鉄と鋼 Vol. 63 (1977), No. 13
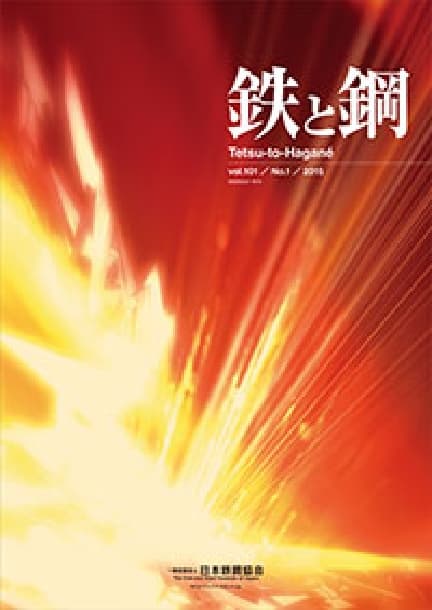
Grid List Abstracts
オンライン版ISSN: | 1883-2954 |
冊子版ISSN: | 0021-1575 |
発行機関: | The Iron and Steel Institute of Japan |
Backnumber
-
Vol. 111 (2025)
-
Vol. 110 (2024)
-
Vol. 109 (2023)
-
Vol. 108 (2022)
-
Vol. 107 (2021)
-
Vol. 106 (2020)
-
Vol. 105 (2019)
-
Vol. 104 (2018)
-
Vol. 103 (2017)
-
Vol. 102 (2016)
-
Vol. 101 (2015)
-
Vol. 100 (2014)
-
Vol. 99 (2013)
-
Vol. 98 (2012)
-
Vol. 97 (2011)
-
Vol. 96 (2010)
-
Vol. 95 (2009)
-
Vol. 94 (2008)
-
Vol. 93 (2007)
-
Vol. 92 (2006)
-
Vol. 91 (2005)
-
Vol. 90 (2004)
-
Vol. 89 (2003)
-
Vol. 88 (2002)
-
Vol. 87 (2001)
-
Vol. 86 (2000)
-
Vol. 85 (1999)
-
Vol. 84 (1998)
-
Vol. 83 (1997)
-
Vol. 82 (1996)
-
Vol. 81 (1995)
-
Vol. 80 (1994)
-
Vol. 79 (1993)
-
Vol. 78 (1992)
-
Vol. 77 (1991)
-
Vol. 76 (1990)
-
Vol. 75 (1989)
-
Vol. 74 (1988)
-
Vol. 73 (1987)
-
Vol. 72 (1986)
-
Vol. 71 (1985)
-
Vol. 70 (1984)
-
Vol. 69 (1983)
-
Vol. 68 (1982)
-
Vol. 67 (1981)
-
Vol. 66 (1980)
-
Vol. 65 (1979)
-
Vol. 64 (1978)
-
Vol. 63 (1977)
-
Vol. 62 (1976)
-
Vol. 61 (1975)
-
Vol. 60 (1974)
-
Vol. 59 (1973)
-
Vol. 58 (1972)
-
Vol. 57 (1971)
-
Vol. 56 (1970)
-
Vol. 55 (1969)
-
Vol. 54 (1968)
-
Vol. 53 (1967)
-
Vol. 52 (1966)
-
Vol. 51 (1965)
-
Vol. 50 (1964)
-
Vol. 49 (1963)
-
Vol. 48 (1962)
-
Vol. 47 (1961)
-
Vol. 46 (1960)
-
Vol. 45 (1959)
-
Vol. 44 (1958)
-
Vol. 43 (1957)
-
Vol. 42 (1956)
-
Vol. 41 (1955)
キーワードランキング
04 Sep. (Last 30 Days)
鉄と鋼 Vol. 63 (1977), No. 13
On the Recent Progress of the RH- and DH- Vacuum Degassing process of Molten Steel
Hisashi MATSUNAGA, Tadao TOMINAGA, Mutsumi OHJI, Fusao TANAKA
pp. 1945-1952
Recent Progress of AOD Process
Yoshio SAWAMURA
pp. 1953-1964
他の人はこちらも検索
鉄と鋼 Vol.69(1983), No.7
材料と環境 Vol.44(1995), No.1
ISIJ International Vol.60(2020), No.6
Advanced Techniques of Alloying Elemnents into Molten Steel in the Ladle
Takaho KAWAWA, Ryoichiro IMAI
pp. 1965-1974
Progress in Electroslag Remelting Process
Kiichi NARITA
pp. 1996-2009
他の人はこちらも検索
鉄と鋼 Vol.61(1975), No.8
鉄と鋼 Vol.63(1977), No.10
鉄と鋼 Vol.63(1977), No.10
Several Melting and Refining Processes with the Special Heat Source such as Electron-beam, PIasma-arc etc
Taro SUGIYAMA, Kiyoo ONO
pp. 2010-2027
Some Applications of Tap Degassing Process
Masayoshi OKAMURA, Hiroyuki NAGATA, Masatoshi MIURA, Takayasu NIIMI, Akira SUZUKI
pp. 2028-2033
抄録
