- TOP
- Tetsu-to-Hagané
- Vol. 63 (1977), No. 3
Tetsu-to-Hagané Vol. 63 (1977), No. 3
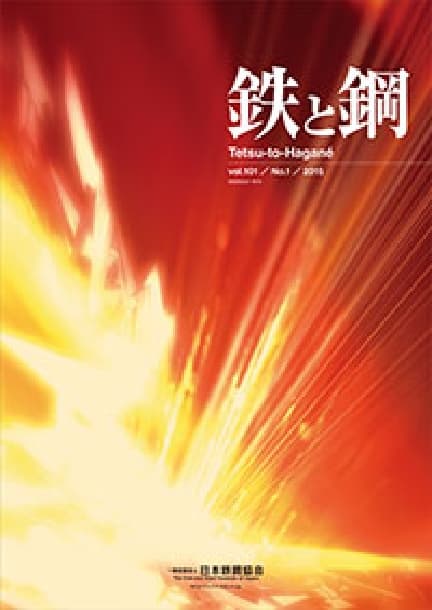
Grid List Abstracts
ONLINE ISSN: | 1883-2954 |
PRINT ISSN: | 0021-1575 |
Publisher: | The Iron and Steel Institute of Japan |
Backnumber
-
Vol. 111 (2025)
-
Vol. 110 (2024)
-
Vol. 109 (2023)
-
Vol. 108 (2022)
-
Vol. 107 (2021)
-
Vol. 106 (2020)
-
Vol. 105 (2019)
-
Vol. 104 (2018)
-
Vol. 103 (2017)
-
Vol. 102 (2016)
-
Vol. 101 (2015)
-
Vol. 100 (2014)
-
Vol. 99 (2013)
-
Vol. 98 (2012)
-
Vol. 97 (2011)
-
Vol. 96 (2010)
-
Vol. 95 (2009)
-
Vol. 94 (2008)
-
Vol. 93 (2007)
-
Vol. 92 (2006)
-
Vol. 91 (2005)
-
Vol. 90 (2004)
-
Vol. 89 (2003)
-
Vol. 88 (2002)
-
Vol. 87 (2001)
-
Vol. 86 (2000)
-
Vol. 85 (1999)
-
Vol. 84 (1998)
-
Vol. 83 (1997)
-
Vol. 82 (1996)
-
Vol. 81 (1995)
-
Vol. 80 (1994)
-
Vol. 79 (1993)
-
Vol. 78 (1992)
-
Vol. 77 (1991)
-
Vol. 76 (1990)
-
Vol. 75 (1989)
-
Vol. 74 (1988)
-
Vol. 73 (1987)
-
Vol. 72 (1986)
-
Vol. 71 (1985)
-
Vol. 70 (1984)
-
Vol. 69 (1983)
-
Vol. 68 (1982)
-
Vol. 67 (1981)
-
Vol. 66 (1980)
-
Vol. 65 (1979)
-
Vol. 64 (1978)
-
Vol. 63 (1977)
-
Vol. 62 (1976)
-
Vol. 61 (1975)
-
Vol. 60 (1974)
-
Vol. 59 (1973)
-
Vol. 58 (1972)
-
Vol. 57 (1971)
-
Vol. 56 (1970)
-
Vol. 55 (1969)
-
Vol. 54 (1968)
-
Vol. 53 (1967)
-
Vol. 52 (1966)
-
Vol. 51 (1965)
-
Vol. 50 (1964)
-
Vol. 49 (1963)
-
Vol. 48 (1962)
-
Vol. 47 (1961)
-
Vol. 46 (1960)
-
Vol. 45 (1959)
-
Vol. 44 (1958)
-
Vol. 43 (1957)
-
Vol. 42 (1956)
-
Vol. 41 (1955)
Keyword Ranking
06 Sep. (Last 30 Days)
Tetsu-to-Hagané Vol. 63 (1977), No. 3
Rate of Dephosphorization of Liquid Iron by CaO-FeO-SiO2 Slag
Yasuji KAWAI, Sadao DOI, Katsumi MORI
pp. 391-399
Abstract
The rate of dephosphorization of liquid iron by slag was investigated by measuring the change of phosphorus content of metal under CaO-FeO-SiO2 slag in a magnesia crucible. Experiments were done with slags of basicity from 0.64 to 1.70 at temperatures from 1540 to 1680°C.
The dephosphorizing reaction proceeded so fast that the equilibrium between metal and slag nearly attained after about 10min.
