- TOP
- Tetsu-to-Hagané
- Vol. 57 (1971), No. 10
Tetsu-to-Hagané Vol. 57 (1971), No. 10
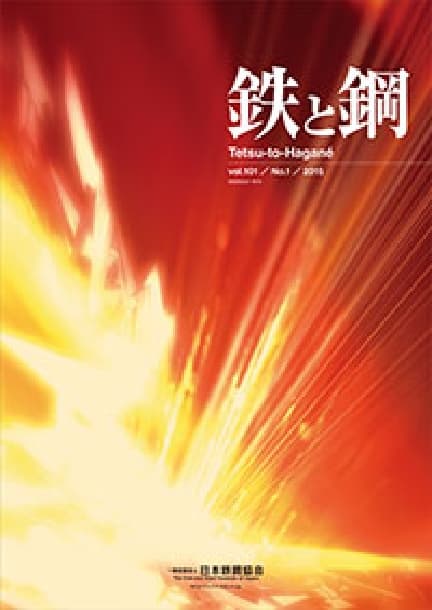
Grid List Abstracts
ONLINE ISSN: | 1883-2954 |
PRINT ISSN: | 0021-1575 |
Publisher: | The Iron and Steel Institute of Japan |
Backnumber
-
Vol. 111 (2025)
-
Vol. 110 (2024)
-
Vol. 109 (2023)
-
Vol. 108 (2022)
-
Vol. 107 (2021)
-
Vol. 106 (2020)
-
Vol. 105 (2019)
-
Vol. 104 (2018)
-
Vol. 103 (2017)
-
Vol. 102 (2016)
-
Vol. 101 (2015)
-
Vol. 100 (2014)
-
Vol. 99 (2013)
-
Vol. 98 (2012)
-
Vol. 97 (2011)
-
Vol. 96 (2010)
-
Vol. 95 (2009)
-
Vol. 94 (2008)
-
Vol. 93 (2007)
-
Vol. 92 (2006)
-
Vol. 91 (2005)
-
Vol. 90 (2004)
-
Vol. 89 (2003)
-
Vol. 88 (2002)
-
Vol. 87 (2001)
-
Vol. 86 (2000)
-
Vol. 85 (1999)
-
Vol. 84 (1998)
-
Vol. 83 (1997)
-
Vol. 82 (1996)
-
Vol. 81 (1995)
-
Vol. 80 (1994)
-
Vol. 79 (1993)
-
Vol. 78 (1992)
-
Vol. 77 (1991)
-
Vol. 76 (1990)
-
Vol. 75 (1989)
-
Vol. 74 (1988)
-
Vol. 73 (1987)
-
Vol. 72 (1986)
-
Vol. 71 (1985)
-
Vol. 70 (1984)
-
Vol. 69 (1983)
-
Vol. 68 (1982)
-
Vol. 67 (1981)
-
Vol. 66 (1980)
-
Vol. 65 (1979)
-
Vol. 64 (1978)
-
Vol. 63 (1977)
-
Vol. 62 (1976)
-
Vol. 61 (1975)
-
Vol. 60 (1974)
-
Vol. 59 (1973)
-
Vol. 58 (1972)
-
Vol. 57 (1971)
-
Vol. 56 (1970)
-
Vol. 55 (1969)
-
Vol. 54 (1968)
-
Vol. 53 (1967)
-
Vol. 52 (1966)
-
Vol. 51 (1965)
-
Vol. 50 (1964)
-
Vol. 49 (1963)
-
Vol. 48 (1962)
-
Vol. 47 (1961)
-
Vol. 46 (1960)
-
Vol. 45 (1959)
-
Vol. 44 (1958)
-
Vol. 43 (1957)
-
Vol. 42 (1956)
-
Vol. 41 (1955)
Keyword Ranking
07 Sep. (Last 30 Days)
Tetsu-to-Hagané Vol. 57 (1971), No. 10
Rate of Reduction of Iron Oxide Pellets with Hydrogen
Reijiro TAKAHASHI, Jun-ichiro YAGI, Yasuo OMORI
pp. 1597-1605
Abstract
In order to analyse the reduction process in the metallurgical reactor, a reduction rate of single iron oxide pellet was expressed by a mathematical model and the rate parameters were determined.
Unreacted core model was employed to the reduction of the iron oxide pellet with hydrogen in the temperature range of 1100°-1400°K.
The activation energy of the pellet used was about 26kcal/mol. The calculated reduction curves based on this model almost coincided with the observed data under various operating conditions; those are reduction temperatures, diameters of the pellet, and compositions of the reducing gas. Furthermore, in the case where one of the experimental conditions was altered during the reduction, the calculated reduction curves were nearly consistent with the observed data.
