- TOP
- Tetsu-to-Hagané
- Vol. 56 (1970), No. 8
Tetsu-to-Hagané Vol. 56 (1970), No. 8
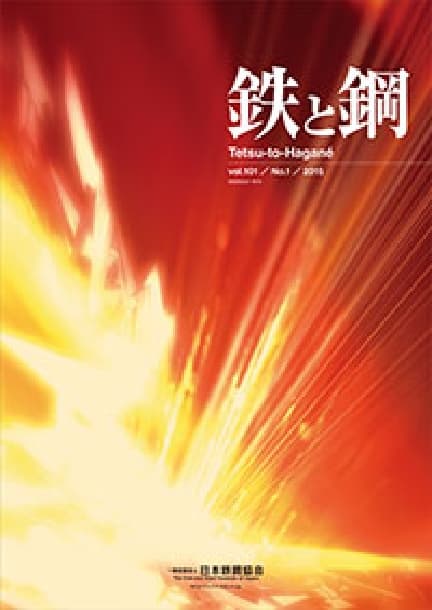
Grid List Abstracts
ONLINE ISSN: | 1883-2954 |
PRINT ISSN: | 0021-1575 |
Publisher: | The Iron and Steel Institute of Japan |
Backnumber
-
Vol. 111 (2025)
-
Vol. 110 (2024)
-
Vol. 109 (2023)
-
Vol. 108 (2022)
-
Vol. 107 (2021)
-
Vol. 106 (2020)
-
Vol. 105 (2019)
-
Vol. 104 (2018)
-
Vol. 103 (2017)
-
Vol. 102 (2016)
-
Vol. 101 (2015)
-
Vol. 100 (2014)
-
Vol. 99 (2013)
-
Vol. 98 (2012)
-
Vol. 97 (2011)
-
Vol. 96 (2010)
-
Vol. 95 (2009)
-
Vol. 94 (2008)
-
Vol. 93 (2007)
-
Vol. 92 (2006)
-
Vol. 91 (2005)
-
Vol. 90 (2004)
-
Vol. 89 (2003)
-
Vol. 88 (2002)
-
Vol. 87 (2001)
-
Vol. 86 (2000)
-
Vol. 85 (1999)
-
Vol. 84 (1998)
-
Vol. 83 (1997)
-
Vol. 82 (1996)
-
Vol. 81 (1995)
-
Vol. 80 (1994)
-
Vol. 79 (1993)
-
Vol. 78 (1992)
-
Vol. 77 (1991)
-
Vol. 76 (1990)
-
Vol. 75 (1989)
-
Vol. 74 (1988)
-
Vol. 73 (1987)
-
Vol. 72 (1986)
-
Vol. 71 (1985)
-
Vol. 70 (1984)
-
Vol. 69 (1983)
-
Vol. 68 (1982)
-
Vol. 67 (1981)
-
Vol. 66 (1980)
-
Vol. 65 (1979)
-
Vol. 64 (1978)
-
Vol. 63 (1977)
-
Vol. 62 (1976)
-
Vol. 61 (1975)
-
Vol. 60 (1974)
-
Vol. 59 (1973)
-
Vol. 58 (1972)
-
Vol. 57 (1971)
-
Vol. 56 (1970)
-
Vol. 55 (1969)
-
Vol. 54 (1968)
-
Vol. 53 (1967)
-
Vol. 52 (1966)
-
Vol. 51 (1965)
-
Vol. 50 (1964)
-
Vol. 49 (1963)
-
Vol. 48 (1962)
-
Vol. 47 (1961)
-
Vol. 46 (1960)
-
Vol. 45 (1959)
-
Vol. 44 (1958)
-
Vol. 43 (1957)
-
Vol. 42 (1956)
-
Vol. 41 (1955)
Keyword Ranking
29 Aug. (Last 30 Days)
Tetsu-to-Hagané Vol. 56 (1970), No. 8
The Desulphurization Velocity by the Rotating Cylinder of Calcium Carbide in Molten Carbon-Saturated Iron
Hiroshi OOI, Yukio OGUTI, Hakaru MINAMI
pp. 991-997
Abstract
The desulphurization velocity of molten iron saturated with carbon by rotating calcium carbide cylinder has been investigated in temperature from 1250° to 1450°C.
Results obtained are as follows:
1) The mass transfer coefficient for the desulphurization reaction may be written by the following equation,
JD=k/U (SC) 0.28=0.038 (Re) -0.49
which is quite similar to the mass transfer coefficients for the dissolution of rotating benzoic acid cylinder into the water.
