鉄と鋼 Vol. 41 (1955), No. 7
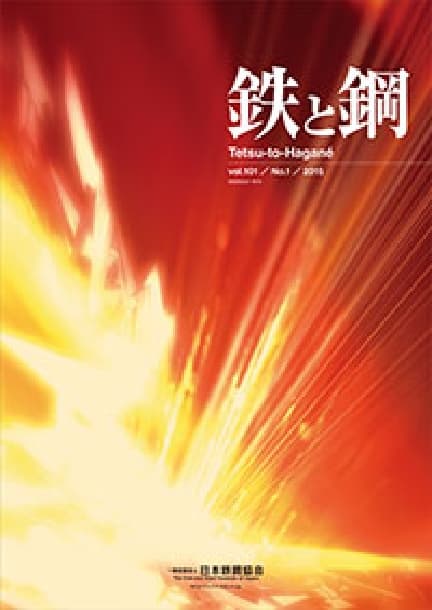
Grid List Abstracts
オンライン版ISSN: | 1883-2954 |
冊子版ISSN: | 0021-1575 |
発行機関: | The Iron and Steel Institute of Japan |
Backnumber
-
Vol. 111 (2025)
-
Vol. 110 (2024)
-
Vol. 109 (2023)
-
Vol. 108 (2022)
-
Vol. 107 (2021)
-
Vol. 106 (2020)
-
Vol. 105 (2019)
-
Vol. 104 (2018)
-
Vol. 103 (2017)
-
Vol. 102 (2016)
-
Vol. 101 (2015)
-
Vol. 100 (2014)
-
Vol. 99 (2013)
-
Vol. 98 (2012)
-
Vol. 97 (2011)
-
Vol. 96 (2010)
-
Vol. 95 (2009)
-
Vol. 94 (2008)
-
Vol. 93 (2007)
-
Vol. 92 (2006)
-
Vol. 91 (2005)
-
Vol. 90 (2004)
-
Vol. 89 (2003)
-
Vol. 88 (2002)
-
Vol. 87 (2001)
-
Vol. 86 (2000)
-
Vol. 85 (1999)
-
Vol. 84 (1998)
-
Vol. 83 (1997)
-
Vol. 82 (1996)
-
Vol. 81 (1995)
-
Vol. 80 (1994)
-
Vol. 79 (1993)
-
Vol. 78 (1992)
-
Vol. 77 (1991)
-
Vol. 76 (1990)
-
Vol. 75 (1989)
-
Vol. 74 (1988)
-
Vol. 73 (1987)
-
Vol. 72 (1986)
-
Vol. 71 (1985)
-
Vol. 70 (1984)
-
Vol. 69 (1983)
-
Vol. 68 (1982)
-
Vol. 67 (1981)
-
Vol. 66 (1980)
-
Vol. 65 (1979)
-
Vol. 64 (1978)
-
Vol. 63 (1977)
-
Vol. 62 (1976)
-
Vol. 61 (1975)
-
Vol. 60 (1974)
-
Vol. 59 (1973)
-
Vol. 58 (1972)
-
Vol. 57 (1971)
-
Vol. 56 (1970)
-
Vol. 55 (1969)
-
Vol. 54 (1968)
-
Vol. 53 (1967)
-
Vol. 52 (1966)
-
Vol. 51 (1965)
-
Vol. 50 (1964)
-
Vol. 49 (1963)
-
Vol. 48 (1962)
-
Vol. 47 (1961)
-
Vol. 46 (1960)
-
Vol. 45 (1959)
-
Vol. 44 (1958)
-
Vol. 43 (1957)
-
Vol. 42 (1956)
-
Vol. 41 (1955)
キーワードランキング
07 Sep. (Last 30 Days)
鉄と鋼 Vol. 41 (1955), No. 7
REMINISCENCE OF THE SITUATIONS AT ESTABLISHMENT OF THE IRON & STEEL INSTITUTE OF JAPAN
Kuniichi Tawara
pp. 680-682
抄録
The present article is a memorandum of 40 years experience of the author in the history of the Institute.
In July 8th,1914 (Taisho-3), Messrs. Kaichiro Imaizumi, Kuniichi Tawara, Kageyoshi Noro and Koroku Komura assembled together to discuss the establishment of an Institute in view of publication of an organ periodical, installation of an laboratory and a display station and making such research as would be suitable for science and industry. On October 4th 1915 (Taisho-4) a meeting of promoters including the aforementioned and besides Messrs. Fuji Tanaka, Masayoshi Tsutsumi, and Seiichi Terano, to discuss about the preparation.
