鉄と鋼 Vol. 62 (1976), No. 5
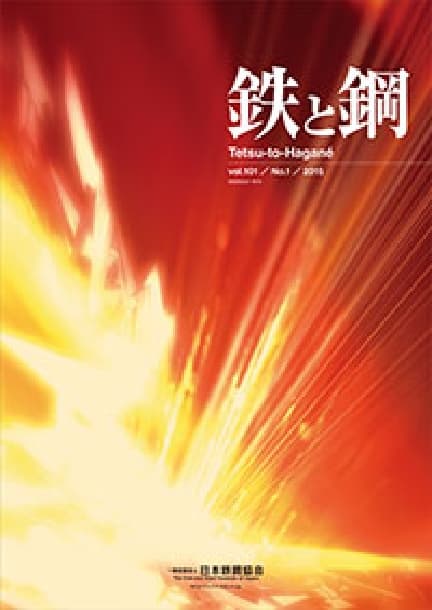
Grid List Abstracts
オンライン版ISSN: | 1883-2954 |
冊子版ISSN: | 0021-1575 |
発行機関: | The Iron and Steel Institute of Japan |
Backnumber
-
Vol. 111 (2025)
-
Vol. 110 (2024)
-
Vol. 109 (2023)
-
Vol. 108 (2022)
-
Vol. 107 (2021)
-
Vol. 106 (2020)
-
Vol. 105 (2019)
-
Vol. 104 (2018)
-
Vol. 103 (2017)
-
Vol. 102 (2016)
-
Vol. 101 (2015)
-
Vol. 100 (2014)
-
Vol. 99 (2013)
-
Vol. 98 (2012)
-
Vol. 97 (2011)
-
Vol. 96 (2010)
-
Vol. 95 (2009)
-
Vol. 94 (2008)
-
Vol. 93 (2007)
-
Vol. 92 (2006)
-
Vol. 91 (2005)
-
Vol. 90 (2004)
-
Vol. 89 (2003)
-
Vol. 88 (2002)
-
Vol. 87 (2001)
-
Vol. 86 (2000)
-
Vol. 85 (1999)
-
Vol. 84 (1998)
-
Vol. 83 (1997)
-
Vol. 82 (1996)
-
Vol. 81 (1995)
-
Vol. 80 (1994)
-
Vol. 79 (1993)
-
Vol. 78 (1992)
-
Vol. 77 (1991)
-
Vol. 76 (1990)
-
Vol. 75 (1989)
-
Vol. 74 (1988)
-
Vol. 73 (1987)
-
Vol. 72 (1986)
-
Vol. 71 (1985)
-
Vol. 70 (1984)
-
Vol. 69 (1983)
-
Vol. 68 (1982)
-
Vol. 67 (1981)
-
Vol. 66 (1980)
-
Vol. 65 (1979)
-
Vol. 64 (1978)
-
Vol. 63 (1977)
-
Vol. 62 (1976)
-
Vol. 61 (1975)
-
Vol. 60 (1974)
-
Vol. 59 (1973)
-
Vol. 58 (1972)
-
Vol. 57 (1971)
-
Vol. 56 (1970)
-
Vol. 55 (1969)
-
Vol. 54 (1968)
-
Vol. 53 (1967)
-
Vol. 52 (1966)
-
Vol. 51 (1965)
-
Vol. 50 (1964)
-
Vol. 49 (1963)
-
Vol. 48 (1962)
-
Vol. 47 (1961)
-
Vol. 46 (1960)
-
Vol. 45 (1959)
-
Vol. 44 (1958)
-
Vol. 43 (1957)
-
Vol. 42 (1956)
-
Vol. 41 (1955)
キーワードランキング
28 Jul. (Last 30 Days)
鉄と鋼 Vol. 62 (1976), No. 5
Theoretical Analysis of Gas Flow in Shaft with Layered Burdens
Mamoru KUWABARA, Iwao MUCHI
pp. 463-471
抄録
To clarify the characteristics of gas flow in the blast furnace shaft with layered ore and coke burdens, the flow equations of continuity and motion were numerically solved for the isothermal flow in two-dimensional bed.
The effects of mass flow rate of gas, compressibility of fluid, shape of bed and non-uniform distribution of permeability on the flow field such as patterns of streamline, mass velocity and isobar in the bed are discussed on the basis of the results calculated for gas fed into the bed at isobaric condition.
Investigation of Reactions and Alkali Circulation in the Blast Furnace Stack by the Use of Vertical Probes
Hiroshi ITAYA, Tsuyoshi FUKUTAKE, Kyoji OKABE, Tamotsu NAGAI
pp. 472-482
抄録
The vertical distribution of gas compositions, temperature, and pressure in the blast furnace stack, and also dust in shaft gas were investigated by the use of vertical probes. Furthermore, the water vapor content was determined by the dew point measurement.
