- TOP
- Tetsu-to-Hagané
- Vol. 54 (1968), No. 7
Tetsu-to-Hagané Vol. 54 (1968), No. 7
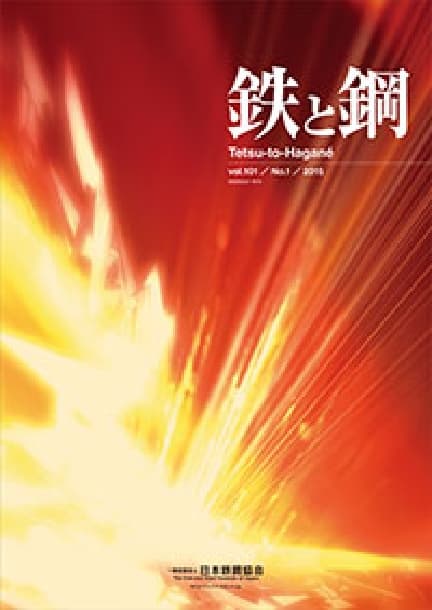
Grid List Abstracts
ONLINE ISSN: | 1883-2954 |
PRINT ISSN: | 0021-1575 |
Publisher: | The Iron and Steel Institute of Japan |
Backnumber
-
Vol. 111 (2025)
-
Vol. 110 (2024)
-
Vol. 109 (2023)
-
Vol. 108 (2022)
-
Vol. 107 (2021)
-
Vol. 106 (2020)
-
Vol. 105 (2019)
-
Vol. 104 (2018)
-
Vol. 103 (2017)
-
Vol. 102 (2016)
-
Vol. 101 (2015)
-
Vol. 100 (2014)
-
Vol. 99 (2013)
-
Vol. 98 (2012)
-
Vol. 97 (2011)
-
Vol. 96 (2010)
-
Vol. 95 (2009)
-
Vol. 94 (2008)
-
Vol. 93 (2007)
-
Vol. 92 (2006)
-
Vol. 91 (2005)
-
Vol. 90 (2004)
-
Vol. 89 (2003)
-
Vol. 88 (2002)
-
Vol. 87 (2001)
-
Vol. 86 (2000)
-
Vol. 85 (1999)
-
Vol. 84 (1998)
-
Vol. 83 (1997)
-
Vol. 82 (1996)
-
Vol. 81 (1995)
-
Vol. 80 (1994)
-
Vol. 79 (1993)
-
Vol. 78 (1992)
-
Vol. 77 (1991)
-
Vol. 76 (1990)
-
Vol. 75 (1989)
-
Vol. 74 (1988)
-
Vol. 73 (1987)
-
Vol. 72 (1986)
-
Vol. 71 (1985)
-
Vol. 70 (1984)
-
Vol. 69 (1983)
-
Vol. 68 (1982)
-
Vol. 67 (1981)
-
Vol. 66 (1980)
-
Vol. 65 (1979)
-
Vol. 64 (1978)
-
Vol. 63 (1977)
-
Vol. 62 (1976)
-
Vol. 61 (1975)
-
Vol. 60 (1974)
-
Vol. 59 (1973)
-
Vol. 58 (1972)
-
Vol. 57 (1971)
-
Vol. 56 (1970)
-
Vol. 55 (1969)
-
Vol. 54 (1968)
-
Vol. 53 (1967)
-
Vol. 52 (1966)
-
Vol. 51 (1965)
-
Vol. 50 (1964)
-
Vol. 49 (1963)
-
Vol. 48 (1962)
-
Vol. 47 (1961)
-
Vol. 46 (1960)
-
Vol. 45 (1959)
-
Vol. 44 (1958)
-
Vol. 43 (1957)
-
Vol. 42 (1956)
-
Vol. 41 (1955)
Keyword Ranking
29 Aug. (Last 30 Days)
Tetsu-to-Hagané Vol. 54 (1968), No. 7
Thermodynamic Properties of Niobium Carbides and Nitrides in Steels
Toshisada MORI, Masaharu TOKIZANE, Ko YAMAGUCHI, Eihachiro SUNAMI, Yoshiyuki NAKAZIMA
pp. 763-776
Abstract
The crystallographic structure and the chemical composition of precipitated δ-phase, δ′-phase and ε-phase were extensively investigated on those specimens which had been prepared from vacuum melted high-purity Fe-Nb-C, Fe-Nb-N and Fe-Nb-C-N alloys containing niobium up to 0.95%. The specimens were solution treated at 1300 or 1350°C for 2hr, and then these were again quenched into water after long time holding at respective temperatures of 1000 to 1300°C. The quantitative determination of soluble-niobium, -carbon and -nitrogen was also investigated in order to calculate the solubility products of niobium-carbide and -nitride in austenite. Results obtained are as follows;
1) The chemical composition of pure δ-niobium-carbide precipitates was determined to be NbC0.87 though the precipitated δ-phase was not pure carbide but carbonitride even in the Fe-Nb-C alloys containing little nitrogen.