On Feb.6th,1915 (Taisho-4), the inauguration meeting was held at the Building of Nippon Kogyokai,, Tokyo and the enlisted members then attained to 610 persons. The directors were Messrs. Kaichiro Imaizumi, Kuniichi Tawara, Koroku Komura and Seiichi Terano, the chairman of directors being Mr. Kageyoshi Noro. The organ periodical “Tetsu-to-Hagané”(The Journal of The Iron & Steel Institute of Japan) was first published in Mar.1915. Since then the Journal has been published every month incessantly excepting a period from Nov.1944 to Dec.1945. The establishment of the Institute was entirely initiated by the merits of Dr. Prof. Noro, former professor of Tokyo Imperial University and other collaborators were all his disciples. In his later years Dr. Noro became consultant to Tanaka (the present Kamaishi) Iron Works and the Governmental Edamitsu (the present Yawata)Iron Works to develop the blast furnace operations and died in 1923 (Taisho-12). The special features of the Regulations of the Institute was the qualification of the Institute members, that comprehended not only the scientists, engineers, manufacturers but the sellers and users. The reason simply lies in that the iron and steel industry could not do without cooperation of the users and sales agents. This must strictly be reminded for a synthetic engineering such as the iron & steel industry. From the first outset the author was appointed an editor of the Journal and has experienecd a number of difficulties. The other editors in cooperation were Messrs. Kajima Muroi, Yoshihiro Kawakami and Katsumi Inouye.
Beside the senior Dr. Noro. the author also recollected Drs. Imaizumi, Komura, Hattori and Tsuruo Noda, Saburo Watanabe and Takeshi Kawamura to be forerunners of the siderurgical engineers in Japan and the best contributors to development of the Institute. Some of the prize funds and the Library books of the Institute were all donations from or in memory of these forerunners.
他の人はこちらも検索
鉄と鋼 Vol.41(1955), No.6
鉄と鋼 Vol.41(1955), No.7
鉄と鋼 Vol.41(1955), No.7
THE POSTWAR DEVELOPMENT OF IRON AND STEEL INDUSTRY IN JAPAN
Takichi Mitsui
pp. 682-695
抄録
Among the greatest obstacles in the postwar recovery of steel industry in Japan were. counted the shortage of coal, the removal of subvention to the iron and steelprices and -decentralization of large steel firms. A tragic atmosphere thus clouded was pushed away by the breakout of the Korean Incident (June 1950). Again the prices became enhanced. The export was extended and the production increased. Thence came a chance of modernization of iron and steel industry in Japan. The scheme of this plan that had been plotted by the Rationalization Council in the first half of 1951 was encouraged in the second half by establishment of Japan Development Bank, institution of special overeas credit by the Bank of Japan and the favorable development in Capital market.
Capital development and production increase of steel firms in Japan was suceessively realized -during the year of 1951. However, towards 1952 the period of reaction began so that an intensification of the sales competition gradually invited a drop in the steel prices, notwith-standing a temporary short boom due to a steel strike in the United States.
In April 1952, the industrial control of the Occupation Forces ended and Japan was again allowed to enter an international economic circles.
At this moment, owing to establishment of the European Coal and Steel Community, progress of modernization progress in several countries and recovery of the West-Germany iron and steel industry, the steel industry of Japan too was obliged to be entangled with the international contest.
In 1953, the steel market again tended to a slight boom due to domestic investment and consumption but at the end of the same year decrease in bath munition demands and steel export again occurred. Without finding domestic demands, the steel products of Japan began to flow out overseas. At this time happily owing to a shortage of steel export from Europe Japanese products filled the markets of South America and India and enjoyed higher prices. It was also evident at the end of 1954 that the iron and steel industry in rapan again inclined to an expansive production.
After such historical introduction, the author described in detail (1) the process of rationalization and financing concerned; (2) trends in the situations of raw materials for iron and steel; (3) domestic market and export; (4) some tendencies in special steels; and (5) future prospects.