Behaviour of hydrogen, oxygen, and nitrogen in tap degassing process is studied and the efficiency of the process is found equivalent to the other processes. The degassing steps are divided into two parts. That is, the first is the birth and fall of droplets and the second is the degassing through the free surface of molten bath. The violent motion of the droplet at the first stage is very important. The applications to the desulphurization treatment, Al addition technique and the production of low carbon stainless steel, are also discussed.
他の人はこちらも検索
鉄と鋼 Vol.63(1977), No.5
鉄と鋼 Vol.62(1976), No.10
鉄と鋼 Vol.63(1977), No.8
On Several Slag-Metal Reactions and Refining Abilities of the Ladle Furnace
Kazushige UMEZAWA, Hiroyuki KAJIOKA
pp. 2034-2042
抄録
Several Slag-metal reactions and refining abilities of the ladle furnace (LF PROCESS) have beenstudied.
The results obtained from these studies are as follows:
(1) Desulfurization is dependent of slag basicity, reducing degree of slag and agitation of melt. (2) The numerical value of sulfur distribution coefficient is above a hundred. (3) Deoxidation is dependent on aluminium content of metal, slag basicity, agitation of melt and lining refractory. (4) Total oxygen content after treatment is below 20ppm in the case of Al-Si killed steel, below 35ppm in the case of Si-Mn killed steel. (5) Hydrogen absorption is caused by flux, so hydrogen content is dependent on drying degree of flux. (6) Nitrogen content is controlable in the required range from 20ppm to 80ppm by the way of alloy addition at tapping from BOF.
他の人はこちらも検索
鉄と鋼 Vol.63(1977), No.5
鉄と鋼 Vol.62(1976), No.10
鉄と鋼 Vol.63(1977), No.10
Production of High Grade Steel by Ladle Refining Furnace
Kanji EMOTO, Takemi YAMAMOTO, Yoshiharu IIDA, Hiroshi OHI, Takesaburo NISHIOKA
pp. 2043-2053
抄録
Since April 1970, a ladle refining furnace (ASEA-SKF process) with 100t capacity has been operating at Mizushima Works of Kawasaki Steel Corp.
Through the LD-LRF procegs, i. e., a combined proccss of a 180t LD converter with ladle refining furnace, high quality steels for forgings and extra heavy plates have been produced successfully instead of using the conventional electric arc furnace-degassing process.
This plant can treat mother metal from 100t (half heat of LD converter) to 30t (electric arc furnace).
The typical operational pattern of this process consists of the carbon dioxidation at degassing period and the sequent aluminium deoxidation with effective induction stirring. The hydrogen content is effectively reduced at the rimmed or semi-killed state.
All this paper, some operational results, especially the deoxidation behavior during induction stirring and hydrogen removal technique are reported.
