- TOP
- Tetsu-to-Hagané
- Vol. 67 (1981), No. 3
Tetsu-to-Hagané Vol. 67 (1981), No. 3
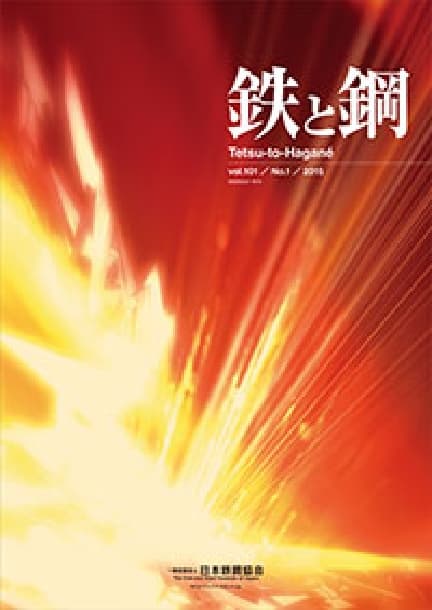
Grid List Abstracts
ONLINE ISSN: | 1883-2954 |
PRINT ISSN: | 0021-1575 |
Publisher: | The Iron and Steel Institute of Japan |
Backnumber
-
Vol. 111 (2025)
-
Vol. 110 (2024)
-
Vol. 109 (2023)
-
Vol. 108 (2022)
-
Vol. 107 (2021)
-
Vol. 106 (2020)
-
Vol. 105 (2019)
-
Vol. 104 (2018)
-
Vol. 103 (2017)
-
Vol. 102 (2016)
-
Vol. 101 (2015)
-
Vol. 100 (2014)
-
Vol. 99 (2013)
-
Vol. 98 (2012)
-
Vol. 97 (2011)
-
Vol. 96 (2010)
-
Vol. 95 (2009)
-
Vol. 94 (2008)
-
Vol. 93 (2007)
-
Vol. 92 (2006)
-
Vol. 91 (2005)
-
Vol. 90 (2004)
-
Vol. 89 (2003)
-
Vol. 88 (2002)
-
Vol. 87 (2001)
-
Vol. 86 (2000)
-
Vol. 85 (1999)
-
Vol. 84 (1998)
-
Vol. 83 (1997)
-
Vol. 82 (1996)
-
Vol. 81 (1995)
-
Vol. 80 (1994)
-
Vol. 79 (1993)
-
Vol. 78 (1992)
-
Vol. 77 (1991)
-
Vol. 76 (1990)
-
Vol. 75 (1989)
-
Vol. 74 (1988)
-
Vol. 73 (1987)
-
Vol. 72 (1986)
-
Vol. 71 (1985)
-
Vol. 70 (1984)
-
Vol. 69 (1983)
-
Vol. 68 (1982)
-
Vol. 67 (1981)
-
Vol. 66 (1980)
-
Vol. 65 (1979)
-
Vol. 64 (1978)
-
Vol. 63 (1977)
-
Vol. 62 (1976)
-
Vol. 61 (1975)
-
Vol. 60 (1974)
-
Vol. 59 (1973)
-
Vol. 58 (1972)
-
Vol. 57 (1971)
-
Vol. 56 (1970)
-
Vol. 55 (1969)
-
Vol. 54 (1968)
-
Vol. 53 (1967)
-
Vol. 52 (1966)
-
Vol. 51 (1965)
-
Vol. 50 (1964)
-
Vol. 49 (1963)
-
Vol. 48 (1962)
-
Vol. 47 (1961)
-
Vol. 46 (1960)
-
Vol. 45 (1959)
-
Vol. 44 (1958)
-
Vol. 43 (1957)
-
Vol. 42 (1956)
-
Vol. 41 (1955)
Keyword Ranking
06 Sep. (Last 30 Days)
Tetsu-to-Hagané Vol. 67 (1981), No. 3
Recent Studies on the Property of Blast Furnace Coke and Its Future Prospect
Yoshiaki MIURA
pp. 468-479
Present State of the Smelting Reduction Processes
Masakazu NAKAMURA, Naoki TOKUMITSU
pp. 480-489
High Reduction Rolling of Strip Sheet and Plate
Hiromu SUZUKI
pp. 490-496
Readers Who Read This Article Also Read
Tetsu-to-Hagané Vol.79(1993), No.3
Tetsu-to-Hagané Vol.70(1984), No.9
Tetsu-to-Hagané Vol.60(1974), No.1
Production of Reduced Iron by Model Plant of Shaft Furnace
Kiichi NARITA, Dentaro KANEKO, Yoshio KIMURA, Yoshiinichi TAKENAKA, Hidetoshi TANAKA, Yutaka INADA
pp. 508-517
Abstract
Experimental production of reduced pellets was performed using a small scale shaft furnace having inside diameter of 250 mm and reduction zone height of 2.7 m. The furnace was designed to permit continuous production of reduced pellets at the rate of 1.5 ton/day.
