鉄と鋼 Vol. 47 (1961), No. 11
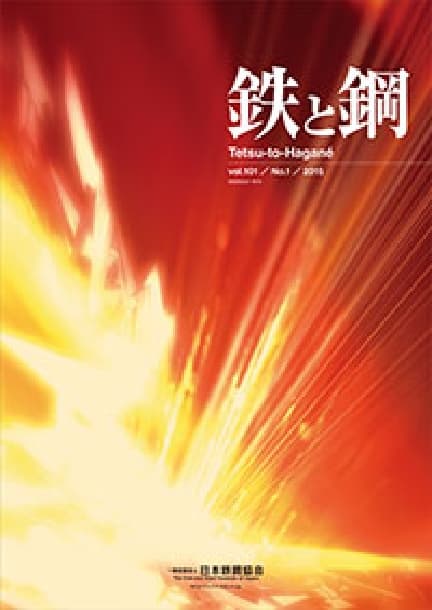
Grid List Abstracts
オンライン版ISSN: | 1883-2954 |
冊子版ISSN: | 0021-1575 |
発行機関: | The Iron and Steel Institute of Japan |
Backnumber
-
Vol. 111 (2025)
-
Vol. 110 (2024)
-
Vol. 109 (2023)
-
Vol. 108 (2022)
-
Vol. 107 (2021)
-
Vol. 106 (2020)
-
Vol. 105 (2019)
-
Vol. 104 (2018)
-
Vol. 103 (2017)
-
Vol. 102 (2016)
-
Vol. 101 (2015)
-
Vol. 100 (2014)
-
Vol. 99 (2013)
-
Vol. 98 (2012)
-
Vol. 97 (2011)
-
Vol. 96 (2010)
-
Vol. 95 (2009)
-
Vol. 94 (2008)
-
Vol. 93 (2007)
-
Vol. 92 (2006)
-
Vol. 91 (2005)
-
Vol. 90 (2004)
-
Vol. 89 (2003)
-
Vol. 88 (2002)
-
Vol. 87 (2001)
-
Vol. 86 (2000)
-
Vol. 85 (1999)
-
Vol. 84 (1998)
-
Vol. 83 (1997)
-
Vol. 82 (1996)
-
Vol. 81 (1995)
-
Vol. 80 (1994)
-
Vol. 79 (1993)
-
Vol. 78 (1992)
-
Vol. 77 (1991)
-
Vol. 76 (1990)
-
Vol. 75 (1989)
-
Vol. 74 (1988)
-
Vol. 73 (1987)
-
Vol. 72 (1986)
-
Vol. 71 (1985)
-
Vol. 70 (1984)
-
Vol. 69 (1983)
-
Vol. 68 (1982)
-
Vol. 67 (1981)
-
Vol. 66 (1980)
-
Vol. 65 (1979)
-
Vol. 64 (1978)
-
Vol. 63 (1977)
-
Vol. 62 (1976)
-
Vol. 61 (1975)
-
Vol. 60 (1974)
-
Vol. 59 (1973)
-
Vol. 58 (1972)
-
Vol. 57 (1971)
-
Vol. 56 (1970)
-
Vol. 55 (1969)
-
Vol. 54 (1968)
-
Vol. 53 (1967)
-
Vol. 52 (1966)
-
Vol. 51 (1965)
-
Vol. 50 (1964)
-
Vol. 49 (1963)
-
Vol. 48 (1962)
-
Vol. 47 (1961)
-
Vol. 46 (1960)
-
Vol. 45 (1959)
-
Vol. 44 (1958)
-
Vol. 43 (1957)
-
Vol. 42 (1956)
-
Vol. 41 (1955)
キーワードランキング
06 Sep. (Last 30 Days)
鉄と鋼 Vol. 47 (1961), No. 11
On the Results of Pilot Plant Tests on Decopperization, Dezincification, etc. of Pyrite Cinders
Kazuhisa OKAJIMA, Michio INOUYE, Kokichi SANO
pp. 1577-1582
抄録
The results of pilot plant tests for selective chlorination roasting of pyrite cinders by the fluidizing roaster were reported in this paper.