他の人はこちらも検索
鉄と鋼 Vol.63(1977), No.5
鉄と鋼 Vol.62(1976), No.10
鉄と鋼 Vol.63(1977), No.8
Treatment of Liquid Steel in the Ladle (Ladle Technology)
Yoichi UMEDA, Katsukiyo MARUKAWA, Yoshiyashu SHIROTA
pp. 2054-2063
抄録
Functions of various ladle technologies were studied, and some future prospects of the ladle technology in steelmaking process were proposed.
i) Ladle technologies proposed so far can be classified to five types.
ii) Eight functions are necessary for the ladle technology and evaluations of the eight functions of each technology were done.
iii) Many factors, for example, grade of steel, layout of the plant, and forecast of energy cost, must be investigated in order to introduce the most suitable process of the ladle technoloty into steelmaking process.
iv) The ladle technology has been developed from needs for improvements of steel quality and productivity. In future, however, developments of the ladle technology will be strongly influenced by needs for saving resources and energy, and for decreasing waste materials.
v) In future, with these developments of the ladle technology, innovations of refining process in steelmaking will be extensively performed.
他の人はこちらも検索
鉄と鋼 Vol.63(1977), No.5
鉄と鋼 Vol.63(1977), No.9
鉄と鋼 Vol.63(1977), No.8
Development of a New Stainless Steel Melting and Refining Process (LD-RH Oxygen Blowing Process)
Norimasa KAMII, Shizuo OKUBO, Bunji ETO
pp. 2064-2069
抄録
Muroran Works, Nippon Steel Corporation, started the researches to produce stainless steel by LD converter in 1965.
After various difficulties were encountered and overcome in the course of these researches a new process to melt and refine stainless steel (LD-RHOB process) was successfully developed.
Since 1972 all the stainless steels have been produced favorably by the LD-RHOB process, and the products were more than 90000t in 1976.
The LD-RHOB process consists of the following five steps.
(1) Desulphurization treatment
: Desulphurization of hot metal by KR treatment.
(2) Base metal refining period
: Dephosphrization in LD converter.
(3) Separation of slag from metal
: Tapping and slagging off and then charging into the LD converter again.
(4) Chromium melting period
: High carbon ferro-chromium melting into base metal.
(5) RHOB treatment
: Decarburization under reduced pressure.
The special features of LD-RHOB process include the following:
(1) Chromium yield and productivity are better than of the same as other processes (AOD, VOD process).
(2) Chemical composition can be freely controlled and tramp elements are lower than those in electric furnace steels. It is remarkable that high pure stainless steels such as ultra low carbon nitrogen stainless steels can be easily produced.
(3) The products are very soft and ensure good workability.
他の人はこちらも検索
鉄と鋼 Vol.63(1977), No.5
鉄と鋼 Vol.62(1976), No.10
鉄と鋼 Vol.63(1977), No.8
On the Operations of LD-VAD Process and Product Qualities
Takaharu MORIYA, Masanori TAWARA
pp. 2070-2076
抄録
VAD (Vacuum Arc Degassing) plant is characterized by 3-phase AC are heating under reduced pressure while Ar gas is injucted by a porous plug set at the bottom of ladle. Thus alloying, desulphurizing, oxygen reduction and dehydrogenation can be made easily and sufficiently. For instance, the sulphur concentration can be easily achieved to less than 0.005%, the oxygen level of the slab of low alloy steels ranges between 10 and 35 ppm, and, the hydrogen in the molten steel after degassing is 1.5 ppm on an average.
At Kure Works, high grade carbon steels and low alloy steels, such as structural steels, tool steels and bearing steels, and extra low carbon steels (carbon concentration is less than 0.005%) are produced economically by this plant from the molten steel of LD converters. This paper describes the techniques procedure for manufacturing these steels by this LD-VAD process.
他の人はこちらも検索
鉄と鋼 Vol.63(1977), No.5
鉄と鋼 Vol.62(1976), No.10
鉄と鋼 Vol.63(1977), No.8
On the Refining Condition of Extremely Low Carbon and Nitrogen Stainless Steel in VOD Process
Hiroyuki KATAYAMA, Hiroyuki KAJIOKA, Makoto INATOMI, Fusao TANAKA, Hideto HOSODA
pp. 2077-2086
抄録
VOD process has been improved for the production of super ferritic stainless steel which is characteristic in ultra low carbon and nitrogen contents.
(1) According to the data of 60t VOD, the obtained carbon content is influenced not only by well known factors, Cr% and temperature of molten steel, but also by the bubbling condition and oxygen blowing pattern.