The experimental results could be interpreted by the rate equation derived from the assumption that the reaction rate was controlled by the transfer of phosphorus in the boundary layer of slag, while the driving force varied during a run.
The effect of slag composition on the reaction rate appeared more clearly in the change of the driving force than in the change of the mass transfer coefficient. Temperature had only a little effect on the reaction rate, because the driving force decreased with temperature while the mass transfer coefficient increased.
Rate of Rephosphorization from CaO-FeO-SiO2-P2O5 Slag into Liquid Iron
Katsumi MORI, Toshiyuki KANEKO, Yasuji KAWAI
pp. 400-408
Abstract
The rate of rephosphorization was investigated by measuring the change of phosphorus content of the metal under CaO-FeO-SiO2-P2O5 slag in a magnesia crucible. Experiments were carried out with slags of basicity from 0.57 to 1.76 in the temperatures range from 1570 to 1650°C.
The results are as follows:
1) The rate of reaction decreased with increase of basicity of slag and with decrease of temperature corresponding to the change of the partition ratio of phosphorus.
2) The reaction rate was increased by the addition of silicon or aluminum into iron.
3) The rate of rephosphorization into liquid iron without any deoxidizer was interpreted by the rate equation derived from the assumption that the reaction was controlled by the diffusion of phosphorus in the boundary layer of liquid iron.
Measurement of Interdiffusion Coefficient in Molten High-Carbon Fe-C Alloy
Yoichi ONO, Masafumi EZAKI
pp. 409-416
Abstract
The interdiffusion coefficient in molten Fe-C alloy has been determined by the capillary-reservoir method in the temperature range from 1350°C to 1550°C under the concentration conditions that the initial carbon content of capillary sample CO was between 1.7 and 3.3% and the carbon content of reservoir melt Cs was the graphite solubility in molten iron.
The results obtained are summarized by the following Arrhenius equation:
Knudsen Cell-Mass Spectrometric Study of the Thermodynamic of the Iron-Aluminum Alloys
Eiji ICHISE, Takashi YAMAUCHI, Toshisada MORI
pp. 417-424
Abstract
Activity coefficients of Al and Fe in Al-Fe alloys were measured in the temperature range from 1400 to 1600°C by the use of knudsen cell mass spectrometer.
Activity curves through the whole composition range were shown for 1400°C.
At higher temperatures, measurements with alloys of high aluminum concentrations and at lower temperatures, measurements with alloys of low aluminum concentrations could not be performed because of experimental difficulties.
It was confirmed that the activity coefficient of Al followed Darken's quadratic formalism in the temperature and composition ranges investigated.
From the temperatuer dependence of the value lim ln (I+AlNFe/I+FeNAl), the temperature dependence of lnγ°Al was determined. By combining the equations of tomperature dependences of lnγ°Al and αFeAl, the following equations were derived for the activity coefficient of Al in Al-Fe alloys. for solid alloys with NAl≤0.33 for liquid alloy with NAl≤0.17.
The temperature dependence of the interaction parameter ε (Al) Al can be given by for solid alloy and for liquid alloy.
From these equations values for γ°Al and ε (Al) Al at 1600°C are calculated as follows:
Temperature dependences of γ°Fe and ε (Fe) Fe are also derived as:
and ε (Fe) Fe=2280/T+6.93
From these equations, values for γ°Fe and ε (Fe) Fe at 1600°C are calculated as follows:
From the temperature dependence of lnγ°Al, the limiting molar heat of mixing of Al in Al-Fealloy at the infinite dilution of Al was calculated to be -17000 cal.
The obtained values were compared with the results of the previous investigatons.
Dendrite Arm Spacing in Iron-Base Binary Alloys
Katsuhiko KISHITAKE, Taira OKAMOTO
pp. 425-431
Abstract
Few systematic studies were made to show the effects of solidification variables and alloying elements on the primary and secondary dendrite-arm spacing in ferrous alloys. This study is aimed to make clear the effects mentioned above in Fe-Ni, Fe-Si and Fe-P binary alloys. The results obtained are summarized as follows:
1) The primary arm spacing, d1 is given by the following equation, where, m is the liquidus slope, C the content of alloying element, k the distribution coefficient, V the cooling rate and a1 a constant.
2) The secondary arm spacing d2 is given by the following equation after the coarsening theory proposed by Kattamis and Flemings, where, θ is the local solidification time and d2-0 is a constant which depends on the diffusion coefficient of the alloying element in both liquid and solid and the solidification temperature.
