- TOP
- Tetsu-to-Hagané
- Vol. 70 (1984), No. 6
Tetsu-to-Hagané Vol. 70 (1984), No. 6
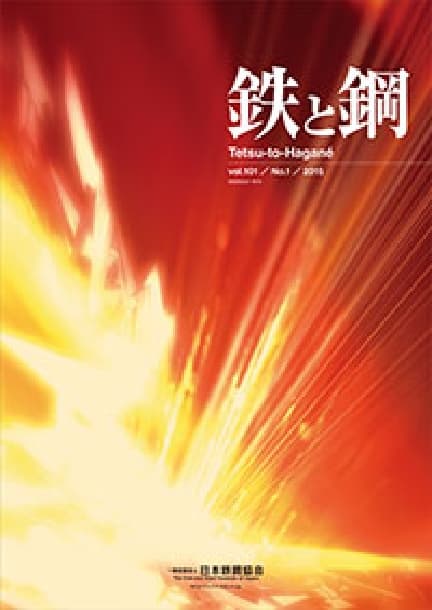
Grid List Abstracts
ONLINE ISSN: | 1883-2954 |
PRINT ISSN: | 0021-1575 |
Publisher: | The Iron and Steel Institute of Japan |
Backnumber
-
Vol. 111 (2025)
-
Vol. 110 (2024)
-
Vol. 109 (2023)
-
Vol. 108 (2022)
-
Vol. 107 (2021)
-
Vol. 106 (2020)
-
Vol. 105 (2019)
-
Vol. 104 (2018)
-
Vol. 103 (2017)
-
Vol. 102 (2016)
-
Vol. 101 (2015)
-
Vol. 100 (2014)
-
Vol. 99 (2013)
-
Vol. 98 (2012)
-
Vol. 97 (2011)
-
Vol. 96 (2010)
-
Vol. 95 (2009)
-
Vol. 94 (2008)
-
Vol. 93 (2007)
-
Vol. 92 (2006)
-
Vol. 91 (2005)
-
Vol. 90 (2004)
-
Vol. 89 (2003)
-
Vol. 88 (2002)
-
Vol. 87 (2001)
-
Vol. 86 (2000)
-
Vol. 85 (1999)
-
Vol. 84 (1998)
-
Vol. 83 (1997)
-
Vol. 82 (1996)
-
Vol. 81 (1995)
-
Vol. 80 (1994)
-
Vol. 79 (1993)
-
Vol. 78 (1992)
-
Vol. 77 (1991)
-
Vol. 76 (1990)
-
Vol. 75 (1989)
-
Vol. 74 (1988)
-
Vol. 73 (1987)
-
Vol. 72 (1986)
-
Vol. 71 (1985)
-
Vol. 70 (1984)
-
Vol. 69 (1983)
-
Vol. 68 (1982)
-
Vol. 67 (1981)
-
Vol. 66 (1980)
-
Vol. 65 (1979)
-
Vol. 64 (1978)
-
Vol. 63 (1977)
-
Vol. 62 (1976)
-
Vol. 61 (1975)
-
Vol. 60 (1974)
-
Vol. 59 (1973)
-
Vol. 58 (1972)
-
Vol. 57 (1971)
-
Vol. 56 (1970)
-
Vol. 55 (1969)
-
Vol. 54 (1968)
-
Vol. 53 (1967)
-
Vol. 52 (1966)
-
Vol. 51 (1965)
-
Vol. 50 (1964)
-
Vol. 49 (1963)
-
Vol. 48 (1962)
-
Vol. 47 (1961)
-
Vol. 46 (1960)
-
Vol. 45 (1959)
-
Vol. 44 (1958)
-
Vol. 43 (1957)
-
Vol. 42 (1956)
-
Vol. 41 (1955)
Keyword Ranking
04 Sep. (Last 30 Days)
Tetsu-to-Hagané Vol. 70 (1984), No. 6
Kinetics of Reducibility of Sinter
Noboru SAKAMOTO, Hiroshi FUKUYO, Yoshihito IWATA, Tsuneo MIYASHITA
pp. 504-511
Abstract
In order to produce sinter with high reducibility, a relation between sinter structure and its reducibility has been quantitatively investigated. Typical sinter structures and single mineral phases were synthesized using chemical reagents. An one-interface unreacted core model was applied to obtain the reduction rate parameters on these structures and the phases.