(2) It is observed in an experiment in 10kg VIF that decarburization in low carbon range proceeds mainly by a reaction between oxide which is formed by oxygen blowing and carbon in molten steel. If agglomeration of oxide is prevented by an appropriate bubbling and oxygen blowing pattern, the course of decarburization is expressed as a first-order reaction until ultra low carbon range.
(3) The obtained nitrogen content is affected by air leakage into the vacuum vessel and the rate of decarburization. When air leakage is much, nitrogen content increases in low carbon range.
(4) For the production of ultra low carbon and nitrogen stainless steel, it is necessary to pay attention to the pattern of molten steel temperature, bubbling condition, and prevention of air leakage.
他の人はこちらも検索
鉄と鋼 Vol.63(1977), No.8
鉄と鋼 Vol.62(1976), No.10
鉄と鋼 Vol.63(1977), No.13
Synthetic Slag Refining of 18Cr Steel in VOD
Morihiro HASEGAWA, Shigeaki MARUHASHI
pp. 2087-2093
抄録
Operation results of refining the stainless steel melt with synthetic slag in combination with vacuum treatment in VOD are presented, The final oxygen content decreased to lower level than that obtained with simple vacuum treatment, and was lowered by increasing slag basicity. depending on carbon content. The metallurgical facter that played the most important role in lowering oxygen level was the increased power of Si deoxidation that was resulted from the reduced silica activity in slag phase. The amount of extracted oxide inclusion was lowered by the synthetic slag refining in vacuum. As a result the surface quality of the sheet was fairly improved.
他の人はこちらも検索
ISIJ International Vol.39(1999), No.5
鉄と鋼 Vol.63(1977), No.13
鉄と鋼 Vol.73(1987), No.11
Reaction Model for the AOD Process
Takamasa OHNO, Toshiaki NISHIDA
pp. 2094-2099
抄録
A reaction model has been developed for the AOD process that predicts the ratc of decarburization during stainless steel making. The reaction model is based on the assumptions that the injeetd oxygen primarily oxidizes chromium in the tuyere zone and that chromium oxide subsequently oxidizes the carbon as it rises in the bath with the argon bubbles. It is assumed that the rate of decarburization is controlled by the liquidphase mass transfer of carbon to the bubble surface. The model has been ex tended to other operating condition such as different O2/Ar ratios, bath depth and so on.
The Decarburization Mechanism for Stainless Steel Melt by Ar-O2 Ascending Gas Bubble
Yoshio KOBAYASHI, Shigeaki MARUHASHI
pp. 2100-2109
抄録
The decarburization mechanism for stainless steel melt by Ar-O2 ascending gas bubbles was studied under atmospheric and reduced pressures in a laboratory-scale induction furnace. Experimental results are summarized as follows:
(1) The rate of decarburization is divided into two stages. In the first stage the rate is constant, being independent of the carbon content, and in the second stage it gradually decreases with the lowering of the carbon content in the bath.
(2) In this experiment, the critical carbon content at 1600°C is higher than the C-Cr equilibrium point that is determined by the Pco, and the cridcal carbon content at 1700°C is slightly higher than the carbon content at which the rate controlling step varies from the gas phase control into the carbon diffusion control at the gas bubble-metal interface.
(3) Regarding chromium yield the submersion depth is a very important factor for reduction of chromium oxide which is formed by Ar-O2 gas bubbling. The temperature of the melt and Ar/O2 ratio are also important opperational factors for effective decarburizing without an excessive chromium loss.
(4) Ar-O2 gas bubbling under reduced pressure is a very effective method for decarburizing to extra low carbon content (C<0.004%) without an excessive chromium loss.
Development of Alloy Bullets Shooting Method into Molten Steel in Ladle
Shigeru TAMAMOTO, Kantaro SASAKI, Hajime NASHIWA, Hiroshi SUGITA, Akiyoshi MORI
pp. 2110-2125
抄録
The bullets shooting method has been developed as one of the alloy adding technologies into ladle.
The charactristic of this method is that it is very effective for adding the elements whose properties are distinctive in terms of high vapour pressure, low specific weight, and high affinity with oxygen.
By utilizing this method, several effects have been obtained.
These are as follows.