The results were summarized as follows:
(1) Under the roasting conditions of 1.3% Cl2 in air, about 940°C and 40-45mn., over 80% of the copper in the pyrite cinder was eliminated. The particle size had little effect on the decopperization obtained.
(2) The zinc and sulfur were effectively eliminated and the iron loss was small, but the cobalt remained unchanged.
(3) The present tests gave fully satisfactory results.
Some Remarks on the Technique of Continuous Temperature Measurement for Steel Bath
Shinsaku ONODERA, Yutaka ARAKIDA, Noboru HIRAOKA
pp. 1582-1588
抄録
To make sufficient control of the casting temperature that is one of the important factors in ingot making, the temperature change in ladles must be known precisely and successively.
A technique of continuous immersion pyrometry has been developed which was established to measure the temperature of steel bath in a ladle uninterruptedly from tapping to casting.
In this method, a long hollow steel spindle covered with refractory sleeves and a refractory endblock (stopper head) is used as the protecting tube of thermocouples, with additional silica sheaths inserted into the top of the endblock. This protecting rod is held vertically in molten steel.
After some preliminary tests have been made, the continuous measurement of temperature in ladle becomes a daily work, and the casting temperature is being controlled precisely.
Up to now, the results obtained from these measurements are as follows:
(1) In a ladle, the slag layer seems to be a good and effective thermal insulator, so the temperature of molten steel in the upper part is considerably higher. Therefore, the temperature of casting stream rises gradually.
(2) The larger the capacity of a ladle, the smaller the rate of temperature drop of molten steel in the ladle.
(3) The variation of temperature drop from tapping to casting in large ladles is smaller than that of small ladles.
(4) From the above results, it is known that the casting temperature is not necessarily estimated from the tapping one, which will stimulate the discussions on the significance of the measurement of casting temperature.
On the Relation between the Sand Marks and Top-and Bottom-Teeming Procedures
Zenichiro TAKAO, Takaaki SIMOSE, Kiichi NARITA, Atsusi MIYAMOTO
pp. 1588-1593
抄録
With the chromium-molybdenum steel No.21 containing aluminum acting as the deoxidizer and the austenite grain refiner, the authors examined into the top-and bottom-teeming procedures for ingot making, which had some effects on the occurrence tendency of the sand marks.
The results are as follows:
1. The occurrence tendency of the sand marks is a little more remarkable in the topteeming than in the bottom-teeming.
2. Sand marks of the complicated, the crystalline and the amorphous types are found in the examined steel. The rate of the occurrence of the sand marks is 60 to 70% for the complicated type, 26 to 30% for the crystalline type and 8 to 10% for the amorphous type.
3. No difference between top-and bottom-teeming procedures in the type of the sand marks and in the nonmetallic inclusions which constitute them has been found.
4. Oxide inclusions in the examined steel mainly consist of Al2O3 and, in general, the top-teemed ingot has a little more oxide inclusions than bottom-teemed one. In the topteemed ingot, oxide inclusions are rich in the top part of the ingot and relatively poor inthe middle and the bottom parts of it. In the bottom-teemed ingot, on the other hand, they are the richest in the bottom part and the next in the top parts in quantity, and relatively poor in the middle part.
5. There is a correlation between the occurrence tendency of the sand marks and the quantities of oxide inclusions. Namely forged or rolled steel containing many oxide inclusions has a great possibility of the occurrence of the sand marks in comparison with forged or rolled steel which has less oxide inclusions.
On the Relation between Reduction Ratio and Mechanical Properties of Killed Steel Plates
Takeshi OKURO, Shigeru WAKUSHIMA, Nobuo FUKAYA, Masuhiro SATO
pp. 1594-1601
抄録
To investigate the relation between reduction ratio and mechanical properties of killed mild steel plates, the following tests were carried out.