他の人はこちらも検索
鉄と鋼 Vol.41(1955), No.7
鉄と鋼 Vol.41(1955), No.7
鉄と鋼 Vol.41(1955), No.6
RECENT DEVELOPMENT IN THE STUDY OF IRON AND STEEL IN JAPAN
Tokushichi Mishima
pp. 695-701
抄録
The development in the study of iron and steel in Japan during the year 1946-55h as been surveyed in this, article. First, subjects of study has been reviewed, then detailed description has been made under the several major headings, classified by the author. The use of semicaking coal produced in Hokkaido has been successfully used for blast furnace works and several other problems, such as the desulphurization of pig iron, elimination of copper from pyrite cinder, pelletizing as well as the pre-treatment of raw materials have been among the problems concerned in the field of iron making. The utilization of pyrite cinder, pyrrohotite, magnetite sand, laterite and other minerals containing iron which has not yet been utilized as an iron ore has been considered. Heat-treatment has been studied by many workers and the application of S-curve, repeated tempering procedure, sub-zero of deep cooling treatment and stepped quenching have been the chief subjects studied. None. the less research works have been made in the field of physical chemistry of iron and steel making; and the measurement of activity in steel making reactions, study on the equillibrium in the reduction of iron oxide, activity measurement of the elements coexisting in molten iron and the study on the mutual-relationships between each stages in open hearth operation have carried out. Besides this, many valuable research results have been published, for example; on white spot problem, behavior of gases, heat-resisting steels, theoretical and practical study of working, boron steel and the measurement of hardenability by Jominy test, use of oxygen in steel making, quality control and process control, development of some new methods of research work and vacuum melting technology. As the reconstruction from the war disaster was not complete during the.. eaatlier years, few important study work was carried out before 1949. The developments made in this decade can be said to be striking, but it is a pity of the author. that only a few purely original study has been found.
他の人はこちらも検索
鉄と鋼 Vol.41(1955), No.7
鉄と鋼 Vol.41(1955), No.7
鉄と鋼 Vol.41(1955), No.6
TRANSITIONS IN RAW MATERIALS FOR IRON MANUFACTURING AFTER WAR IN JAPAN
Yuzuru Asada
pp. 702-713
抄録
This article gives an outline of the transitions in the raw materials for the manufacture of iron from the end of the war. It explains how the international situation has caused the changes in the raw materials used in iron making because of the dependence of Japanese iron and steel industry on the raw materials from abroad. It analyses and discusses, from the angle of raw materials, Japanese iron and steel industry which has been rehabilitated rapidly after the war, and records the results of various researches and improvements. The article concludes with writer's view on the measures to be taken in the future for the solution of the question of raw materials for iron making in Japan.
他の人はこちらも検索
鉄と鋼 Vol.41(1955), No.6
鉄と鋼 Vol.41(1955), No.7
鉄と鋼 Vol.41(1955), No.7
PROGRESS OF PIG IRON MAKING PROCESS IN JAPAN
Kamekichi Wada
pp. 714-722
抄録
As nothing but domestic iron ore of high sulphur and of poor quality was used, pig iron making operation in Japan right after the ternination of the War could not reach the high efficiency of production, despite of the all-out efforts they were making. As the result of rationalization of equipments and strictly-enforced quality control launched in around 1950, however, the 1000 ton blast furnace, the actual production of which had been 800 tons before the War, was able to tap out 1200 tons per day at the highest in the monthly average in 1954. The average coke ratio in Japan came down below 700 kg. per ton of pig iron, and that of Yawata Works since Sept.1954 has kept up the bright record of 680 kg, surpassing the world level.
The present author explained that this advancement was brougnt about chiefly by the improvement of facilities and the quality control of coke as well as by the increased ratio of sinter in the burden of B. F. A mention is also made of the technical progress achieved in Yawata Works.
他の人はこちらも検索
鉄と鋼 Vol.41(1955), No.6
鉄と鋼 Vol.41(1955), No.7
鉄と鋼 Vol.41(1955), No.7
PROGRESS OF STEEL MAKING PROCESS IN JAPAN
Shigeo Hachiya
pp. 723-731
抄録
The iron and steel industry in Japan was full of great difficulties for several years after the cessation of World War-I due to social chaos, shortage of coal and electric power which are the prime moving power of industries, and poor qualitif; s of raw materials.
However, with the importation of iron ores from Feb.1948, the iron and steel industry gradually started to rehabilitate to its normal production. Furthermore, after 1949 with the kind assistance of the United States of America, it was possible to modernize the steel making facilities and improve its operation by introducing the American technical “know-how”. Especially, by using fuel oil for firing the open hearth furnaces, its operation were greatly rationalized by controlling its operation with instruments and also adopting the epoch making process of oxygen steelmaking method, both of which greatly contributed in improving the efficiency cf steel making.