Following results were obtained.
(1) Water gas shift reaction was in equilibrium in the temperature region higher than 800°C.
(2) The rate of indirect reduction of iron oxide showed a maximum between 1000 and 1050°C andthen decreased with formation of the shell of iron reduced.
(3) The rate of solution-loss reaction was controlled by the rate of indirect reduction of iron oxide in the temperature range higher than 900°C. The rate of solution-loss reaction RZS was expressed as follows. RZS (kg mol c/m3 bed. hr) =kS (PH2O+PCO2) ρc (%C/100) · (1/Mc)
kS (1/hr) =5.4×1011 exp (-67000/RT)
(4) Measured concentration of water vapor differed from that of calculated on the basis of mass-balance. The difference corresponded to the hydrogen content of heavy oil injected.
(5) Vapor pressure of potassium was estimated at 8.2×10-4 atm in the temperature range from 1000 to 1200°C and 3.7×10-4 in the range from 900 to 1000°C.
Change of Conditions in the High-Temparature Region Caused by the Variation of Heat Level
Mitsuru TATE, Kichiya SUZUKI, Hesu REE, Yoshikazu KUWANO, Tongshik CHANG, Hirao GO, Mikiyasu MATSUZAKI, Shigeko NAKAMURA
pp. 483-494
抄録
During the 24th and 25th campaign of the experimental blast furnace, the “heat level” characterized by Si was changed from high to low or reversely by altering either blast temperature and humidity or ore to coke ratio (O/C). Summarizing informations obtained by sampling, temperature-measurement ana observation with scopes, effects of the “heat level” on the position of melt-down level and on the processes of molten products formation were investigated.
1. In case the difference of Si was same, melt-down level displaced more largely by the change of ratio O/C than by the alteration of blast heat.
2. The decrease of blast heat caused not only the fall of melt-down level, but also the increase of (FeO) in molten slag.
3. Partly reduced ore particles adhered together by the “Sintering” mechanism to make a consolidated ore layer. Melting-down of metallic part of this layer was estimated to take place at 1350-1400°C (after its carbon content increased to 0.8-1.0%).
4. Chemical analysis of metal samples showed remarkably unequal radial and peripheral distribution. Especially, Si contents were much higher around the raceway than their final values, while they were much less at the periphery between two adjacent tuyeres.
5. Chemical compositions of slag samples were, in general, fairly close to those of final slag with the exception of high (FeO) and slightly lower (Al2O3), both of which seemed to attain their final values in the hearth.
Abnormal Operation Due to High-Temperature Degradation of Coke
Mitsuru TATE, Yoshikazu KUWANO, Kichiya SUZUKI, Tongshik CHANG, Hirao GO, Mikiyasu MATSUZAKI
pp. 495-504
抄録
In the last period of the 25th campaign, during which coke (B) made from an inferior coal mixture was used, a stagnant stock movement and an increase of pressure drop in the lower region occurred at the times when maximum volume of molten products was accumulated in the hearth. Observations with a fibre or bore-scope showed:
(1) Feeding of flaky coke fines from above into the raceway around the tuyere nose;
(2) Scattering of coke fines in the upper bosh (at the position BIII-1);
(3) Alternative fluidization and rapid descent of flaky coke fines in the furnace center (at the position CII-1);
(4) Rise of slag bath surface to a high level (at position CII-1).
These phenomena together with the results of hot-model experiments made the authors conclude that the flaky coke fines, generated at some high-temperature region above the combustion zone as a result of a degradation of charged coke, accumulated gradually in the bosh and hearth and caused a marked increase of slag hold-up and of resistance to gas flow.
Investigations on the cooled furnace contents after blowing-out suggested that the degradation, or the revelation of defects inherent in coke (B), might start at about 1000°C in the lower shaft and become remarkable in the belly. Though a degradation due to the gasification with CO2 may be supposed, other mechanisms should also be examined in view of a large quantity of alkaline matters adsorped by coke in the region from lower shaft to belly.
他の人はこちらも検索
鉄と鋼 Vol.50(1964), No.13
鉄と鋼 Vol.70(1984), No.11
鉄と鋼 Vol.45(1959), No.11
Analysis of the Combustion Zone in the Experimental Blast Furnace
Michiharu HATANO, Bunsho HIRAOKA, Mitsuichiro FUKUDA, Tamotsu MASUIKE
pp. 505-513
抄録
The combustion of fuels in the raceway and the resultant raceway depth were investigated using an experimental blast furnace simulated to the lower part of a commercial furnace. The results obtained are as follows:
1) The combustion of a great majority of cokes takes place near the boundary of the raceway. When fuel is not injected, CO and H2 are hardly observed in the raceway, although their concentration increases rapidly by the carbon solution reaction which takes place near the boundary of the raceway.
