鉄と鋼 Vol. 61 (1975), No. 15
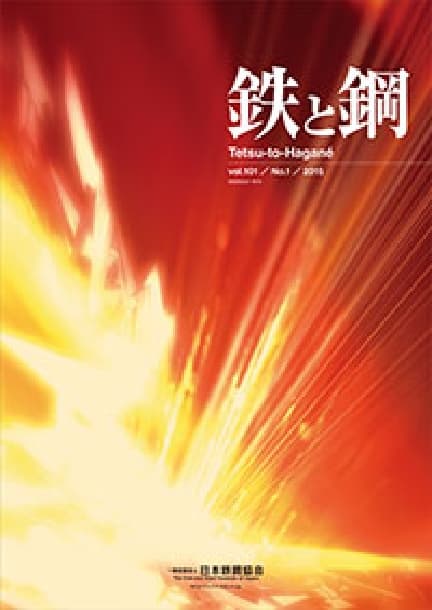
Grid List Abstracts
オンライン版ISSN: | 1883-2954 |
冊子版ISSN: | 0021-1575 |
発行機関: | The Iron and Steel Institute of Japan |
Backnumber
-
Vol. 111 (2025)
-
Vol. 110 (2024)
-
Vol. 109 (2023)
-
Vol. 108 (2022)
-
Vol. 107 (2021)
-
Vol. 106 (2020)
-
Vol. 105 (2019)
-
Vol. 104 (2018)
-
Vol. 103 (2017)
-
Vol. 102 (2016)
-
Vol. 101 (2015)
-
Vol. 100 (2014)
-
Vol. 99 (2013)
-
Vol. 98 (2012)
-
Vol. 97 (2011)
-
Vol. 96 (2010)
-
Vol. 95 (2009)
-
Vol. 94 (2008)
-
Vol. 93 (2007)
-
Vol. 92 (2006)
-
Vol. 91 (2005)
-
Vol. 90 (2004)
-
Vol. 89 (2003)
-
Vol. 88 (2002)
-
Vol. 87 (2001)
-
Vol. 86 (2000)
-
Vol. 85 (1999)
-
Vol. 84 (1998)
-
Vol. 83 (1997)
-
Vol. 82 (1996)
-
Vol. 81 (1995)
-
Vol. 80 (1994)
-
Vol. 79 (1993)
-
Vol. 78 (1992)
-
Vol. 77 (1991)
-
Vol. 76 (1990)
-
Vol. 75 (1989)
-
Vol. 74 (1988)
-
Vol. 73 (1987)
-
Vol. 72 (1986)
-
Vol. 71 (1985)
-
Vol. 70 (1984)
-
Vol. 69 (1983)
-
Vol. 68 (1982)
-
Vol. 67 (1981)
-
Vol. 66 (1980)
-
Vol. 65 (1979)
-
Vol. 64 (1978)
-
Vol. 63 (1977)
-
Vol. 62 (1976)
-
Vol. 61 (1975)
-
Vol. 60 (1974)
-
Vol. 59 (1973)
-
Vol. 58 (1972)
-
Vol. 57 (1971)
-
Vol. 56 (1970)
-
Vol. 55 (1969)
-
Vol. 54 (1968)
-
Vol. 53 (1967)
-
Vol. 52 (1966)
-
Vol. 51 (1965)
-
Vol. 50 (1964)
-
Vol. 49 (1963)
-
Vol. 48 (1962)
-
Vol. 47 (1961)
-
Vol. 46 (1960)
-
Vol. 45 (1959)
-
Vol. 44 (1958)
-
Vol. 43 (1957)
-
Vol. 42 (1956)
-
Vol. 41 (1955)
キーワードランキング
04 Sep. (Last 30 Days)
鉄と鋼 Vol. 61 (1975), No. 15
酸化鉄の還元と浸炭の相関に関する研究
李 海洙
pp. 3041-3049
抄録
The relationship between reduction and carburization has been investigated, by way of the reduction experiments of highly pure chemical hematite (Fe2O3) at high temperatures in CO gas as well as in solidcarbon-N2 atmosphere, followed by the microscopic examination on various samples of reduced iron oxide. The results are summarized as follows;
1) In the CO gas atmosphere the rate of reduction becomes rather slow at the temperature higher than about 1100°C, whereas in the solid-carbon-N2 atmosphere the reduction proceeds with a notably high speed in the same region of the temperature. Namely a contrast effect on the rate of reduction is shown between these two atmospheres.