Consequently some of the shops in Japan has achieved an excellent record with such low fuel consumption rate of 700,000 Kcal per ton of steel, which is the highest standard in the world. With the blowing-in of the converter in Japan belonging to Nippon Steel Tube Co. for the first time in 1949 since the end of the war, the blowing of open hearth furnaces and the adoption of oxygen steelmaking process, there has been made a remarkable progress in the quality and production of steel ingots.
Thus the production of steel ingots in 1953 has, broke the record of 7,650,000 tons and exceeded it with the operation of only 56% of the total furnaces in Japan. Today Japan has completely recovered from the chaos of war in the field of steelmaking and the author took this opportunity to report the development in technical progress.
他の人はこちらも検索
鉄と鋼 Vol.41(1955), No.7
鉄と鋼 Vol.41(1955), No.7
鉄と鋼 Vol.41(1955), No.6
RECENT DEVELOPMENT IN ROLLING OF BARS AND SECTION IN JAPAN
Masao Yukawa
pp. 732-743
抄録
At the end of Pacific War, Japan had 8 units of blooming mills. During ten years since then new establishment of 4 mills and renovation of 1 plant were performed. Besides, bulk amount of fund was invested to the established blooming mills to improve the soaking pits and other accessories. Above all, the Chiba plant of Kawasaki Iron Mfg. Co. constructed a latest and largest blooming mill, in which majority of mechanical equipments had been imported from the United States. On the cotrary, the plant of Nippon Steel Tube Co. shows the most modern mill made of Japanese equipments. Majority of soaking pits had been improved_in Japan following instructions of Messrs. Fred N. Hays and James T. Macleod (Carnegie-Illinois Steel Co. ). As for the bloom-rolling stands, renovation of the millmotors and the motor-generator sets was performed by turns in respective plants. The quality of cast or forged rolls still remained an unsolved problem. No continuous mill for billets, however, had been constructed anew. Nevertheless, some improvements had been made in the ways of rolling such as utilization of diamond-squared calibers and roller guides. As for the finishing of billets, Yawata Iron & Steel Works had used since July 1952 a. hot-scarfing equipment (Lindé Co. ) with heat-resisting nozzles made in Japan.
Moreover, in the field of bar sections rolling efforts had been made for recovery of devastated equipments, improvement in the quality, of products, reduction of consumption-unit of fuels and power and enhancement of the labor-productivity. In the continuous reheating furnaces, rationalization of the structure, amelioration of refractories and control-automation were performed. Heavy oil and high-pressure gas began to be utilized rationally instead of the traditional coal-combustion. As for the main motor, the chartacteristics were increase of output and magnification in the number of rotation and widening of the range of velocitychange. To meet recent demands in multiformed sections, some equipment was devised for a speediest resetting of rolls especially for the sake of heavy sections. In the new wire-rod mill at Hikari (Yawata Iron & Steel Co.). all-continuous equipment had been projected so that increase in the unit-weight of billets, increase in the finish-rolling speed, independent driving of each stand and utilization of vertical rolling stands were prospected for an enhanced production of products homogenous in quality and shape. In conclusion, the stress was laid on further improvement in the bar and section mills in Japan, although majority of the rationalization fund in the postwar Japan had been invested to amelioration of the plate or sheet mills.
PROGRESS IN ROLLING OF FLAT STEELS IN JAPAN
Satoru Uchikawa
pp. 744-756
抄録
In this article the writer reviews the progress of Japanese steel industry in the making of flat steels during the past ten years since the end of War, referring to the changes in the production and improvements in rolling mills, together with the developments in the erection of new equipment under the Steel Industry Rationalization Program.
The advancements during the same period in the methods of operation and techniques of the manufacture of plates, steets and secondary or other related products are also outlined. The writer further adds briefly his view on the future prospect of this matter.
DEVELOPMENT OF STEEL TUBE ROLLING IN JAPAN
Kanamé Mochizuki
pp. 757-762
抄録
In Japan, many tube manufacturing equipments have been improved and excellently. progressed during last decade. Fourteen electric-resistance-weld tube mills have been installed and one continuous buttweld tube mill is under operation. But the operation of two Ehrhardt push-bench-type seamless-tube mills have been suspended. In tube-finishing plants, many new threading machines have been imported, and a new cold-drawing machine and a Rockrite rolling mill have been installed. Now many experiments are being made on the cold tube-drawing process with the back tension.