Measurement of the Standard Free Energy of Formation of Sulfides and Sulfates Using Oxygen Concentration Cells with ZrO2·CaO
Katsuyuki SADAKANE, Masahiro KAWAKAMI, Kazuhiro S. GOTO
pp. 432-440
Abstract
The following cells were constructed with ZrO2·CaO as an electrolyte and pure SO2 gas was supplied to the tesing electrode chamber.
pure SO2, MnO, MnS, Pt/ZrO2·CaO/Pt, Air… (1)
pure SO2, Cu, Cu2S, Pt/ZrO2·CaO/Pt, Air… (2)
pure SO2, NiO, NiSO2, Pt/ZrO2·CaO/Pt, Air… (3)
pure SO2, CoO, CoSO2, Pt/ZrO2·CaO/Pt, Air… (4)
pure SO2, Fe2O2, Fe2 (SO2) 2, Pt/ZrO2·CaO/Pt, Air… (5)
The electromotive forces of those cells in the temperature range from 800 to 1400K were generally very stable and very reproducible except for the cell of equation (3). Reversibility of the electromotive forces was proved sufficiently good by supplying a small external current to the cells.
From the electromotive forces and the standard free energies of formation of the relevant oxides, those of MnS, Cu2S, NiSO4, CoSO4 and Fe2 (SO4) 3 were determined as follows.
The above free energy changes showed good agreements with the previous data by other investigators except for iron sulfate. However, all of the standard deviations of the present data were much smaller than those of the data by other investigators.
Dendrite Morphology and Solute Redistribution during Solidification of 25Cr-20Ni Austenitic Stainless Steel
Takateru UMEDA, Syunya MATSUYAMA, Hirokazu MURAYAMA, Masataka SUGIYAMA
pp. 441-449
Abstract
In the previous paper we discussed the solute distribution during dendritic growth as a function of the area fraction solidified, and suggested that the diffusion layer exists ahead of the solid-liquid interface near growing dendrite tips. In the present work, we investigated the solute distribution and the three dimensional morphology of a growing columnar dendrite in 25-20 austenitic stainless steel.
The results obtained are as follows:
1) The growth process of columnar dendrites can be classified into four stages. The growth of the secondary dendrite plates belongs to the first and the second stage of solidification. In the third and final stages dendrite substructures generally grow in the plane normal to the primary dendrite arm.
2) The area fraction solidified in the transverse section to the primary dendrite arm is nearly equivalent to the volume fraction solidified. The area fraction solidified is sufficient to explain the solute redistribution mechanism during dendritic growth.
3) A diffusion layer exsits ahead of the solid-liquid interface in the intermediate liquid region between two neighboring secondary dendrite plates, as in the case of near the growing primary dendrite tip.
Readers Who Read This Article Also Read
ISIJ International Vol.57(2017), No.5
Planar Anisotropy of r Value of High Strength Cold Rolled Steel Sheets
Kazuo MATSUDO, Koichi OSAWA, Hideo KOBAYASHI
pp. 450-459
Abstract
Planar anisotropy of r value in high strength cold rolled steel sheets produced at mill, of which composition are low C-Si-Mn-Nb-or low C-Si-Mn-Nb-Ti, is r45>r90>r0 type. The reason for the development of this type planar anisotropy in these high strength cold rolled steel sheets has been investigated from the view point of texture and microstructure.
The following results are obtained:
(1) These high strength cold rolled steel sheets have r45>r90>r0 type planar anisortopy even after recrystallization annealing, which is attributed to the remaining {211} <011> and {100} <011> components.
(2) These retained components are not attributed to the partial recrystallization, but mainly to the both effects of strong cold rolled texture due to strong hot rolled texture and recrystallization in situ due to fine precipitates of Nb (C, N) or Ti (C, N).
(3) It is suggested that the hot rolled texture has a strong influence on the recrystallization texture in cold rolled steel sheets containing Nb or Ti.
Surface Textures in Cold Rolled or Recrystallized Silicon Iron Single Crystals
Ei-ichi FURUBAYASHI, Takehiko KIKUCHI
pp. 460-468
Abstract
Cold rolled textures at the surfaces of (011) [100] - and (001) [110] -oriented 3%Si-Fe single crystals which were rolled with various lubricants, e. g. sheets of paper, plastic film, as well as conventional oil were tudied. In the (010) [100] crystals rolled by 60%, preferred surface texture was (011) [100] when no lubrication was used, whereas in the case of using adhesive paper labels pasted on the surface the texture was {111} <211> which coincided exactly with the midplane texture. A slip mechanism was proposed to explain the formation of surface textures at frictional surfaces.