2) With heavy fuel oil injection, the combustion zone approaches to the tuyere nose and the temperature rises at the furnace wall around the tuyere. At the same time, the region where CO and H2 arc generated shifts near to the tuyere.
3) The raceway depth under the condition of combustion is possibly estimated by taking account the properties of coke, the changes of gas volume and temperature in front of tuyere into Wagstaff's equation.
他の人はこちらも検索
鉄と鋼 Vol.65(1979), No.5
鉄と鋼 Vol.62(1976), No.5
鉄と鋼 Vol.62(1976), No.1
Heavy Oil Combustion in Blowpipe and Tuyere of Blast Furnace
Toshihiro INATANI, Kyoji OKABE, Tetsuji NISHIYAMA, Yasunori SERIZAWA, Hiromitsu TAKAHASHI, Mitsuo SAINO
pp. 514-524
抄録
The injection of large quantities of auxiliary fuels to reduce the coke rate at blast furnaces is an economic necessity because of the shortage of coke and its increasing cost. One of the reasons of the limitation of the amount of injected heavy oil is incomplete combustion with unacceptable soot formation.
Firstly, the authors observed the phenomena in the raceway by using the experimental model and, secondly, they analyzed the combustion process in the real raceway on the basis of the gas composition measured by the probe inserted through the tuyere.
The heavy oil is generally injected from the tip of oil nozzle settled near the tuyere at the oxygen excess ratio (μ) over 1.1. A great part of injected oil burns simultaneously with coke in the raceway and soot formation begins with increasing the amount of injected oil.
In order to gasify the heavy oil in the blowpipe and tuyere before the beginning of the coke combustion, the nozzle tip was moved backward 1.75 or 0.75m away from the tuyere nose. The test of the new injection system was carried out at No. 6 tuyere of No. 2 blast furnace in Chiba Works and its results were also discussed. Much quantity of heavy oil could be gasified without soot formation on the condition of μ=0.9.
Formation of Titanium Compounds, So-called Titanium-Bear, in the Blast Furnace Hearth
Kiich NARITA, Masahiro MAEICAWA, Toshio ONOYE, Yoshitomo SATOH, Manabu MIYAMOTO
pp. 525-534
抄録
Titanium compounds, so-called titanium-bear, are generally formed in the blast furnace hearth, because iron ore contains more or less titanium oxide. Physico-chemical examinations on the titanium compounds picked up from the blown-out blast furnace hearth were carried out.
It was found that the titanium compounds are TiC-TiN solid solution and a section surface of the crystal seems to be an annual ring consisting of many layers, of which color changes corresponding to the carbon / nitrogen concentration ratio. This is also related to the condition of circumstances, such as the temperature, partial pressure of nitrogen, and motion of molten iron, at which the crystal grew. Therefore, the titanium compounds, which had grown over long period, reflect the course of operation of the blast furnace.
他の人はこちらも検索
鉄と鋼 Vol.75(1989), No.6
鉄と鋼 Vol.65(1979), No.10
鉄と鋼 Vol.87(2001), No.5
Dissection of Blast Furnaces and Their Inside State
Kenjiro KANBARA, Tomoro HAGIWARA, Akitoshi SHIGEMI, Shin-ichi KONDO, Yuji KANAYAMA, Kei-ichi WAKABAYASHI, Nobuyoshi HIRAMOTO
pp. 535-546
抄録
For the purpose of investigating the inside of operating blast furnace, Higashida No. 5 B.F. (inner volume 646 m3) was dissected and examined, after quenched with water under normal operating condition in 1968. This was the first trial in Japan of dissecting a commercial blast furnace.
Next, Hirohata No. 1 B. F. (inner volume 1407m3), which had been operated with considerably high productivity, was dissected in 1970.
Thirdly, Kukioka No. 4 B.F. (inner volume 1279m3) was also dissected in 1971, so as to clarify the features of low coke ratio furnace.
In this paper, the procedure of dissection, the general views on the inside of these furnaces, the characteristics of each furnace, and the relationships between the inside state and operating conditions are described.
On the Inside State of the Lumpy Zone of Blast Furnace
Yasuto SHIMOMURA, Kiyoshi NISHIKAWA, Shunsuke ARINO, Tsutomu KATAYAMA, Yukihiro HIDA, Tadashi ISOYAMA
pp. 547-558
抄録
Hirohata No. 1 BF and Kukioka No. 4 BF of Nippon Steel Corporation were blown down in a usual operating state and dissected very cautiously after quenched with water. The conditions in the reducing zone of the furnace shaft are explained in this report.