2) In either CO gas atmosphere and solid-carbon-N2 atmosphere at higher temperature, the carburization does not begin to proceed unless the reduction degree exceeds 90% (for the sample of φ10mm×10mm).
3) The lattice constant of α-Fe (110) yielded by reduction varies with the progress of reduction.
The lattice constant has a comparatively larger value at the beginning of reduction than the usual one, and tends gradually with the progress of reduction to a constant value slightly larger than the usual one. This gradual change of the lattice constant seems to stop when the process of carburization which follows up reduction begins.
4) The process of carburization is analyzed by means of the following diffusion model:
1/D·∂C/∂t=1/r·∂C/∂r+∂2C/∂r2+∂2C/∂Z2
The result shows that the coincidence between the calculated values and experimental ones satis factory.
5) As a consequence of the above theoretical analysis for the process of carburization, it has been shown that the diffusion coefficient D has the nearly same value 0.79×10-4 (cm/sec) in either case of 1200°C and 1300°C, on the other hand, the (equivalent) rate constant k is computed 2.61×10-4 (cm/sec) for the case of 1200°C and 3.15×10-4 (cm/sec) for the case of 1300°C.
Study of the Relation between Reduction and Carburization in the Reduction of Iron Oxide
HeSu REE
pp. 3041-3049
抄録
The relationship between reduction and carburization has been investigated, by way of the reduction experiments of highly pure chemical hematite (Fe2O3) at high temperatures in CO gas as well as in solidcarbon-N2 atmosphere, followed by the microscopic examination on various samples of reduced iron oxide. The results are summarized as follows;
1) In the CO gas atmosphere the rate of reduction becomes rather slow at the temperature higher than about 1100°C, whereas in the solid-carbon-N2 atmosphere the reduction proceeds with a notably high speed in the same region of the temperature. Namely a contrast effect on the rate of reduction is shown between these two atmospheres.
2) In either CO gas atmosphere and solid-carbon-N2 atmosphere at higher temperature, the carburization does not begin to proceed unless the reduction degree exceeds 90% (for the sample of φ10mm×10mm).
3) The lattice constant of α-Fe (110) yielded by reduction varies with the progress of reduction.
The lattice constant has a comparatively larger value at the beginning of reduction than the usual one, and tends gradually with the progress of reduction to a constant value slightly larger than the usual one. This gradual change of the lattice constant seems to stop when the process of carburization which follows up reduction begins.
4) The process of carburization is analyzed by means of the following diffusion model:
1/D·∂C/∂t=1/r·∂C/∂r+∂2C/∂r2+∂2C/∂Z2
The result shows that the coincidence between the calculated values and experimental ones satis factory.
5) As a consequence of the above theoretical analysis for the process of carburization, it has been shown that the diffusion coefficient D has the nearly same value 0.79×10-4 (cm/sec) in either case of 1200°C and 1300°C, on the other hand, the (equivalent) rate constant k is computed 2.61×10-4 (cm/sec) for the case of 1200°C and 3.15×10-4 (cm/sec) for the case of 1300°C.