2) The precipitated δ′-nitride in Fe-Nb-N alloys containing little carbon was substantially carbonitride containing a little amount of carbon, while the precipitated ε-nitride was estimated to be a pure niobium-nitride NbN.
3) The solubility products of niobium-carbide and -nitride in austenite were given respectively by the following equations;
log [%Nb][%C]0.87=-7, 700/T+3.18
log [%Nb][%N]=-10.150/T+3.79
4) It has been proved that oxygen has the stronger affinity to niobium than carbon and nitrogen in austenite. The preferential precipitation of a little amount of tapiolite [(Fe, Nb) O2 or FeO. Nb2O5] was recognized in all specimens.
Readers Who Read This Article Also Read
ISIJ International Vol.43(2003), No.9
Tetsu-to-Hagané Vol.56(1970), No.10
Tetsu-to-Hagané Vol.53(1967), No.11
On the Isothermal Age-hardening of Fe-Ni-Mn Martensitic Alloys
Minoru TANAKA, Tommo SUZUKI, Masayoshi YODOGAWA
pp. 776-786
Abstract
The age-hardening behaviours of the Fe-Ni-Mn martensitic alloys have been studied in relation to hardness, microstructure, lattice constant, electrical resistivity and magnetic properties comparing with those of the non-age-hardenable Fe-Ni and Fe-Mn martensitic alloys. The results obtained in this study are summarized as follows.
(1) In the age-hardenable Fe-Ni-Mn alloys, the matrix becomes etchable accompanying the reveal of fine particles during age-hardening. In this hardening stage, the electrical resistivity decreases and the lattice constant of matrix is maintained in almost constant while the half width of X-ray diffraction line increases. The reversion can be observed in the age-hardened Fe-Ni-Mn alloys.
(2) In the non-age-hardenable Fe-Ni alloy, austenite appears during aging and grows in lameller and the half width decreases abruptly on a short time aging.
(3) Although the age-hardening of Fe-Ni-Mn martensitic alloys cannot be ascribed to one factor, it seems likely that the strain hardening due to the formation of the coherent precipitate or zone in the matrix is a major factor. It is difficult to consider that such coherent precipitate or zone will be formed in the non age-hardenable Fe-Ni or Fe-Mn martensitic alloys.
(4) The formation of such precipitate or zone will be possible when the miscibility gap island can be assumed in the martensitic matrix of Fe-Ni-Mn alloys.
Readers Who Read This Article Also Read
Tetsu-to-Hagané Vol.50(1964), No.5
Tetsu-to-Hagané Vol.53(1967), No.11
Tetsu-to-Hagané Vol.54(1968), No.11
Determination of Zinc in Steelmaking Dust
Shigeo WAKAMATSU
pp. 787-795
Abstract
A simple chelatometric titration method for the determination of zinc in steel making dust has been developed.