From these investigations burden distribution, gas flow at the shaft deduced from the burden distribution, changes of burden properties according to the progress of reduction, and the behaviors of Zn, S and alkali materials in the shaft were clarified. Both furnace conditions were carefully compared to the respective operating conditions. The relation between the operating conditions and the changes of burden properties at the shaft were cleared.
Based on the results of dissection, burden testing methods and necessary burden properties are discussed.
Formation and Melt-Down of Softening-Melting Zone in Blast Furnace
Minoru SASAKI, Katsuya ONO, Akira SUZUKI, Yoshio OKUNO, Ken-ichi YOSHIZAWA, Takashi NAKAMURA
pp. 559-569
抄録
The processes of formation and melt-down of the softening-melting zone are discussed based on the results of dissection of water-quenched blast furnaces.
1) Iron ore granules of the ore layer change to half-molten state through softening. The transformation of the granules is mainly effected by the hot reducing gas passing through the ore layer.
2) Two processes of melt-down of metal are considered as followed: One is the formation of “Icicle”from the mixture of metal particle and molten slag. The other is the rapid carbonization in metal which contacts with hot coke at about 1500 C. Reduction of silicon in metal does not occur in these processes.
3) The original slags generating in granules of pellet and lumpy ore are rich in FeO. After separating from the granules they are blended with the slag from sinter. FeO in total slag is further decreased by gas-reduction. Consequently, FeO content of the slag just before melt-down is only a few percent.
4) The drop metal and slag have changed their composition after the blowing down of the furnace. Therefore, the change in composition during the dropping process is much difficult to be estimated.
他の人はこちらも検索
鉄と鋼 Vol.51(1965), No.6
鉄と鋼 Vol.58(1972), No.2
鉄と鋼 Vol.58(1972), No.14
Change of Coke Properties in Blast Furnace
Kojiro KOJIMA, Tetu NISI, Tokuji YAMAGUCHI, Hiroyuki NAKAMA, Shiro IDA
pp. 570-579
抄録
The change of coke properties in the blast furnace was investigated using samples from Higashida No. 5, Hirohata No. 1 and Kukioka No. 4 blast furnaces, which were dissected after being quenched with water in normal operating state.
The results of the research are summarized as follows:
1) The change of coke properties becomes remarkable below the lower shaft level.
2) According to the microscopic observation, this change of coke properties seems to be due to the selective carbon solution-loss reaction at specified textures of coke, resulting in the weakening of strength and the generation of fine particles.
3) This phenomenon is particularly remarkable around the race-way of blast furnace.
Investigation of Quenched No. 2 Blast Furnace at Kokura Works
Kantaro SASAKI, Michiharu HATANO, Masao WATANABE, Teruhisa SHIMODA, Katuhiro YOKOTANI, Takao ITO, Takashi YOKOI
pp. 580-591
抄録
When Kokura No. 2 B.F. was blown out on 25th, Sept., 1974, the furnace was quenched with water and the investigation in the blast furnace was carried out concerning the following items:
(1) The distribution of burden materials, patterns of melting zone and shapes of the raceway in the furnace.
(2) The change of some properties of coke and sinter in the furnace.
(3) The relationship between operating conditions and some phenomena in the furnace.
論文アクセスランキング
28 Jul. (Last 30 Days)
-
Perspectives on the Promising Pathways to Zero Carbon Emissions in the Steel Industry toward 2050
ISIJ International Vol.65(2025), No.2
-
-
Effect of BN surface segregation on coatability in hot-dip galvanizing of B-added steel
ISIJ International 早期公開
-
Factors affecting generation of iron fines in cold sheet rolling of steel
ISIJ International 早期公開
-
Wettability of CaS Against Molten Iron at 1873 K
ISIJ International Vol.65(2025), No.2
-
Copper removal of liquid steel containing 0.25 % carbon using Fe2O3-CaCl2-SiO2 flux
ISIJ International 早期公開
-
-
Dislocation Density and Reverse Transformation Kinetics in Martensitic Steel Under Cyclic Ultrafast Heating and Cooling
ISIJ International Vol.65(2025), No.8
-
銅含有棒鋼の熱間圧延プロセスにおける表面欠陥の発生
鉄と鋼 Vol.111(2025), No.5
-
Experimental Study on Heat Transfer Characteristics of a Moving Single-Nozzle Jet Impingement
ISIJ International 早期公開
この機能はログイン後に利用できます。
下のボタンをクリックしてください。