鉄と鋼 Vol. 58 (1972), No. 5
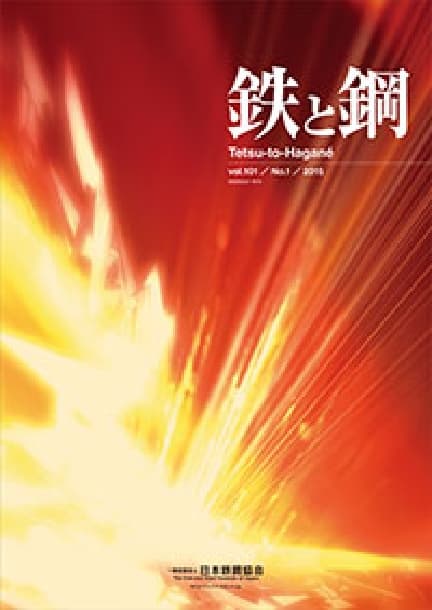
Grid List Abstracts
オンライン版ISSN: | 1883-2954 |
冊子版ISSN: | 0021-1575 |
発行機関: | The Iron and Steel Institute of Japan |
Backnumber
-
Vol. 111 (2025)
-
Vol. 110 (2024)
-
Vol. 109 (2023)
-
Vol. 108 (2022)
-
Vol. 107 (2021)
-
Vol. 106 (2020)
-
Vol. 105 (2019)
-
Vol. 104 (2018)
-
Vol. 103 (2017)
-
Vol. 102 (2016)
-
Vol. 101 (2015)
-
Vol. 100 (2014)
-
Vol. 99 (2013)
-
Vol. 98 (2012)
-
Vol. 97 (2011)
-
Vol. 96 (2010)
-
Vol. 95 (2009)
-
Vol. 94 (2008)
-
Vol. 93 (2007)
-
Vol. 92 (2006)
-
Vol. 91 (2005)
-
Vol. 90 (2004)
-
Vol. 89 (2003)
-
Vol. 88 (2002)
-
Vol. 87 (2001)
-
Vol. 86 (2000)
-
Vol. 85 (1999)
-
Vol. 84 (1998)
-
Vol. 83 (1997)
-
Vol. 82 (1996)
-
Vol. 81 (1995)
-
Vol. 80 (1994)
-
Vol. 79 (1993)
-
Vol. 78 (1992)
-
Vol. 77 (1991)
-
Vol. 76 (1990)
-
Vol. 75 (1989)
-
Vol. 74 (1988)
-
Vol. 73 (1987)
-
Vol. 72 (1986)
-
Vol. 71 (1985)
-
Vol. 70 (1984)
-
Vol. 69 (1983)
-
Vol. 68 (1982)
-
Vol. 67 (1981)
-
Vol. 66 (1980)
-
Vol. 65 (1979)
-
Vol. 64 (1978)
-
Vol. 63 (1977)
-
Vol. 62 (1976)
-
Vol. 61 (1975)
-
Vol. 60 (1974)
-
Vol. 59 (1973)
-
Vol. 58 (1972)
-
Vol. 57 (1971)
-
Vol. 56 (1970)
-
Vol. 55 (1969)
-
Vol. 54 (1968)
-
Vol. 53 (1967)
-
Vol. 52 (1966)
-
Vol. 51 (1965)
-
Vol. 50 (1964)
-
Vol. 49 (1963)
-
Vol. 48 (1962)
-
Vol. 47 (1961)
-
Vol. 46 (1960)
-
Vol. 45 (1959)
-
Vol. 44 (1958)
-
Vol. 43 (1957)
-
Vol. 42 (1956)
-
Vol. 41 (1955)
鉄と鋼 Vol. 58 (1972), No. 5
Recent Progress and Future Prospects in Blast Furnace Fuel Injection
Heiji IKEGAMI
pp. 559-565
Consideration of Oil Replacement Ratio and Large Amount of Oil Injection in Blast Furnace
Yasumoto OTAKE, Fumio NAKAMURA
pp. 578-588
抄録
An expression for oil replacement ratio has been fully derived on the basis of theoretical carbon rate with or without oil injection.
As two examples of the modified blast, injection of a large amount of heavy oil combined with exygen enriched blast or with high temperature blast have been discussed by the proposed method.
Moreover, the operating results of domestic blast furnaces with liquid fuel injection have been analyzed statistically.
他の人はこちらも検索
鉄と鋼 Vol.57(1971), No.1
鉄と鋼 Vol.79(1993), No.2
鉄と鋼 Vol.59(1973), No.13
Investigations on the Phenomena in the Blast Furnace with Heavy Oil Injection
Masaharu SHIMIZU, Tamotsu NAGAI, Kyoji OKABE, Mikio KONDO, Toshihiro INATANI
pp. 589-599
抄録
In order to study the phenomenological changes in the blast furnace accompanied with the injection of heavy oil at the tuyere, the reaction gas at the tip of the tuyere was sampled by, the use of the horizontal probe and analysed. In the case of no oil injection, CO2 content increased with decreasing oxygen content in the inward direction gradually, and after reaching the maximum point of CO2 content, CO and H2 content increased. When the injection rate of heavy oil increased, these phenomena tended to proceed rapidly and to be accomplished in shorter range. When the nozzle head of the oil burner was pulled backward in the blow pipe, the decrease of oxygen occurred even in the blow pipe. The decrease of the space of the raceway accompanied with the increase of oil rate was found also by the bar-test. The gas distribution at the top of the shaft was measured by the horizontally inserted probe installed at the stockline level and the gas efficiency was calculated.