質量分析法による1600℃におけるFe-V, Fe-V-Cr合金の熱力学的研究
古川 武, 加藤 栄一
pp. 3050-3059
抄録
The activities and partial molar heats of mixing in the Fe-V system and the activities of Fe and V in the Fe-V-Cr system at 1600°C have been determined. The analysis of Knudsen cell effusates with a mass spectrometer was applied as the experimental technique. The ion current ratio for the alloy components was measured through the whole range of composition for the Fe-V system and in the range of composition, NV≤0.3 NCr≤0.2, for the Fe-V-Cr system, and the thermodynamic values were calculated by the modified GIBBS-DUHEM equation. The Fe-V binary system exhibits negative deviation from ideal behaviour. The results for the Fe-V binary system can be partially represented by the equations
log γV =-1.02 N2Fe+0.24 (0≤NV≤0.20)
log γFe=-0.11 N2V-0.31 (0≤NFe≤0.02)
The results for the Fe-V-Cr ternary system can be represented by the equations
log γV=-0.42+0.70 NCr (NV=0.2, 0≤NCr≤0.2)
log γFe=-0.04-0.18 NCr (NV=0.2, 0≤NCr≤0.2)
log γV=-0.28+0.48 NCr (NV=0.3, 0≤NCr≤0.2)
log γFe=-0.08-0.20 NCr (NV=0.3, 0≤NCr≤0.2)
Thermodynamic Properties of the Fe-V, Fe-V-Cr Alloys at 1600°C by Mass-Spectrometry
Takeshi FURUKAWA, Eiichi KATO
pp. 3050-3059
抄録
The activities and partial molar heats of mixing in the Fe-V system and the activities of Fe and V in the Fe-V-Cr system at 1600°C have been determined. The analysis of Knudsen cell effusates with a mass spectrometer was applied as the experimental technique. The ion current ratio for the alloy components was measured through the whole range of composition for the Fe-V system and in the range of composition, NV≤0.3 NCr≤0.2, for the Fe-V-Cr system, and the thermodynamic values were calculated by the modified GIBBS-DUHEM equation. The Fe-V binary system exhibits negative deviation from ideal behaviour. The results for the Fe-V binary system can be partially represented by the equations
log γV =-1.02 N2Fe+0.24 (0≤NV≤0.20)
log γFe=-0.11 N2V-0.31 (0≤NFe≤0.02)
The results for the Fe-V-Cr ternary system can be represented by the equations
log γV=-0.42+0.70 NCr (NV=0.2, 0≤NCr≤0.2)
log γFe=-0.04-0.18 NCr (NV=0.2, 0≤NCr≤0.2)
log γV=-0.28+0.48 NCr (NV=0.3, 0≤NCr≤0.2)
log γFe=-0.08-0.20 NCr (NV=0.3, 0≤NCr≤0.2)
質量分析法による溶融Fe-Ti合金の熱力学的研究
古川 武, 加藤 栄一
pp. 3060-3068
抄録
The activities and partial molar heats of mixing have been determined in the Fe-Ti system at 1600°C. The experimental teqhnique is the same as described in the paper on the Fe-V and Fe-V-Cr systems, which has been reported previously.
The selection of oxide crucible material for the alloy and the effect of a small amount of added substance for the purpose of lowering the oxygen partial pressure in the cell have been discussed. The system exhibits a negative deviation from the ideal behaviour. The results can be partially represented by the equation
logγFe=-0.89N2T1-0.48 (NFe≤0.10)
logγTi=-2.29N2Fe+0.53 (NTi≤0.10)
Thermodynamic Properties of Liquid Fe-Ti Alloys by Mass-Spectrometry
Takeshi FURUKAWA, Eiichi KATO
pp. 3060-3068
抄録
The activities and partial molar heats of mixing have been determined in the Fe-Ti system at 1600°C. The experimental teqhnique is the same as described in the paper on the Fe-V and Fe-V-Cr systems, which has been reported previously.
The selection of oxide crucible material for the alloy and the effect of a small amount of added substance for the purpose of lowering the oxygen partial pressure in the cell have been discussed. The system exhibits a negative deviation from the ideal behaviour. The results can be partially represented by the equation
logγFe=-0.89N2T1-0.48 (NFe≤0.10)
logγTi=-2.29N2Fe+0.53 (NTi≤0.10)
他の人はこちらも検索
鉄と鋼 Vol.60(1974), No.3
鉄と鋼 Vol.77(1991), No.2
MATERIALS TRANSACTIONS Vol.60(2019), No.9
平衡状態図に基づいた鉄鋼の凝固モデル
渡辺 一雄
pp. 3069-3076
抄録
A mathematical model for the estimation of the solidification processes of steels of various carbon concentrations has been made.