1) The shooting method of aluminium gives a much higher aluminium yield of addtion compared with the conventional method, and the amount of aluminium addtion becomes 80% of that in the convetional method for killed steel. In addition to this effect the scatter in soluble aluminium content in products has been reduced to about 1/3 and the steel quality has been improved.
2) SCAT is a comprehensive system of calcium adding technique by utilizing the shooting method, and gives a high and stable yield of calcium. By adopting SCAT the shape and distribution of inclusions in steel are altered, and this results in the improvement of mechanical properties such as low temperature thoughness, elongation and notch impact toughness in T and Z directions, and toughness in welded zone.
3) It has become possible to control baron content in steel precisely by utilizing the shooting method combined with other technical developments, and thereby to obtain the tergetted mechanical properties.
Further development in ladle treatments is expected and especially the bullets shooting method will take a significant part in this area.
Outline of 25t Vacuum Refining Furnace
Teiichi SUZUMOTO, Toru TAKAHASHI, Kazuo KARASHIMA, Sigenori KAWAI
pp. 2126-2133
抄録
A vacuum induction melting process is one of the most useful process for high-grade special steel production.
Yasugi Works of Hitachi Metals Ltd. have installed 25t ‘Vacuum Refining Furnace’, which is a type of vacuum induction furnace possible to charge a vacuum vessel with molten metal. This facility is effective for quality-improvement of tool steels, super alloys and others.
The facility has been operated satisfactorily since May, 1970 and showed excellent results in high-grade tool steels, super alloys, ultra low carbon stainless steels and other products. This paper is described the outline of the system and the operation on the 25t ‘Vacuum Refining Furnace’.
A Study of Melting Process for 20% Mo-Ni Alloy in Vacuum Induction Furnace
Hiroshi YAMANISHI, Eijiro ISHIKAWA
pp. 2134-2140
抄録
For the purpose of improving the hot workability of 20% Mo-Ni alloy, the melting pattern was established by studying several important parameters.
The results are summarized as follows:
(1) Deoxidation rate reached up to approximately 80% before melt down. Keeping the molten bath for long times under vacuum deteriorated the hot workability. Therefore, the quick melting pattern should be applied after melt down.
(2) There was a clear relationship between the CO reaction rate (RCO=CM/CCO×100%) during melting process and the hot workability. This shows that the CO reaction rate can be applied as one of the important parameters during melting.
(3) The necessary amount of carbon to get the higher deoxidation before melt down could be calculated and-the Co reaction rate could be higher.
By these results, we could conduct an ideal melting pattern to get a good deoxidation rate and hot workability.
Density, Surface Tension and Electrical Conductivity of Calcium Fluoride Based Fluxes for Electroslag Remelting
Kazumi OGINO, Shigeta HARA
pp. 2141-2151
抄録
The density, surface tension and electrical conductivity of calcium fluoride bearingfluxes and interfacial tension between iron alloys and those fluxes were measured at molten state.
From the results, especially from the change of molar volume, the behaviour of alumina and lime added to molten calcium fluoride is discussed and the dissociation mechanism of aluminate by fluorine is proposed as follows; fiuorine added to CaO-Al2O3 melt, firstly, changes the (O-……Ca2+……O-) bond to the (O-…Ca2+……F-) bond and when the process is completed, the fluorine begins to attack the aluminate complex and changes gradually aluminate complex to the smallest aluminium-oxyfluouride such as AlO2F2-or AlOF2-.
Temperature Distributions in the Slag and Metal Pools in a Laboratory-scale ESR Furnace
Yukio OGUTI, Yujiro TANBE, Saburo MIYAMA, Akio EJIMA
pp. 2152-2161
抄録
Temperature distributions in the slag and metal pools during electroslag remelting have been measured using BN sheathed thermocouples imerted through the mould wall.
The main results are as follows:
(1) The slag temperature varies from 1700 to 1950°C, depending on the applied voltage. (2) The average temperature of slag bulk is fairly uniform with lower applied voltages. (3) The temperature in the metal pool is 1500-1550°C independent on melting conditions. (4) The melting rate is controlled by the slag temperature as well as the heat transfer to the electrode. (5) The heat input from the metal pool to the solidification front is larger by two times or more than the generation of the latent heat of solidification. (6) On the basis of thermodynamics it is suggested that chemical reactions such as the reduction of Al2O3 do not take place at the slag-metal pool interface.
