鉄と鋼 Vol. 50 (1964), No. 10
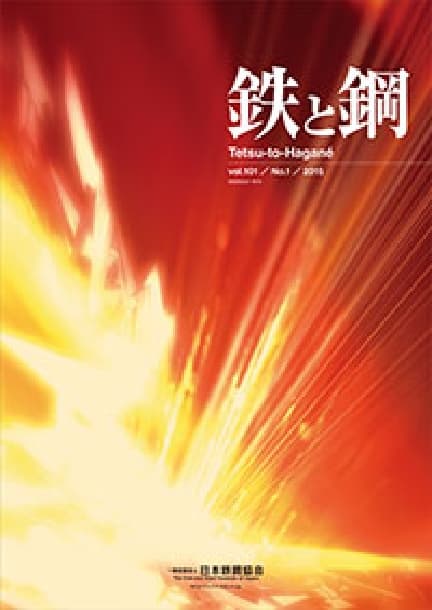
Grid List Abstracts
オンライン版ISSN: | 1883-2954 |
冊子版ISSN: | 0021-1575 |
発行機関: | The Iron and Steel Institute of Japan |
Backnumber
-
Vol. 111 (2025)
-
Vol. 110 (2024)
-
Vol. 109 (2023)
-
Vol. 108 (2022)
-
Vol. 107 (2021)
-
Vol. 106 (2020)
-
Vol. 105 (2019)
-
Vol. 104 (2018)
-
Vol. 103 (2017)
-
Vol. 102 (2016)
-
Vol. 101 (2015)
-
Vol. 100 (2014)
-
Vol. 99 (2013)
-
Vol. 98 (2012)
-
Vol. 97 (2011)
-
Vol. 96 (2010)
-
Vol. 95 (2009)
-
Vol. 94 (2008)
-
Vol. 93 (2007)
-
Vol. 92 (2006)
-
Vol. 91 (2005)
-
Vol. 90 (2004)
-
Vol. 89 (2003)
-
Vol. 88 (2002)
-
Vol. 87 (2001)
-
Vol. 86 (2000)
-
Vol. 85 (1999)
-
Vol. 84 (1998)
-
Vol. 83 (1997)
-
Vol. 82 (1996)
-
Vol. 81 (1995)
-
Vol. 80 (1994)
-
Vol. 79 (1993)
-
Vol. 78 (1992)
-
Vol. 77 (1991)
-
Vol. 76 (1990)
-
Vol. 75 (1989)
-
Vol. 74 (1988)
-
Vol. 73 (1987)
-
Vol. 72 (1986)
-
Vol. 71 (1985)
-
Vol. 70 (1984)
-
Vol. 69 (1983)
-
Vol. 68 (1982)
-
Vol. 67 (1981)
-
Vol. 66 (1980)
-
Vol. 65 (1979)
-
Vol. 64 (1978)
-
Vol. 63 (1977)
-
Vol. 62 (1976)
-
Vol. 61 (1975)
-
Vol. 60 (1974)
-
Vol. 59 (1973)
-
Vol. 58 (1972)
-
Vol. 57 (1971)
-
Vol. 56 (1970)
-
Vol. 55 (1969)
-
Vol. 54 (1968)
-
Vol. 53 (1967)
-
Vol. 52 (1966)
-
Vol. 51 (1965)
-
Vol. 50 (1964)
-
Vol. 49 (1963)
-
Vol. 48 (1962)
-
Vol. 47 (1961)
-
Vol. 46 (1960)
-
Vol. 45 (1959)
-
Vol. 44 (1958)
-
Vol. 43 (1957)
-
Vol. 42 (1956)
-
Vol. 41 (1955)
キーワードランキング
04 Sep. (Last 30 Days)
鉄と鋼 Vol. 50 (1964), No. 10
Mass Transfer in B. O. H. Metal Bath
Hisashi MORI, Midori MATSUO, Takekazu YAMAGUCHI, Masao ITO, Hitoshi YOSHII
pp. 1411-1418
抄録
198 Au sealed in a steel capsule was introduced into the center of metal bath in 130t B. O. H. F. In order to investigate the mass transfer in metal bath, steel samples were taken at 5 doors every 2 minutes after 198 Au addition, and to examine the uniformity between 1st and 2nd ladle, samples were taken from tap gutter during tapping, and from several moulds during teeming of these 2 ladles.
The mass transfer in metal bath seemed to be caused mainly by turbulent diffution and additionally by forced flow with combustion flame.
