鉄と鋼 Vol. 52 (1966), No. 2
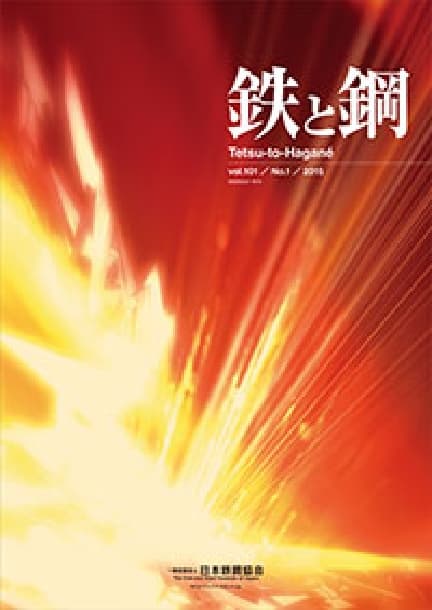
Grid List Abstracts
オンライン版ISSN: | 1883-2954 |
冊子版ISSN: | 0021-1575 |
発行機関: | The Iron and Steel Institute of Japan |
Backnumber
-
Vol. 111 (2025)
-
Vol. 110 (2024)
-
Vol. 109 (2023)
-
Vol. 108 (2022)
-
Vol. 107 (2021)
-
Vol. 106 (2020)
-
Vol. 105 (2019)
-
Vol. 104 (2018)
-
Vol. 103 (2017)
-
Vol. 102 (2016)
-
Vol. 101 (2015)
-
Vol. 100 (2014)
-
Vol. 99 (2013)
-
Vol. 98 (2012)
-
Vol. 97 (2011)
-
Vol. 96 (2010)
-
Vol. 95 (2009)
-
Vol. 94 (2008)
-
Vol. 93 (2007)
-
Vol. 92 (2006)
-
Vol. 91 (2005)
-
Vol. 90 (2004)
-
Vol. 89 (2003)
-
Vol. 88 (2002)
-
Vol. 87 (2001)
-
Vol. 86 (2000)
-
Vol. 85 (1999)
-
Vol. 84 (1998)
-
Vol. 83 (1997)
-
Vol. 82 (1996)
-
Vol. 81 (1995)
-
Vol. 80 (1994)
-
Vol. 79 (1993)
-
Vol. 78 (1992)
-
Vol. 77 (1991)
-
Vol. 76 (1990)
-
Vol. 75 (1989)
-
Vol. 74 (1988)
-
Vol. 73 (1987)
-
Vol. 72 (1986)
-
Vol. 71 (1985)
-
Vol. 70 (1984)
-
Vol. 69 (1983)
-
Vol. 68 (1982)
-
Vol. 67 (1981)
-
Vol. 66 (1980)
-
Vol. 65 (1979)
-
Vol. 64 (1978)
-
Vol. 63 (1977)
-
Vol. 62 (1976)
-
Vol. 61 (1975)
-
Vol. 60 (1974)
-
Vol. 59 (1973)
-
Vol. 58 (1972)
-
Vol. 57 (1971)
-
Vol. 56 (1970)
-
Vol. 55 (1969)
-
Vol. 54 (1968)
-
Vol. 53 (1967)
-
Vol. 52 (1966)
-
Vol. 51 (1965)
-
Vol. 50 (1964)
-
Vol. 49 (1963)
-
Vol. 48 (1962)
-
Vol. 47 (1961)
-
Vol. 46 (1960)
-
Vol. 45 (1959)
-
Vol. 44 (1958)
-
Vol. 43 (1957)
-
Vol. 42 (1956)
-
Vol. 41 (1955)
キーワードランキング
06 Sep. (Last 30 Days)
鉄と鋼 Vol. 52 (1966), No. 2
Research on Coal-Oil Slurry Injection into Blast Furnace
Kozo MORINAGA, Kikuo TAJIMA, Keizo KUSUNO, Yosimitsu JOMOTO, Yuji KANAYAMA, Hiroshi MATSUOKA
pp. 107-113
抄録
Since 1961 a research on the injection of coal-oil slurry into the blast furnace has been carried on at Muroran Works, Fuji Iron & Steel Co., Ltd., Japan.