In this model, it is assumed that the latent heat release is proportional to the solid precipitation volume, and the solid precipitations of each δ and γ phases and also the latter at the peritectic point based on the Fe-C equilibrium phase diagram are considered.
The calculated time-temperature curve shows the constant-temperature time at the liquidus, and the higher the initial liquid carbon concentration, the shorter is the constant-temperature time.
From the distributions of the solid fraction for various initial liquid carbon concentrations, it is induced that the initial high carbon concentration is one of the factors to promote the equiaxed grain growth, on the contrary the low carbon concentration to promote the columnar grain growth.
A Mathematical Model of Solidification Based on the Fe-C System Equilibrium Phase Diagram
Kazuo WATANABE
pp. 3069-3076
抄録
A mathematical model for the estimation of the solidification processes of steels of various carbon concentrations has been made.
In this model, it is assumed that the latent heat release is proportional to the solid precipitation volume, and the solid precipitations of each δ and γ phases and also the latter at the peritectic point based on the Fe-C equilibrium phase diagram are considered.
The calculated time-temperature curve shows the constant-temperature time at the liquidus, and the higher the initial liquid carbon concentration, the shorter is the constant-temperature time.
From the distributions of the solid fraction for various initial liquid carbon concentrations, it is induced that the initial high carbon concentration is one of the factors to promote the equiaxed grain growth, on the contrary the low carbon concentration to promote the columnar grain growth.
鋼のミクロ凝固組織形成に関する一考察
大橋 徹郎, W. A. FISCHER
pp. 3077-3091
抄録
Microstructures of steels during unidirectional solidification in zone melting have been investigated by mainly observation of solid/liquid interface.
The solidification rate was in the range of 3-60×10-4cm/sec. Fe-C and Fe-S systems were mainly investigated, and the specimen dimension was 35mm in diameter and 600 mm in length.
After observations of solidification structures, the formation and stability of solid/liquid interface were discussed theoreticaly under the consideration of solute redistribution and thermal flow.
With increase of the supercoal in liquid iron near the interface, solidification front changes from planar to cellular, and finally to dendritic form. Critical conditions for this interface transitions were determined by solute concentration, solidification rate, and temperature gradient. Especially the interfacial tension between solid/liquid iron was intended as a primary foctor for cellular-dendritic transition.
The interfacial tension of iron containing carbon was estimated around 200-600 erg/cm2 with measurement of interfacial curvatures.
There was a good agreement between experimental observations and theoretical estimations for critical conditions of interface transitions.
Formation of Micro Solidification Structures of Steels
Tetsuro OHASHI, W. A. FISCHER
pp. 3077-3091
抄録
Microstructures of steels during unidirectional solidification in zone melting have been investigated by mainly observation of solid/liquid interface.
The solidification rate was in the range of 3-60×10-4cm/sec. Fe-C and Fe-S systems were mainly investigated, and the specimen dimension was 35mm in diameter and 600 mm in length.
After observations of solidification structures, the formation and stability of solid/liquid interface were discussed theoreticaly under the consideration of solute redistribution and thermal flow.
With increase of the supercoal in liquid iron near the interface, solidification front changes from planar to cellular, and finally to dendritic form. Critical conditions for this interface transitions were determined by solute concentration, solidification rate, and temperature gradient. Especially the interfacial tension between solid/liquid iron was intended as a primary foctor for cellular-dendritic transition.
The interfacial tension of iron containing carbon was estimated around 200-600 erg/cm2 with measurement of interfacial curvatures.
There was a good agreement between experimental observations and theoretical estimations for critical conditions of interface transitions.