The time required to get nearly homogeneous 198Au concentration-defined as the time in which mean square deviation of radioactivities at 5 doors from steady value reaches within 10 pct.-was 10 or 17 minutes in the case of boiling, 10 or 14 minutes in reboiling, 21 or 23 minutes in blocking. Furthermore, in the case of blocking, mixing rate was slowed down at 6 and 10 minutes after198. Au and alloy addition: These periods were recognized to correspond with the complete dissolution of alloy from both data on radioactivity and analysis. When 198 Au was introduced in the end of metal bath (just below the burner) during boiling, it did not distribute homogeneously within 30 minutes.
When 198 Au was introduced in the center of bath at 4 to 7 minutes before tap, concentration of 198Au in 2nd ladle was 8 to 45 pct lower than that of 1st ladle in 4 of 5 cases.
On the Distribution of Chromium at Low-Chromium Concentration
Yasushi KOJIMA, Kokichi SANO
pp. 1418-1423
抄録
There have been few researches on the distribution of chromium between an acidic slag saturated with silica and a liquid of iron alloy with low chromium content.According to F. KÖRBER and D. C. HILTY, chromium oxide in the acidic slag changes its chemical form with the change in the concentration of chromium in the liquid iron alloy. The reaction of chromium or the behavior of chromium phase is, therfore, followed by the change in the chromium concentration in liquid phase.
In our latest report over the concentration range of chromium higher than 3 per cent, it was shown that the chromium oxide in the acidic slag behaved like the chromous ion (CrO).
In the present paper, an iron alloy of low chromium concentration is studied. The results are summarized as follows:
1) When the chromium concentration was less than 3%, the oxidation-reduction reaction between chromium and iron in the two phases was represented as 4 (FeO)+3[Cr]→←(Cr3O4) +4 [Fe]
2) The distribution of chromium between two phases and the solubility of oxygen were measured, and from their results the equilibrium constants were determined as follows:
(CrO1.33)slag
_??_
[CrO1.33]metal_??_[Cr]+1.33[O]
K1=(CrO1.33)/[CrO1.33]
K2=[Cr]·[O]1.33/[CrO1.33]
K=(K1/K2)=(CrO1.33)/[Cr]·[O]1.33
log K=6679/T-0.724
Diffusion of Iron and the Rate of Solution of Steel in Liquid Zinc
Susumu MINOWA, Mineo KOSAKA
pp. 1424-1431
抄録
The rates of solution of a still-standing and a rotated steel bar in liquid zinc were measured in the range from 550°C to 600°C. In addition, diffusion coefficients of iron were estimated from this study because no experimental values of diffusion coefficients are available in the existing literatures.
The results obtained are as follows:
(1) Arrhenius relation is satisfied in the relation between the rate of solution and temperature. The activation energy for solution, Ev, is given by Ev=ED+Es+Eη/2 where ED and EηAare the activation energy for diffusion and the viscosity of liquid metal and Es is the heat of solution.
(2) The relation between the rate of solution, V, and the speed of rotation of steel bar, U, is given by V=kU0.64, where k is constant.
(3) On the basis of boundary layer theory, it was found that the dissolution of steel in molten zinc was a liquid diffusion-controlled process.
Continuous Cooling Transformation Characteristics of Some Low Alloy Steels
Tatsuro KUNITAKE, Takayasu OKADA
pp. 1431-1440
抄録
Continuous cooling transformation characteristics have been determined for four grades of steels which are being used as rotor shaft materials. Data on continuous cooling transformation characteristics of these low alloy steels were collected from literatures and were summarized together with the present result.
Critical cooling rates for the formation of pearlite and bainite were obtained respectively for twenty kinds of low alloy steels including four steels in the present paper, and steels were classified according to the critical cooling rate in consideration of actual cooling rates for larger mass.These steels have a so-called bainitic hardenability.Remarkably larger differences in critical cooling rate among steels were observed in the formation of pearlite rather than in the formation of bainite.The prediction of the critical cooling rate for the pearlite formation from the ideal critical diameter calculated by the conventional empirical formula was difficult for these steels with relatively large alloy contents.The effect of Ni on the critical cooling rate for the pearlite formation was remarkable. In mainly bainitic structures, the appearance of bainite was different among steels and this seemed to have a profound influence on hardness.The structural appearance of bainite was significantly dependent on the temperature of formation.Addition of Cr lowered this temperature, resulting in a fine distribution of carbides in bainite.