The research was started with the selection of coal, preparation of slurry and the fundamental pipeline flow tests. According to the results thereof, a slurry injection system having a capacity of 85 tons per day was erected. Slurry began to be injected through the ten tuyeres of Muroran No.1 blast furnace from February 1963. Since then, the slurry density has been increased to 50wt% coal finesand a considerable coke saving was made.
Comparative tests, carried out between fuel oil and slurry, showed that there were no noticeable differences between them with respect to the output and the coke rate.
Experiments on the Solidification of Steel Ingots by Scrape Method
Shoichi SHIKANO, Yoshitaka NAKAGAWA, Masaru FUKUMOTO, Iwao HAGIWARA, Tadayoshi TAKAHASHI
pp. 113-119
抄録
Many investigations have been made to get sound ingots by means of modifying the solidifiCation process. Scrape method is one of them. This method was developed from the experiments worked on Al-4% Cu alloy ingots. It is to make molten metal solidify by stirring with a rod after pouring. This is, however, not simple hydrodynamic stirring. The surface of the zone of partial solidification is scraped with the rod, and this zone is destroyed.
Hence, the successive progress of this zone from the scraped region is stopped and the whole bulk liquid is brought into a creamy state. The ingots obtained are segregationless and remarkably finegrained. The causes of these phenomena are considered to be the self-nucleation of crystals and the effect of turbulent flow by scraping.
We attempted to apply this method to two steel ingots; 800kg ingot poured into metal mold and 1600kg ingot poured into sand mold.
The results obtained are as follows;
(1) Scrape method could be applied to 800kg steel ingot successfully.
(2) Macro-structure of this ingot became remarkably fine by the application of Scrape method.
But, originally, segregation is slight in this size of steel ingot poured into metal mold and because of inadequate experimental condition it was impossible to check the effect of Scrape method on V and A ghost.
(3) The results of the experiment on 1, 600kg cast steel ingot in order to check the effect of this method on V and A ghost show that the branched columnar zone, so-called the hot-bed of A ghost was destroyed by scraping, thereby developing no A ghost and the exterior of ingot was cleen. In addition, the growth of V ghost was prevented.
On the Desulphurization of Molten Pig Iron for Steelmaking in the Reversible Shaking Ladle (D. M. Converter) and the Production of Low Sulphur Steels
Takeshi OKURO, Hideo TOMOMATSU, Uichiro IIHAMA, Noboru HAYASHI, Rinnosuke YAGURA, Jiro JIZAIMARU
pp. 120-139
抄録
The authors have studied the practical aspects of the D. M. Converter for the production of low sulphur steels containing decreased sulphur of under 0.010% by the duplex method with L. D. Converter, and compared these steels of extra low sulphur content with those of normal sulphur content by the ordinary L. D. Converter process.
Test results are summarized as follows.
(1) It is easy to desulphurize the molten steelmaking pig iron (even of comparatively low temperature) to the low sulphur pig iron of under 0.010% by use of the D. M. Converter in two or three minutes' mixing treatment with suitable eccentricity, number of revolutions, inner diameter of the ladle, and with suitable time cycle of clockwise revolution, halt, and counter-clockwise revolution given to the ladle alternately; using calcium carbide of under 1.0wt% as a desulphurizing agent.
(2) It is also technically possible to desulphurize the whole molten steelmaking pig iron from blast furnace to the low sulphur pig iron and to produce the corresponding quantity of low sulphur steels of under 0.010%S by the duplex method with L. D. Converter.
(3) The merit of desulphurizing normal sulphur steels to low sulphur steels of under 0.010%S is not always clear, but the low sulphur steels (JIS SM50 grade) have proved the marked improvement of notch impact toughness and of plastic deformation characteristics, being probably caused by the remarkable decrease of amount of sulphide inclusions.