(1) The reducibility of the diffusion bonded type sinter was higher than that of the melting one, because of its high diffusivity of reducing gas through the reduced layer.
(2) As a result of the reduction tests on the single mineral phase, it was proved that the reducibility of the fine type hematite and calciumferrite were higher than that of the prismatic type calciumferrite in slag melt, because of the same reason as described above.
(3) By knowing the reducibility of the single mineral phase and each ratio of the phase in the sinter structure, the reducibility of their complex structures can be nearly estimated.
Readers Who Read This Article Also Read
Tetsu-to-Hagané Vol.70(1984), No.6
Tetsu-to-Hagané Vol.55(1969), No.9
Tetsu-to-Hagané Vol.73(1987), No.15
Mineralogical Study on Degradation of Sinter Structure at Low Temperature Reduction
Noboru SAKAMOTO, Hiroshi FUKUYO, Yoshihito IWATA, Tsuneo MIYASHITA
pp. 512-519
Abstract
A study on degradation of sinter structure during low temperature reduction has been made by considering strain formation in mineral phases and propagation of crack in the structure.
The results obtained are summarized as follows:
(1) The degradation is observed in any sinter structure, however the cracks propagated through melting bonded sinter structures are comparatively longer than that through diffusion bonded ones.
(2) X-ray diffraction patterns indicate that the spacing of lattice planes of alumina containing skeletal hematite are shrinked compared to that of fine type hematite. One of the causes of the degradation is considered to be due to the shrinkage.
(3) X-ray line broadening analysis revealed that the value of nonuiform strain in magnetite phase obtained from 550°C reduction was higher than that from 900°C reduction. The higher nonuniform strain is considered to cause the degradation during only low temperature reduction.
(4) By a statistical analysis of the crack propagations through various mineral phases, prismatic type calciumferrite and glassy slag were estimated to be unsuitable for sinter structure.
Readers Who Read This Article Also Read
Tetsu-to-Hagané Vol.70(1984), No.6
Tetsu-to-Hagané Vol.55(1969), No.9
Tetsu-to-Hagané Vol.73(1987), No.15
Fundamental Study on the Sintering Process Using Duplex Mini-pellets
Eiki KASAI, Ienbin SHU, Saburo KOBAYASHI, Yasuo OMORI
pp. 520-526
Abstract
A new sintering process was proposed which may cope with the increase in the ratio of fine iron ores. The basic concept associated with the new process using double layered mini-pellets (named duplex mini-pellets) was presented. The sintering experiments were conducted by using duplex mini-pellets and the quality of the produced sinter was evaluated by the various physical tests.
(1) Excellent permeability was observed for the sintering bed using the duplex mini-pellets compared with that for the current sinter practice.The bed-permeation resistance was reduced because size and structure of the pellets remained unchanged in the course of sintering before the fusion.
(2) By selecting the low melting region in CaO-Fe2O3 phase diagram as the chemical composition of the shell layer fines (CaO 20 wt%, Fe2O3 80 wt%), the sintering of the duplex mini-pellets was achieved at low temperature around 1230°C.
(3) The sinter produced by the method mentioned above had the texture of primary hematite and binary calciumferrite without secondary hematite.
(4) The sinter having such texture had excellent metallurgical properties, that is to say, low RDI, high JIS RI and good softening and melt-down properties.
Effects of Sulfur on High Temperature Softening-melting Properties of Acid Pellets
Rokuro KUWANO, Ynichi ONO
pp. 527-532
Abstract
Effects of H2S on the softening-melting properties of pellets during reduction under load have been experimentally studied with seven different brands of industrial pellets and an Fe2O3 pellet as samples. The results show that the presence of H2S in reducing gas has detrimental effects on the high temperature properties of the pellets. For example, the addition of only 0.1% of H2S to 35%CO-65% N2 gas mixture increased extremely the shrinking velocity of the pellets due to softening, although it hardly affected the reduction rate. Formation of easy-melting eutectic liquid from FeS and FeO has been found to be the main cause of the above-mentioned effects.
