鉄と鋼 Vol. 52 (1966), No. 1
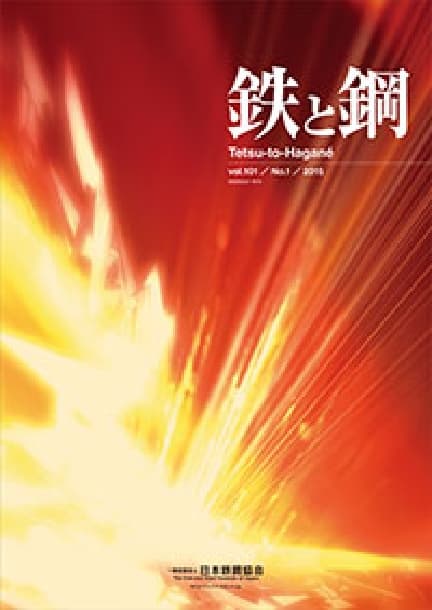
Grid List Abstracts
オンライン版ISSN: | 1883-2954 |
冊子版ISSN: | 0021-1575 |
発行機関: | The Iron and Steel Institute of Japan |
Backnumber
-
Vol. 111 (2025)
-
Vol. 110 (2024)
-
Vol. 109 (2023)
-
Vol. 108 (2022)
-
Vol. 107 (2021)
-
Vol. 106 (2020)
-
Vol. 105 (2019)
-
Vol. 104 (2018)
-
Vol. 103 (2017)
-
Vol. 102 (2016)
-
Vol. 101 (2015)
-
Vol. 100 (2014)
-
Vol. 99 (2013)
-
Vol. 98 (2012)
-
Vol. 97 (2011)
-
Vol. 96 (2010)
-
Vol. 95 (2009)
-
Vol. 94 (2008)
-
Vol. 93 (2007)
-
Vol. 92 (2006)
-
Vol. 91 (2005)
-
Vol. 90 (2004)
-
Vol. 89 (2003)
-
Vol. 88 (2002)
-
Vol. 87 (2001)
-
Vol. 86 (2000)
-
Vol. 85 (1999)
-
Vol. 84 (1998)
-
Vol. 83 (1997)
-
Vol. 82 (1996)
-
Vol. 81 (1995)
-
Vol. 80 (1994)
-
Vol. 79 (1993)
-
Vol. 78 (1992)
-
Vol. 77 (1991)
-
Vol. 76 (1990)
-
Vol. 75 (1989)
-
Vol. 74 (1988)
-
Vol. 73 (1987)
-
Vol. 72 (1986)
-
Vol. 71 (1985)
-
Vol. 70 (1984)
-
Vol. 69 (1983)
-
Vol. 68 (1982)
-
Vol. 67 (1981)
-
Vol. 66 (1980)
-
Vol. 65 (1979)
-
Vol. 64 (1978)
-
Vol. 63 (1977)
-
Vol. 62 (1976)
-
Vol. 61 (1975)
-
Vol. 60 (1974)
-
Vol. 59 (1973)
-
Vol. 58 (1972)
-
Vol. 57 (1971)
-
Vol. 56 (1970)
-
Vol. 55 (1969)
-
Vol. 54 (1968)
-
Vol. 53 (1967)
-
Vol. 52 (1966)
-
Vol. 51 (1965)
-
Vol. 50 (1964)
-
Vol. 49 (1963)
-
Vol. 48 (1962)
-
Vol. 47 (1961)
-
Vol. 46 (1960)
-
Vol. 45 (1959)
-
Vol. 44 (1958)
-
Vol. 43 (1957)
-
Vol. 42 (1956)
-
Vol. 41 (1955)
キーワードランキング
07 Sep. (Last 30 Days)
鉄と鋼 Vol. 52 (1966), No. 1
1965 Perspective of Production and Technique of Iron and Steel in Japan
Takeshi YAMAOKA
pp. 3-9
On the Improvement of Reduction by Rotary Kiln
Hideo ARAKAWA
pp. 10-22
抄録
Synopsis:
The present paper in this series of studies shows the results of testing the new techniques which improve the kiln reduction. So far the design and operation of the so-called ‘throwing-coal method’have been examined in order to prevent adhesion trouble, that is, dam-ring. Previous studies confirmed the fact that immoderate reoxidation of the material bed at the discharge end of the kiln causes adhesion trouble. The present study finds that we can succesfully prevent not only adhesion trouble, but also spalling by adding a little amount of highly volatile coal to the material bed through the discharge end. It also finds that 30 kg coal per a ton of the products is enough for the purpose mentioned above.