Fe-C合金の冷延, 再結晶集合組織
野村 伸吾, 柚鳥 登明, 福塚 淑郎
pp. 3092-3105
抄録
The influence of carbon content on cold rolling and annealing textures of Fe-C alloys containing 0.003, 0.011, 0.021 wt%C has been studied. To avoid the effects of pre-existing grain boundary and texture, hot rolled sheets with coarse grain and random texture are used. The results obtained are as follows.
(1) The structure and the texture of cold rolled sheet are largely affected by the amount of carbon in solution. When the amount of carbon in solution is small, sharp cell structure and rolling texture are formed. In the deformed grains with {111} planes parallel to sheet surface, crystal rotation from {111} <112> to {111} <110> around the <111> //N. D. axis is dominant. The main components of the annealing texture are {111} <112> and {111} <110>. When the amount of carbon in solution is large, cell structure and rolling texture are diffuse in the cold rolled sheet. In this case, crystal rotation from {111} <112> to {110} <001> around the <110> //T. D. axis is indicated to be dominant in the {111} <112> deformed matrix. The main component of the recrystallization texture is {110} <001>.
(2) The effect of reducing carbon in solution by precipitation treatment before cold rolling on the formation of rolling and annealing textures is more important than that of the precipitated cementite itself.
Cold-Rolling and Annealing Textures in Fe-C Alloys
Shingo NOMURA, Toshiaki YUTORI, Toshiro FUKUTSUKA
pp. 3092-3105
抄録
The influence of carbon content on cold rolling and annealing textures of Fe-C alloys containing 0.003, 0.011, 0.021 wt%C has been studied. To avoid the effects of pre-existing grain boundary and texture, hot rolled sheets with coarse grain and random texture are used. The results obtained are as follows.
(1) The structure and the texture of cold rolled sheet are largely affected by the amount of carbon in solution. When the amount of carbon in solution is small, sharp cell structure and rolling texture are formed. In the deformed grains with {111} planes parallel to sheet surface, crystal rotation from {111} <112> to {111} <110> around the <111> //N. D. axis is dominant. The main components of the annealing texture are {111} <112> and {111} <110>. When the amount of carbon in solution is large, cell structure and rolling texture are diffuse in the cold rolled sheet. In this case, crystal rotation from {111} <112> to {110} <001> around the <110> //T. D. axis is indicated to be dominant in the {111} <112> deformed matrix. The main component of the recrystallization texture is {110} <001>.
(2) The effect of reducing carbon in solution by precipitation treatment before cold rolling on the formation of rolling and annealing textures is more important than that of the precipitated cementite itself.
粗大粒界析出処理中に圧延加工した18Cr-12Ni鋼の高温強さ
武藤 功, 山崎 道夫
pp. 3106-3118
抄録
Coarse and irregular precipitates of carbide along grain boundaries are now well known to increase creep rupture strengths of austenitic heat resisting steels, through the effect of retarding grain boundary cracking. In an 18Cr-12Ni-0.3C steel, for instance, the coarse carbide precipitation occurs when the steel is solution-treated at such a temperature that makes the carbide dissolve completely (the first step temperature), directly cooled to the second step temperature that is a little lower than the solvus temperature of the carbide, held at the second step temperature, if necessary, and water-quenched.
In the present paper, the effect of rolling deformation at the second step of the treatment mentioned above has been studied. The purpose of this thermo-mechanical treatment is two fold; it is intended first that the irregularity in grain boundaries may be increased by the formation of small recrystallized grains along the original grain boundary or by the bulging of a grain to another, and secondly that the proof stress may be increased by the work hardening without recrystallization. The first aim is not realized due to the occurence of unexpected types of recrystallization, while the second one is achieved.