Readers Who Read This Article Also Read
Tetsu-to-Hagané Vol.70(1984), No.6
Thermodynamic Considerations on Manganese Equilibria between Liquid Iron and FetO-MnO-MOx(MOx=PO2.5, SiO2, AlO1.5, MgO, CaO) Slags
Hideaki SUITO, Ryo INOUE
pp. 533-540
Abstract
The previous results on manganese distribution between liquid iron and FetO-containing slags have been summarized. The apparent equilibrium constant K'Mn=NMnO/([%Mn]·NFetO) in the FetO-MnO slags can be expressed as log K'Mn=7572/T-3.559
The variations of K'Mn with slag compositions in the FetO-MnO-MOX(MOX=PO2.5, SiO2, AlO1.5, MgO, CaO) ternary melts as well as in MgO-saturated CaO-FetO-SiO2-MnO slags have been discussed on the basis of the regular solution model and the RICHARDSON's ideal silicate mixing.
Readers Who Read This Article Also Read
Tetsu-to-Hagané Vol.70(1984), No.6
Local Corrosion of Blast Furnace Trough Material at the Slag-metal Interface
Kusuhiro MUKAI, Jyouki YOSHITOMI, Tsutomu HARADA, Kouichi HURUMI, Shoichiro FUJIMOTO
pp. 541-548
Abstract
Local corrosion of clay bonded SiC specimen at the liquid iron alloy-slag interface has been investigated at 1550°C in order to elucidate the mechanism of local attack of blast furnace trough material at the slag-metal interface. Results obtained are as follows:
Local corrosion arises in the narrow zone just below the two liquid interface, regardless of partial pressure of oxygen of gas phase and also impurities contained in pig iron and slag. The extent of the corrosion depends on carbon concentration of the metal. The corrosion zone has a thin slag film between the specimen and the metal phase. It is estimated that the slag film plays important roles in the occurrence of the local corrosion because of its vigorous movements which accelerate the mass transfer and the abrasion of the specimen.
This movements are caused by the Marangoni effect and CO bubbles evolved as a product of SiO2 reduction in the film by carbon in the metal. SiC granules on the surface of the specimen are oxidized by iron oxide in the film into carbon granules, which may facilitate the abrasion of the specimen by the turbulence of the film in the case of the metal not saturated with carbon. When the metal is saturated with carbon, the carbon granules remain in the film and may supress the local corrosion.
Readers Who Read This Article Also Read
Tetsu-to-Hagané Vol.73(1987), No.15
Tetsu-to-Hagané Vol.62(1976), No.14
Tetsu-to-Hagané Vol.70(1984), No.8
Knudsen Cell Mass Spectrometric Study of the Thermodynamic Properties of Fe-W Alloys
Yoshiyuki UESHIMA, Hisashi YAMANA, Toyoko SUGIYAMA, Eiji ICHISE
pp. 549-556
Abstract
High temperature thermodynamic properties of Fe-W alloys were studied by the use of Knudsen cell mass spectrometer. As this alloy system has only single volatile component, the internal standard method was utilized to obtain activities in alloys. By taking advantage of high melting point of Fe-W alloys, Fe was used as the standard material. In applying this technique, the effect of the height of sample surface in the cell on the ion intensity was taken into consideration. Samples were melted and solidified preliminarily in a Knudsen cell before each run and then iron foil was placed on the sample surface so that the change in the height of sample surface in the cell on melting during the measurement was minimized.
Activities and free energy and enthalpy of mixing were derived at 1873 and 1773 K. The following were obtained
γ°W(S)=7.6(±1.1), εWW=-2.2(±0.8), at 1873K
Values for the activities of Fe-Mo alloys were revised on the basis of the present knowledge about the influence of the height of sample surface on the ion intensity. The following values were obtained.