It was found from these results that the reduction model in this paper could apply to process analysis of metallurgical reactor.
Readers Who Read This Article Also Read
Tetsu-to-Hagané Vol.57(1971), No.1
Tetsu-to-Hagané Vol.79(1993), No.2
Tetsu-to-Hagané Vol.59(1973), No.13
Some Properties and Degrading Patterns of Materials in a Blast Furnace Shaft
Yoshiteru JOMOTO, Yuji KANAYAMA, Yoshio OKUNO, Masashi ISOYAMA
pp. 1606-1626
Abstract
An investigation was made on properties of materials (sinter, are and pellet) taken from various levels and positions on the radii of the shaft in four blast furnaces of Muroran Works. Degrading properties of these materials were discussed by the comparison of the results obtained from the blast furnace with these from an experimental apparatus designed for analogy in the conditions of shaftregion.
Remarkable informations were conducted as follows.
1) Excessive size degradation of sinter and are was found at upper level of the shaft. At lower level, these mean size fell by 2-6mm.
2) Degree of reduction of sinter, are and pellet was found to be about equal throughout the shaft.
3) Degradation of sinter was characterized by the pattern of bulk degrading mechanism, in view of the facts that many cracks were formed all over the inner grain and the sinter was broken to small pieces.
4) Degradation of both are and pellet was characterized by the pattern of surface degrading mechanisni, in view of the facts that many cracks were formed on their surfaces and fine are and pellet were produced.
5) The degree of degradation of the materials observed in the experimental apparatus coincided with that observed in the shaft region. It was assured that the result of the experimental apparatus was able to be used for evaluation of the nature of degradation.
Readers Who Read This Article Also Read
Tetsu-to-Hagané Vol.57(1971), No.1
Tetsu-to-Hagané Vol.79(1993), No.2
Tetsu-to-Hagané Vol.59(1973), No.13
An Influence of High Top-Pressure Operation on Pressure Drop in a Blast Furnace
Tsuyoshi FUKUTAKE, Kyoji OKABE
pp. 1627-1635
Abstract
On the basis of laboratory experiments, a series of formulas is derived to estimate a gas flow resistance of the blast furnace burdens. By applying these formulas, the total pressure drop of the blast furnace can be divided into two parts, i. e., for the upper zone where the melts do not exist and for the lower zone where the solids and the melts coexist.
The calculated results of the pressure drops of the upper and the lower zones of No1 blast furnace at Mizushima Works of Kawasaki Steel Corporation showed the following observations;
(1) When the blowing rate increases with increasing the top pressure, the pressure drop of the upper zone decreases and the pressure drop of the lower zone increases.
(2) With increasing the top pressure, loading or flooding at the lower zone plays an important role for hanging.
(3) With increasing the pressure drop of the lower zone, the scattering range of sulpher content in pig iron within a day increases.
Absorption Rate of Oxygen Jetted into Molten Metal
Mitsugu MATSUSHIMA, Kazumi MORI
pp. 1636-1644
Abstract
A study was made on the absorption of oxygen jetted into molten silver to clarify the mechanism of interact ion between a gas jet and molten metal. At 1050°C preheated oxygen gas was blown on to molten silver of 230g through an alumina nozzle of 1mm in diameter. The oxygen content in themelt was measured continuously by the solid electrolyte galvanic cell. The oxygen flow rate was 1-12Nl/min and the height of the nozzle from the melt surface was -10-+20mm. The critical condition required to produce a homogeneous bulk liquid concentration was expressed in terms of the depth of the cavity. At low jet momentums a stable cavity was produced. As the jet momentum increased, the cavity became deeper, and bubbles and liquid droplets were formed, resulting in an abrupt increase of the absorption rate. The rate was described by the ordinary equation of mass transfer except for the range of low oxygen concentration of the melt. The apparent rate constant at high jet momentums was correlated to the jetting conditions, by introducing a factor characterizing jet steepness.
A Model Analysis of the Temperature Variation of Molten Steel in Continuous Casting Tundish
Tetsuya FUJII, Yasuhiro HABU, Hiroshi OOI
pp. 1645-1653
Abstract
In order to obtain the temperature variation of molten steel in tundish during the teeming of continuous casting, a mathematical model which consists of heat balance of molten steel in tundish has been developed. The results calculated from this model were compared with the data of operation of the bloom caster at the Mizushima Iron Works, and it was proved that this model was useful for predicting the temperature variation of molten steel in tundish.
