鉄と鋼 Vol. 64 (1978), No. 13
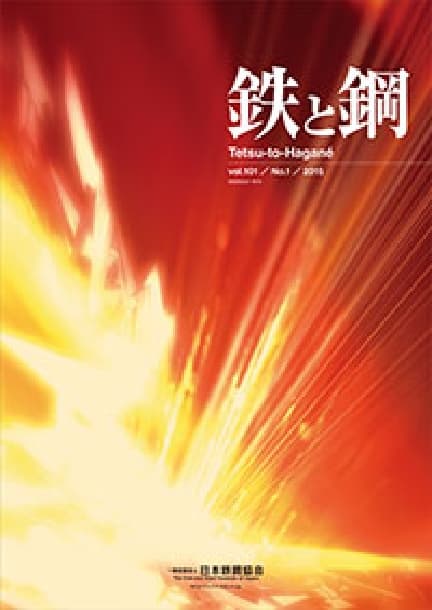
Grid List Abstracts
オンライン版ISSN: | 1883-2954 |
冊子版ISSN: | 0021-1575 |
発行機関: | The Iron and Steel Institute of Japan |
Backnumber
-
Vol. 111 (2025)
-
Vol. 110 (2024)
-
Vol. 109 (2023)
-
Vol. 108 (2022)
-
Vol. 107 (2021)
-
Vol. 106 (2020)
-
Vol. 105 (2019)
-
Vol. 104 (2018)
-
Vol. 103 (2017)
-
Vol. 102 (2016)
-
Vol. 101 (2015)
-
Vol. 100 (2014)
-
Vol. 99 (2013)
-
Vol. 98 (2012)
-
Vol. 97 (2011)
-
Vol. 96 (2010)
-
Vol. 95 (2009)
-
Vol. 94 (2008)
-
Vol. 93 (2007)
-
Vol. 92 (2006)
-
Vol. 91 (2005)
-
Vol. 90 (2004)
-
Vol. 89 (2003)
-
Vol. 88 (2002)
-
Vol. 87 (2001)
-
Vol. 86 (2000)
-
Vol. 85 (1999)
-
Vol. 84 (1998)
-
Vol. 83 (1997)
-
Vol. 82 (1996)
-
Vol. 81 (1995)
-
Vol. 80 (1994)
-
Vol. 79 (1993)
-
Vol. 78 (1992)
-
Vol. 77 (1991)
-
Vol. 76 (1990)
-
Vol. 75 (1989)
-
Vol. 74 (1988)
-
Vol. 73 (1987)
-
Vol. 72 (1986)
-
Vol. 71 (1985)
-
Vol. 70 (1984)
-
Vol. 69 (1983)
-
Vol. 68 (1982)
-
Vol. 67 (1981)
-
Vol. 66 (1980)
-
Vol. 65 (1979)
-
Vol. 64 (1978)
-
Vol. 63 (1977)
-
Vol. 62 (1976)
-
Vol. 61 (1975)
-
Vol. 60 (1974)
-
Vol. 59 (1973)
-
Vol. 58 (1972)
-
Vol. 57 (1971)
-
Vol. 56 (1970)
-
Vol. 55 (1969)
-
Vol. 54 (1968)
-
Vol. 53 (1967)
-
Vol. 52 (1966)
-
Vol. 51 (1965)
-
Vol. 50 (1964)
-
Vol. 49 (1963)
-
Vol. 48 (1962)
-
Vol. 47 (1961)
-
Vol. 46 (1960)
-
Vol. 45 (1959)
-
Vol. 44 (1958)
-
Vol. 43 (1957)
-
Vol. 42 (1956)
-
Vol. 41 (1955)
キーワードランキング
06 Sep. (Last 30 Days)
鉄と鋼 Vol. 64 (1978), No. 13
Japan's Iron and Steel Industry with the Viewpoint of Energy Problem
Shuji YAMAMOTO
pp. 1817-1826
An Overall Study of Energy Consumption and Savings at Steelworks
Tadashi KATADA
pp. 1827-1838
Energy Saving in Ironmaking Processes
Shunsuke TAKAGI
pp. 1839-1856
他の人はこちらも検索
鉄と鋼 Vol.57(1971), No.1
鉄と鋼 Vol.68(1982), No.2
鉄と鋼 Vol.68(1982), No.15
Automatic Control of Fuel-Air Ratio in Soaking Pit
Katuhiko KABURAGI, Yosihiro UMEGATUJI
pp. 1857-1859
他の人はこちらも検索
Energy Saving in Steelmaking Processes
Takashi FUJII, Hirohiko NOZAKI, Yoshinao YAMAGISHI
pp. 1860-1878
A New Advanced Energy Center Computer System in Steel Works
Toshihisa HIKOSAKA, Norihiko SAITO, Hiroyuki TOKUYAMA, Munetoshi KURASHIGE, Yoshiyuki IENAGA, Mikio MORITA
pp. 1896-1905
抄録
For energy saving in integrated steel works, it is important not only to develop the technique in process (e. g., optimal control of heating furnaces and recovery of waste energy), but also to establish the following techniques for keeping energy demand/supply balances optimal.