他の人はこちらも検索
鉄と鋼 Vol.41(1955), No.7
鉄と鋼 Vol.41(1955), No.8
DEVELOPMENT OF STEEL FORGING PROCESS IN JAPAN
Sasaburo Kobayashi
pp. 762-770
抄録
The steel forging industry in Japan, which had suffered a tragic outcome due to downfall of heavy industries after the Great War- H, gradually has been recovering with rehabilitation. of industries. Nevertheless, from the perspective of quantity, the 1953 figure still lies at the stage of 38% of the 1940 statistics. In the field of techniques, however, rationalization of the equipment has proceeded and attained to an international level in many points owing to introduction of the heat control, the metallurgical control and the statistical quality control. The present paper described the progress in the modern forging technique with. reference to heavy rotorshafts. for generators, steam-turbine rotorshafts and others. The heat treatment after forging of these forged products has made so much progress and, by utilization of the S-curves, forgings have been less liable to suffer from occurrence of flakes. Also, the inspection of internal defects in these forged products by use of supersonic waves has been applied in practice, especially to the generator-rotorshafts.
他の人はこちらも検索
鉄と鋼 Vol.41(1955), No.8
鉄と鋼 Vol.41(1955), No.7
鉄と鋼 Vol.105(2019), No.4
PROGRESS OF IRON AND STEEL CASTING INDUSTRY IN JAPAN
Hironu Tanimura
pp. 770-776
抄録
A review of the iron and steel casting industry, during the past ten years, was described. The progress of the casting industry in this period has much correlation to the research activity in the pre-war and war time, therefore this review covers some details of pre-war progress.
他の人はこちらも検索
鉄と鋼 Vol.41(1955), No.6
鉄と鋼 Vol.41(1955), No.7
鉄と鋼 Vol.41(1955), No.7
PROGRESS OF SPECIAL-STEEL MAKING PROCESS IN JAPAN
Y. Ishihara
pp. 777-786
抄録
1. Special-Steel Making iu Japan
In Japan special steel makin was started in 1882 by means of the crucible furnace melting, and since 1914 the electric arc furnace steel-making has been studied. The production of arcfurnace steel increased year by year, and subsequently in 1938 crucible-furnace steel was wholly replaced by electric furnace steel.
In 1931 steel making by means of induction furnace was. started.
At first the capacity of the arc furnace was, as small as, not over 3t. However., towards 1932 it was developed to 5t-10t, and a few 15t and 30t furnaces were erected. About 1937 many furnaces rated 10t-15t were erected. Accordingly the promotion reached to the maximum amount of 2,258,000t, of which the electric furnace steel occupied 75%, in 1944.
After the war the production suddenly decreased to only 80,000t, but during the Korean war it increased to 300,000t.
In 1954, Japan had 142 arc furnaces, whose total capacity was 1,100,000t, and 75 induction furnaces, whose capacity 140,000t.
Owing to the investigation of the Research Institute for Ion, Steel and Other Metals and the 19th Sub-Committee of the Japan Society for the Production of Science, the practice of Special-Steel making of Japan was remarkably improved and steels of good quality are now made by overcoming the bad conditions of raw materials and refractory materials.
2. Development of Electric Furnaces
The range of the transformer capacity, was 300-400 KVA/t, but the recent practice tends towards utilizing higher voltage and larger transformer capacity aiming at quick melting. In order to control electric fluctuation, the “Amplidine” system is in use.
An electric induction stirrer is now studied for stirring the bath in order to obtain both the uniform chemical composition and good quality.
3. Basic Arc Furnace Process (referring constructional steel and case-hardening steel)
(a) Oxidizing Period:
In the early stage until about 1945, active boiling by adding the ore was not in practice. But between 1936 and 1940 some light boiling practice was introduced, and after 1940 the violent boiling was carried out adding ore 20-30kg/t. Since 1951 the oxygen lancing has been applied to the melting resulting in a success to produce low-hydrogen content, good steel and Iow-carbon stainless steel.