Profiles of Temperature, Voltage and Local Heat Generation in Slag Phase and Metal Pool of ESR Unit under Operation
Masahiro KAWAKAMI, Kazuhiro NAGATA, Minoru YAMAMURA, Naoki SAKATA, Yoshio MIYASHITA, Kazuhiro GOTO
pp. 2162-2171
抄録
Local temperature and voltage in the molten flux and metal pool beneath the electrode of ESR porcesses were measured directly by a bare hot junction of W-WRe thermocouple.
The temperature in the flux during remelting was almost uniform at 1750±30°C. No temperature gradient was found at the metal pool-flux interface. The temperature in the metal pool decreased smoothly downward in the pool with a platea at 1500°C which was the liquidus temperature of the steel used.
The iso-voltage line was densely distributed at the electrode-flux interface and broadened toward the metal pool-flux interface. Most of the “Joule heat” in the flux was generated very close to the electrode. However, Faradaic heat generation at the electrode-flux interface was hardly found.
It is suggested from the experimental results that refining processes, not only slag-metal reaction but also inclusion removal take place mainly at the metal pool-flux interface. Because the temperature in the flux was uniform even with the localized heat generation, a violent convection should exist in the flux.
One of the driving forces for the convertion, the pinch effect of the current, was calculated. The selection of the proper voltage and current in order to have a good shape of the metal pool was suggested on an I-V diagram.
Removal of Phosphorus from Liquid Iron-Alloys with Ca-CaF2 Melt
Naoki TOKUMITSU, Kazu-umi HARASHIMA, Yasushi NAKAMURA
pp. 2172-2180
抄録
ESR experiments were made to study the dephosphorization of S45C, SUS304, and 25% Cr steels with Ca-CaF2melt used as an electroflux. The reaction was found to occur mainly at the electrode-tip/Ca-CaF2melt interface. The distribution of P between the liquid steel and the Ca solution was determined only by the Ca content of CaF2 melt, irrespective of the remelting rate, the flux weight, and the P content of electrode studied. For SUS304 and 25% Cr steels the distribution ratio was given as follows:
(%P) / [%P] =4 (%Ca) (%Ca) 2
For S45C steel the ratio appeared to be larger than that expected from the above equation. The experimental results indicate that the dephosphorization reaction is nearly completed during the remelting process.
The observed dependence of the distribution ratio on the Ca content was proved to be consistent with a model for Ca-CaF2 solution in which an equilibrium for the reaction, 2Ca+++2e=Ca2++, is assumed.
他の人はこちらも検索
鉄と鋼 Vol.63(1977), No.10
鉄と鋼 Vol.63(1977), No.10
鉄と鋼 Vol.63(1977), No.11
Some Important Factors Affecting Hydrogen Pick-up and Oxidation during ESR Treatment
Akira MASUI, Yasutoshi SASAJIMA, Naoki SAKATA, Minoru YAMAMURA
pp. 2181-2190
抄録
ESR experiment was made by a test furnace (600kVA) in order to investigate the hydrogen pick-up and oxidation of Al, Si, and Mn during ESR tereatment.
From the studies on the behaviour of hydrogen during ESR treatment, it has been found that the partial pressure of water vapor in the atmosphere, gas/slag interface area, slag composition, electrode hydrogen content, remelting rate, and slag quantity are the factors that control the hydrogen content in ESR ingot.
Based on these test results, and on the assumption that the transfer rate of (OH-) through the gas/slag interface controls the hydrogen pick-up velocity, a mathematical model was made for the behaviour of hydrogen during ESR treatment. The physical and chemical constants used in this model were discussed.
From the experiments on oxidation of metal, it was found that SiO2 content in slag played a very important role for the oxidation of metal and that Si, Al and Mn contents in metal were in an apparent equilibrium with slag compositions. By using these test results, a mathematical model for the oxidation of metal during ESR treatment was made and discussed.