Effects of operational factors such as reduction temperature, gas composition and gas flow rate on the reduction behaviors of iron oxide pellets as well as the properties of products were investigated and following results were obtained.
1) Reduction rate of the pellets in the furnace increases according to the rise of reducing gas temperature and gas ratio.
2) The utilization of reducing gas is in a range from 30 to 43% and it becomes higher as reducing gas temperature increases.
3) The degree of reduction of products decreases rapidly when R value of reducing gas is less than 15.
4) The temperature in the furnace is lowered and progress of reduction is retarded as the ratio of H2 to CO in the reducing gas increases due to the endothermic reaction caused by H2 reduction of iron oxide.
A Mathematical Model of Blast Furnace for Control of Hot Metal Temperature
Michiharu HATANO, Yoshisuke MISAKA, Yoshiyuki MATOBA, Koichi OTSUKA
pp. 518-527
Abstract
For the automatic control of hot metal temperature, a new simplified mathematical model of blast furnace has been developed on the following assumptions:
(1) The working volume in the furnace is divided into five horizontal zones. Only the specified materials and reactions are considered in each zone.
(2) By taking material balance, the flow rates of solid and gas at each zone are determined so that the amount of the material existed in each zone remains constant.
(3) Heat balance is applied to solid and gas in each zone respectively taking account of their average temperature.
(4) The reaction rates are formulated as the functions of operational variables on the basis of their step response characteristics.
The temperature of solid and gas at each zone can be predicted by the adjustment of parameters in the model using actual operational data. Since the predicted solid temperature at the fifth zone (tuyere level) agrees well with the actual hot metal temperature, the validity of the model has been proved.
At Kokura No. 2 BF, the model is being used for the automatic control and contributes to the stable blast furnace operation.
Automatic Control of Hot Metal Temperature of Blast Furnace
Michiharu HATANO, Yoshiyuki MATOBA, Koichi OTSUKA, Michiyasu YOSHIKI, Toshimitsu MIYAGI
pp. 528-535
Abstract
For the automatic control of hot metal temperature, an advanced computer control system was developed on the basis of the new mathematical model of blast furnace described in the other paper.
The characteristic features of the system are as follows:
(1) The parameters of the model are adjusted in advance by the adaptive feedback of actual operational data.
(2) Through the forward simulation of the process by the model, the hot metal temperature is predicted.
(3) The oil injection rate required for the control is derived from the difference between the predicted hot metal temperature and the aimed one. By examining the control characteristics of the system through the simulation, it is confirmed that the system is effective for the stable blast furnace operation.
With this system, the automatic control has been carried out at Kokura No. 2 BF since 1977 and the fluctuations of the hot metal temperature and the silicon content have been decreased. As the result of the control of the thermal condition, the hot metal temperature could be lowered by 15°C, which contributed to the decrease of fuel ratio by 4 kg/t-pig.
Phosphorus Distribution between Slag and Metal at Hot Metal Temperatures
Katsuhiro IWASAKI, Nobuo SANO, Yukio MATSUSHITA
pp. 536-540
Abstract
In order to understand quantitatively the dephosphorization behavior of hot metals, the equilibrium distribution ratio of phosphorus between solid iron strip and molten CaO-SiO2-FeO(-CaF2) slags, violent CO evolution from molten iron being avoided, was measured in the temperature from 1300° to 1380° as a function of slag composition and then was converted for the hot metal system, using available thermodynamic data of phosphorus in solid and liquid irons.
The results are summarized as follows.
(1) Less basic slags than conventional steelmaking ones have sufficiently high dephosphorization capasity in the hot metal system.
(2) Fluorspar significantly promotes dephosphorization.
(3) Healy's equation which is applicable at steelmaking temperatures predicts far better dephospho rization than the present measurements for hot metals. Accordingly the equation is not valid at around 1300°C.