Applying this model, the effects of the operating conditions and of a size of tundish were considered, and the following results were obtained.
(1) Concerning the preheating conditions of refractory for preventing the temperature drop of molten steel, preheating temperature is more important than preheating time. A rise of 200°C in preheating temperature decreases the temperature drop of molten steel in tundish by 10 to 15°C in usual operation.
(2) A slag layer of 15mm thick is adequate as an insulator for heat loss from molten steel to atmosphere.
(3) Molten steel of 600mm depth in tundish is necessary to the stabilization of teeming temperature.(4) To prevent the temperature drop of molten steel, the ratio of width to depth of tundish is desirable to be nuity.
(5) The rate of temperature drop in the pouring stream from ladle to tundish is desirable to be 0.3-0.5°C/min for the stabilization of temperature throughout the teeming period.
Readers Who Read This Article Also Read
Tetsu-to-Hagané Vol.57(1971), No.1
Tetsu-to-Hagané Vol.79(1993), No.2
Tetsu-to-Hagané Vol.59(1973), No.13
Consideration on the Formation Mechanisms of Macroscopic Segregation in Large Steel Ingot or Casting
Koichi TASHIRO, Toru TODOROKI, Shigeo KIMURA
pp. 1654-1675
Abstract
The cause for macroscopic segregation in large steel ingot and casting is reviewed. The formation mechanisms of macroscopic segregations, which have not yet been solved, are as follows.
1. A-segregation and speckle-segregation.
2. V-segregation (positive V-segregation and negative V-segregation).
3. Pock mark segregation and negative V-shape segregation accompanied with electric arc heating in feeder head or upper part of ingot or casting.
4. Negative segregation in lower part of ingot or casting.
In order to solve the cause for above-mentioned macroscopic segregations, the authors investigated. metallographically the macro-segregations of large ingots or castings sectioned longitudinally or transversely, and furthermore carried out model experiments with water-oil, etc. to elucidate the floatation mode of lighter segregated metal in bulk liquid metal.
Based on the results obtained and microscopic feature of dendrite structure, the authors made clear that the macroscopic segregation of steel was induced by difference of specific gravity between segregated liquid metal in the dendritic region and bulk liquid metal and also by interfacial tension between them.
Readers Who Read This Article Also Read
Tetsu-to-Hagané Vol.59(1973), No.12
Tetsu-to-Hagané Vol.60(1974), No.5
Tetsu-to-Hagané Vol.59(1973), No.12
The Effect of High Pressure on the Isothermal Transformation in High Purity Fe-C Alloys and Commercial Steels
Mitsutane FUJITA, Masatoshi SUZUKI
pp. 1676-1689
Abstract
The effects of high pressure on the isothermal transformation are studied for three high purity Fe-C alloys and commercial steels. The specimens (3mm∅×3mm) are inserted into a “girdle” type high pressure apparatus and the isothermal transformation are carried out at 29 or 38.5kbar.
The results obtained were as follows:
(1) The rates of isothermal transformation both in Fe-C alloys and commercial steels are retarded by pressure, and the retardation is much stronger in the latter.
(2) By increasing the pressure from 29 to 38.5kbar in all alloys and steels, the incubation time increases by approximately five times.
(3) The structures obtained in isothermal transformation at high temperature can be explained from the phase equilibrium diagram under high pressure which is different from that at atmospheric pressure.
(4) As singular structures appeared in the transformation at low temperature and high pressure, ‘aggregate’ or “columnar bainite” structures are observed in place of the acicular bainite at atmospheric pressure. The ranges in which those structures appear are determined.
(5) The shape of carbide in a commercial steel containing 1.1%C changes from spherical shape to acicular one with the increase of pressure from 29 to 38.5kbar.
Readers Who Read This Article Also Read
Tetsu-to-Hagané Vol.66(1980), No.6
The Bainite in Low Carbon Low Alloy High Strength Steels
Yasuya OHMORI, Hiroo OHTANI, Tatsuro KUNITAKE
pp. 1690-1705
Abstract
The morphology of the bainite in some low carbon, low alloy high strength steels has been investigated by means of dilatometry and both optical and electron microscopies. The results indicate that the bainite can be divided into three distinct types by the morphology of the cementite precipitation.
The bainite I is formed above 500°C and is the carbide-free bainitic ferrite. The bainite II is formed in the intermediate temperature range or by cooling at intermediate cooling rate. Although some amount of cementite particles are formed within the grains, the bainite II consists mainly of ferrite laths with cementite layers between them, being a typical of upper bainite. The bainite III is formed at temperatures close to the Ms or during cooling as fast as the upper critical cooling rate, the morphology of cementite formation is similar in appearance to the high carbon lower bainite. However, these bainites have the lath-like ferrite morphology with the same ‹111›α{110}α habit. This is different from the high carbon lower bainite with plate-like ferrite. Therefore, it seems reasonable to classify the bainites observed in low carbon low alloy high strength steels as the upper bainite.