On the Oxygen Transfer during Direct Current Electroslag Remelting of Carbon Steel
Yasushi KOJIMA, Makoto KATO, Shoichi NOMURA, Michio INOUYE
pp. 2191-2197
抄録
In order to study the mechanism of oxygen transfer during electro-slag remelting, carbon steel (S 48 C) was remelted in CaF2-Al2O3 slag using a small scale ESR unit of direct current under the open atmosphere.
It was confirmed that those ingots remelted with an electrode of negative polarity give higher oxygen content than those with positive. Those differences of oxygen behavior would be resulted from the differences of the current density and of the inter facial area between the metal and slag. The oxygen content in those ingots remelted in large scale ESR furnace could be estimated from the present results on the oxygen transfer through the molten metal/ slag interface, on the assumption that the mass transfer coefficient of oxygen depends on the current density of the interface.
他の人はこちらも検索
鉄と鋼 Vol.61(1975), No.8
鉄と鋼 Vol.64(1978), No.2
鉄と鋼 Vol.64(1978), No.10
On the Behavior of Active Elements during Electroslag Remelting Process of Ni-base Alloy
Shigeki SAWA, Shohgo SHIBUYA, Shigeru KINBARA
pp. 2198-2207
抄録
Behavior of such active elements as magnesium, aluminum and silicon during electroslag remelting process of a nickel-base alloy has been studied in a small scale ESR unit.
CaF2-base Mg++ bearing slags of two or three components; CaF2-MgO, CaF2-MgF2, CaF2-MgO-Al2O3, CaF2-MgF2-Al2O3, CaF2-MgO-AlF3, CaF2-MgO-CaO were compared with conventional CaF2 monoand CaF2-Al2O3 binary slags.
Several hundred ppm of magnesium was found in the ESR ingots remelted under slags containing suitable amount of Mg++ and low CaO and Al2O3, although none of magnesium but aluminum or silicon was added to the original electrodes.
It was shown that the distribution ratio of magnesium between slag and metal was related to the concentration of Al+++ in the slag, oxygen and aluminum in the metal.
Refining and Qualty of Slabs and Heavy Plates Produced by 40t Electro-Slag-Remelting Process
Yutaka HIROSE, Kazuo OKOHIRA, Takaharu SHIMIZU, Nobuo SATO, Masazumi HIRAI, Minoru NISHIWAKI
pp. 2208-2223
抄録
Our experience and study on the refining and solidification in a 40t slab ESR process at Yawata Works and the properties of the rolled heavy plates are reported in this paper.
Inclusions in the ESR ingot are quite small and few. Desulphurization to gaseous phase plays an important role in the total desulphurization of ESR. The deoxidation is discussed form the viewpoint of Al-O equilibrium. In order to obtain hydrogen contents lower than 1 ppm, the control of atmosphere and the use of recycled slag are necessary.
The secondary mist cooling practice has been developed for the prevention of ghost lines in large ESR ingots.
Heavy plates rolled from the ESR ingot show excellent ductility and impact properties to convetional materials.
A high reliability in material properties is secured by the application of ESR process.
Plasma-Arc Remelting of Steels and Superalloys
Tatsuo FUJIWARA, Koshi KATO, Kiyoo ONO, Hiroyuki YAMADA
pp. 2224-2235
抄録
The feature of plasma-arc remelting and the quality of plasma-arc remelted steels and superalloys were investigated by using an originally designed and constructed PPC (Plasma Progressive Casting) furnace with a 110mm dia. water-cooled copper mould and a maximum 150kW power source.
The results obtained are as follows:
1) It was possible to some extent, to control the solidification structure of the PPC ingot. By selec ting a relatively slow melting rate against a given plasma power, the metal pool became very shallow and flat, so that columnar crystals grew nearly vertical.
2) The hot workability, based on the Gleeble test, of a solidification controlled PPC ingot, which had verlcal columnar crystals, was superior to that of VAR ingot.
3) No chemical composition change including for Ti, Al, Mn etc. was observed, and deoxidization could be done in the PPC process. As the deoxidizing mechanism, the C-O reaction and the removal of the Al2O3 type oxide inclusions were considered.
4) The ingot surface was comparable to that of ESR ingot, though some differences were observed between the steel grades.
5) The distribution of alloy elements in a PPC ingot and the mechanical properties of the ingot were almost the same as those of the VAR ingot.