Thermo-Mechanical Treatments of 18Cr-12Ni Steel Containing Coarse Grain-Boundary Precipitates
Isao MUTO, Michio YAMAZAKI
pp. 3106-3118
抄録
Coarse and irregular precipitates of carbide along grain boundaries are now well known to increase creep rupture strengths of austenitic heat resisting steels, through the effect of retarding grain boundary cracking. In an 18Cr-12Ni-0.3C steel, for instance, the coarse carbide precipitation occurs when the steel is solution-treated at such a temperature that makes the carbide dissolve completely (the first step temperature), directly cooled to the second step temperature that is a little lower than the solvus temperature of the carbide, held at the second step temperature, if necessary, and water-quenched.
In the present paper, the effect of rolling deformation at the second step of the treatment mentioned above has been studied. The purpose of this thermo-mechanical treatment is two fold; it is intended first that the irregularity in grain boundaries may be increased by the formation of small recrystallized grains along the original grain boundary or by the bulging of a grain to another, and secondly that the proof stress may be increased by the work hardening without recrystallization. The first aim is not realized due to the occurence of unexpected types of recrystallization, while the second one is achieved.
中炭素低合金鋼のベイナイトの靱性に及ぼす合金元素の影響
中島 宏興, 荒木 透
pp. 3119-3128
抄録
The effect of C (0.25-0.45%), Ni (0-2.6%), Mo (0-0.5%) and Cr (0-2.2%) contents on the toughness of the as formed and tempered bainite was investigated in 0.4%C-0.8%Mn-1.1%Cr-0.25% Mo steels, and factors which affect the toughness of bainite were discussed. Bainite was formed in the isothermal transformation. Increase of C, Ni and Cr contents and rise of transformation temperature raised the transition temperature of bainite. The results were attributed to the increase of both fracture facet size and carbide length and the latter was more deteriorate. In the increase of Cr content, another factor might be also necessary to be taken into account for the full interpretation of the results. Addition of molybdenum lowered the transition temperature of tempered bainite mainly by the relief of the temper embrittlement.
Effect of Alloying Elements on the Toughness of Bainite in Medium Carbon Low Alloy Steels
Hirooki NAKAJIMA, Toru ARAKI
pp. 3119-3128
抄録
The effect of C (0.25-0.45%), Ni (0-2.6%), Mo (0-0.5%) and Cr (0-2.2%) contents on the toughness of the as formed and tempered bainite was investigated in 0.4%C-0.8%Mn-1.1%Cr-0.25% Mo steels, and factors which affect the toughness of bainite were discussed. Bainite was formed in the isothermal transformation. Increase of C, Ni and Cr contents and rise of transformation temperature raised the transition temperature of bainite. The results were attributed to the increase of both fracture facet size and carbide length and the latter was more deteriorate. In the increase of Cr content, another factor might be also necessary to be taken into account for the full interpretation of the results. Addition of molybdenum lowered the transition temperature of tempered bainite mainly by the relief of the temper embrittlement.
鋼の焼入れにおける逆硬化現象について
清水 信善, 田村 今男
pp. 3129-3138
抄録
Quenching of steels normally produces heighest hardness at the surface and successively lower hardness into the center of the article. In oil quenching of bearing grade steels, however, an inverse hardness distribution (called inverse quench-hardening, hereinafter) is sometimes found. In this investigation, the inverse quench-hardening was examined. The main results are as follows
(1) The inverse quench-hardening is caused by a rapid change of cooling rate during cooling. This phenomenon is particularly liable to occur when the steels are quenched into oil having long vapor blanket cooling stage and a low characteristic temperature.
(2) This phenomenon occurs more often at the upper part than the lower part of the article treated. This is due to that the vapor blanket cooling stage is longer at the upper part than the lower part.
(3) The inverse quench-hardening is attributed to higher consumption of incubation period for perlitic transformation at the surface than at the center of the steel during vapor blanket cooling stage in quenching. In such a case, the hardening at the surface becomes difficult even by rapid cooling in the following boiling stage.