(b) Reducing Period:
In the early stage until about 1935, reducing was controlled only by the carbide slag process. From about 1936 the white slag process was adopted. Since about 1940, the practice has changed to the following: After refining the oxidizing slags, a few deoxidizing materials such as ferro-silicon, calcium-silicide and aluminium are added in order to force the active deoxidizing reaction, then the slag was controlled to be white one of weak diffusion, thereby to refine the steel. It is important to lower the content of hydrogen in steel to obtain sound ingots.
It should be noted that the quick method of hydrogen analysis was invented by Japan Special Steel Co., Ltd. By this method they control the furnace pactice in order to lower the hydrogen content under 7cc/100g for medium-and low-carbon or alloy steel and 11cc/100g for 13%Cr stainless steel. They are now obtaining gpod, sound ingots by the method.
4. Ingot Making
Exothermic hot-topping mixtures are used for the purpose of obtaining larger yield, and recently the electric arc hot-topping process is applied.
The continuous casting process, comprising William's process and Rossi-yunghan's process, is now planned in some works in Japan.
It is important to eliminate the hair cracks or sand marks from steel. As it was found that the process of casting the ingots was partly responsible for this failure, the method of teaming practi is now studied.
他の人はこちらも検索
鉄と鋼 Vol.41(1955), No.6
鉄と鋼 Vol.41(1955), No.7
鉄と鋼 Vol.41(1955), No.7
PROGRESS OF MEASUREMENT TECHNIQUES IN IRON AND STEEL INDUSTRY
Ziro Yamauti
pp. 787-795
抄録
Therea re two main fields of the measuring techniques developed and applied to the iron and steel industry in Japan during these ten years since the War end. The one is that for the heat economical request which has arisen from the insufficiency of fuel and the other is - that for the improvement of quality and yield of products, which has been studied at the 19th and the 54th Research Committes of the Japan Society for Promotion of Science long before the War.
1. Progress of the Instrumentation for the Heat Econony.
In order to overcome the worst condition of fuel at the time of the after-war, the movement of heat control was vividly started in iron and steel industry and the instrumentation was taken to be important to be applied. In December, a Committee of Instrumentation was organized to study various problems to be solved to realize the instrumentation in iron and steel industry.
In June,1949, the Technical Organiration of Heat Economy was started, under which a Special Committee of Instruments was organised to study the instrumentation techniques. This Committee worked to elevate the interest to instrumentation among the steel works in Japan, and the instrumentation of open hearth furnaces and heating furnaces advanced to be adopted very rapidly in the great many works.
The Committee decided to adopt the standard instruments to be installed for the furnace operation. The instrument makers developed various instruments of new idea to meet the special requirements, which were proposed by the Committee. After some time of researches and studies proceeded with the instrumentation, the Commitee found many problems to be solved and made success in determining the normal conditions of operation.
In November,1953, the Committee published a manual of the instrumentation which covered the administration, the kind of instruments, the methods of installation, maintainance, repair, calibration, instrumentation, and so forth.
2. Progress of the Measuring Techniques for the Improvement of Quality of Products.
Among various measuring techniques to improve the quality of products, the high temprature measuremnt for steel making have been studied since 1935 by the Second Sub-Committee of the 19th Research Committee. In the pre-war period, many fruitful results were obtained in contributing to improve steel making. After the war-end, some of the items to be studied by the Subcommittee were changed to meet the urgent need, while some others were continued to match the conditions at that time.
Among the latter items, there was the development of photoelectric pyrometer, which was effectively used to measure continuously and to control the temperature of the ceiling of open hearth furnaces. Another item was the cobalt glass for use before the open hearth furnace. Before the war Sub-committee studied the standardization of the cobalt glass and after the war the sub-commitee studied it from the view point of temperature deterimination which was analysed by colorimety. This new idea of research resulted in the development of a coloritheter without an artificial light source and in the standardization of the cobalt glass of two kinds for forging. In the next step the cobalt. glass was studied from the view point of protection of eyes against non-visible rays, without changing the hue. It was in effect in getting a blue glass which guard the eyes against even infra-red light.
The third item which is very important is the temperature measurement of molten steel in the open hearth furnace. Before the war there were records of temperatue distribution in the furnaces, with specially designed direct immersion thermo-couples. After the war they studied practically the constructions of the thermo-couples which were suited to be used for daily works and made success in using them daily combined with electronic recorders. They were usually calibrated with Pd-wire method.
