鉄と鋼 Vol. 65 (1979), No. 5
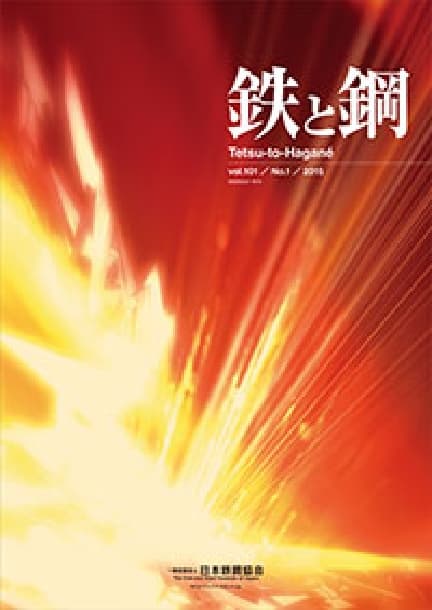
Grid List Abstracts
オンライン版ISSN: | 1883-2954 |
冊子版ISSN: | 0021-1575 |
発行機関: | The Iron and Steel Institute of Japan |
Backnumber
-
Vol. 111 (2025)
-
Vol. 110 (2024)
-
Vol. 109 (2023)
-
Vol. 108 (2022)
-
Vol. 107 (2021)
-
Vol. 106 (2020)
-
Vol. 105 (2019)
-
Vol. 104 (2018)
-
Vol. 103 (2017)
-
Vol. 102 (2016)
-
Vol. 101 (2015)
-
Vol. 100 (2014)
-
Vol. 99 (2013)
-
Vol. 98 (2012)
-
Vol. 97 (2011)
-
Vol. 96 (2010)
-
Vol. 95 (2009)
-
Vol. 94 (2008)
-
Vol. 93 (2007)
-
Vol. 92 (2006)
-
Vol. 91 (2005)
-
Vol. 90 (2004)
-
Vol. 89 (2003)
-
Vol. 88 (2002)
-
Vol. 87 (2001)
-
Vol. 86 (2000)
-
Vol. 85 (1999)
-
Vol. 84 (1998)
-
Vol. 83 (1997)
-
Vol. 82 (1996)
-
Vol. 81 (1995)
-
Vol. 80 (1994)
-
Vol. 79 (1993)
-
Vol. 78 (1992)
-
Vol. 77 (1991)
-
Vol. 76 (1990)
-
Vol. 75 (1989)
-
Vol. 74 (1988)
-
Vol. 73 (1987)
-
Vol. 72 (1986)
-
Vol. 71 (1985)
-
Vol. 70 (1984)
-
Vol. 69 (1983)
-
Vol. 68 (1982)
-
Vol. 67 (1981)
-
Vol. 66 (1980)
-
Vol. 65 (1979)
-
Vol. 64 (1978)
-
Vol. 63 (1977)
-
Vol. 62 (1976)
-
Vol. 61 (1975)
-
Vol. 60 (1974)
-
Vol. 59 (1973)
-
Vol. 58 (1972)
-
Vol. 57 (1971)
-
Vol. 56 (1970)
-
Vol. 55 (1969)
-
Vol. 54 (1968)
-
Vol. 53 (1967)
-
Vol. 52 (1966)
-
Vol. 51 (1965)
-
Vol. 50 (1964)
-
Vol. 49 (1963)
-
Vol. 48 (1962)
-
Vol. 47 (1961)
-
Vol. 46 (1960)
-
Vol. 45 (1959)
-
Vol. 44 (1958)
-
Vol. 43 (1957)
-
Vol. 42 (1956)
-
Vol. 41 (1955)
キーワードランキング
06 Sep. (Last 30 Days)
鉄と鋼 Vol. 65 (1979), No. 5
Degradation of Coke due to Alkali Adsorption
Tongshik CHANG, Mitsuru TATE
pp. 479-487
抄録
A fundamental study on the degradation by alkali adsorption of two cokes made from ordinary (A) and specially inferior (B) coal blends, which had been used in the 26th run of the experimental blast furnace, was carried out.