(1) Daily production scheduling of works under the condition of balances of blast furnace gas, LD gas, electric power, steam and so on.
(2) on-line optimal controlling of demand/supply of energy while it varies time to time.
In Wakayama Works of Sumitomo Metal Industries, a new energy center compurer system has been developed to put these facilities in practice, and the expected energy saving has been achieved.
Present State of Top Gas Pressure Recovery Turbine Plants
Yozo SASAKI
pp. 1906-1913
抄録
Recently, top gas pressure recovery turbine plants have been installed in some steel making plants for energy saving. Eleven turbine plants have been operated including two test plants in Japan.
Total operation time of the first plant (Kawasaki Steel Corp. Mizushima Works No. 2 B.F) was approximately 26 400 hours.
There are two basic types of turbines for energy recovery; wet and dry. A radial flow turbine is of the wet type, and an axial flow turbine is of the dry type. Each turbine has special devices designed for prevention of corrosion, erosion and clogging of the turbine by dust and moisture-laden gas. These turbine systems have had no effect in any way on the blast furnace operation. Recovery turbine output of the first plant reaches 20 to 30% of blast blower input energy and its availability, approximately 85%, is over the average of self-thermal power plants in steel making plants.
In the future, economical plants will be developed for further improvement of turbine output and higher reliability of turbine systems including gas cleaning equipment.
他の人はこちらも検索
鉄と鋼 Vol.64(1978), No.13
The Coke Dry Quenching Process as the Energy-saving Technology
Takashi MORI, Takeo FUJIMURA, Seiichiro SATO
pp. 1914-1921
抄録
Nippon Kokan K.K. (NKK) undertook the so-called “Ogishima Project” in 1969 with a view of replacing the obsolete steel-making facilities at its Keihin Works with a modern steelmaking base to be constructed at Ogishima, a newly developed industrial area of the Keihin Works. Fortunately, the new C.D.Q. plant made a good start-up and operation. We would like to report its operating data and to consider the effects as the energy-saving technology. As a result, the NKK-Licensintorg C.D.Q. plant is showing high operational stability in coke quenching and is demonstrating excellent performance in energy-saving equipment.
他の人はこちらも検索
鉄と鋼 Vol.64(1978), No.13
Waste Heat Recovery from Sintering Plants
Noriyuki TANAKA
pp. 1922-1925
抄録
Currently, about 33% of the heat needed for production of sinter is discharged into the atmosphere in the form of exhaust air from sinter coolers. In the present-day sintering practice, one of the most effective ways to recover and utilize the waste heat is considered to use the exhaust air from coolers.
Recovery of the sensible heat of the exhaust air from coolers in now in widespread use in pelletizing plants, which, like sintering plants, agglomerate ore fines. With sintering plants, however, waste-heat recovery has been slow to find acceptance, for many reasons. One major reason is a difference in the agglomerating mechanism between the sintering process and the palletizing process. Another is that there have been too many uncertainties about the economic justifiability of energy-saving efforts in the sintering operation.