CONTROL SYSTEMS AND THEIR PROGRESS IN IRON AND STEEL PLANTS IN JAPAN
Takeshi Yamaoka
pp. 796-803
抄録
Since the surrender, every industry in Japan suffered a great change and obliged. to meet n free competition.. For such purpose it was necessary to make. rationalization and to. improve in quality of steel products. In July 1949 the Industrial Stadardization Law was established in Japan, based on which the Japanese Industrial Standard(JIS) Research Association was instituted. Besides, the Industrial Rationalization Council was established and the Heat Control Law was promulgated in 1951.
In the present paper the recent progress in statistical quality. control(SQC), the heat control and other type controlling techniques in siderurgy in Japan were discussed. At first the introduction of statistical quality control(July 1950) and its performance in Japan, applications of the statistical methods, their systematization in steel firms, formulation of the operational standards and the necessity of sampling were discussed. Then an establishment of the inspection department and applications of random sampling, the study and performance of the market survey and the SQC applied in JIS specifications were. informed.
Next, the advent of the Heat Economy Technical Committee and its activities since June 1949, popularization of the heat balance, the improvements in reheating furnaces, lowering of the analysed unit of fuel consumption in open hearth furnaces, strengthening of the gas control and progressive use of heavy oil in place of coal for the purpose of rationalised fuel control were dealt with.
Moreover, ideas of the preventive maintenance of machinery and equipments were introduced, among which is counted the lubricant control. Recent birth of the color dynamic and the color control and a penetration of the industrial salty were informed.
In conclusion, the author mentioned the recent revolution in control systems, re-examination of various control syetems, some problems of “staffs” and the “line” in plants and other problems such as “operation research” (OR) were discussed with reference to the future iron and steel industry in Japan.
MODERN TRENDS IN THE IRON AND STEEL STANDARD SPECIFICATION IN JAPAN
Hiroshi Yoshimura
pp. 803-812
抄録
The enterprise of Goverment engineering normalization started by the hand of the Research Committe for Engineering Products Specification Unification (Kogyohin-Kikaku-Toitsu Chosakai)in 1921, when the specification of the metallic tensile specimen was marked as No.1 of Japanese Engineering Standard(JES). In 1939, when the Chino-Japanese Incident was prospected to be long-lasting, another group of Provisional JES specifications were established to meet the quasi-war or war-time demands. At the time of defeat(Aug.1945), there were present 520 JES and 933 provisinal JES specifications.
In 1949, the old Committee since 1921 was abolished and an Engineering Standard Research Committee(Kogyo-Hyojun-Chosakai) was instituted. Here new specifications(New JES) under 20 divisions were to be determined. The iron and steel specifications belonged to the division of Japanese Metal Standard (chairman Dr. Kuniichi Tawara), which was again subdivided into several subdivisions. The conversion from the old to new standard were successively performed in this Division.
However, to overcome all out-of-date traditions and to realize a scientific rationalization, the 5 th Session of Japanese Parliament in 1949 decided to pass an Industrial Standardization Law (Kogyo-Hyojunka-ho). To promote this standardization Japanese Industrial Standard Research Committee (Nihon Kogyo-Hyojun-Chosakai) was instituted, that belonged to 10 Ministries including Ministry of International Trade and Industry (MITI). At the top of this organization was situated a Standard Council (Hyojun-Kaigi), under which there were several divisions under which again respective technical committees should be organized for discussion of each (JIS) specifications. To all discussions in these organizations equitably participated opinions of manufactacturers, users, sellers and neutral scientists. In the Metal Divisions, Dr. Tokushichi Mishima was appointed chairman. In March 1954 all necessary transference from the old to the new iron and steel specifications had been completed. In February 1955, the number of specifications in the iron and steel division amounted to 138.
On the other hand,. in view of encouraging the specified products and protecting the, bona fide manufacturers, the Industrial Standardization Law instituted a system of JIS marking for the qualified products.
After the aforementioned historical introduction the author descibed in detail the postwar progress of iron and steel JIS specifications in fields of raw meterials, rolled steel products by different shapes, chemical compostions, steel casting and various methods of testing.
TREND AND DEVELOPMENT OF LUBRICATION ENGINEERING IN MODERN IRON AND STEEL INDUSTRY
Hideo Tonomura
pp. 813-816
抄録
Among various machines and equipments included in the iron and steel industry, rolling mills and their accessories are most difficult and hence progressive in the view point of lubrication. Therefore hereby statements are made upon this field of industry mainly. In this connection brief review on oil film bearings in strip mills, centralized greasing systems, plastic laminated bearings, gears and gear lubricants are covered as high spots.