On the Inverse Quench-Hardening of Steel
Nobuyoshi SHIMIZU, Imao TAMURA
pp. 3129-3138
抄録
Quenching of steels normally produces heighest hardness at the surface and successively lower hardness into the center of the article. In oil quenching of bearing grade steels, however, an inverse hardness distribution (called inverse quench-hardening, hereinafter) is sometimes found. In this investigation, the inverse quench-hardening was examined. The main results are as follows
(1) The inverse quench-hardening is caused by a rapid change of cooling rate during cooling. This phenomenon is particularly liable to occur when the steels are quenched into oil having long vapor blanket cooling stage and a low characteristic temperature.
(2) This phenomenon occurs more often at the upper part than the lower part of the article treated. This is due to that the vapor blanket cooling stage is longer at the upper part than the lower part.
(3) The inverse quench-hardening is attributed to higher consumption of incubation period for perlitic transformation at the surface than at the center of the steel during vapor blanket cooling stage in quenching. In such a case, the hardening at the surface becomes difficult even by rapid cooling in the following boiling stage.
低摩擦速度における鉄鋼材料の摩耗と摩擦面温度の関係
川本 信, 新谷 進, 岡林 邦夫
pp. 3139-3148
抄録
The wear characteristics of 0.42%C steel, 17Cr stainless steel and pearlitic cast iron at relatively low sliding speed have been examined by the pin-disc type wear machine in relation to the sliding surface temperature, and the general relation between wear of iron and steel and the sliding surface temperature has been estimated from this experiment and the previous reports. Both the temperature of actual contacting regions (flash temperature) and the mean temperature of apparent contacting surface were considered as the sliding surface temperature. To measure the flash temperature by the dynamic thermoelectromotive force method, 0.42%C steel and cast iron were rubbed against 17Cr stainless steel and 17Cr stainless steel was rubbed against 0.60%C steel.
It has become clear that the wear characteristics of iron and steel can be understood systematically by the mutual relation between the flash temperature and the mean temperature of the sliding surface. Regardless of the sliding condition, when the flash temperature is about 300°C, the maximum point of wear by the severe wear appears, and wear being a very little below 250°C. When the flash temperature is so high as some of the actual contacting regions reach or approach to the melting point, wear depends on the mean temperature. It occurs slightly at relatively low mean temperature and the scuffing occurs at relatively high mean temperature.
Relation between Wear of Iron and Steel and Sliding Surface Temperature
Makoto KAWAMOTO, Susumu SHINTANI, Kunio OKABAYASHI
pp. 3139-3148
抄録
The wear characteristics of 0.42%C steel, 17Cr stainless steel and pearlitic cast iron at relatively low sliding speed have been examined by the pin-disc type wear machine in relation to the sliding surface temperature, and the general relation between wear of iron and steel and the sliding surface temperature has been estimated from this experiment and the previous reports. Both the temperature of actual contacting regions (flash temperature) and the mean temperature of apparent contacting surface were considered as the sliding surface temperature. To measure the flash temperature by the dynamic thermoelectromotive force method, 0.42%C steel and cast iron were rubbed against 17Cr stainless steel and 17Cr stainless steel was rubbed against 0.60%C steel.
It has become clear that the wear characteristics of iron and steel can be understood systematically by the mutual relation between the flash temperature and the mean temperature of the sliding surface. Regardless of the sliding condition, when the flash temperature is about 300°C, the maximum point of wear by the severe wear appears, and wear being a very little below 250°C. When the flash temperature is so high as some of the actual contacting regions reach or approach to the melting point, wear depends on the mean temperature. It occurs slightly at relatively low mean temperature and the scuffing occurs at relatively high mean temperature.
住友金属鋼管製造所50t Elo-Vac設備と操業について
小谷 良男, 池田 隆果, 石原 和雄, 阪根 武良
pp. 3149-3155
抄録
The vacuum treatment is now a necessary process especially for high grade steel. In our works, the stream degassing of ingot had been applied for producing seamless pipe with heavy wall and large diameter. However our vacuum degassing process had not enough capacity to be applied for all necessary heats. Thus, we have newly installed 50 t Elo-Vac Unit of the ladle degassing process, called Witten process which is possible to treat both normal degassing for all heats and vacuum oxygen decarburization for stainless steel. Our 50t Elo-Vac Unit has been operated since October, 1972.