Oxygen Enrichment and Oil Injection in Blast Furnaces at Wakayama Steel Works
Shunji YAMAZAKI, Fumitada NAKATANI, Takuo KANO, Masayoshi NAKAGAWA
pp. 600-607
抄録
Operation data of the blast furnaces at Wakayama Steel Works were analyzed.
Under insufficient heat compensation, the increase of fuel oil results in the decrease of direct reduction, and replacement coefficient is lowered. In this case, top gas ratio, CO/CO2 decreases with the increase of ratio ore/coke, and the decrease of CO/CO2 results in prevention of the decrease of replacement coefficient. It seems, however, that the top gas ratio is limited to certain value.
The oxygen atomized burner were used at Wakayama No 2BF. Much quantity of heavy oil was burned successfuly even under the condition of oxygen excess coefficient (μ) 1.0.(in the case of ordinary type, minimum μ=1.5)
他の人はこちらも検索
鉄と鋼 Vol.57(1971), No.1
鉄と鋼 Vol.79(1993), No.2
鉄と鋼 Vol.59(1973), No.13
Reducing Gas Injection into Furnace Stack in an Experimental Furnace
Tsuneo MIYASHITA, Hiroaki NISHIO, Teruo SIMOTSUMA, Takeo YAMADA, Mitsuru OHOTSUKI
pp. 608-623
抄録
The effect of reducing gas injection on the coke rate and coke to oil replacementratio was investigated in an experimental furnace of 3.2 m3 inner volume under conditions similar to a commercial furnace. Reducing gas made by partial combustion of oil with oxygen was injected at a constant blast volume.
(1) The 571 kg/t HM of coke rate in the standard process decreased to 374 kg/tHM with 628 Nm3/tHM of gas injection. The replacement ratio was between 0.75 and 0.82 depending on the amount of injected gas.
(2) An appropriate amount of injection of reducing gas together with oxygen enrichment improved heat exchange condition at the furnace shaft to increase productivity without any increase in coke rate.
(3) 85 percent of oxygen of are was removed by CO and H2 with 628Nm3/tHM of injected gas in comparison with 65% in the standard process. Ore reduced in the same retention time increased by two times by this gas injection.
(4) By considering the staged heat balance, it was shown that the gas should contain less CO2 and H2O and had to be heated above 1000°C. The gas should be injected at below the thermal reserve zone.
(5) The economy of the technipue depended on the prices of coke and gas, and the replacement ratio. Even at present, this technipue has been proved to be economical.
他の人はこちらも検索
鉄と鋼 Vol.59(1973), No.10
鉄と鋼 Vol.56(1970), No.7
材料と環境 Vol.64(2015), No.11
Injection of Reducing Gas into Blast Furnace (FTG Process)
Takeo YATUZUKA, Kazuyuki NAKAYAMA, Kazuo OHMORI, Yoshiaki HARA, Masaaki IGUCHI
pp. 624-636
抄録
Since the lack of coking coal is a serious problem for steel industry, various studies have been carried out for saving coking coal, such as the way of decreasing coal consumption in blast furnace process, the research and development of formed coke process and of direct iron making process etc. Among them fuel injection through blast tuyere is a very effective process because coke is directly replaced by injected fuel, and recently coke rate of 360kg/t level was obtained by several blast furnaces under fuel oil injection of approximately 100kg/t in combination with the oxygen enrichment. However, the capacity of race way is limited as gasifying chamber to burn injected fuel from tuyere. In order to save coal moreover, it may be a good idea to produce reducing gas from fuel oil outside blast furnace and to inject it into blast furnace.
Reducing gas injection processes have long been subjects of investigation, where reducing gas is produced from fuel by cracking in an exclusive gasifying chamber and is injected into blast furnace, and recently reports of some performances with actual experimental equipment were published. On this subject authors have carried out several fundamental studies such as investigation of reducing gas production process, estimation of the effect of reducing gas injection by a mathematical model of blast furnace, examination on mixing of injected gas inside blast furnace using air-CO2 model, and plant engineering for dealing with hot reducing gas. As for reducing gas production a joint research has been conducted with Texaco Inc. who has many experiences in this technology.
A commercial scale experiment (FTG process) has been carried out using a blast furnace of 1691m3 inner volume with which a Texaco-type generator of fuel oil gasifying capacity of 5 t/hr was installed, and the following results were obtained;
(1) Partial oxidation process was considered to be optimum in order to produce hot reducing gas of high reducing power from the available fuel oil.