2) The activation energy for the desulphurization reaction obtained from this experiments was 13.4±7.4 kcal/mol. This agrees well with 6.5-18.4 kcal/mol calculated from the equation of mass transfer coefficient using activation energies of sulphur diffusion and viscosity of molten iron saturated with carbon.
On the Deoxidation of Liquid Iron with Argon-Calcium Bubbles
Saburo KOBAYASHI, Yasuo OMORI, Koji SANBONGI
pp. 998-1013
Abstract
In order to pursue a possibility of application of metallic gas bubble to the cleaning of iron and steel melt, a study was made of the deoxidation characteristics of Ar-Ca gas bubble floating up in iron melt. The results of this study will also give some fundamental information on the behavior of complex deoxidizider containing calcium. The results obtained are as follows;
1) At 1550°C, e (Ca) O=-535, e (O) Ca=-1330 for interaction parameter, log KCa=log aCa·aO=-9.82 for equilibrium constant KCa of a reaction [Ca] + [O] =CaO, and log [%Ca] [%O] /PCa (atm) =-3.86 for the equilibrium relation between the melt and Ca vapour pressure.
2) [O] decreased with increase of the amount of Ca added in a form of straight line in the range of high oxygen content ( [O] >150 ppm) and in a form exponential line in the range of the low content ( [O] <100 ppm). It could be interpreted that the reaction Ca-O was controled by the supply of calcium from the bubble to reaction place in the former and by the supply of oxygen from the bulk of the melt to the place in the latter.
3) The melt deoxidzed with Ar-Ca gas bubble was free from the product CaO, probably owing to removal of it with the bubble, and it was easy to attain to high efficiency of calcium utilization by increasing of floating distance of the bubble.
Readers Who Read This Article Also Read
Tetsu-to-Hagané Vol.49(1963), No.2
Tetsu-to-Hagané Vol.55(1969), No.2
Tetsu-to-Hagané Vol.53(1967), No.7
The Effect of Mo, N, and C on High Temperature Properties of 25%Cr-28%Ni Heat Resisting Steels
Ryohei TANAKA, Takayuki SHINODA, Yoichiro TOBE
pp. 1014-1033
Abstract
Creep rupture strength has been measured at 700°C and microstructure has been examined during aging at 700, 800, and 900°C in 25Cr-28Ni steels containing up to 6%M, 0.54%N, and 0.35%C.
Sigma phase is formed both at grain boundaries and within grains in the steels with low nitrogen and high molybdenum content. Precipitation of chromium nitride (Cr2N) in addition to sigma phase takes place in the steels containing low nitrogen and low molybdenum content. Only chromium nitride (Cr2N) is precipitated by grain boundary reaction, then grains become in being covered with that in the steels containing low molybdenum and high nitrogen content. A large amount of Cr23C6is precipitated within all over the grain in the steels with high carbon content.
Addition of up to 2%Mo increases remarkably the creep rupture strength, but further addition of molybdenum more than 2% does not increase so much the strength. Nitrogen without molybdenum improves on it slightly, but the molybdenum-bearing steels containing more than 0.2%N gives the highest strength. Carbon up to 0.2% with 2%Mo improves on high temperature strength, but further addition of carbon does not improve on it. Creep rupture strength of nitrogen-bearing steels with low carbon content is higher than that of steels with high carbon content.
The steels with a higher recrystallization temperature give a higher creep rupture strength at 700°C.
Statistical Analysis of Creep Data
Tomoyoshi KAWADA, Shin YOKOI, Chiaki TANAKA, Yoshio MONMA, Norio SHINYA
pp. 1034-1055
Abstract
In the presentation of creep data on the materials for elevated temperature use, it is most desirable to analyse them by use of statistical procedures and express the results in objective form.
In this paper an attempt has been made to fit statistically regression curves for the creep data actually obtained for 21/4Cr-1Mo, 1Cr-1Mo-1/4V, 18Cr-10Ni-Ti and 16Cr-13Ni-3Mo steels, concerning relations of stress vs. rupture-time, stress vs. minimum creep rate and stress vs. parameters (LARSONMILLER etc.), which contain rupture-time and temperature or creep rate and temperature.
The results obtained are as follows;
(1) The maximum significant degree of polynomials used for the regression equations for curve fitting turns out to be the third (cubic).