At present, operations have been performed satisfactorily and we have produced approximately 49000 t stainless steel by V. O. D. process and 45000t carbon and alloy steel by normal degassing till December, 1974. This unit is making a great contribution toward keeping high quality as well as saving production cost in manufacturing stainless steel. This paper describes the outline and operations of the Elo-Vac Unit, especially vacuum refining process of stainless steel.
Outline and Operation of 50t Elo-Vac Unit at Steel Tube Works of Sumitomo Metal Iudustries, Ltd.
Yoshio KOTANI, Takami IKEDA, Kazuo ISHIHARA, Takeyoshi SAKANE
pp. 3149-3155
抄録
The vacuum treatment is now a necessary process especially for high grade steel. In our works, the stream degassing of ingot had been applied for producing seamless pipe with heavy wall and large diameter. However our vacuum degassing process had not enough capacity to be applied for all necessary heats. Thus, we have newly installed 50 t Elo-Vac Unit of the ladle degassing process, called Witten process which is possible to treat both normal degassing for all heats and vacuum oxygen decarburization for stainless steel. Our 50t Elo-Vac Unit has been operated since October, 1972.
At present, operations have been performed satisfactorily and we have produced approximately 49000 t stainless steel by V. O. D. process and 45000t carbon and alloy steel by normal degassing till December, 1974. This unit is making a great contribution toward keeping high quality as well as saving production cost in manufacturing stainless steel. This paper describes the outline and operations of the Elo-Vac Unit, especially vacuum refining process of stainless steel.
将来の製鉄プラントと研究計画に関する一提案
Sven EKETORP
pp. 3156-3166
第5回日ソ製鋼物理化学合同シンポジウム報告
日本鉄鋼協会訪ソ学術使節団
pp. 3167-3188
Report of the 5th Japan-USSR Joint Symposium on Physical Chemistry of Metallurgical Processes
The Scientific Delegation of the Iron and Steel
pp. 3167-3188
抄録
室屋 正広, 古川 武, 郡司 好喜, 高橋 謙治, 石田 寿秋, 小口 征男, 垣生 泰弘, 菊池 実, 宮地 博文, 田中 徹, 武田 修一, 藤井 哲雄, 松村 祐治, 浜上 和久, 田中 徹
pp. 3189-3195
抄録
室屋 正広, 古川 武, 郡司 好喜, 高橋 謙治, 石田 寿秋, 小口 征男, 垣生 泰弘, 菊池 実, 宮地 博文, 田中 徹, 武田 修一, 藤井 哲雄, 松村 祐治, 浜上 和久, 田中 徹
pp. 3189-3195
論文アクセスランキング
04 Sep. (Last 30 Days)
-
Perspectives on the Promising Pathways to Zero Carbon Emissions in the Steel Industry toward 2050
ISIJ International Vol.65(2025), No.2
-
溶鋼中での各種酸化物系介在物の成長・除去と凝集
鉄と鋼 Vol.111(2025), No.11
-
Finite Element Analysis of Bubble Growth and Particle Swelling during Coal Pyrolysis
ISIJ International Vol.65(2025), No.9
-
通電誘起高速共晶反応によるAl/Cu異材接合形成につながる界面挙動
溶接学会論文集 Vol.43(2025), No.2
-
Corrosion Behavior of Carbon Steel under Soil Drying Conditions
ISIJ International 早期公開
-
980 MPa級高張力鋼板の固相抵抗スポット接合
鉄と鋼 早期公開
-
-
-
Copper removal of liquid steel containing 0.25 % carbon using Fe2O3-CaCl2-SiO2 flux
ISIJ International 早期公開
-
Evaluation of Feature Selection Methods for Oxygen Supply Prediction in BOF Steelmaking
ISIJ International 早期公開
この機能はログイン後に利用できます。
下のボタンをクリックしてください。