Preferred recrystallization texture originating from the surface of large friction of the (011) [100] crystal was found to have the same orientation as the minor recrystallization texture at the midplane. Surface textures and their control were suggested to be important to control secondary recrystallization texture when cold rolled sheets were annealed.
Low Temperature Ductility of Ultrafine Grain α Iron and Its Substitutional Solid Solutions
Masato ENOMOTO, Ei-ichi FURUBAYASHI
pp. 469-477
Abstract
A study was made of the effect of substitutional solute elements on the ductility of ultrafine grain α iron which was prepared by cold rolling and subsequent annealing to various stages of recovery and recrystallization. The addition of Si or Ti was found to have a remarkable effect in improving the low temperature ductility of the alloy recrystallized into the ultrafine grain structure which in an unalloyed condition showed a very small uniform elongation owing to the plastic instability. Al or Ni addition, however, was not very efficient. Ni was found to suppress the intergranular fracture which was one of the most important causes of low temperature failure of iron having relatively coarse grain structure.
Lüders strain was also measured and it was found that a critical grain size, dc, at which Lüders strain exceeded uniform elongation and a transition from stable to unstable plastic flow occurred was reduced by the addition of substitutional solute elements.
Possible causes for reducing Lüders strain or dc were briefly discussed in terms of slip character and interstitial distribution which were expected to undergo a considerable change by the presence of those substitutional elements.
Tensile Properties and Fracture Toughness of Two-phase 0.2% C-Ni-Cr-Mo Steel
Tetsaya SAITO, Iku UCHIYAMA
pp. 478-487
Abstract
Two-phase steels of ferrite-martensite were used to study the tensile properties and plane strain fracture toughness which was estimated by experimentally determined critical J-value. The ferrite-martensite two-phase structures of a 0.2% C-Ni-Cr-Mo steel were obtained either by heating at intercritical temperatures and quenching or by hot-rolling (rolling reduction of area≈50%) at that temperature range and direct quenching.
Main results obtained are as following.
(1) The 0.2% offset proof stress and tensile strength decrease with an incresae in the volume fraction of the ferrite phase; this shows a deviation from the so-called mixture rule.
(2) The tensile ductility is not improved by mixing of the ferrite phase in the range of small volume fraction.
(3) The fracture toughness remains nearly constant in the range of small volume fraction of ferrite phase. This may be attributed to the fracture at ferrite-martensite interfaces.
(4) The tensile properties and fracture toughness are improved by hot-rolling and direct quenching in comparison with those by heating at intercritical temperatures and quenching. One of the main reasons of the improvement in the fracture toughness seems to be the relaxation of plastic constraint due to the fracture along the mechanical fibers produced by the hot-rolling.
Ductility of 18Cr-12Ni Steel Containing Coarse Irregular Carbide Precipitates along Grain Boundaries in Tensile Test at Room Temperature
Michio YAMAZAKI, Yutaka KOIZUMI
pp. 488-495
Abstract
Creep-rupture strengths of austenitic steels are improved by coarse irregular carbide precipitates along grain boundaries. This structure is obtained by a two-step heat treatment, i. e., steels are solution-treated above the solvus of carbide and then directly cooled to and held at an intermediate temperature below the solvus to make a portion of carbide precipitate preferentially along grain boundaries. The improvement in creep-rupture strengths by this treatment, though it is quite remarkable and attractive, accompanies a reduction in ductility at lower temperatures.
The present study aims to find such conditions of the above two-step treatment as the creep-rupture strength is highly improved but yet the room-temperature tensile ductility does not seriously decrease.
In an 18Cr-12Ni-0.3C steel, a holding time of two to 5h at the second-step temperatures yielded substantial covering of grain boundaries by carbide precipitates which were appropriate in thickness.
This state of precipitation gave a maximum creep-rupture strength and still retained a sufficient ductility at room temperature. Longer holding times, which gave no further improvement in creeprupture, decreased room temperature ductility seriously.
The coarse irregular carbide precipitates were exposed by deep etching, observed in a scanning electron microscope, and were found to be “dendritic”.