This report briefly describes the sintering equipment built in 1976 and discusses the effects of the waste-heat recovery technology incorporated in it.
The Dehumidifying System for the Blast Furnace Air
Kazutoshi OMODA
pp. 1926-1931
抄録
The dehumidifying system for the blast furnace air is going to adopt at a number of furnaces in Japan where the air humidity changes fairly with the seasons.
The type of the system has emplayed the principles of condensation or dehydration, or a combination of the two. It is able to condition the blast humidity in constant and low level with the system.
The advantage of this blast conditioning are to operate stably and to reduce the coke ration for the blast furnace practice.
This report classified the contents of these systems, and analized the effect of these system on the operation of the blast furnace.
New Dehumidification Plant of Direct Contact Cooler Type for Blast Furnace Air
Yoshimasa KAWAMOTO, Kichinosuke MATSUNAGA, Masayuki TAKEMURA, Takeji ASAI
pp. 1932-1936
抄録
There are thirteen units of blast furnace dehumidifiers now at works in our country. We have four methods: dry type lithium chloride method, wet type lithium chloride method, refrigerating method, and blower discharge side-cooling method. Each method has its merits and demerits. It seems there is no conclusive factor to select one from these four.
Among these dehumidifying methods, we gave attention to the blower discharge side-cooling method which had the most compact equipment. Then we developed the direct contact cooling method. Alter we manufactured a test plant on a scale of 1 to 20 and made an actual gas test, we equipped at No. 2 BF in our Kokura Steel Works in May this year. This plant is working satisfactorily.
We developed this method for the purpose of reducing the equipment cost and operating cost. Our direct contact cooling plant is constituted by the heat pipe type exchanger, direct contact air cooler, and high-efficiency mist separator.
In comparison with the conventional type, the installation space and equipment weight are about half. So we could reduce the equipment cost drastically.
OG Gas Recovery System and Its Gas Utilization
Takekazu YAMAGUCHI, Masaaki TAKAHASHI, Katsuhiro IJICHT, Toyoo MURATA
pp. 1937-1946
抄録
In these days when energy saving is urgently emphasized in steel works, LD gas recovery is expected to become more and more popular since it satisfied the requirement of the time as the most effective energy saving in the BOF plant.
60 percent or more of total energy contained in the gas generated in the BOF vessel can be recovered as usable gas.
Recently, the recovered LD gas accounts for approx.
6 percent of the total by-product gas in the integrated steel works.
In this paper, the concept, equipment, operation, and actual results of OG system are mentioned as the typical process for the gas recovery system.
Only a half year is enough to recover the additional investment for gas recovery facilities in case of two out of three BOF.
In Japan, more than 60 percent of BOF are operating with gas recovery system in 1977.
In foreign countries, BOF with gas recovery equipment are increasing in number too.
他の人はこちらも検索
ISIJ International Vol.55(2015), No.2
ISIJ International Vol.49(2009), No.11
ISIJ International Vol.54(2014), No.11
A Study on a Reduction in Fuel Consumption in Soaking Pits
Yooichi TAMURA, Kazuo KUNIOKA, Yukio HAGA
pp. 1947-1958
抄録
Conventional ordinary methods of heating steel ingots in soaking pits consist in setting the furnace temperature at about 1300°C upon charging hot steel ingots into a soaking pit, feeding the fuel at a maximum flow rate at the early period of heating, and gradually reducing the amount of the fuel when the furnace temperature has reached a set value. When the steel ingots heated for a definite period of time have reached the uniform temperature throughout, the soaking process is completed and they are extracted and rolled. For this reason, large quantities of heat are given off as the sensible heat of exhaust gas and as heat radiation from the furnace. Thus this situation is not desirable from the standpoint of energy-saving. To cope with this high fuel price age after the oil shock, the authors have studied heating methods and developed “the inverted-L type heating method”, a new method entirely different from conventional heating methods.
This method consists in heating steel ingots with the fuel at a minimum definite flow rate required for heat balance until the latent heat of solidification has spread throughout the steel ingots, increasing the fuel flow rate just before extraction, and thereby abruptly heating the surface.
