicity of About 1.2
Kojiro KOJIMA, Kyoichi NAGANO, Tadahiro INAZUMI, Tadao KISHI, Koichi SHINADA
pp. 1789-1808
Abstract
Process of mineral formation of sinter with a basicity of about 1.2 was studied by specimens obtained from the sintering-interruption experiment, re-treatment (re-heating) of commercially produced sinter and various test-pan sinter test. Phase of sinter, which was fired well, consisted of magnetite and silicate glass. Peterogeneity and deficiency of firing were reflected in the distribution of the calcium ferrites. The mechanism of sintering was elucidated theoretically by using phase diagrams. Formation of liquid at relatively lower temperature depended on a oxygen potential (Fe++/Fe+++ ratio) of the condensed system; in the case of higher oxygen potential, liquid of calcium ferrite (β) was formed and in the case of lower potential, liquid of silicate (γ) was formed. At initial stage of the sintering process (in the case of basicity about 1.2) more amount of liquid of calcium ferrte (β) was formed than that of liquid of silicate (γ), but at the latter stage, liquid of silicate (γ) increased by transition of Fe+++ to Fe++. higher temperature these two kinds of liquid reacted each other and interacted and liquid of calcium ferrite (β) tended to decrease. The proper phase of well-fired sinter consisted of magnetite and silicate, which resulted in well assimilation of these liquids.
Readers Who Read This Article Also Read
Tetsu-to-Hagané Vol.68(1982), No.15
Tetsu-to-Hagané Vol.68(1982), No.15
Tetsu-to-Hagané Vol.73(1987), No.15
Activity of Carbon and Oxygen in Liquid Iron Alloys
Yoshitomo SUZUKI, Shiro BAN-YA, Tasuku FUWA
pp. 1809-1818
Abstract
The effects of alloying elements on the activity coefficient of carbon and oxygen in liquid iron have been studied by measuring the equilibrium, C (in Fe) + CO2=2CO, at a temperature of 1560°C. The activity coefficient of carbon is increased by the addition of cobalt and decreased by molybdenum, tungsten, vana-dium, niobium and tantalum. The activity of oxygen in Fe-C-O-j systems containing the-deoxidizing elements such as vanadium and niobium will be expressed by applying the first terms and cross product terms in WAGNER'S use of the Taylor series. Phosphorus, nickel, and cobalt decrease the product of carbon and oxygen in liquid iron, and vanadium, niobium, chromium, and molybdenum increase it.
The Behavior of Oxygen in Liquid Steel during the Continuous Casting
Mitsunofu KURITA, Takami IKEDA, Kctsukiyo MARUKAWA
pp. 1819-1823
Abstract
In order to clarify the origin of macrcscopic oxide inclusions in continuously cast steel, it is necessary to understand quantitatively (1) the balance of oxygen in steel during casting and (2) the entrapment of floating oxide inclusions by solidified steel.
Accordingly, the behavior of cxygen in steel was investigated during casting of AISI 304 grade steel containing silicate inclusions, then the balance of oxygen and the entrapnent of oxide inclusions were analyzed.
It became clear that the behavior of oxygen in steel is remarkably different during casting between by open nozzle and by submerged nczzle. A characteristic of casting by open nczzle is that the oxygen content of liquid steel in mold is remarkably higher than that of poured steel. The oxygen content of solidified steel, however, does not always become higher than that of poured steel. This shows that the oxidation of liquid steel by the air is sufficiently compensated by the separation of scum. On the other hand, the oxygen content of poured steel, that of liquid steel in mold and that of solidified steel are equivalent during casting by submerged nozzle.
Readers Who Read This Article Also Read
Tetsu-to-Hagané Vol.49(1963), No.2
Tetsu-to-Hagané Vol.54(1968), No.8
Tetsu-to-Hagané Vol.53(1967), No.7
Large Inclusions in Continuously Cast Carbon Steel Billets
Hisashi MORI, Nobuyoshi TANAKA, Masazumi HIRAI
pp. 1824-1843
Abstract
Effects of various factors on large inclusions (greater than 0.05 mm in dia.) in plain carbon steel billets were investigated, and following results were obtained.
1) The numbers of large inclusions in Si killed steel billets are decreased with decreasing total oxygen content or Mn/Si ratio, with increasing amount of carbon or soluble Al in the billets or amount of Ti added to low Mn steel; whereas the numbers of entrapped scum are increased with decreasing Mn/Si ratio and addition of Ti to low Mn steel.