(1) Six 10-t ingots from a coarse austenitic-grained heat melted with a basic open hearth furnace were hot-rolled into several plates of different thickness, which corresponded the reduction ratios (=ingot thickn./plate thickn.) of 4, 6, 7, 8, 12 and 20, respectively.
(2) For the comparison with test 1, one 10-t ingot from fine austenitic-grained heat melted with a basic open hearth furnace was hot-rolled in to a reduction ratio of 7.5.
(3) One twelve-sided 15t ingot from an acid open hearth furnace was forged into a slab previously, then rolled in to a 100mm thick plate. The total reduction ratio combined with forging and rolling reductions was 10.1.
The results obtained were as follows:
(1) The mechanical properties of rolling-direction specimens were improved with increase of reduction ratio, rapidly up to a reduction ratio of 12 and slowly thereafter. This tendency was remarkable in elongation, reduction of area and notch-toughness but a little in yield and tensile strengths.
(2) The mechanical properties of transversal-direction specimens were improved rapidly with increase of reduction ratio up to 8, but better effects were not expected with further proceeding of rolling. This tendency was conspicuous in elongation and reduction of area.
(3) In mechanical properties in the thickness direction, tensile and yield strengths wereimproved remarkably with plates of reduction ratios between 7 and 8. Elongation, reduction of area and notch-toughness were increased with plates of reduction ratio up to 12, but decreased thereafter.
(4) Hence, in considering the properties in the thickness direction, it was desirable to apply the rolling reduction ratio over 8 for commercial steel plate. At the reduction ratio of 12, best properties were obtained for all directions in the plate.
(5) After normalizing, the properties except tensile strength were improved, but the behavior of reduction ratio was scarcely varied from the as-rolled condition.
(6) Application of forging in slabbing process was effective as well as rough rolling, and a property impro.vement corresponding to total reduction ratio was achieved.
(7) The same behavior was obtained in the case of a fine-grained steel in the relation between reduction ratio and mechanical properties.
Hot-Twist Ductility of High-C Ferritic Steels
Fujio TSUKAMOTO, Takashi SUZUKI
pp. 1602-1606
抄録
The hot-twist ductility of AISI Type 446 and some other high-Cr ferritic steels, especially effects of metallurgical factors such as alloying elements, microstructure and grain size were investigated by hot-twist test rotated at 200r.p.m at a temperature ranging from 800 to 1250°C.
The hot-twist ductility of high-Cr steels was much influenced by its microstructure.
Some steels which had a single ferritic structure at these testing temperatures showed higher twist value and a convex type twist curve against the testing temperatures, while other steels which transformed at a testing temperature showed a lower twist value and had a concave-type twist curve. The temperature at which the specimen showed the minimum twist value nearly corrresponded to the transformation temperature.
As to the influence of the alloying elements in 25% Cr steels, C and N were the most detrimental ones which lowered these twist values. Addition of C+N up to about 0.2% greatly reduced a hot-twist ductility and about 0.2% of C+N was the inflection point of curve figure. Addition of Si, Ni, and Cr reduced a hot-twist value although Ni improved hottwist value above 1200°C.
The difference of hot-twist value could not be recognized between air- and vacuum-melted specimens which had similar chemical compositions.
Grain-coarsening owing to the elevation of annealing temperature lowered hot-twistductility, especially when single-phase specimens were annealed at a temperature higher than the temperature of maximum ductility. In the latter case intercrystalline fracture occurred at every test temperature and consequently twist values were much reduced.