Age-Hardening Behaviors and Mechanical Properties of Fe-8%Ni-Ti Maraging Steels
Yoshinao MISHIMA, Tomoo SUZUKI, Minoru TANAKA
pp. 496-504
Abstract
An attempt has been made to survey the effect of the nature of properties, i. e., on the combination of strength and ductility in Fe-8%Ni-1.5%Ti alloys and Fe-8%Ni-1.5%Ti-0.3%Al alloys. It is confirmed that the precipitate contributing to hardening is Ni3Ti phase (DO21) in higher nickel martensitic alloys and that in lower nickel martensitic alloys NiTi phase (B2) tends to precipitate at lower aging temperatures, by the effect of small amounts of aluminum addition on aging kinetics and hardening response, by transmission electron microscopy and by acrude thermodynamic consideration. For Fe-8%Ni-1.5%Ti alloys, fine and coherent precipitation of NiTi phase on the initial stage of hardening at low aging temperature below 525°C is found to be extremely brittle. On the other hand, semicoherent precipitation of Ni3Ti η phase at high aging temperature above 525°C results in a better combination of the strength and ductility.
Readers Who Read This Article Also Read
Tetsu-to-Hagané Vol.60(1974), No.1
Tetsu-to-Hagané Vol.60(1974), No.1
Tetsu-to-Hagané Vol.60(1974), No.3
Precipitation Process in 13Ni-15Co-10Mo (400ksi-Grade) Maraging Steels
Ko SOENO, Mitsuo CHIGASAKI, Masatoshi TUGHIYA
pp. 505-512
Abstract
A resistometric investigation of the precipitation process in 13Ni-15Co-10Mo 400ksi-grade maraging steels has been made in comparing with the precipitation in 18Ni-10Co-5Mo, 14Ni-15Co-5Mo, and 14Ni-15Co-7Mo maraging steels. Two precipitation stages are observed in aging of the 400ksi-grade maraging steels. The precipitation stages in the lower and higher temperature regions are named as stage-PA and stage-PB, respectively. In the precipitation of the 18Ni-10Co-5Mo, 14Ni-15Co-5Mo, and 14Ni-15Co-7Mo maraging steels, two stages are also observed.
In the 18Ni-10Co-5Mo, 14Ni-15Co-5Mo, and 14Ni-15Co-7Mo maraging steels, most of the precipitateds formed in the low temperature percipitation stage are resoluted by heating to temperatures where the high temperature precipitation stage preceeds rapidly. However, the reversion of the precipitates formed in the stage-PA of 400ksi-grade maraging steel is relatively small in heating up to 600°C. Accordingly, it is considered that the upper limit of temperatures where the stage-PA proceeds as the early precipitation stage of the 400ksi-grade maraging steel is located at a relatively high temperature. The strength of the 400ksi-grade maraging steel is reached to its maximum near the end of the stage-PA, and is decreased gradually with the proceeding of the stage-PB.
Interfacial Phenomena in Iron and Steelmaking Processes
Hiroshi SAKAO, Kusuhiro MUKAI
pp. 513-536
抄録
天辰 正義, 雀部 実, 川上 正博, 高橋 謙治, 土田 裕, 盛山 博一, 今津 勝宏, 上正原 和典, 矢崎 勝仁, 田中 徹, 武田 修一, 斧田 一郎, 佐藤 隆樹, 長井 寿, 福森 正仁
pp. 552-559
Article Access Ranking
06 Sep. (Last 30 Days)
-
Perspectives on the Promising Pathways to Zero Carbon Emissions in the Steel Industry toward 2050
ISIJ International Vol.65(2025), No.2
-
Growth, Removal, and Agglomeration of Various Type of Oxide Inclusions in Molten Steel
Tetsu-to-Hagané Vol.111(2025), No.11
-
Finite Element Analysis of Bubble Growth and Particle Swelling during Coal Pyrolysis
ISIJ International Vol.65(2025), No.9
-
Interface behavior leading to Al/Cu dissimilar metal bonding formation with high-speed eutectic reaction induced by applying current
QUARTERLY JOURNAL OF THE JAPAN WELDING SOCIETY Vol.43(2025), No.2
-
Corrosion Behavior of Carbon Steel under Soil Drying Conditions
ISIJ International Advance Publication
-
Cold Spot Joining of 980 MPa-class Ultra-high Strength Steel
Tetsu-to-Hagané Advance Publication
-
Combination Effect of Premixing Conditions and Iron Ore Size Distribution in Sintered Ore Granulation Process with Intensive Mixer
ISIJ International Advance Publication
-
A preliminary study on reduction degradation of iron ore sinter using sinter analogue and X-ray micro-computed tomography (MCT)
ISIJ International Advance Publication
-
Copper removal of liquid steel containing 0.25 % carbon using Fe2O3-CaCl2-SiO2 flux
ISIJ International Advance Publication
-
Evaluation of Feature Selection Methods for Oxygen Supply Prediction in BOF Steelmaking
ISIJ International Advance Publication
You can use this feature after you logged into the site.
Please click the button below.