Uranium Addition to Low-Alloy High-Tension Steels
Masayoshi HASEGAWA, Ichiro ONODA
pp. 1440-1449
抄録
In the previous papers, the authors suggested about the behaviour of Fe2U and UC formed in carbon steels that Fe2U was decomposed by the solution treatment over 950°C and UC was very stable even by the solution treatment at 1200°C.
In this paper, the authors reported the results of investigations into the effect of uranium, addition on three low-alloy high-tension steels, Si-Mn series, Mo-B series and Cr-Ni-Cu series, and into uranium application instead of molybdenum in order to obtain a bainitic structure.
For Si-Mn series, the effect of uranium is almost the same as in the previous papers. Impact resistance at low temperature is reduced by addition of uranium and the transition temperature increases remarkably.The merit of uranium addition to this series is the formation of stable carbide and improvement of corrosion resistance against dilute hydrochloric. acid.
For Mo-B series, no effect is recognized in normalizing at 920°C, but at 1150°C, the bainitic structures of the specimen containing uranium become very fine and have an increased in hardness.The same effect is observed in the hardenability test. This finer microstructure has higher tempering resistance than the standard one, and secondary hardening occursat the tempering temperature of 550-600°C. As compared with the effects of other elements, the effect of uranium is as little as niobium but less than V, W and Ti. It indicates that the solubility of uranium to austenite is improved by the coexistence of molybdenum and uranium precipitates in the carbide reaction of tempering. But insoluble carbide is retained at the previous austenite grain boundary in the steel containing excessive uranium. The bainitic structure is gained in 0.48% uranium steel normalized at 1150°C, but this structure has not so high tempering resistance as that of molybdenum-bearing steels.
For Cr-Ni-Cu series, the effect of uranium is similar to that of molybdenum, but of mecha-nical properties the ductility and impact resistance are reduced by the addition of uranium. Slight secondary hardening based on the precipitaion of uranium appears in this series through the high temperature solution treatment. This is different from the Si-Mn series.
On the High-Chromium High-Cobalt Type Steels for Hot Work Dies
Tomitaka NISHIMURA
pp. 1449-1457
抄録
The fundamental characteristics of 12Cr-7W-0.5V-5Co (DSE) and 12Cr-7W-0.5V-10Co (DSF) type steels for hot work dies have been investigated.The results obtained are as follows:
(1) Transformation temperature on heating, specific gravity, specific heat and coefficient of thermal expansion are measured, and particularly it is noticeable that the coefficients of thermal expansion show small values.
(2) Secondary hardening occurs in the temperature range from 500 to 550°C, and that resistance to tempering softening becomes larger with increasing austenitizing temperature. The temperature range suitable for hardening is from 1050 to 1100°C, so the austenitizing temperature of 1050°C only is used for all tests.
(3) The nose of isothermal transformation curve situates at the temperature of 750°C and 15min for DSE, and 750°C and 25min for DSF.Ms temperature is 205°C for DSE and 175°C for DSF.
(4) At the testing temperature of 600°C, hardness, tensile strength and impact strength are Hv 225, 93 kg/mm2 and 8 kg m/cm2 for DSE, and Hv 270, 107 kg /mm2 and 5 kg m/cm2 for DSF.
(5) The dimensional change of a round bar at the tempering temperature of 600°C is +0.045% for DSE and + 0.040% for DSF in the direction of diameter, and 0% for DSE and -0.010% for DSF in the direction of length.
(6) The tempering at 600°C gives the best impact strength and wear resistance at room temperature.
(7) When both steels are isothermally tempered for 1000 hr at 600, 650 and 700°C, hardness decreases linearly and impact strength slightly with increasing tempering time at each temperature.
And in the process of these temperings, the following sequence of changes in carbides takes place: M6C+M7C3→M6C+M7C3+M23C6→M6C+M23C6→6C+M23C6+Fe2W→M23C6+Fe2W.
(8) Resistance to heat checking is better than that of SKD5 (JIS) steel of 10W-3Cr-0.5V type.
(9) Resistance to oxidation at high temperatures is very excellent as compared with SKD 5 steel.
他の人はこちらも検索
鉄と鋼 Vol.50(1964), No.5
鉄と鋼 Vol.53(1967), No.11
鉄と鋼 Vol.54(1968), No.11
On the Spring Properties of Refractaloy 26 Type Alloy
Kazunori KAMISHOHARA, Yoshiaki KANAI, Fujio SEKI, Michira UCHIYAMA
pp. 1457-1467
抄録
Authors investigated, as part of a study on super alloys for springs, the spring properties at the room temperature or elevated temperature of Refractaloy 26 type alloy, which was treated with various combinations of solution temperature, aging temperature, aging time and cold reduction before or after aging.