Effects of Additional Elements on Characteristics of Age-Hardening of the Gamma Type Fe-Co-Cr-Ni-Base Heat-Resisting Alloy, LCN-155
Yunoshin IMAI, Tsuyoshi MASUMOTO
pp. 1607-1613
抄録
Individual or combined effects of additional elements (N, Cb, Mo, and W) on the hardness as solution-treated, the characteristics of age-hardening, and the rates of age-hardening and softening du to over aging of the Fe-Co-Cr-Ni base heat-resisting alloy were investigated by measurement of hardness.
The excellent properties on age-hardening of LCN-155 alloy were due to the combined effect of nitrogen together with molybdenum and tungsten in addition due to the effect of carbon, and the effect of nitrogen together with columbium was available in the presence of molybdenum and tungsten.
The advantageous effects of such elements on the age-hardening should be presumably due to change of a dispersion state, shape, or transition process of precipitates.
On the Corrosion of Cast Iron by Various Sulphuric Gases at High Temperature
Hiroshi NAKAI
pp. 1613-1616
抄録
Sulphidation of iron and steel at high temperatures is lately discussed in many literatures. The author has experimented on the sulphidation of cast iron at high temperature. In this report, he dealt with the corrosion of cast iron at high temperature in S vapour, CS2 vapour, H2S gas and SO2 gas. The following results were obtained:
(1) The sulphidation product of cast iron was composed of pyrrhotite Fe1-xS. And from the X-ray analysis, it was found that the outer layer was composed of FeS and FeS2 in Svapour, FeS in CS2 vapour, FeS in H2S gas and that FeS and Fe3O4 in SO2 gas. In the outer layer C and P did not diffuse, on the contrary Mn diffused freely and Si did a little.
(2) The sulphidation rate was controlled by the parabolic rate law, and the following formula was obtained:
S vapour: W2=0.36×10-8 t
CS2 vapour: W2=0.64×10-7t
H2S gas: W2=1.15×10-6t
SO2 gas: W2=0.12×10-7 t W: sulphidation rate, g/cm2 t: sulphidation time, s.
(3) In this experiment, the sulphidation rate of cast iron in H2S gas was superior to those in other gases, which followed in order of CS2 vapour, SO2 gas and S vapour.
On the Iron Ore Reduction in Blast Furnaces
Kamekichi WADA, Koretaka KODAMA, Akitosi SIGEMI
pp. 1617-1630
他の人はこちらも検索
鉄と鋼 Vol.47(1961), No.11
鉄と鋼 Vol.105(2019), No.5
鉄と鋼 Vol.105(2019), No.6
Cast Iron Rolls for Steel Rolling
Kakunosuke MIYASHITA
pp. 1631-1643
他の人はこちらも検索
鉄と鋼 Vol.47(1961), No.11
鉄と鋼 Vol.105(2019), No.5
鉄と鋼 Vol.105(2019), No.6
論文アクセスランキング
06 Sep. (Last 30 Days)
-
Perspectives on the Promising Pathways to Zero Carbon Emissions in the Steel Industry toward 2050
ISIJ International Vol.65(2025), No.2
-
溶鋼中での各種酸化物系介在物の成長・除去と凝集
鉄と鋼 Vol.111(2025), No.11
-
Finite Element Analysis of Bubble Growth and Particle Swelling during Coal Pyrolysis
ISIJ International Vol.65(2025), No.9
-
通電誘起高速共晶反応によるAl/Cu異材接合形成につながる界面挙動
溶接学会論文集 Vol.43(2025), No.2
-
Corrosion Behavior of Carbon Steel under Soil Drying Conditions
ISIJ International 早期公開
-
980 MPa級高張力鋼板の固相抵抗スポット接合
鉄と鋼 早期公開
-
-
-
Copper removal of liquid steel containing 0.25 % carbon using Fe2O3-CaCl2-SiO2 flux
ISIJ International 早期公開
-
Evaluation of Feature Selection Methods for Oxygen Supply Prediction in BOF Steelmaking
ISIJ International 早期公開
この機能はログイン後に利用できます。
下のボタンをクリックしてください。