γ°Mo(S)=2.2(±0.17), εMoMo=-0.14(±0.18) at 1823K
Diffusional Transformation Kinetics from Work-hardened Austenite
Minoru UMEMOTO, Hideyuki OHTSUKA, Imao TAMURA
pp. 557-564
Abstract
The deformation of austenite below its recrystallization temperarure markedly accelerates the subsequent diffusional transformation. This acceleration is mostly caused by the increase in the nucleation rate. The increase in the nucleation rate per unit volume of specimen is attributed (1) to the increase in the austenite grain area by the elongation of grains, (2) to the increase in the nucleation rate per se per unit area of grain surface, and (3) to the formation of additional nucleation sites such as annealing twin boundaries, deformation bands, etc. Considering these effects, a kinetic equation for the deformed sepcimens was derived and from this equation, a method to estimate quantitatively the individual effect of the above three factors on the increase in the transformation rate was developed by defining the acceleration multiplying factors. Furthermore, the effects of the amout of rolling reduction and austenite grain size on the individual effect of the three factors on the acceleration of transformation were discussed based on the derived kinetic equation. Finally, as an application of the developed method, the acceleration multiplying factors for the pearlite transformation in the hot-rolled SKD 6 steel were calculated as functions of rolling reduction and austenite grain size.
Creep Damage of 1Cr-1Mo-1/4V Steel
Takashi MATSUO, Tetsuya KISANUKI, Ryohei TANAKA, Shyuichi KOMATSU
pp. 565-572
Abstract
Microstructural changes and degradation of high temperature tensile properties due to creep damage have been studied on 1Cr-1Mo-1/4V steel specimens obtained by interrupting the creep test up to 9 000 h at 600°C.
The loss of strength in the 1Cr-1 Mo-1/4V steel after long term creep exposure is due to three mechanisms: (I) the strength loss accompanying the change in the carbide morphology that usually occurs during tempering, (2) the strength loss resulted from local recovery of ferrite matrix in the vicinity of prior austenite grain boundary carbide particles, and (3) the strength loss due to formation of voids and cracks.
It is considered that the progress of creep damage during primary creep stage is attributed mainly to the first mechanism, and that of tertiary creep to the second one which is most important. On the other hand, no crack and the limited numbers of voids were observed at the grain boundary, then it is assumed that the third one is not essentially responsible for creep damage of Cr-Mo-V steel studied.
An Assessment of Creep Damage by Density Change Measurements for Cr-Mo-V Steel
Norio SHINYA, Junro KYONO, Shin YOKOI
pp. 573-579
Abstract
Creep cavity populations and resultant density changes have been measured on interrupted creep specimens with aim of assessing the bulid up of creep damage in Cr-Mo-V steel that eventually leads to fracture.
Metallographic observations have shown two types of creep cavities associated with either grain boundary carbides or with non-metallic inclusions. The number of creep cavities associated with grain boundary carbides increases linearly with increasing creep strain and growth of the cavities along grain boundaries leads to grain boundary cracks, whereas nucleation and growth of the creep cavities associated with non-metallic inclusions are limited by the number and size of the inclusions. The data of density change is expressed reasonably by the empirical equation
-ΔD/D=2.5×103εtσ3.0exp(-234000/RT)
where ΔD/D is the density change, εis the creep strain (%), t is the time (h), σis the stress (kgf/mm2), R is the gas constant (8.314 J·mol-1·K-1), and T is the absolute temperature (K). This equation can be used to estimate the residual life of Cr-Mo-V steel components working under creep conditions.
On Sliding Wear of Ultra-high Carbon-Chromium Steels
Hisakichi SUNADA, Hisashi IZUMI, Imao TAMURA
pp. 580-587
Abstract
The sliding wear performance of high carbon-chromium steels has been investigated. The specimens were prepared by hot forging and isothermal rolling in order that the sizes of grains and size, shape and distributed carbide particles were varied. The wear tests were carried out by changing contact load, hardness of specimen and contact ring without lubricant. The wear resistance was determined by weight loss after 100 h sliding.
The results obtained were as follows:
1) The wear loss of quenched and tempered structure increased with increasing the contact load, decreasing the hardness of specimen and decreasing the ring hardness.
2) For as-worked structure, forged or pearlite structure had more improved wear resistance than rolled or ferritic structure. While wear resistance of rolled structure was better than that of forged one in the case of quenched-and-tempered structure.
3) As-forged structure which consisted of pearlite showed as much waer resistance as quenched structure.
4) Wear surface was flat in the case of hard specimen against hard ring, whereas combination of soft-soft tended to become rough. The thickness of wear damaged layer was almost constant in spite of hardness or structure.