Readers Who Read This Article Also Read
Tetsu-to-Hagané Vol.51(1965), No.6
Tetsu-to-Hagané Vol.58(1972), No.2
Tetsu-to-Hagané Vol.58(1972), No.14
Atomization of Molten Steel by Annular Concentric Nozzles
Shozo SEKINO, Masao YAMAMIYA, Tokuhiko NISHIDA
pp. 541-546
Abstract
An experimental annular concentric nozzle was made to study its features for gas atomization of molten steel and factors governing particle sizes. From experimental results the following conclusions were obtained. The nozzle must be adjusted so as not to focus the gas stream at the steel stream to avoid blowing up of molten steel and it was less effective for atomization than the individual jet nozzles(IJN) used by Lubanska. It showed narrower distribution of mean particle sizes, than IJN.
The following expressin was obtained for the mean particle diameter χm,
χm=2.9D(M/A·1/√W)2/3
D : nozzle diameter
M : molten steel flow rate
A : gas flow rate
W : Weber number
It can express the experimental values fairly well under the present conditions.
Solidification Analysis of Steel Ingots with Consideration of Fluid Flow
Itsuo OHNAKA, Tatsuichi FUKUSAKO, Kiyoaki NISHIKAWA
pp. 547-556
Abstract
A numerical technique of solidification analysis is presented which is based on "Inner Nodal Point Method" and takes account of fluid flow induced by solidification shrinkage and variable fluid density. As examples. solidifications of tapered steel ingots have been analysed. It is shown that (1) a step by step method, where the equations of conservation laws for heat- and fluid-flow are solved alternately, can be employed, (2) the value of permeability in solid-liquid region affects considerably the magnitude of fluid velocity, pressure and rate of solidification, (3) the magnitude of negative pressure and rate of solidification decrease with increasing taper, and (4) the movement of solid phase should be considered in some cases. In addition, the mechanisms of formation of V- and A-segregation are discussed on the flow and pressure field calculated. The proposed technique, which can handle complicated boundary shape, may be more useful for the determination of ingot shape and casting condition than conventional ones.
Development of Heavy Gauge Hot Coils with High Strength and Excellent Low Temperature Toughness by Controlled Rolling
Kazutoshi KUNISHIGE, Masashi TAKAHASHI, Seiichi SUGISAWA, Tadao HAMANAKA
pp. 557-566
Abstract
Steel plate used for line pipe is produced by both plate and hot-strip mills. Controlled rolling is used in both type of mills to obtain a good combination of strength and low temperature toughness. A Iaboratory simulation method for producing coiled-strip and plates is devised, taking account of a great difference in thermal conditions after finish-rolling.
The results in laboratory test reveals that microstructure and precipitation of carbonitride in the simulated hot coils differ from those in the air-cooled plates, and these lead to different controlling practices between hot-strip and plate mills.
For niobium bearing steel, bainitic transformation occurs in hot-coils by rapid cooling on runout table. To avoid the embrittlement caused by a bainitic structure, carbon content should be reduced to the level similar to that of acicular ferrite steel and also the slab-reheating temperature and rough rolling temperature should be lowered.
For vanadium bearing steel, lowering the slab-reheating temperature in the middle position of the length is recommended to prevent the embrittlement caused by vanadium carbonitride precipitation during slow cooling especially in that position after coiling.
The manufacturing trials of 14.3 mm thick heavy gauge coils are carried out, using 0.14%C-Nb-V steel and 0.04%C-1.9%Mn-Nb-Mo-Ca steel. Both steels are found to meet API-X70 strength with excellent low temperature toughness.
Effect of Intercritical Rolling on the Strength and Notch Toughness of Steel Plate
Susumu GOHDA, Kunio WATANABE, Yoshio HASHIMOTO, Yasuo SOGO, Katsuaki MINAMIDA, Okitsugu MANTANI
pp. 567-576
Abstract
The intercritical rolling method has been applied to the manufacture of strong and tough steel plate. The results obtained are as follows:
(1) An excellent combination of strength and notch toughness can be achieved by increasing rolling reduction in the intercritical range. Notch toughness and arrestability of brittle crack propagation are much improved also by the intercritical rolling of Nb bearing steel with fine austenite grains.
(2) The main characteristic of the intercritically rolled plate is the decrease of variation of mechanical properties both within a single plate and throughout simularly rolled plates due to temperature equalization and work hardening mitigated by the recovery of the worked ferrite, which in turn is due to heavy rolling reduction in the intercritical range. A further result is the stability of the manufacturing conditions.