(2) The frequency distribution of residuals obtained from the estimated value and the observed value of logarithms of the rupture-time, the minimum creep rate and the parameters shows normality.
(3) There are some cases where a segmentwise regression curve composed of two straight lines fits the data better than a single curve with an increased degree of regression.
(4) The propriety of the general use of twenty as the value of the constant C in LARSON-MILLER parameter is confirmed statistically. It should be noted, however, that there are some cases where the contribution in curve fitting suddenly deteriorates when the constant C increase over twenty.
(5) As the results of the statistical studies regarding the comparison of the three different parameter methods, the MANSON'S parameter method is shown to be better than the LARSON-MILLER'S and DORN'S methods in respect of curve fitting for the creep rupture data.
Construction and Operation of the Kimitsu Iron Works, Yawata Iron & Steel Co., Ltd.
Shunzo FUJIKI
pp. 1056-1088
Abstract
Kimitsu Works is one of the world's most modern steel mills. It is located in Chiba Prefecture near Tokyo, facing the Bay of Tokyo.
Yawata Iron & Steel Co., Ltd. has devoted a great number of personnel and up-to-date techniques to the construction of this new steel mill in order to meet an increasing demand for steel in the Kanto area, one of the biggest steel markets in Japan, as well as to cope with severe competition.
Annual steel ingot production in Kimitsu Works after completion of the 1st phase construction will reach 5 000 000 tons. Ultimately this works will produce 12 000 000 tons of ingots per year after completion of the 2nd phase construction.
This paper summarizes the 1st phase construction and operation.
Kimitsu Works was constructed on reclaimed land like most other Japanese integrated steel works. The first blast furnace was blown-in on November 27, 1968 only one year and nine months after the reclaiming started in March, 1967. The blowing-in of the second blast furnace took place on October 1, 1969. The 1st phase construction was thus completed in a surprisingly short length of time.
The world's largest and most modern equipment is installed at the mill. Ideally planned from its beginnings as an integrated works, the plant features the latest in layout and machinery. The application of a computer system, a modernized transportation system and an efficient control system ensures smooth operation of the mill.
An integrated process from rolling to fabrication is planned for the 2nd phase construction in order to meet diversified steel demand. In addition, the 2nd phase will serve to stengthen and increase equipment capacity. Thus a vast steel complex will be formed at Kimitsu after completion of the 2nd phase construction.
Rolling Theory and Its Application
Samon YANAGIMOTO, Toshitaka TAMANO
pp. 1118-1135
Readers Who Read This Article Also Read
Tetsu-to-Hagané Vol.92(2006), No.11
Tetsu-to-Hagané Vol.65(1979), No.11
Effect of Various Specimen Sizes on Elongation in Tensile Strength
日本鉄鋼協会, 標準化委員会データシート部会, 伸び値と試験片寸法効果分科会
pp. 1136-1142
Article Access Ranking
29 Aug. (Last 30 Days)
-
Perspectives on the Promising Pathways to Zero Carbon Emissions in the Steel Industry toward 2050
ISIJ International Vol.65(2025), No.2
-
Growth, Removal, and Agglomeration of Various Type of Oxide Inclusions in Molten Steel
Tetsu-to-Hagané Vol.111(2025), No.11
-
Copper removal of liquid steel containing 0.25 % carbon using Fe2O3-CaCl2-SiO2 flux
ISIJ International Advance Publication
-
Finite Element Analysis of Bubble Growth and Particle Swelling during Coal Pyrolysis
ISIJ International Vol.65(2025), No.9
-
Corrosion Behavior of Carbon Steel under Soil Drying Conditions
ISIJ International Advance Publication
-
Cold Spot Joining of 980 MPa-class Ultra-high Strength Steel
Tetsu-to-Hagané Advance Publication
-
Factors Affecting Generation of Iron Fines in Cold Sheet Rolling of Steel
ISIJ International Vol.65(2025), No.9
-
Experimental Study on Heat Transfer Characteristics of a Moving Single-Nozzle Jet Impingement
ISIJ International Vol.65(2025), No.9
-
Combination Effect of Premixing Conditions and Iron Ore Size Distribution in Sintered Ore Granulation Process with Intensive Mixer
ISIJ International Advance Publication
-
Evaluation of Feature Selection Methods for Oxygen Supply Prediction in BOF Steelmaking
ISIJ International Advance Publication
You can use this feature after you logged into the site.
Please click the button below.