The average unit fuel consumption decreased from 183×103 kcal/t in 1973 to 111×103 kcal/t in 1977 when this method was adopted, thus showing a decrease of 34%.
Development of the Slab Cooling Boiler in the Steel Plant
Yoshiaki SHINOHARA, Akito TAKAHASHI, Norihisa SHIRAISHI
pp. 1959-1967
抄録
Hot slabs after the slabbing mill are at a mean temperature of 1 000°C and have the sensible heat of 160×103 kcal/t-slab. The main features of a Slab Cooling Boiler (SCB) are the recovery of the sensible heat to steam (16kg/cm2 G) by mean of heat radiation from the surface of hot slabs, and continuation of cooling process of almost every kind of slab.
The first installation of an SCB was completed at Slabbing Mill No. 2 in Mizushima Works of Kawasaki Steel Corporation and it has been operating successfully since March, 1976.
The capacity of the heat recovery in this SCB is 72000 kcal/t-slab. It is equal to or greater than the heat consumption of rimmed and semikilled steel in the soaking pit.
This paper discusses the basic heat transfer experiments performed under this development, the basic planning of the installation, the outlines of the system, and some results of the operations.
他の人はこちらも検索
鉄と鋼 Vol.64(1978), No.1
鉄と鋼 Vol.65(1979), No.7
鉄と鋼 Vol.64(1978), No.11
On the Minimum Specific Heat Consumption of the Reheating Furnace in the Iron and Steel Industry and a Calculation of It
Yoshiro WADA
pp. 1988-1995
抄録
The influence of various factors were considered on the specific heat consumption of reheating furnace in the iron and steel industry. The value of minimum specific heat consumption on the continuous slab reheating furnace which will be built in future was estimated at 266×103kcal/t.
This valus was obtained by mean of calculation and analysis based on the heat balance of a continuous slab rehaeting furnace which is operating with high heat efficiency in this country at present. Further, if the higher heat recovery recuperater is developed, this value will be reduced to about 245×103kcal/teasily.
他の人はこちらも検索
鉄と鋼 Vol.64(1978), No.13
Development of Reheating Furnace with Waste Gas Jet Preheating Equipment
Yozo FUKUHISA, Jiro YAMASAKI, Akihiro NAKAMA, Ryuzo OKUNO, Syozo MINAMI
pp. 1996-2005
抄録
Slab reheating furnace with waste gas jet preheating equipment is purposed for reductin of energy consumption and the improvement of productivity. This paper describes the utilization of this equipment with special reference to the reduction of energy consumption.
The high heat transfer coefficient is obtained by gas jet. The Waste gas of furnace is blown on the charged slabs at a high speed to preheat slabs. As a result, the heat of waste gas is utilized more by the new equipment than by the conventional furnace. Kawasaki Heavy Industries Ltd. has studied the heat transfer of gas jet under the conditions of a actual furnace and the application method of gas jet.
This equipment has been applied to No. 1 reheating furnace of new plate mill of Oita Works. Since January, 1977, the reheating furnace has been operated well without any equipment trouble and has improved energy consumption.
The Rotary Hearth Furnace Designed for Saving Energy
Kazuyoshi YAMASHIMA, Kazuo TSUMURA, Shin-ichi HAYASHI, Takao SASAKI
pp. 2006-2011
抄録
A Rotary Hearth Heating Furnace has been designed and installed for both saving energy and reducing NOx emission. The characteristic of this furnace is as follows.
(1) The ceramic fiber lining is used.
(2) The Low-NOx Burner with high efficient combustion is developed.
(3) The combusion control with O2% is adopted.
As a result of those improvement of the efficiency, the amount of town-gas consumption was reduced to 70% and that of NOx emission to 40% of that by the conventional type furnace.
This paper refers to the outline of this new furnace.