(3) In addition to its well ballanced strength and notch toughness, the intercritically rolled plate with low carbon equivalent excels or matches the plate subjected to heat treatment in fracture properties, various kinds of workability and weldability.
Through the application of intercrtical rolling to various types of mills, the optimal rolling conditions for strength and notch toughness have been found to differ according to the various rolling mill characteristics; whereas the most effective condition for a hot-strip mill is rolling with a few passes within a highertemperature intercrtical range, rolling with higher total reduction with many passes within a lower-temperature range is appropriate for a plate mill.
Readers Who Read This Article Also Read
Tetsu-to-Hagané Vol.67(1981), No.1
Tetsu-to-Hagané Vol.71(1985), No.2
Tetsu-to-Hagané Vol.70(1984), No.7
Precipitation Behavior of σ Phase in a Duplex Phase Stainless Steel
Yasuhiro MAEHARA, Masao KOIKE, Nobukatsu FUJINO, Tatsuro KUNITAKE
pp. 577-586
Abstract
Precipitation of σ phase in an Fe-25Cr-7Ni-3Mo alloy with a duplex structure of α and γ phases, has been studied systematically by means of optical microscopy, X-ray diffraction, hardness measurement, tensile test, SEM observation and dilatometric measurement. The results obtained in this study are as follows:
(1) TTT diagram for the precipitation of σ phase was a C-type with a nose at about 820°C and 2030 min.
(2) σ phase nucleated on the α/γ boundaries and grew into α grains, and thereafter the nucleation of σ and new γ phases began also in α grains. Volume fraction of α phase decreased and that of γ phase increased with increasing σ phase. Precipitation of σ phase occurred by the reaction, α→σ+γ. It was found that Cr, Mo and W were concentrated into α phase.
(3) Increase of hardness with precipitation of α phase was not so large, on the contrary, impact value decreased drastically even at a few percent precipitation of α phase. α phase was also found to be harmful for hot ductility.
(4) The precipitation range during cooling were about 700900°C and a phase precipitation could be avoided if cooling rate were larger than about 20°C/min after solution treatment.
It was clarified from the above results that α embrittlement during production of duplex phase stainless steels could be avoided by selecting adequate manufacturing conditions.
Effects of Alloying Elements and Solution-annealing Temperature on the Mechanical Properties of Austenitic Fe-Mn-C Alloy
Tetsuo KATO, Masakuni FUJIKURA, Shin-ichiro YAHAGI, Kiyohito ISHIDA
pp. 587-595
Abstract
In order to investigate the effects of various alloying elements including S as a free-machining element on the mechanical properties of high manganese non-magnetic steel, tensile and Charpy impact tests were carried out in the annealed condition. The mechanism of the observed large strengthening effect of V especially on the 0.2% proof stress was investigated by examining Petch relation and its solution hardening effect.
A linear regression equation which relates the 0.2% proof stress to the chemical composition is obtained. The strengthening effect of ferrite-forming substitutional element becomes greater in the order of Cr, Mo and V. Especially, the effect of V on the 0.2% proof stress is comparable with that of interstitial element C. While, austenite-forming substitutional elements Ni and Mn have little effect on the strength. The elongation and Charpy impact toughness show decreasing tendencies by the additions of ferrite-forming substitutional elements and S. However, interstitial elements C and N hardly decrease the elongation irrespective of their large strengthening effect. 0.2% proof stress and tensile strength decrease with increasing solution annealing temperature and a Petch relation is found. The large strengthening effect of V cannot be explained by its small solution hardening effect and is rather considered to be mainly attributable to grain refining by the V addition.
Effects of Microstructure and Carbon Content in the Case on the Fatigue Strength Properties of Carburized Steel
Tôru FURUKAWA, Shizuyo KONUMA, Satoru NISHIWAKI
pp. 596-605
Abstract
The rotating bending fatigue and static bending tests were carried out to know the roles of surface non-martensitic structure and sub-zero treatment and the effects of retained austenite and carbon contents in the carburized case on the fatigue strength properties of carburized steel.
The main results obtained are as follows:
(1) For both tests of rotating bending fatigue and static bending, the existence of surface non-martensitic structure decreased the mechanical properties of carburized steel when fracture occured at the specimen surface. On the other hand, the fatigue limit was independent of the existence of the structure if fracture did not occur at the specimen surface.