2) The numbers of large inclusions are increased with addition of slag powder into mould if a submerged nozzle is not used. It was found by EPMA identification that they were originated from slag powder. The numbers of large inclusions are decreased by use of a air-tight submerged nozzle and slag powder.
3) Large Mn-silicate inclusions are occasionaly detected in Al killed steel billets in the case of open nozzle and oil casting.
4) Sodium is detected in mould scum when glass powder is added into the tundish.
5) The numbers of large inclusions and ratio of very large inclusions (greater than 0.5 mm in dia.) are decreased with increasing billet's size from 80 mm square to 160 mm square, but slightly increased with increasing from 160 mm square to 260×370 mm.
6) The effects of these factors are discussed from the view point of a) cleanliness of molten steel in tundish, b) air oxidation of pouring stream to mould, c) entrapment of mould scum, d) possibilities of floatation and coagulation of large inclusions during solidification process.
Readers Who Read This Article Also Read
Tetsu-to-Hagané Vol.49(1963), No.2
Tetsu-to-Hagané Vol.54(1968), No.8
Tetsu-to-Hagané Vol.53(1967), No.7
On the Agitation and Mixing of Molten Steel in a Ladle during DH Degassing Treatment
Kiichi NARITA, Takehisa MAKINO
pp. 1844-1853
Abstract
The behavior of agitated flow and the mixing efficiency of molten steel in a ladle during DH degassing treatment was analogized by observing the motion of glycerin solution in a model equipment. The results were as follows.
(1) The motion of the fluid after spouting out from a degassing vessel into a ladle is changed by the moving speed of ladle and the viscosity of fluid.
(2) The volume of fluid, which is lifted up into degassing vessel from the ladle at one cycle of ladle lifting, does not depend on the viscosity of fluid but on the moving speed of a ladle.
(3) The number of cycles required for mixing addition agent uniformly in the ladle is related to the moving speed of ladle and the viscosity of fluid, and isalso closely related to the volume of fluid lifted up into degassing vessel.
Effects of Combined Additions of Al, Be, and Ti on Precipitation Hardening of Fe-Ni Alloys
Masao KANAO, Toru ARAKI, Hideo NUMATA, Keishi NAKANO
pp. 1854-1866
Abstract
Effects of combined additions of Al, Be, and Ti on age hardening characteristics and precipitated phases in Fe-4-7% Ni alloys were investigated. The results obtained were as follows:(1) When Al and Be were added simultanously, the maximum aged hardness obtained was the average of those of the single additions. The precipitated phases were NiAl and NiBe, both being CsCI type. The hardening was considered due to formation of clusters with ordered structure and also to precipitation of NiAl.(2) When Be and Ti were added simultanously, the age hardening effect was found to be additive and NiBe and Ni3Ti phases were separately recognized in the electro-chemically extracted residue.(3) When Al and Ti were both added, fine spherical Ni2AlTi phase was precipitated and the hardness increase due to aging was remarkable.(4) Even if 24% Cr was added to Fe-4% Ni alloys, the combined effect of Al was also recognized. The precipitated phase of Fe-24% Cr-4% Ni-Ti alloy was mainly X phase.
Microstructures and Charpy Fracture Surface Characteristics of Aged Refractaloy 26 Type Alloy and Inconel X Type Alloy
Yoshiaki KANAI
pp. 1867-1879
Abstract
Electron microstructures, precipitates and fracture surface characteristics of Ni-Co-Cr-Fe alloy (Refractaloy 26 type) and Ni-Cr alloy (Inconel X type) for spring at high temperature service are investigated.
These alloys that are optimumly aged in order to get superior properties for spring at high temperature services, are observed for the microstructures, precipitates and fracture surface characteristics with transmission electron microscope and scanning electron microscope. Precipitates, which are the cause of precipitation hardening, are diffracted with X-ray.
The contents of study are as follows;
(1) Effects of aging on the microstructure and precipitate.
(2) Relation between the misfit percent of γ′ to matrix and the rate of increase in hardness.
(3) Effect of aging on the size of γ′.
(4) The measurement of hardness of the γ′ and matrix at high temperature.
(5) Effect of the precipitate on fracture surface characteristics.