(4) It is possible to apply desulphurizing process with the D. M. Converter widely, which proved the profitable means for the production of each low sulphur high grade of steels. Desulphurization by the D. M. Converter does not result in variation of other elemental contents. It is supposed that the low sulphur steels of under 0.010%S should become more and more needed in the fields of production of each low cost high grade special steel (of heat treating type) and of quality improvement in the products requiring much less sulphur segregation in future.
他の人はこちらも検索
鉄と鋼 Vol.50(1964), No.5
鉄と鋼 Vol.53(1967), No.11
鉄と鋼 Vol.54(1968), No.11
On the Thermomechanical Treatment of Steel
Imao TAMURA
pp. 140-162
他の人はこちらも検索
鉄と鋼 Vol.50(1964), No.5
鉄と鋼 Vol.53(1967), No.11
鉄と鋼 Vol.54(1968), No.11
Preparation of Single Crystals of Iron and Iron Alloys
Tadami TAOKA, Tomoyuki TAKEUCHI, Shin TAKEUCHI
pp. 187-203
Diagram Showing Phase Relations of the Oxide Inclusions Formed in Steels of the System Fe-Cr-O
Akira ADACHI, Nobuya IWAMOTO, Masaji KITAMURA
pp. 204-205
抄録
As we have pursued recently the formation mechanism about oxide inclusions formed in steels of the system Fe-Cr-O, we could summerize it from various experimental results obtained.
Those inclusions composed of mutual solid solutions between iron chromite (FeO·Cr2O3) and sesquioxide solid solution series (Fe2O3·Cr2O3), and appearance of iron chromite having tetragonal structure depend upon added chromium contents, oxygen potential and melting temperature.
According to our proposed diagram about the system FeO·Cr2O3-Cr2O3-Fe2O3, the formation mechanism of the distorted iron chromite is reduced to the ratio of Fe+3/Fe+2 and not related to the difference of valency of chromium as previously suggested.
The results induced from our diagram are as follows:
1) There are two sorts of existence ranges from FeO·Cr2O3 to iron chromite having axial ratio c/a=0.95 and from one having c/a=0.89 to 0.86, and these tendencies agree to theresult about the oxygen content dissolved in steels of this system from the equilibrium study. Under experimental conditions of oxygen potential given, two sorts of iron chromite will be formed, that is, one (Fe, Cr) 2O3 dissolved in FeO·Cr2O3 and the other little FeO·Cr2O3 dissolved in (Fex, Cry) 2O3.
2) In the case of the steel containing much chromium or electrolytic chromium, chromic oxide is formed at the moment, then as temperature falls, FeO·Cr2O3 will be dissolved into it and arrive to c/a=0.86 type iron chromite.
論文アクセスランキング
06 Sep. (Last 30 Days)
-
Perspectives on the Promising Pathways to Zero Carbon Emissions in the Steel Industry toward 2050
ISIJ International Vol.65(2025), No.2
-
溶鋼中での各種酸化物系介在物の成長・除去と凝集
鉄と鋼 Vol.111(2025), No.11
-
Finite Element Analysis of Bubble Growth and Particle Swelling during Coal Pyrolysis
ISIJ International Vol.65(2025), No.9
-
通電誘起高速共晶反応によるAl/Cu異材接合形成につながる界面挙動
溶接学会論文集 Vol.43(2025), No.2
-
Corrosion Behavior of Carbon Steel under Soil Drying Conditions
ISIJ International 早期公開
-
980 MPa級高張力鋼板の固相抵抗スポット接合
鉄と鋼 早期公開
-
-
-
Copper removal of liquid steel containing 0.25 % carbon using Fe2O3-CaCl2-SiO2 flux
ISIJ International 早期公開
-
Evaluation of Feature Selection Methods for Oxygen Supply Prediction in BOF Steelmaking
ISIJ International 早期公開
この機能はログイン後に利用できます。
下のボタンをクリックしてください。