(2) For the specimen with the carburized case containing carbon of about 0.9% (0.9%C specimen), sub-zero treatment followed by oil-quenching reduced the fatigue limit of about 15 kgf/mm2 by comparison with the case of no sub-zero treatment. Also, the maximum fatigue limit was obtained for the specimen with the carburized case containing austenite of about 20-25%.
(3) The fatigue limit, the value of the fatigue crack initiating stress, the fatigue crack propagating stress, the nominal fatigue crack propagating stress at the tip of the maximum non-propagating crack, and the static bending strength and deflection up to rupture for 0.5%C specimen were higher than those for 0.9%C specimen.
(4) The existence of the non-propagating crack at 107 cycles was observed in the case of the notched specimen with the notch root radius of 0.16 mm.
Ion Microprobe Mass Analysis of Boron in Steel
Toshio SHIRAIWA, Nobukatsu FUJINO, Jun'ichiro MURAYAMA
pp. 606-612
Abstract
Ion microprobe mass analyzer has been applied to analysis of boron in high strength steels. It is proved that the analytical technique has sufficient sensitivity and resolution to determine the distribution of boron in precise correspondence with metallogrophic microstructure. It is also shown that quantitative analysis of bolon in solid solution is possible, and that the effect of nitrogen on the amount of solute boron can be detected.
An Automatic Apparatus for Isolation of Precipitates from Steels
Ken-ichi TAKIMOTO, Isamu TAGUCHI, Ryutaro MATSUMOTO
pp. 613-619
Abstract
An automatic apparatus has been developed for isolation of precipitates and inclusions from steels. The developed apparatus is mainly composed of a sample exchanger, an electrolytic cell, a potentiostat, solution-injectors, ultrasonic vibrations and a program timer.
Steel samples in the twelve electrolytic cells on the turntable are potentiostatically electrolyzed one by one in the non-aqueous electrolyte, 10% acetylacetone-1% tetramethylammonium chloride-methylalcohol, provided by one of the solution-injectors. Electrolysis is performed by the highly precise potentiostat with the built-in coulometer until the predetermined weight of samples is dissolved. The precipitates dispersed in the electrolyte are collected with an organic microfilter and those on the sample surface are subjected to ultrasonic vibration generated by combination of horn-typed vibrator and ring-typed one.
The developed apparatus is automatically operated by the program timer. Time required for twelve samples was about ten hrs. and repeatability of the results was better than those by a manual method. Analytical results of AlN, Cr7C3 and MnS by the proposed automatic apparatus are also discussed.
Preparation of Metallurgical Education in Kaiseigakko and Kobugakko in 18681871
Zenshiro HARA
pp. 620-623
Abstract
[in Japanese]
抄録
月橋 文孝, 小林 一彦, 拝田 治, 戸村 寿孝, 檀 武弘, 糸山 誓司, 望月 俊男, 青木 孝夫, 村上 雅人, 中野 恵司, 赤沢 和夫
pp. 644-648
Article Access Ranking
06 Sep. (Last 30 Days)
-
Perspectives on the Promising Pathways to Zero Carbon Emissions in the Steel Industry toward 2050
ISIJ International Vol.65(2025), No.2
-
Growth, Removal, and Agglomeration of Various Type of Oxide Inclusions in Molten Steel
Tetsu-to-Hagané Vol.111(2025), No.11
-
Finite Element Analysis of Bubble Growth and Particle Swelling during Coal Pyrolysis
ISIJ International Vol.65(2025), No.9
-
Interface behavior leading to Al/Cu dissimilar metal bonding formation with high-speed eutectic reaction induced by applying current
QUARTERLY JOURNAL OF THE JAPAN WELDING SOCIETY Vol.43(2025), No.2
-
Corrosion Behavior of Carbon Steel under Soil Drying Conditions
ISIJ International Advance Publication
-
Cold Spot Joining of 980 MPa-class Ultra-high Strength Steel
Tetsu-to-Hagané Advance Publication
-
Combination Effect of Premixing Conditions and Iron Ore Size Distribution in Sintered Ore Granulation Process with Intensive Mixer
ISIJ International Advance Publication
-
A preliminary study on reduction degradation of iron ore sinter using sinter analogue and X-ray micro-computed tomography (MCT)
ISIJ International Advance Publication
-
Copper removal of liquid steel containing 0.25 % carbon using Fe2O3-CaCl2-SiO2 flux
ISIJ International Advance Publication
-
Evaluation of Feature Selection Methods for Oxygen Supply Prediction in BOF Steelmaking
ISIJ International Advance Publication
You can use this feature after you logged into the site.
Please click the button below.