他の人はこちらも検索
鉄と鋼 Vol.52(1966), No.9
ISIJ International Vol.29(1989), No.10
ISIJ International Vol.53(2013), No.6
Hot Direct Rolling
Morio TAKAHASHI, Yoshiro MASUI
pp. 2012-2019
抄録
For energy saving, following new hot rolling processes are very useful. One is the hot rolling system which the slab is passed directly without cooling from slabbing mill to hot strip mill (called Hot Direct Rolling). The other is the system which the slab is charged into reheating furnace in hot condition and then is supplied to hot strip mill (called Hot Charge Rolling). Since energy crisis, in 1974, in steel industries, various utmost efforts for the development of these new processes have been made, so that these techniques were established in the mass production scale and were adopted in seven iron workers in Japan.
In this report, for the purpose of cost minimizing from steel making shop to rolling shop, hot direct rolling process and also future aspects of further developments are described.
Color TV System for Inspection of Hot Slabs under Slabbing
Toshio SHIRAIWA, Tatsuo HIROSHIMA, Ken-ichi MATSUI, Yukio KUBO, Kozabro OZAKI
pp. 2020-2025
抄録
A color TV system for inspection of hot slabs has been developed. The system consists of a color TV camera with a mechanical shutter, video disk recorders, and color monitors.
A hot slab under slabbing is shot to be composed of five pictures, and the video disk recorders record the five pictures of the slab. These pictures are simultaneously displayed on five large color monitors. The inspector can easily see surface flaws on the still enlarged pictures.
This system has been installed in Wakayama Steel Works of Sumitomo Metal Ind., Ltd. since 1976, and is used on hot direct rolling from the slabbing mill to the hot strip mill.
Energy-saving by Hot Charging and Direct Rolling in the Manufacturing Process of Wide Flange Beams
Hanji OBA, Yotaro TAJIMA, Toyoichi TANIZAKI, Itaru SUZUKI
pp. 2026-2036
抄録
Owing mainly to the development of beam-blank hot charging and direct rolling, the Nippon Steel Corporation has succeeded in saving 50% of the fuel consumed when the oil crisis happened, at the wide flange beam mill in Sakai Works.
These processes have four problems, namely surface-defects of products, rolling temperature, mechanical properties of products and production schedule. The results of the study on these problems are as follows.
(1) Surface-defects were mainly caused by blow holes and influenced by rolling temperature. These have been prevented by optimizing deoxidization, hot scarfing and rolling temperature.
(2) The adequate rolling temperature could be secured by altering the size of the beam-blank based on a simulation for the optimum pass schedule.
(3) On mechanical properties, there is little difference between products (JIS SS41 class) made by direct rolling and by ordinary process.
(4) The application rate of hot charging and direct rolling has been raised exceedingly by the introduction of a production control computer system.
The Recent Development of Refractories and Insulating Materials on the Point of Energy Saving
Takeshi HAYASHI
pp. 2037-2056
A Note on Reducing of Energy Consumption in Rolling Process of Steel
Junji KIHARA
pp. 2057-2060
他の人はこちらも検索
鉄と鋼 Vol.64(1978), No.1
鉄と鋼 Vol.65(1979), No.7
鉄と鋼 Vol.64(1978), No.11
論文アクセスランキング
06 Sep. (Last 30 Days)
-
Perspectives on the Promising Pathways to Zero Carbon Emissions in the Steel Industry toward 2050
ISIJ International Vol.65(2025), No.2
-
溶鋼中での各種酸化物系介在物の成長・除去と凝集
鉄と鋼 Vol.111(2025), No.11
-
Finite Element Analysis of Bubble Growth and Particle Swelling during Coal Pyrolysis
ISIJ International Vol.65(2025), No.9
-
通電誘起高速共晶反応によるAl/Cu異材接合形成につながる界面挙動
溶接学会論文集 Vol.43(2025), No.2
-
Corrosion Behavior of Carbon Steel under Soil Drying Conditions
ISIJ International 早期公開
-
980 MPa級高張力鋼板の固相抵抗スポット接合
鉄と鋼 早期公開
-
-
-
Copper removal of liquid steel containing 0.25 % carbon using Fe2O3-CaCl2-SiO2 flux
ISIJ International 早期公開
-
Evaluation of Feature Selection Methods for Oxygen Supply Prediction in BOF Steelmaking
ISIJ International 早期公開
この機能はログイン後に利用できます。
下のボタンをクリックしてください。