Following results were obtained:
1) The rate of alkali adsorption at the temperature ranging from 800 to 1000°C in N2 atmosphere depends on the initial porosity of coke.
2) Alkali is adsorbed by either coke and its rate near 1% of enough to generate macro-cracks. The degree of macro-crack formation increases with the increase of alkali adsorption, and it is higher in the less porous coke (A) than in the more porous one (B) under the same rate of alkali adsorption.
3) The presence of CO2 in the atmosphere diminishes macro-cracks due to alkali adsorption, and the crack formation is completely prevented at some PCO2 higher than 0.05-0.06atm.
4) Micro-strengths of every macro-cracked cokes and of coke fines generated by alkali adsorption decrease extremely.
Alkali adsorption is considered to be a cause of degradation common to all kinds of coke, but it is difficult to regard it as the cause of remarkable degradation of coke (B) in the 26th run.
Degradation of Coke due to Gasification
Tonshik CHANG, Mitsuru TATE
pp. 488-494
抄録
Experiments on the degradation of cokes due to gasification with CO2 under the presence of ore and alkali were carried out.
Following results were obtained:
1) The degree of gasification increases with the increase of blending ratio of ore, and this brings about the corresponding decrease of strength.
2) The presence of alkali increases the chemical reaction rate by its catalytic action, and results in the localization of reaction sphere to the surface zone of a coke particle. It also results in the conservation of a sound core and in the apparent alleviation of the degradation of the particle as a whole (compared to that without alkali).
3) Coke B made from a specially inferior coal blend shows a steep fall of strength after reaction at a overall gasification ratio of 10% or so, and this feature becomes remarkable under the presence of alkali, while the strength of coke A made from an ordinary coal blend decreases gradually as the degree of reaction increases.
The difference between coke A and B seems to suggest that “critical degree of gasification”, at which it may disintegrate, of the latter is essentially smaller than that of the former. It also seems to suggest that the remarkable degradation of coke B probable at some high degree of reaction may be at least one of the reason of its severe disintegration in the experimental blast furnace (in the 26th run).
他の人はこちらも検索
鉄と鋼 Vol.50(1964), No.13
鉄と鋼 Vol.70(1984), No.11
鉄と鋼 Vol.45(1959), No.11
Removal of Phosphorus and Other Impurities from Cokes by Heating and Leaching
Kyojiro KANEKO, Masafumi MAEDA, Nobuo SANO, Hajime OHTSUKA, Yukio MATSUSHITA
pp. 495-504
抄録
One of the means to produce low phosphorus stainless steel is the removal of phosphorus from ferrochromium, which is its main source into the steels. In view of the fact that 70% of phosphorus in ferrochromium comes from cokes used as the reducing agent, the technical possibility to remove phosphorus and other impurities from various cokes has been studied in the present work by heating at elevated temperatures under argon at atmospheric and reduced pressures and followed by leaching into various acid solutions.
It was found that as the temperature was raised, phosphorus, sulfur, and nitrogen originally incorporated in coke matrix were gradually eliminated, following the initial decomposition of those included in inorganic minerals. At the same time, aluminum, calcium, and iron were removed as metallic vapor, silicon remaining in cokes as silicon carbide to the last.
Acid solutions dissolved only inorganic phosphorus and sulfur.
他の人はこちらも検索
鉄と鋼 Vol.64(1978), No.1
鉄と鋼 Vol.65(1979), No.7
鉄と鋼 Vol.64(1978), No.11
The Melt-Down Properties of the Blast Furnace Burdens
Katsuya ONO, Kazuyoshi YAMAGUCHI, Akitoshi SHIGEMI, Nobunao NISHIDA, Kenjiro KANBARA
pp. 505-514
抄録
The melt-down properties of the burdens is very important for operation of the blast furnace. For high efficiency and stabilization of the blast furnace operation, it seems desirable to use the burdens which melt down rapidly at high temperature in the blast furnace.
A series of the experiments was carried out for clarifying the factors which govern the melt-down properties of the burdens, using various kinds of iron ores and agglomerates.