Zinc form negatively charged chloride complex which is adsorbed by the strongly basic anion exchange resin. Maximum adsorption of zinc is obtained in 2N HCl. In this medium most elements with which zinc are associated in dust are not adsorbed by the resin. It is therefore possible to separate zinc from iron, aluminium, manganese, calcium, magnesium, chromium and nickel.
Zinic is then eluted from the resin with 0.3N HNO3, and titrated with EDTA using EBT as the indicator. Part of iron, copper, tin, lead and arsenic are adsorbed on the resin, but a subsequent EDTA titration procedure is described which obviates their interference.
The proposed has the advantage of speed, yet has the same accuracy as the gravimetric method.
Construction and Operation of Fukuyama Iron Works, Nippon Kokan K. K
Hiroshi NAKANO
pp. 796-816
Abstract
Construction of a giant iron works was planned by Nippon Kokan with a crude steel production of ten million tons as the final target, to cope with increasing competition in domestic and foreign marketsfor the future development of the steel industry of Japan. Another reason of this decision was the fact that the crude steel production at the three iron works in Tokyo-Yokohama area was limited to five million tons because of the local restrictions.
Company policy for this construction was directed toward the adoption of largest and most highly automated facilities and a layout permitting the most rational transportation. An area of 7.26million m2 was selected from among many possible sites of construction within Japan at the coast of Fukuyama in compliance with this policy. Reclamation was launched in January 1962. The first period construction was completed in summer 1966 with the production of sheets as objective. The crude steel production has reached in June 1967 a level of two million tons. The second period construction isalready underway, and a production system comprising hot and cold rolled sheets and wide plates corresponding to a crude steel production of four million tons will be established at the beginning of 1968.
Readers Who Read This Article Also Read
Tetsu-to-Hagané Vol.50(1964), No.3
Tetsu-to-Hagané Vol.63(1977), No.1
Tetsu-to-Hagané Vol.69(1983), No.15
An Investigation of the Sintering Machine to be Enlarged and Modernized
Kumao UESHIMA
pp. 817-836
Application of Special Instrumental Analysis to the Analysis of Iron and Steel
Hidehiro GOTO, Kichinosuke HIROKAWA
pp. 837-844
Readers Who Read This Article Also Read
ISIJ International Vol.58(2018), No.2
Tetsu-to-Hagané Vol.54(1968), No.7
ISIJ International Vol.58(2018), No.1
Article Access Ranking
29 Aug. (Last 30 Days)
-
Perspectives on the Promising Pathways to Zero Carbon Emissions in the Steel Industry toward 2050
ISIJ International Vol.65(2025), No.2
-
Growth, Removal, and Agglomeration of Various Type of Oxide Inclusions in Molten Steel
Tetsu-to-Hagané Vol.111(2025), No.11
-
Copper removal of liquid steel containing 0.25 % carbon using Fe2O3-CaCl2-SiO2 flux
ISIJ International Advance Publication
-
Finite Element Analysis of Bubble Growth and Particle Swelling during Coal Pyrolysis
ISIJ International Vol.65(2025), No.9
-
Corrosion Behavior of Carbon Steel under Soil Drying Conditions
ISIJ International Advance Publication
-
Cold Spot Joining of 980 MPa-class Ultra-high Strength Steel
Tetsu-to-Hagané Advance Publication
-
Factors Affecting Generation of Iron Fines in Cold Sheet Rolling of Steel
ISIJ International Vol.65(2025), No.9
-
Experimental Study on Heat Transfer Characteristics of a Moving Single-Nozzle Jet Impingement
ISIJ International Vol.65(2025), No.9
-
Combination Effect of Premixing Conditions and Iron Ore Size Distribution in Sintered Ore Granulation Process with Intensive Mixer
ISIJ International Advance Publication
-
Evaluation of Feature Selection Methods for Oxygen Supply Prediction in BOF Steelmaking
ISIJ International Advance Publication
You can use this feature after you logged into the site.
Please click the button below.