Influence of C, N and Ni Contents and Temper Rolling on Intergranular Corrosion and Mechanical Properties of 17Cr-7Ni Steel
Hiroshi HIRAMATSU, Michio NAKATA, Hidehiko SUMITOMO, Hirofumi YOSHIMURA
pp. 588-595
Abstract
A study has been made of the influence of C, N and Ni contents and temper rolling on intergranular corrosion and mechanical properties of a 17Cr-7Ni steel, in order to develop a high strength stainless steel with high corrosion resistance. The results obtained are as follows:
(1) Intergranular corrosion sensitivity increases with increasing C content or temper rolling reduction. (2) 0.2% proof stress of annealed materials increases with increasing (C+2N) content. Tensile stress decreases with increasing stability of austenite phase, and increases with increasing C or N content in the case of the same austenite stability. Elongation increases with increasing austenite stability.
(3) The influence of C, N and Ni contents on the tensile properties of 25% temper rolled materials is similar to that on annealed materials and 0.2% proof stress increases with (2C+N) content. (4) The strengths of austenite and martensite phase increase with increasing C or N content. The effect of C content is smaller in austenite phase and is larger in martensite phase compared with the effect of N content. (5) Tensile stress and elongation of steel with 0.2% proof stress of 780 MPa increase with increasing C and N contents and decreasing Ni content. The optimum composition of 0.02C-17Cr-6.7Ni-0.12N has been determined by the consideration of corrosion resistance and high strength.
Development of 60 kgf/mm2 Steel for Power-transmission Pipe Tower and Its Resistance to Liquid Zinc Embrittlement
Tetsujiro TAKEDA, Ken KANAYA, Kazunari YAMATO, Kiyotsugu EIRO, Zensaku CHANO, Shogo KANAZAWA, Teruo HIROKI, Tooru IEZAWA
pp. 596-602
Abstract
There are many recently constructed power-transmission steel towers that are larger in size than ordinary ones. Higher strength steel is considered necessary for the large size tower to reduce its weight. Besides usual mechanical properties, the steel must have the resistance to zinc coating-induced cracking (ZIC) due to liquid metal embrittlement (LME).
1) Testing methods are developed to evaluate the ZIC susceptibility quantitatively. 2) Index for the ZIG susceptibility (S400LM) is expressed as a function of chemical composition of steel. If the value of S400LM is larger than 42%, the ZIC would not occur. 3) New 60 kg/mm2 steels are developed as plate, UO pipe and ERW pipe for the use of a power-transmission tower. The steels show the excellent resistance properties to the ZIC and mechanical properties including buckling properties of pipes.
Manufacturing Process and Properties of Iron and Steel Foil
Nobuyuki TSUTSUI, Yoshihiro TANAKA, Kazuyuki KOIKE
pp. 603-607
Article Access Ranking
04 Sep. (Last 30 Days)
-
Perspectives on the Promising Pathways to Zero Carbon Emissions in the Steel Industry toward 2050
ISIJ International Vol.65(2025), No.2
-
Growth, Removal, and Agglomeration of Various Type of Oxide Inclusions in Molten Steel
Tetsu-to-Hagané Vol.111(2025), No.11
-
Finite Element Analysis of Bubble Growth and Particle Swelling during Coal Pyrolysis
ISIJ International Vol.65(2025), No.9
-
Interface behavior leading to Al/Cu dissimilar metal bonding formation with high-speed eutectic reaction induced by applying current
QUARTERLY JOURNAL OF THE JAPAN WELDING SOCIETY Vol.43(2025), No.2
-
Corrosion Behavior of Carbon Steel under Soil Drying Conditions
ISIJ International Advance Publication
-
Cold Spot Joining of 980 MPa-class Ultra-high Strength Steel
Tetsu-to-Hagané Advance Publication
-
Combination Effect of Premixing Conditions and Iron Ore Size Distribution in Sintered Ore Granulation Process with Intensive Mixer
ISIJ International Advance Publication
-
A preliminary study on reduction degradation of iron ore sinter using sinter analogue and X-ray micro-computed tomography (MCT)
ISIJ International Advance Publication
-
Copper removal of liquid steel containing 0.25 % carbon using Fe2O3-CaCl2-SiO2 flux
ISIJ International Advance Publication
-
Evaluation of Feature Selection Methods for Oxygen Supply Prediction in BOF Steelmaking
ISIJ International Advance Publication
You can use this feature after you logged into the site.
Please click the button below.