1) Melt-down behavior is closely related to amount and melting point of gangue and degree of pre-reduction. By the combination of these properties, either coagulation and fusion of slag formed from gangue or absorption of carbon in metal produced by reduction governs the melt-down behavior, and the temperature at beginning of melt-down is determined.
2) The burdens which have following properties melt down at high temperature and are desirable for the blast furnace operation.
Lump ore: comparative large amount (100-200kg/t·Fe) and high melting temperature (>1600°C) of gangue.
Acid pellet: high melting temperature of gangue (>1600°C).
Sinter: basicity (CaO/SiO2) from 1.5 to 1.8.
Self-fluxing and cold bond pellets: melting point of ganguc from 1500 to 1700°C.
The Construction of Lath Martensite
Tadashi MAKI, Kaneaki TSUZAKI, Imao TAMURA
pp. 515-524
抄録
Structural characteristics of lath martensite were investigated in detail using Fe-C alloys and plain carbon steels with carbon contents of up to 0.8%, 18%Ni maraging steel and Fe-0.2%C alloys with an addition of about 1% of Mn, Si, Ni, Cr, or Mo. The construction of lath martensite structure changes with carbon content. The packet regions are clearly formed within a prior austenite grain at lower carbon content (up to about 0.4%C), but they are not observed in the range of 0.5-0.8%C. The block regions within a packet are observed only in the steels bclow about 0.3%C. Structure of lath martensite in the 18Ni maraging steel is characterized by the block regions which are well-developed and completcly partition a packet region, whereas the blocks in the low carbon steels are not well-developed regions. A packet size gradually decreases with increase in carbon content up to 0.4%C and rapidly decreases in the 0.6 and 0.8%C. A linear relation exists between the austenite grain size and packet size in Fe-0.2%C alloy and 18Ni maraging steel. The increase in block width of maraging steel with increasing austenite grain size is very small. Alloying elements within about 1% have little effect on the construction of lath martensite and the packet size.
他の人はこちらも検索
鉄と鋼 Vol.80(1994), No.12
Effect of Hydrogen on Crack Propagation Behavi or and Microstructures around Cracks in α-Iron
Akihisa INOUE, Yoshihiro HOSOYA, Tsuyoshi MASUMOTO
pp. 525-534
抄録
The effect of hydrogen on the crack propagation behavior and the microstmctures around cracks in α-iron has been examined by means of tensile testing with simultaneou scharging of hydrogen and microscopic observation. The results obtained are summarized as follows:
(1) The yield strength and the flow stress at 2% strain increase by absorbing hydmgen, whereas the fracture strain and the total energy spent in the tensile test decrease remarkably.
(2) According to the notch tensile tests, the force for crack initiation does not change so much with the increase in hydrogen content, but the plastic strain induced around crack and the amount of wark required for the propagation of cracks decrease notably with increasing the hydrogen content.
(3) Near the crack edge in notched specimen deformed underuncharged condition, well-defined cell walls which are elongated along the crack edge are observed. As the hydrogen content increases, the distribution of dislocations becomes uniform, the formation of well-developed cell structure is supPressed and the dislocation density slightly increases, indicating the difficulty in relaxation of stress concentration around cracks of α-iron.
(4) It is suggested that the hydrogen embrittlement of α-iron is mainly due to the lowering of deformability in the vicinity of cracks by the absorption of hydrogen and the easy initiation of the grain boundary cracking caused by the segregation and precipitation of absorbed hydrogen.
他の人はこちらも検索
鉄と鋼 Vol.64(1978), No.1
鉄と鋼 Vol.65(1979), No.7
鉄と鋼 Vol.64(1978), No.11
Delayed Fracture under Repeating Stress in Various High Strength Steels
Mitsuo KIDO, Keijiro NAKASA, Hideo TAKEI
pp. 535-541
抄録
The effect of superposition of small repeating stress on σsec the endurance stress under which no crack initiation occurs within 100h, and on the incubation time (time of crack initiation) has been investigated using notched specimens of four kinds of steels (JIS: SKD61, SNCM8, SUS420J2, and 18Ni mamging steel) quenched and tempered at various temperatures. The results obtained are as follows:
(1) For all the steels examined, the endurance stress σsec was not varied by the superposition of repeating stress when the stress amplitude, σa, was 2.5kg/mmmm2, when σa was larger than 5kg/mmmm2, however, σsec decreased with increase of σa.