Now, the special arrangement of the particle-size of burden material is needed in order to regulate segregation between are and reductant in the process of kiln reduction. We find that segregation is regulated and controlled by arranging the particle-size in such a way that the differences among repose angles of the binary system may be kept within narrow limits, that is, within ab out five degrees.
Ingeneral, since there is a considerable amount of reducing gases inthe exhaust gases of kiln reduction, we make a great deal of heat recovery by injecting air at themiddle part of the kiln shell.
The amount of air theoretically measured for complete combustion of exhaust gases, together with a small amount of excess air, was introduced into the kiln by means of the air fan installed at 55% of the total length of the kiln shell from its discharge end. From thisexperiment we found that reducing gases burned with injection air of 720m3 per an hour, and that the middle part of 46m long kiln was heated up and reached the reduction temperature because of this combustion; as the result, the heat loss amounting to 515×103 kcal had been recovered.
The operation of the kiln under new techniques such as throwing-coal, control of particle-size, and air injection, shows very satisfactory results. The kiln through-putincreased by about 30%; the consumption of fuel oil was reduced by 20%; the residual carbon contained in the products decreased to 2%; the reductant needed in burden was reduced by 7%; and the total heat consumption per a ton of the products decreased by 270×103 kcal to 1840×103 kcal. Furthermore, the new techniques made the operation remarkably easier and freer from dam-ring.
Finally, we test and evaluate other improvements such as:- dust circulation, installation of chains in the feed-end, sectional air injection, installation of ring-dams at the intermediate.
Effect of the Hardness on the Damages due to Rolling Contact of Back-up Roll Materials
Hideo SHIMODA, Yutaka ARAKIDA, Kiyoshi HORI, Koichi KUDO
pp. 23-31
抄録
Spalling of back-up rolls is a matter of great concern for both roll users and manufacturers because it makes the unit cost of a roll higher and gives unfavorable effect upon the surface of the rolled products.
In order to make this problem clear, measurements of wear, temperature and mill load are required and further it seems to be desirable to test rolls in practical mills. But as these measurements and tests take much cost and long time, the short-cut to the solution of this problem will be to design and manufacture a test mill and to observe the development of the damages by reproducing the spalling on the model roll.
There are many factors which affect the generation of spalling of back-up rolls from the standpoints of both application and materials and such factors seem to act on each other and to make the phenomena of spalling complex. Of these many factors, heat treatment of roll materials, especially their hardness, is considered to be the most important for the roll manufacturing.
With the intention of clarifying the effect of the hardness of back-up roll materials on the damages due to rolling contact, a new 3-high rolling contact testing machine was designed and constructed.
This testing machine consists of two hardend rolls (Hs 85∼90, 140mm_??_) and a specimen (70mm_??_) with 15mm effective width which is placed between these two hardened rolls and is rolled under various loads.“Damage index” was defined to evaluate the defects on the surface of a specimen by roll on roll under heavy load.
The specimens are heated to 850°C and quenched in oil. Then they are tempered to various hardnesses.The rolling on roll test was carried out under 120kg/mm2 of Hertz maximum stress.
The main results obtained are as follows:(1) As the hardness of materials become higher, resistan ceto rolling contact damages increases.(2) The surface layers of low hardness specimens are strengthend by rolling contact, so it seems to make the life of these specimens longer.
他の人はこちらも検索
鉄と鋼 Vol.57(1971), No.1
鉄と鋼 Vol.57(1971), No.5
鉄と鋼 Vol.50(1964), No.12
Diffusion of Iron in Some Molten Non-Ferrous Metals
Makoto KATO, Susumu MINOWA
pp. 32-41
抄録
The diffusivity is an important variable in a number of metallurgical phenomena. However, until recently few quantitative data have been availiable on diffusion phenomena of iron in liquid nonferrous metals. Therefore, we attempted to determine the diffusion coefficients of iron in molten Al, Zn, Sn and Mg.