他の人はこちらも検索
鉄と鋼 Vol.63(1977), No.10
鉄と鋼 Vol.63(1977), No.10
鉄と鋼 Vol.63(1977), No.11
Plasma Induction Melting of High Nickel Alloys
Tatsuo FUJIWARA, Saburo SUGIURA
pp. 2236-2245
抄録
The plasma arc melting process had been researched and developed in Daido Steel Co., Ltd. since 1963 and a 0.5t plasma induction furnace (PIF) of nearly industrial scale was installed in Central Research Laboratory of Daido Steel Co., Ltd. in spring, 1969.
In this report, the refining characteristics of this furnace are described when low alloy steels, stainless steels, Ni-base magnetic alloys and high Mn electronics alloy are melted.
The effectiveness of this furnace was confirmed from the view-point of both quality and cost, especially in case of Ni-base magnetic alloys.
The reasons are:
1) Return scrap can be used without great operational difficulties.
2) Decarburization down to 0.01% C is easy and so is other composition controls.
3) Sulfur which is harmful for hot workability and oxygen which makes magnetic properties deteriorated can be removed very easily if a flux is used in argon atmosphere.
他の人はこちらも検索
鉄と鋼 Vol.63(1977), No.10
鉄と鋼 Vol.63(1977), No.10
鉄と鋼 Vol.63(1977), No.11
Behaviours of Impurities in SUS 304 and NCF-1 Alloys during Continuous Electron-Beam Melting
Yasushi NAKAMURA, Tatsuo MUKAI, Masatoshi KUWABARA, Kazuhiko ARIHARA
pp. 2246-2253
抄録
The purpose of this work is to present experimental results of impurity elimination during electron-beam melting (EBM) of SUS 304 and NCF-1 alloys. A continuous drip-type EBM furnace of 30kW max. Power and water cooled copper mold of 55mm in inner diameter were used. SUS 304 alloy was twice melted at a given melting rate, while NCF-1 alloy was melted for once. Concentration changes of elements in the alloys were summarized as follows:
Remarkably decreased: Sb, O, Mn for SUS 304, and Pb. Bi, O, Mn for NCF-1.
Decreased: Cu, Zn, N, Cr, for SUS 304, and Cu, Sb, N, Cr for NCF-1.
Slightly decreased: As, Pb, (Sn, S) for SUS 304, and Sn, S for NCF-1.
Unchanged or increased: Si, P, Al, Ni, C.B, for SUS 304 and As, C, Si, P, Ni, Fe for NCF-1.
NCF-1 alloy was also melted by VAR, ESR, MSR, and PAM by using laboratory-scale furnaces. Removal degree of impurities during these melting processes were compared with that of EBM as to certify the superiority of EBM for the impurity removal.
An Intermediate Reports on Activities of Committee on Special Refining Techniques of Steels of the Joint Society on Iron and Steel Basic Research
Kazuhiro GOTO
pp. 2254-2264
論文アクセスランキング
04 Sep. (Last 30 Days)
-
Perspectives on the Promising Pathways to Zero Carbon Emissions in the Steel Industry toward 2050
ISIJ International Vol.65(2025), No.2
-
溶鋼中での各種酸化物系介在物の成長・除去と凝集
鉄と鋼 Vol.111(2025), No.11
-
Finite Element Analysis of Bubble Growth and Particle Swelling during Coal Pyrolysis
ISIJ International Vol.65(2025), No.9
-
通電誘起高速共晶反応によるAl/Cu異材接合形成につながる界面挙動
溶接学会論文集 Vol.43(2025), No.2
-
Corrosion Behavior of Carbon Steel under Soil Drying Conditions
ISIJ International 早期公開
-
980 MPa級高張力鋼板の固相抵抗スポット接合
鉄と鋼 早期公開
-
-
-
Copper removal of liquid steel containing 0.25 % carbon using Fe2O3-CaCl2-SiO2 flux
ISIJ International 早期公開
-
Evaluation of Feature Selection Methods for Oxygen Supply Prediction in BOF Steelmaking
ISIJ International 早期公開
この機能はログイン後に利用できます。
下のボタンをクリックしてください。