As regards lubrication maintenance and control, many of factories had started the committees during the wartime or shortly after the war, to control the consumption of petroleum products which had been hard to obtain. However, as the importance and influence of lubrication has'been recognized., the plant managements are reorganizing the committee to a department dealing with maintenance of machines and equipment along with lubrication. In most progressive plant, lubrication problems are handled by Preventive Maintenance Department.
As the cost paid for purchasing lubricants are so small, the managements often overlook the importance of lubrication. The reports of the Lubrication Conference of The Iron and Steel Institute of Japan, carried in 1950 told us that about 30% average of the troubles happend in steel rolling shops are based upon poor lubrication, thus resulting in enormous loss, if considered repair cost and production loss, heat loss and labor cost by mill shutdown.
RECENT DEVELOPMENTS IN REFRACTORIES FOR IRON AND STEEL INDUSTRY
Yosio Kora
pp. 817-822
抄録
Marked advances have been made in refractories for iron and steel industry during the last decade. A brief paper cannot cover all refractories developments in detail, but ten examples of the outstanding develpoments and trends are discussed as follows:
1. One of the most important recent developments in refractories for open hearth furnaces is the increased use of basic bricks. The unburned chemically bonded chrome-magnesia bricks with a steel cover or shield are used widely for front walls, back walls and end walls as a substitute for the silica brick. New roof constructions such as Zebra (black and white) or basic shoulder are also discussed.
2. Development of super-duty silica bricks which are low alumina, low alkali and low porosity, are discussed.
3. Improvements in steel pouring refractories (low porosity or bloating ladles, sleeves, and carbon stoppers) are discussed.
4. Use of fireclay bricks instead of silica bricks for checker works is increasing.
5. Carbon lining for blast furnaces.
6. Developments of manufacturing machinery results in more accurate dimensions and shapes than those in a few years ago.
7. Developments of dolomite refractories.
8. The increasing use of insulating refractories.
9. Use of plastic and castable refractories.
10. Improvment has been made in workability of mortar and cement, and greater control of grain size.
RECENT ADVANCES IN ANALYTICAL CHEMISTRY OF IRON AND STEEL
Takayuki Somiya
pp. 823-830
抄録
The 19th Sectional Committee (Steel) of the Japan Society for the Promotion of Scientific Research was formed in 1935 by Professor Kuniichi Tawara, and the Analysis Sub-Committee of it has been actively engaged in the study of methods of chemical analysis of iron and steel, endevouring to standardizing them. In recent years a great amount of research work on the methods for the determination of gases and non-metallic inclusions in iron and steel, and on the very rapid analytical methods for use on the furnace stage have been undertaken and published in the papers of. the Sub-Committee and the following books: K. Tawara, Tekko Kagaku Bunseki Zensho (Chemical Analysis of Iron and Steel),1951; Japan Society for the Promotion of Scientific Research, Rapid Methods of Chemical Analysis of Iron and Steel,4 th ed.,1955.
Recent development in the following methods is also written: classical methods of chemical analysis, rationalization of analysis, standard methods and specification methods, electrochemical methods, spectrographic methods, metallurgical analysis (metallkundliche Analyse), gas analysis, application of radio-isotopes, and application of statistical methods.
論文アクセスランキング
07 Sep. (Last 30 Days)
-
Perspectives on the Promising Pathways to Zero Carbon Emissions in the Steel Industry toward 2050
ISIJ International Vol.65(2025), No.2
-
溶鋼中での各種酸化物系介在物の成長・除去と凝集
鉄と鋼 Vol.111(2025), No.11
-
Finite Element Analysis of Bubble Growth and Particle Swelling during Coal Pyrolysis
ISIJ International Vol.65(2025), No.9
-
通電誘起高速共晶反応によるAl/Cu異材接合形成につながる界面挙動
溶接学会論文集 Vol.43(2025), No.2
-
Copper removal of liquid steel containing 0.25 % carbon using Fe2O3-CaCl2-SiO2 flux
ISIJ International 早期公開
-
Corrosion Behavior of Carbon Steel under Soil Drying Conditions
ISIJ International 早期公開
-
980 MPa級高張力鋼板の固相抵抗スポット接合
鉄と鋼 早期公開
-
-
-
この機能はログイン後に利用できます。
下のボタンをクリックしてください。