(2) Cok saving was 0.9-1.0kg per gasified fuel oil of 1.0kg when hot reducing gas was injected into lower part of blast furnace shaft under following conditions;
Fuel oil rate injected through tuyere:<70kg/t
Fuel oil rate gasified by FTG process:<30kg/t
R. R. value of injected gas: 6-8
where; R. R.(CO+H2)/(CO2+H2O)
(3) The fuel oil gasifying system and the hot reducing gas transfer system were kept under good conditions, and the blast furnace was operated smoothly.
他の人はこちらも検索
鉄と鋼 Vol.56(1970), No.7
鉄と鋼 Vol.59(1973), No.10
材料と環境 Vol.66(2017), No.1
On the Highly Oxygen-Enriched Blast Furnace Operation Utilizing Top Gas for Ammonia Synthesis
Takashi OKAMOTO, Yoshinosuke TADA, Taku SUGIURA
pp. 637-650
抄録
In order that top gas of a pig iron blast furnace can be utilized for ammonia synthesis by itself, oxygen content of the blast should be enriched to about 50-60%.
It seems that there has never been any report on the industrialization of a blast furnace by such highly oxygen-enriched blast.
The authors have succeeded in the operation of test furnaces and an industrial furnace by such blast, the results of which are reported in this paper.
As the results of test furnaces, blow-in of the cleaned top gas through tuyeres together with the blast or injection of heavy oil was adopted to lower extremely high combustion temperature in front of the tuyeres and to increase the volume of ascending bosh gas.
The industrial operation was successfully continued for three years and ten months at max. 55% oxygen in blast and produced about 90 000 tons of foundry pig iron and 134×106 Nm3 of effective gas (CO+H2) equivalent to about 60 000 tons of ammonia by the time of stoppage on account of changerof ammonia plant.
High Blast Temperature Operation of Blast Furnace at Kakogawa Works, Kobe Steel LTD
Osamu SAEKI, Setsuo TAMURA, Toshiyuki UENAKA, Yoshio OOTA, Kozo TANAKA
pp. 651-659
抄録
The technique of high blast-temperature operation of blast furnace is advantageous in that it can reduce coke ratio and increase production of hot metal. Therefore, it is now a common practice to operate blast furnace with blast temperature over 1 100°C. With the advent of large, high top-pressure blast furnace operations, however, an increase in physical load caused by rising inside temperature and pressure due to high blast temperature leads to troubles in equipments. This is the bottleneck of such operation.
By adopting the following measures, we have achieved a satisfactory operation of No 1 blast furnace at our Kakogawa Works with blast temperature of 1 250 to 1 300°C.
(1) Adoption of Martin type hot stoves.
(2) Increase in thickness of the linning of hot main and bustle pipe and improvement of their structure.
(3) Adoption of blowing stock with two-fold linning structure.
(4) Increase of dome temprature of hot stoves through adoption of air preheater.
(5) Protector for hot blast valves.
(6) Control of charging material for blast furnace and adjustment of gas distribution by using movable armour and sampling equipment of furnace gas.
The basic construction plan for No 2 blast furnace at Kakogawa will be worked out based on our experiences in No 1 blast furnace. Furthermore, through lap parallel operation with four hot stoves and hot blast valves made of steel plates etc., we are intending to establish a technique of high blast temperature operation for a large, high top pressure blast temperature operation for a large, high top pressure blast furnace of 4 000m3 class.
他の人はこちらも検索
鉄と鋼 Vol.68(1982), No.7
鉄と鋼 Vol.68(1982), No.6
鉄と鋼 Vol.71(1985), No.2
抄録
pp. 660-666
他の人はこちらも検索
鉄と鋼 Vol.57(1971), No.1
鉄と鋼 Vol.79(1993), No.2
鉄と鋼 Vol.59(1973), No.13
論文アクセスランキング
02 Aug. (Last 30 Days)
-
Perspectives on the Promising Pathways to Zero Carbon Emissions in the Steel Industry toward 2050
ISIJ International Vol.65(2025), No.2
-
Effect of BN surface segregation on coatability in hot-dip galvanizing of B-added steel
ISIJ International 早期公開
-
Copper removal of liquid steel containing 0.25 % carbon using Fe2O3-CaCl2-SiO2 flux
ISIJ International 早期公開
-
-
-
溶銑予備処理技術の開発,発展の歴史と将来展望
鉄と鋼 Vol.100(2014), No.4
-
銅含有棒鋼の熱間圧延プロセスにおける表面欠陥の発生
鉄と鋼 Vol.111(2025), No.5
-
Factors affecting generation of iron fines in cold sheet rolling of steel
ISIJ International 早期公開
-
-
Dislocation Density and Reverse Transformation Kinetics in Martensitic Steel Under Cyclic Ultrafast Heating and Cooling
ISIJ International Vol.65(2025), No.8
この機能はログイン後に利用できます。
下のボタンをクリックしてください。