Chromizing of Austenitic Heat Resistant Alloys
Jun HOASHI, Mitsunori YOSHIMOTO, Makoto KATSUTA, Hiroshi YOSHIDA
pp. 1880-1890
Abstract
One of the most serious problems in gas turbines in which residual fuel oil is used would be the control of accelerated corrosion caused by fuel ash. In this paper, were studied chromium diffusion coating (chromizing) by powder method for austenitic heat resistant alloys used for gas turbine blades. The depth of chromium diffusion layer and surface chromium concentration of the layer were proved to be determined primarily by chemical compositions of the base alloy when the chromizing condition was fixed.
When super alloys such as S590 or S816 that have low iron contents were chromized by a mixture of chromium powder, alumina powder, and ammonium chloride, the thickness of the layer was limited to a small value mainly because of low diffusion constant of chromium in these alloys.
The maximum depth of the layer on S590 alloy obtained by powder method was 50 microns and surface chromium concentration was 84 wt per cent.
Addition of iron powder in the above chromizing powder showed a considerable effect on the growth of diffusion layer. This effect can be explained by a pronounced increase of chromium diffusion constant caused by dilution of chromium concentration in the layer. Chromium concentration of the layer decreases almost linearly with addition of iron powder. When 8590 alloy was chromized with powder consisted of 20% chromium-10% iron-70% alumina, the surface chromium concentration of the layer was 60 per cent.
Readers Who Read This Article Also Read
Tetsu-to-Hagané Vol.50(1964), No.5
Tetsu-to-Hagané Vol.53(1967), No.11
Tetsu-to-Hagané Vol.54(1968), No.10
Temperature Distribution of Structural Sections during Hot Rolling
Hiroyuki HIRAMATSU, Tatsuhiko EGASHIRA, Koich YUTA, Shinich NAKAMATA
pp. 1891-1898
Abstract
The calculation of temperature drops and distributions during hot rolling has been carried out using the two-dimensional model and the results are compared with measured results. Reasonable agreements of the two have been achieved within the accuracy of temperature measurement in the reversing rail mill, by considering the metal flow, the radiation heat losses and the generation of heat by deformation. However, a difference may be caused by conduction of heat from the sections to water falling or being sprayed on the web of the structural sections.
Outline for the Kinetics of the Reduction of Iron Ore
Masanori TOKUDA, Hideyuki YOSHIKOSHI, Masayasu OHTANI
pp. 1899-1915
Some Phenomena during the Solidication of Steel Ingots
Koichi ASANO, Hisashi MATSUNAGA
pp. 1916-1941
Readers Who Read This Article Also Read
Tetsu-to-Hagané Vol.53(1967), No.11
Tetsu-to-Hagané Vol.51(1965), No.2
Tetsu-to-Hagané Vol.55(1969), No.7
Cast Structure of Ingot
Akira SUZUKI
pp. 1942-1959
Readers Who Read This Article Also Read
Tetsu-to-Hagané Vol.50(1964), No.5
Tetsu-to-Hagané Vol.53(1967), No.11
Tetsu-to-Hagané Vol.54(1968), No.10
Article Access Ranking
29 Aug. (Last 30 Days)
-
Perspectives on the Promising Pathways to Zero Carbon Emissions in the Steel Industry toward 2050
ISIJ International Vol.65(2025), No.2
-
Growth, Removal, and Agglomeration of Various Type of Oxide Inclusions in Molten Steel
Tetsu-to-Hagané Vol.111(2025), No.11
-
Copper removal of liquid steel containing 0.25 % carbon using Fe2O3-CaCl2-SiO2 flux
ISIJ International Advance Publication
-
Finite Element Analysis of Bubble Growth and Particle Swelling during Coal Pyrolysis
ISIJ International Vol.65(2025), No.9
-
Corrosion Behavior of Carbon Steel under Soil Drying Conditions
ISIJ International Advance Publication
-
Cold Spot Joining of 980 MPa-class Ultra-high Strength Steel
Tetsu-to-Hagané Advance Publication
-
Factors Affecting Generation of Iron Fines in Cold Sheet Rolling of Steel
ISIJ International Vol.65(2025), No.9
-
Experimental Study on Heat Transfer Characteristics of a Moving Single-Nozzle Jet Impingement
ISIJ International Vol.65(2025), No.9
-
Combination Effect of Premixing Conditions and Iron Ore Size Distribution in Sintered Ore Granulation Process with Intensive Mixer
ISIJ International Advance Publication
-
Evaluation of Feature Selection Methods for Oxygen Supply Prediction in BOF Steelmaking
ISIJ International Advance Publication
You can use this feature after you logged into the site.
Please click the button below.