Characteristics at the room temperature were determined by tensile, hardness, grain size or bending tests to confirm the spring properties.
Characteristics at the elevated temperature were investigated using coil springs treated with an optimum heat treatment and cold working (to develop the superior room temperature properties). For this object, compression coil springs were manufactured and heated from room temperature, with the temperature and deflection registered.To confirm the stability of deflection under load and heating, coil springs were heated and cooled cyclically.Also the micro-structure and the process of precipitation were observed in representative treatments with the help of electron-microscope.
Results obtained were as follows:
1) Without cold working, a combination of 982°C (solution treatment) and 732°C (aging treatment) develops more favorable mechanical properties in the alloy than other combinations.
2) The cold working (up to 50% reduction) before aging improves the low temperature characteristics, but somehow deteriorates the quality of spring at the elevated temperatures. The higher the cold reduction, and the higher the aging temperature, the shorter is the optimum aging time.
3) The rigidity is influenced by the aging temperature, while the aging time or cold reduction does not affect it noticeably.
4) The proportional limit of twisting is influenced by the temperature and time of aging and also by the cold reduction.
5) Several or more cycles are required to estimate the deflectional stability under repeated heating condition, which is mainly affectedby the load, temperature of heat cycle or treatments given to the spring.
6) Permissible temperature for this alloy is up to about 600°C for one strengthened only by heat treatment, and up to about 500°C for one strengthened by heat treatment and cold working.
Study on the Economical Production Scale at Chiba Works
Ichiro FUJIMOTO
pp. 1491-1502
他の人はこちらも検索
鉄と鋼 Vol.63(1977), No.11
The Status quo and the Future Plan of the Iron and Steel Industry in Italy
Shunta HAYASI
pp. 1503-1508
Study on the Electrolytic Isolation of δ Ferrite from Austenitic Stainless Steel
Tadamichi TAKEI, Haruo SHIMADA
pp. 1509-1511
抄録
The present paper deals with the technique for the electrolytic isolation of δ ferrite iron the 18% Cr, 7% Ni, 1% Cu austenitic stainless steel in relation with the various conditions of electrolysis.The results obtained are as folloues.
(1) The electrolyte, EC1-ethylalcohol, was most suitable for the electrolytic isolation of δ ferrite.Using the electrolyte, HC1-propylalcohol, only a part of δ ferrite existing in this steel could be isolated. However, δ ferrite could not be isolated in the case of using the electrolyte, HC1-methylalcohol
(2)δ ferrite could be most isolated in the case of using the electrolyte consisting of 4 or 5vol (%) HC1, 96 or 95 vol (%) ethylalcohol and 36 gr zinc chloride.The concentration of H Cl being set as low as 3vol (%), S ferrite was contaminated with the matrix metal (γ phase) fallen down during electrolysis.On the other hand, it's concentration being set as much as 10 vol (%), 6 ferrite could not be isolated,
(3)δ ferrite could be more isolated from this steel at the value of pH>0.4 and with platinum cathode instead of mercury cathode.
他の人はこちらも検索
鉄と鋼 Vol.47(1961), No.10
鉄と鋼 Vol.76(1990), No.7
鉄と鋼 Vol.62(1976), No.6
論文アクセスランキング
04 Sep. (Last 30 Days)
-
Perspectives on the Promising Pathways to Zero Carbon Emissions in the Steel Industry toward 2050
ISIJ International Vol.65(2025), No.2
-
溶鋼中での各種酸化物系介在物の成長・除去と凝集
鉄と鋼 Vol.111(2025), No.11
-
Finite Element Analysis of Bubble Growth and Particle Swelling during Coal Pyrolysis
ISIJ International Vol.65(2025), No.9
-
通電誘起高速共晶反応によるAl/Cu異材接合形成につながる界面挙動
溶接学会論文集 Vol.43(2025), No.2
-
Corrosion Behavior of Carbon Steel under Soil Drying Conditions
ISIJ International 早期公開
-
980 MPa級高張力鋼板の固相抵抗スポット接合
鉄と鋼 早期公開
-
-
-
Copper removal of liquid steel containing 0.25 % carbon using Fe2O3-CaCl2-SiO2 flux
ISIJ International 早期公開
-
Evaluation of Feature Selection Methods for Oxygen Supply Prediction in BOF Steelmaking
ISIJ International 早期公開
この機能はログイン後に利用できます。
下のボタンをクリックしてください。