Readers Who Read This Article Also Read
Tetsu-to-Hagané Vol.57(1971), No.1
Tetsu-to-Hagané Vol.79(1993), No.2
Tetsu-to-Hagané Vol.59(1973), No.13
Study on the Production of Iron Whiskers
Akimitsu OKURA, Kyojiro KANEKO
pp. 1706-1713
Abstract
The growth of whiskers by reduction of iron oxide-iron halide mixture has been widely investigated so far, and the mechanism of growth of whiskers has been reported.
The growth condition of iron whisker by the hydrogen gas reduction of iron halide is being clarified (at the author's laboratory) with a view to the industrial use of iron whiskers.
The effect of added materials and the kind of boats used for the growth of whiskers have been especially investigated.
The results are as follows.
1) The addition of hematite ore was better than magnetite ore.
2) The addition of 15% Fe2O3 by volume gave good results.
3) It was clear that the growth of iron whiskers was not due to the presence of Fe2O3 but to that of Fe from the experiments using iron boats and alumina boats respectively.
4) Impurities from the reduction boat and from the added materials entered into the iron whiskers produced.
5) Long (8cm at the most) iron whiskers could be produced by controlling the reduction gas volume and vapour pressure of FeCl2 in the reaction vessel.
The Plastic Deformation of Iron Whiskers in the Temperature Range 20-230°C
Kyojiro KANEKO, Akimitsu OKURA
pp. 1714-1720
Abstract
Iron whiskers were examined by tensile test in the temperature range from 20°C to 230°C, and the stress-strain curves were obtained. In those curves serrations appeared, this being affected by the diameter of whiskers and test temperature. Microscopic observations of deformed whiskers showed that the serrations corresponded to the slip steps. The upper and lower yield stresses were also obtained with regard to the diameter and the temperature. The upper yield stress showed a linear relation to the logarithm of the reciprocal of the absolute temperature, and the lower yield stress presented a strong temperature dependence in the temperature range 20-75°C and a weak one in the range 120-230°C. From those results it was concluded that the serrations might be due to the formation of the simplified slip bands.
Computer Control of Hot Strip Mills
Toyohiko OKAMOTO
pp. 1721-1730
Readers Who Read This Article Also Read
Tetsu-to-Hagané Vol.57(1971), No.1
Tetsu-to-Hagané Vol.79(1993), No.2
Tetsu-to-Hagané Vol.59(1973), No.13
Influence of Applied Stress on Stress Corrosion Cracking of Stainless Steel in Sulfuric Acid Solutions
Mitsuo ASAWA
pp. 1731-1732
Article Access Ranking
07 Sep. (Last 30 Days)
-
Perspectives on the Promising Pathways to Zero Carbon Emissions in the Steel Industry toward 2050
ISIJ International Vol.65(2025), No.2
-
Growth, Removal, and Agglomeration of Various Type of Oxide Inclusions in Molten Steel
Tetsu-to-Hagané Vol.111(2025), No.11
-
Finite Element Analysis of Bubble Growth and Particle Swelling during Coal Pyrolysis
ISIJ International Vol.65(2025), No.9
-
Interface behavior leading to Al/Cu dissimilar metal bonding formation with high-speed eutectic reaction induced by applying current
QUARTERLY JOURNAL OF THE JAPAN WELDING SOCIETY Vol.43(2025), No.2
-
Copper removal of liquid steel containing 0.25 % carbon using Fe2O3-CaCl2-SiO2 flux
ISIJ International Advance Publication
-
Corrosion Behavior of Carbon Steel under Soil Drying Conditions
ISIJ International Advance Publication
-
Cold Spot Joining of 980 MPa-class Ultra-high Strength Steel
Tetsu-to-Hagané Advance Publication
-
Combination Effect of Premixing Conditions and Iron Ore Size Distribution in Sintered Ore Granulation Process with Intensive Mixer
ISIJ International Advance Publication
-
A preliminary study on reduction degradation of iron ore sinter using sinter analogue and X-ray micro-computed tomography (MCT)
ISIJ International Advance Publication
-
Viscosity Measurement of Foam with High Gas Volume Fraction Using Sphere Pull-up and Dam-break Experiments
ISIJ International Advance Publication
You can use this feature after you logged into the site.
Please click the button below.