(2) The amount of decrease ofσsec by the superposition of repeating stress seemed to be dependent not only on the yield strength of the materials but also on the stability of protective film on the notch surface against repeating stress and the intensity of metal-environment corrosion reaction after the destruction of the protective film by repeating stress. 18Ni maraging steel and SUS420J2 stainless steel with higher value of σsec under static stress revealed the smaller decrease of σsec under repeating stress than SKD61 and SNCM8 steels.
Effect of Alloying Elements on Strengthening and Toughening of Maraging Steels through α′_??_γ Cyclic Heat Treatment
Kozo NAKAZAWA, Yoshikuni KAWABE, Seiichi MUNEKI
pp. 542-550
抄録
The effect of addition of 5Co, 1Ti or 1-2Mo (per cent by weight) to Fe-17Ni-15Co-4Mo-2Ti alloy has been studied in order to produce higher strength maraging steels. Grain refinement through α′_??_γ cyclic heat treatment was applied and the microstructures and mechanical properties were investigated in comparison with the results of conventional solution heat treatment. Initial grain size prior to cyclic treatment was coarse (0.6mm) because of complete solution treatment at high temperature. The addition of each alloying element increased strength level for base alloy from 2550MPa to 2750MPa and lowered fracture toughness irrespective of the kind of alloying elements and the heat treatment. The results of conventional solution treatment showed that there existed little effect of alloying elements on grain size, and the ductility decreased monotonously according to the increase in strength level. In the case of cyclic treatment, the addition of Co promoted grain refinement (7μm) and thus yielded the same ductility as that of the base alloy even at higher strength level, whereas the addition of Ti and Mo suppressed refinement (11-20μm) leading to marked decrease in ductility. The cyclic treatment was thus found to be more useful in obtaining good combination of strength, ductility and toughness than the conventional solution treatment, particularly, in the alloy with high Co.
Two-Strands Welded Steel Tube Mill Installation
Miyoshi NISHIMURA, Yutaka HIROKI, Shigeru TANEBE
pp. 551-555
抄録
A new two-strands welded tube mill, developed for the increase of productivity of small diameter welded steel tubes, is introduced. Detailed discussion are made on the composition of the mill which consists of two production lines and the process of production which is described as follows:
A strand of hoop steel is supplied to the uncoiler and further to the slitter in order to be divided into two strands. After slitting, each two strands are simultaneously formed, welded and finished into tubes. The two tubes thus obtained are then simultaneously cut to the predetermined length and passed through a high efficiency smoothing and fine finishing Process to obtain final products. In addition, a description is given of the improvement of production efficiency attained by the installation of the mill as well as the possibility of producing high quality welded steel tubes by the use of an automatic welding temperature control system.
論文アクセスランキング
06 Sep. (Last 30 Days)
-
Perspectives on the Promising Pathways to Zero Carbon Emissions in the Steel Industry toward 2050
ISIJ International Vol.65(2025), No.2
-
溶鋼中での各種酸化物系介在物の成長・除去と凝集
鉄と鋼 Vol.111(2025), No.11
-
Finite Element Analysis of Bubble Growth and Particle Swelling during Coal Pyrolysis
ISIJ International Vol.65(2025), No.9
-
通電誘起高速共晶反応によるAl/Cu異材接合形成につながる界面挙動
溶接学会論文集 Vol.43(2025), No.2
-
Corrosion Behavior of Carbon Steel under Soil Drying Conditions
ISIJ International 早期公開
-
980 MPa級高張力鋼板の固相抵抗スポット接合
鉄と鋼 早期公開
-
-
-
Copper removal of liquid steel containing 0.25 % carbon using Fe2O3-CaCl2-SiO2 flux
ISIJ International 早期公開
-
Evaluation of Feature Selection Methods for Oxygen Supply Prediction in BOF Steelmaking
ISIJ International 早期公開
この機能はログイン後に利用できます。
下のボタンをクリックしてください。