The results obtained were as follows:
1) In some examinations of diffusion run in molten Zn by semi-infinite medium, the unexpected distributions of iron concentration in molten Zn were observed. These phenomena were considered as “precipitation” originating from the difference of specific gravity. Therefore, prior to determining the diffusion coefficient of iron, the solubility of it in molten Zn was measured by some methods in the temperature range from 450°C to 700°C. The solubility measured in this work is very small compared with the value shown in literatures.
2) The diffusion coefficients of iron in molten Al, Zn, Sn and Mg were determined by Stefan and Kawalki's method. The diffusion coefficients determined were:
In molten Al (700-900°C) DFe=37×10-3 exp (-4, 000/RT) cm2/sec In molten Zn (470-900°C) DFe= 27×10-2 exp (-8, 700/R T)
In molten Sn (500-900°C) DFe=19×10 exp (-3, 000/R T)
In molten Mg (800-900°C) DFe=17×10-3 exp (-2, 500/RT)
3) Above results were compared with the calculated values by some representative equations. The obtained diffusion coefficients of iron in this work agree well with the calculated values by the Li-Chang's equation, using Goldshmit's ionic radius of iron for radius of diffusion molecule. This result shows that cations of iron diffuse in molten non-ferrous metals, because the activation energy of diffusion is of the same order as in the nonmetallic solutions.
Some Observations on Niobium in Steel
D. R. BELL, G. P. CONTRACTOR
pp. 42-54
抄録
The effects of niobium on silicon-killed, low carbon steel were investigated. Most of the data relate to 450-1b laboratory melts, forged and rolled to 3/4 in. plate. Data from one heat of commercial steel were also examined.
In the as-rolled condition, it was found that small additions of niobium increased the yield strength and raised the transition temperature markedly, but that larger additions were less effective.In the normalized condition, the effects on yield strength were similar to those in the as-rolled condition but the changes were less marked. The transition temperature was improved with all levels of niobium, the smallest additions (up to 0.04%) being most effective.
Commercial plate of a similar composition to the laboratory steel was procured with niobium contents of approximately zero, 0.010% and 0.023%, in 1/4 in., 3/4in., and 1-1/2 in. thicknesses. The yield strength and transition temperature results obtained on the commercial material qualitatively corroborated the findings of the laboratory steels. Niobium was most effective in increasing the yield strength in the 1/4 in. plate, the effectiveness decreasing as the plate thickness increased. Rotating beam fatigue tests showed that niobium slightly increased the fatigue limit of smooth bars and had no effect on the fatigue limit of notched bars. The fatigue ratio was unaffected by niobium for smooth bars and decreased somewhat for notched bars.
Limited data, based on electrolytically extracted residues, indicated that the major bulk of the niobium added to the steels was partitioned to the carbide phase. Similarly, much of the nitrogen present in the steels was found to occur in the residues.
The evidence indicated that the effects of niobium on the yield strength and notch ductility of normalized carbon steel were qualitatively explicable in terms of grain refinement, and precipitation strengthening. The evidence did not account for the pronounced effects of small quantities of niobium on as-rolled steel.
他の人はこちらも検索
鉄と鋼 Vol.74(1988), No.9
MATERIALS TRANSACTIONS Vol.49(2008), No.4
ISIJ International Vol.44(2004), No.7
View of the Future Shipbuilding World and Demand for Steel Materials.
Motomi AKITOMO
pp. 55-64
論文アクセスランキング
07 Sep. (Last 30 Days)
-
Perspectives on the Promising Pathways to Zero Carbon Emissions in the Steel Industry toward 2050
ISIJ International Vol.65(2025), No.2
-
溶鋼中での各種酸化物系介在物の成長・除去と凝集
鉄と鋼 Vol.111(2025), No.11
-
Finite Element Analysis of Bubble Growth and Particle Swelling during Coal Pyrolysis
ISIJ International Vol.65(2025), No.9
-
通電誘起高速共晶反応によるAl/Cu異材接合形成につながる界面挙動
溶接学会論文集 Vol.43(2025), No.2
-
Copper removal of liquid steel containing 0.25 % carbon using Fe2O3-CaCl2-SiO2 flux
ISIJ International 早期公開
-
Corrosion Behavior of Carbon Steel under Soil Drying Conditions
ISIJ International 早期公開
-
980 MPa級高張力鋼板の固相抵抗スポット接合
鉄と鋼 早期公開
-
-
-
この機能はログイン後に利用できます。
下のボタンをクリックしてください。